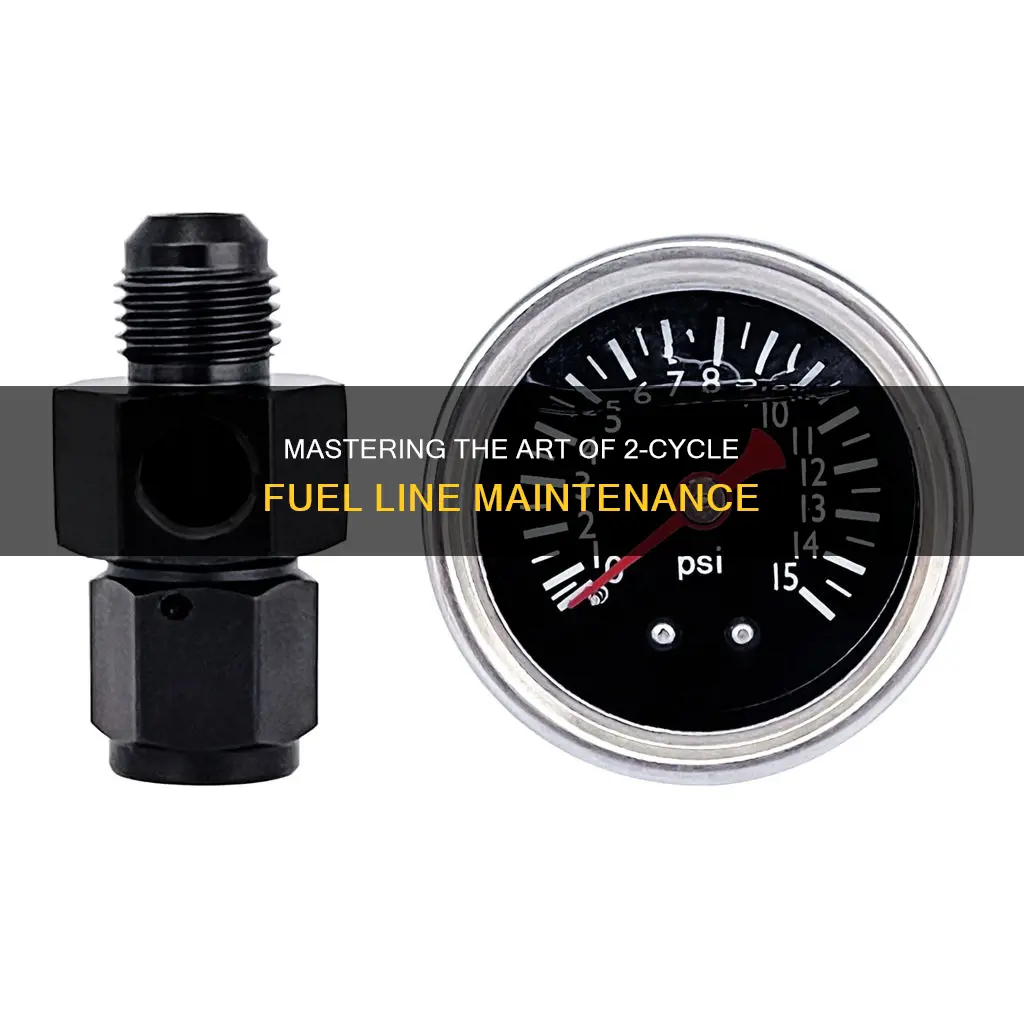
Measuring and gauging 2-cycle fuel lines is a crucial step in ensuring the proper functioning of your engine. This process involves assessing the fuel flow rate and pressure to guarantee optimal performance. By understanding how to gauge these lines, you can prevent issues like fuel starvation, which can lead to engine misfires or even stall. This guide will provide a step-by-step approach to help you accurately measure and gauge your 2-cycle fuel lines, ensuring your engine runs smoothly and efficiently.
What You'll Learn
- Fuel Line Material: Choose the right material for durability and flexibility
- Line Diameter: Measure and select the appropriate diameter for optimal flow
- Length and Routing: Ensure proper length and route to prevent kinks and blockages
- Fittings and Connections: Use compatible fittings for secure and leak-free connections
- Pressure Testing: Test fuel lines for leaks and ensure they hold pressure
Fuel Line Material: Choose the right material for durability and flexibility
When it comes to choosing the right material for your 2-cycle fuel lines, durability and flexibility are key factors to ensure optimal performance and longevity. The fuel lines in your engine are responsible for delivering the gasoline-oil mixture to the carburetor, and any damage or degradation can lead to poor engine operation and potential breakdowns. Here's a detailed guide on selecting the appropriate material:
Rubber: A Classic Choice: Rubber has been the traditional material for fuel lines due to its inherent flexibility and resistance to abrasion. Natural rubber or synthetic rubber compounds are commonly used, offering a good balance between flexibility and strength. Look for fuel lines made from high-quality rubber, as some lower-grade options may become brittle over time, especially in outdoor environments. Rubber's ability to withstand temperature fluctuations and its resistance to gasoline and oil make it an excellent choice for 2-cycle engines.
Reinforced Rubber: Adding Strength: For applications requiring extra strength and durability, consider reinforced rubber fuel lines. These lines incorporate a braided or spiral-reinforced structure, providing enhanced resistance to pressure and abrasion. The reinforcement ensures that the fuel lines can handle the rigors of engine operation, including vibrations and potential impacts. Reinforced rubber is particularly useful in high-performance or off-road vehicles where fuel lines might be subjected to more extreme conditions.
PVC (Polyvinyl Chloride): PVC is another popular material for fuel lines, especially in marine and recreational vehicle applications. It offers excellent chemical resistance, making it ideal for engines that use different types of fuels or additives. PVC fuel lines are known for their flexibility and ability to withstand UV radiation, ensuring long-lasting performance. However, it's important to note that PVC may not be as flexible as rubber in very cold temperatures, so consider this when operating in extreme climates.
Silicone: Extreme Conditions, Extreme Material: In high-temperature environments or for engines that require specialized fuel handling, silicone fuel lines are an excellent choice. Silicone is highly flexible and resistant to heat, making it suitable for applications where traditional rubber might fail. It can withstand temperatures far beyond those of conventional rubber, ensuring that the fuel lines remain pliable and functional. Silicone is also resistant to gasoline and oil, providing reliable performance.
When selecting fuel line material, consider the specific requirements of your 2-cycle engine, including operating conditions, fuel type, and environmental factors. Each material offers unique advantages, and choosing the right one will contribute to the overall reliability and efficiency of your engine's fuel delivery system. Remember, the goal is to find a balance between flexibility and strength to ensure your fuel lines can withstand the demands of your engine's operation.
The Dangers of Driving with a Fuel Line Leak: What You Need to Know
You may want to see also
Line Diameter: Measure and select the appropriate diameter for optimal flow
When it comes to 2-cycle fuel lines, the diameter plays a crucial role in ensuring optimal performance and efficient fuel delivery. The line's diameter directly impacts the flow rate of the fuel mixture, which is essential for proper engine operation. Here's a detailed guide on how to measure and select the appropriate line diameter:
Understanding the Importance of Diameter: The fuel line's diameter determines the cross-sectional area, which in turn affects the fuel flow rate. A larger diameter allows for a higher volume of fuel to pass through, ensuring a well-mixed and consistent fuel-air mixture. This is particularly important in 2-cycle engines, where the fuel and air are mixed and ignited simultaneously. An incorrect diameter can lead to poor engine performance, reduced power, and even starting difficulties.
Measuring the Existing Line (Optional): If you're replacing a fuel line, it's helpful to measure the existing one to ensure compatibility. Use a tape measure or caliper to record the diameter at the widest point of the line, typically near the carburetor. This measurement will guide your choice of a replacement line.
Selecting the Right Diameter: The optimal diameter depends on various factors, including engine displacement, carburetor type, and operating conditions. As a general rule, a larger diameter is often preferred for higher-performance applications or engines with larger displacements. For example, a 2-cycle engine with a displacement of 250cc or more might benefit from a fuel line with a diameter of 3/8 inch or larger. Always refer to the manufacturer's specifications or consult a technical guide for your specific engine model.
Flow Rate Considerations: The flow rate of the fuel line should match the engine's requirements. A too-small diameter may result in inadequate fuel supply, while an oversized line could lead to unnecessary fuel wastage and potential performance issues. Finding the right balance ensures that the fuel mixture reaches the engine at the desired rate, promoting efficient combustion.
Installation and Testing: Once you've selected the appropriate diameter, ensure a proper installation. Check for any kinks or bends that could restrict flow. After installation, start the engine and monitor its performance. Adjust the fuel line's position if necessary to optimize flow and ensure the engine runs smoothly.
Mastering Dorman Steel Fuel Lines: A Guide to Secure Connections
You may want to see also
Length and Routing: Ensure proper length and route to prevent kinks and blockages
When dealing with two-stroke engines, proper fuel line installation is crucial to ensure optimal performance and longevity. One critical aspect often overlooked is the length and routing of the fuel lines. Here's a detailed guide on how to ensure your fuel lines are correctly installed:
Length and Routing:
The fuel lines should be long enough to reach the carburetor without any unnecessary tension or kinks. A general rule of thumb is to allow for at least 12 inches of extra length beyond the engine's fuel tank. This extra length provides flexibility and accommodates any potential movement of the engine or fuel tank. Ensure that the lines are not too long, as this can lead to fuel line sagging, which may cause blockages or reduced fuel flow.
Routing the fuel lines correctly is essential to prevent damage and ensure a smooth flow of fuel. The lines should be routed away from hot engine components to avoid overheating and potential fuel degradation. Keep the lines as straight as possible, avoiding sharp bends or kinks, as these can restrict fuel flow and cause pressure drops. A common practice is to use fuel line clips or ties to secure the lines in place, ensuring they remain taut and free from any obstructions.
When routing the lines, consider the engine's layout and any potential interference. Avoid crossing over other engine components or cables, as this can lead to damage or fuel contamination. Proper routing will also make maintenance and inspections easier, allowing for quick access to the fuel lines when needed.
Additionally, pay attention to the carburetor's location and the engine's orientation. If the carburetor is positioned lower than the fuel tank, the lines should be sloped downward to facilitate gravity-fed fuel flow. Ensure that the lines are not too close to the ground, as this can lead to fuel line damage from debris or small animals.
In summary, proper length and routing of two-cycle fuel lines are vital to prevent kinks, blockages, and potential engine issues. By allowing sufficient length, avoiding sharp bends, and considering the engine's layout, you can ensure a reliable and efficient fuel supply to your two-stroke engine. Regular inspection and maintenance of the fuel lines will further contribute to the overall performance and longevity of your engine.
Nylon Fuel Lines: Essential Clamps or Optional?
You may want to see also
Fittings and Connections: Use compatible fittings for secure and leak-free connections
When working with 2-cycle fuel lines, ensuring secure and leak-free connections is crucial for optimal performance and reliability. The key to achieving this lies in the choice and proper installation of fittings. Here's a detailed guide on how to approach this aspect:
Understanding Fitting Compatibility: Begin by understanding the importance of using compatible fittings. Different types of fuel lines require specific fittings to ensure a tight seal and prevent fuel leaks. Common types of fittings include barbed, compression, and quick-connect fittings. Each type has its own unique design and purpose, so it's essential to match the fitting to the fuel line's specifications. For instance, barbed fittings are ideal for flexible fuel lines, while compression fittings provide a secure seal for rigid lines.
Selecting the Right Fittings: Choose fittings that are specifically designed for 2-cycle engine applications. These engines often require high-pressure fuel lines, so opt for fittings that can withstand such conditions. Look for fittings made from durable materials like brass or stainless steel to ensure longevity. Check the manufacturer's recommendations or specifications for your fuel line to determine the appropriate fitting type and size.
Installation Techniques: Proper installation is as important as choosing the right fittings. When connecting the fuel line to the carburetor or fuel tank, ensure a tight and secure fit. Use the appropriate tools, such as crimping pliers or compression fitting tools, to create a reliable connection. Take your time and follow the manufacturer's instructions for each fitting type. A secure connection will prevent fuel from leaking out and ensure efficient fuel delivery to the engine.
Leak-Prevention Measures: To avoid fuel leaks, pay attention to detail during the installation process. Ensure that all fittings are tightened to the recommended torque specifications. Over-tightening can damage the fuel line, while under-tightening may result in leaks. Inspect the connections regularly, especially in areas with vibration or potential impact, to identify and address any issues promptly.
Maintenance and Inspection: Regular maintenance and inspections are essential to maintaining a healthy fuel system. Periodically check the fittings and connections for any signs of wear, corrosion, or damage. Clean or replace fittings as needed to prevent fuel contamination and ensure optimal engine performance. By following these practices, you can guarantee secure and leak-free connections, contributing to a well-functioning 2-cycle engine.
Fuel Line Routing: Connecting Cylinder Heads for Optimal Performance
You may want to see also
Pressure Testing: Test fuel lines for leaks and ensure they hold pressure
Pressure testing is a crucial step in ensuring the integrity of your 2-cycle fuel lines. It helps identify any potential leaks or weaknesses in the system, preventing fuel loss and potential engine damage. Here's a detailed guide on how to perform this test:
Preparation: Before you begin, ensure you have the necessary tools and materials. You'll need a fuel pressure gauge, which can be either mechanical or digital, depending on your preference and the availability of tools. It should be capable of measuring the pressure in the range of 0-100 psi (pounds per square inch). Additionally, you'll require a source of compressed air or an air compressor to generate the test pressure. It's also a good idea to have some cleaning supplies, like a brush or a compressed air nozzle, to remove any debris or fuel residue from the fuel lines.
Procedure: Start by disconnecting the fuel lines from the carburetor and the fuel tank. This step ensures that you can test the lines without the interference of the engine's running system. Use a suitable fuel line disconnect tool to avoid damaging the lines. Once disconnected, attach the fuel pressure gauge to one end of the line and the compressed air source to the other. Ensure a tight and secure connection. Now, slowly open the compressed air valve to build up pressure in the line. Start with a low pressure and gradually increase it, allowing the gauge to read the pressure accurately. Aim for a pressure of around 50-70 psi, which is a typical operating pressure for 2-cycle engines.
As you increase the pressure, be vigilant for any signs of fuel escaping from the lines. Leaks can occur at connections, bends, or any points where the fuel lines are not properly secured. If you notice any fuel seeping out, immediately release the pressure and inspect the lines for damage or loose fittings. It's essential to identify and fix any leaks before proceeding.
Leak Detection: If no leaks are detected, the next step is to ensure the fuel lines can hold the test pressure. Close the compressed air valve and observe the gauge reading. The pressure should remain stable for a few seconds, indicating that the lines are holding the test pressure effectively. If the pressure drops significantly or the gauge shows an unstable reading, it suggests that there might be an issue with the fuel lines' integrity, such as a crack or a weakened section. In such cases, the lines may need to be replaced or repaired.
Safety and Maintenance: Pressure testing should be performed regularly, especially if you notice any changes in engine performance or fuel consumption. It is a preventive maintenance measure that can save you from potential engine damage caused by fuel leaks. Always remember to follow safety guidelines when working with compressed air and fuel systems. Keep your tools and equipment clean to avoid contamination of the fuel lines.
Fuel Filter's Three Lines: Unraveling the Mystery in Ford Expedition
You may want to see also
Frequently asked questions
Gauging 2-cycle fuel lines is essential for ensuring optimal engine performance and longevity. It helps to maintain the correct fuel-to-oil ratio, which is critical for two-stroke engines. This process ensures that the engine receives the right amount of fuel, preventing issues like excessive smoke, reduced power, and potential engine damage.
It is recommended to gauge your fuel lines regularly, especially before each use of the equipment. Over time, fuel can degrade and become less effective, leading to performance issues. Additionally, after refilling the fuel tank, it's a good practice to gauge the lines to ensure the new fuel is properly mixed.
You will typically need a fuel line gauge, which is a specialized tool designed for this purpose. These gauges often have a clear scale to measure the fuel pressure and ensure it falls within the optimal range. Some gauges might also include a built-in pressure regulator to adjust the fuel flow.
The ideal fuel pressure can vary depending on the specific engine and its manufacturer's recommendations. Generally, a pressure reading between 20-40 psi (pounds per square inch) is considered optimal for most 2-cycle engines. It's crucial to consult the engine's manual or seek expert advice for the precise pressure range suitable for your equipment.
If you notice any of the following signs, it may indicate that your fuel lines need replacement: persistent engine misfires, excessive fuel consumption, reduced power output, or visible damage to the fuel lines. Regular maintenance and gauging can help identify potential issues early on, ensuring your engine remains in good condition.