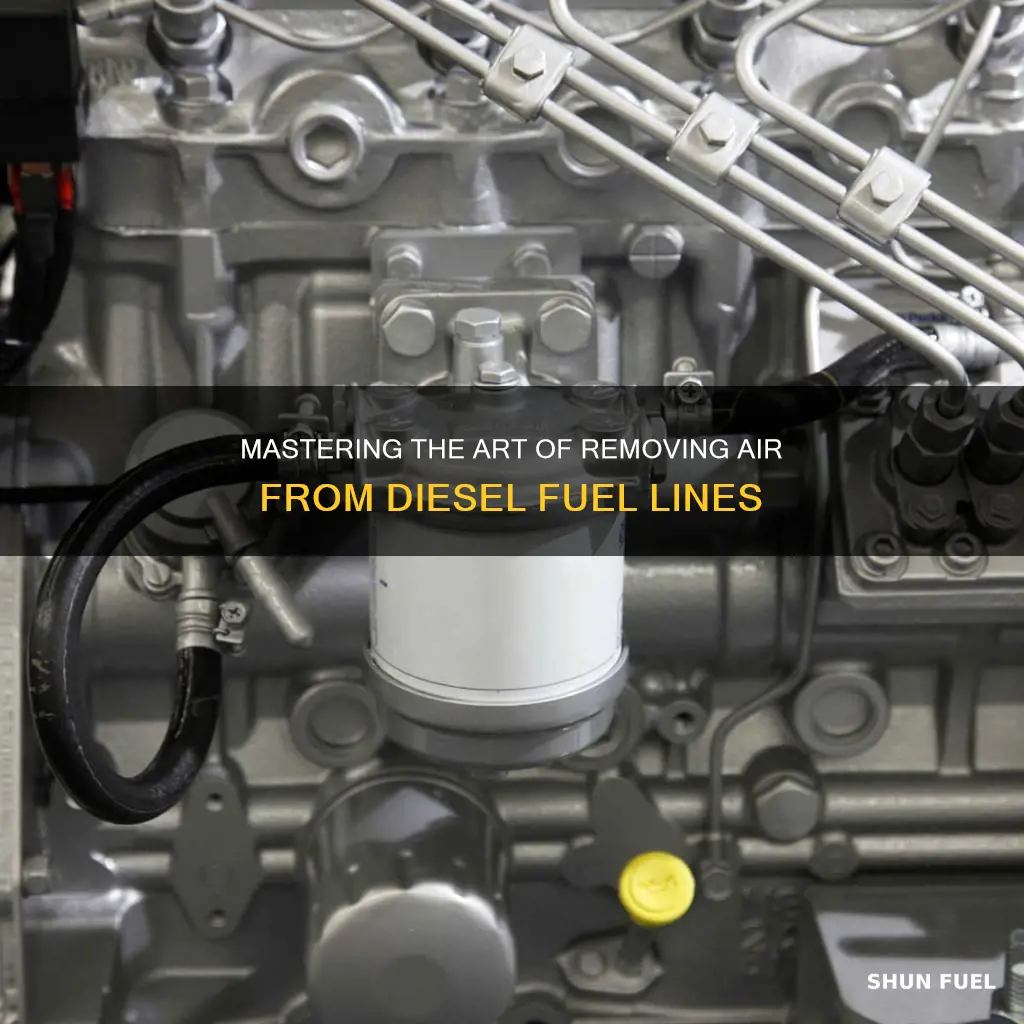
If you've ever encountered an air bubble in your diesel fuel line, you know it can cause a host of problems. Air bubbles can lead to poor engine performance, reduced fuel efficiency, and even engine damage. Fortunately, there are several methods to eliminate these air bubbles and get your diesel engine running smoothly again. This guide will explore the most effective techniques to remove air from a diesel fuel line, ensuring your vehicle operates at its best.
What You'll Learn
- Bleeding the System: Use a hand pump or vacuum to draw air out of the line
- Venting: Open vents or bleeder valves to release air pockets
- Pressure Testing: Check for leaks and air bubbles with a pressure gauge
- Fuel Filter Replacement: New filters can trap air bubbles and prevent contamination
- Line Inspection: Visually inspect for damage or blockages that may trap air
Bleeding the System: Use a hand pump or vacuum to draw air out of the line
To effectively remove air from a diesel fuel line, you can employ a simple yet effective method using a hand pump or a vacuum. This process, known as bleeding the system, is crucial to ensure optimal fuel delivery and engine performance. Here's a step-by-step guide to help you through this process:
Start by locating the fuel line that needs to be bled. It is typically found running from the fuel tank to the engine. Identify any accessible points along the line where you can connect your hand pump or vacuum. These points should be close to the fuel tank and engine to facilitate the removal of air.
Once you've identified the suitable locations, attach the hand pump or vacuum to the fuel line. Ensure a secure connection to create an airtight seal. If using a hand pump, position it so that the pump's action mimics the flow of fuel, pushing it through the line. For a vacuum, create a suction effect to draw air out.
Now, begin the bleeding process. If using a hand pump, operate it slowly and steadily, allowing the fuel to flow through the line. This action will force any trapped air out of the system. If a vacuum is your choice, create a strong suction to draw air out of the line. You may need to adjust the position of the vacuum or pump to find the most effective spot for air removal.
As you continue, you should notice a decrease in the air hissing or bubbling sounds, indicating that the air is being expelled from the system. Keep the process going until you are confident that all the air has been removed. This might require some patience, especially if the line is long or the air pockets are extensive.
Remember, the goal is to ensure that the fuel line is free of any air bubbles, as air in the fuel can lead to engine misfires, reduced performance, and potential damage. By following these steps and using a hand pump or vacuum, you can efficiently bleed the diesel fuel system and maintain the health of your engine.
Unrusting the Fuel Line: A Step-by-Step Guide to Removing Corroded Fittings
You may want to see also
Venting: Open vents or bleeder valves to release air pockets
When dealing with air in a diesel fuel line, one of the most effective methods to eliminate air pockets is by utilizing open vents or bleeder valves. These components are specifically designed to allow air to escape from the fuel system, ensuring a smooth and efficient flow of fuel. Here's a step-by-step guide on how to use these vents effectively:
Locate the vents: In a diesel engine, vents are typically found along the fuel lines, often near the fuel tank or the engine itself. These vents might be small openings or valves that can be manually opened or automatically activated. Identify these vents as they are crucial for the venting process.
Open the vents: Once you've located the vents, carefully open them. This action creates a pathway for air to escape from the fuel line. You can usually open the vents by turning them clockwise or counterclockwise, depending on the design. Ensure that you open them wide enough to allow air to pass through but not so much that it causes fuel to spill.
Observe the release of air: As you open the vents, you should hear or notice the release of air. This process might take a few moments, and you may see small bubbles or feel a slight pressure release. The air escaping indicates that the vents are functioning correctly and helping to eliminate air pockets.
Monitor the fuel flow: While venting, keep an eye on the fuel flow to ensure there are no sudden surges or spills. This step is crucial to prevent any potential hazards or fuel wastage. Adjust the vent opening as needed to maintain a steady and controlled flow.
Repeat as necessary: Depending on the severity of the air issue, you might need to repeat the venting process multiple times. If air pockets persist, continue opening and closing the vents until the problem is resolved. This method is often more effective than simply trying to 'knock' air out, as it provides a controlled and safe way to remove air from the fuel system.
Unraveling the Mystery: Chainsaw Fuel Lines Explained
You may want to see also
Pressure Testing: Check for leaks and air bubbles with a pressure gauge
Pressure testing is a crucial step in ensuring that your diesel fuel system is free from air bubbles and leaks. This process involves using a pressure gauge to measure the pressure within the fuel lines and system, allowing you to identify any potential issues. Here's a detailed guide on how to perform this test:
Preparation: Before you begin, ensure you have the necessary tools, including a pressure gauge specifically designed for fuel systems. It should have a range suitable for diesel fuel pressures, typically ranging from 0 to 100 psi (pounds per square inch). Also, gather the required materials like a fuel line adapter and a suitable cleaning agent. Make sure the diesel engine is off and the fuel system is cooled down to avoid any safety hazards.
Procedure: Start by connecting the pressure gauge to the fuel line using the adapter. Ensure a tight seal to get accurate readings. Then, slowly open the fuel line valve or the engine's fuel supply to allow fuel to enter the system. Close the valve once the gauge reaches the desired pressure, typically around 30-50 psi for diesel engines. This initial reading will give you a baseline to compare against.
Next, you'll need to identify potential leak points. Inspect all connections, including fuel injectors, pumps, and filters, for any signs of leakage. Use a soapy water solution to create a visual indicator for bubbles, which will help you pinpoint leaks. If you notice any bubbles forming or soap suds appearing, it indicates the presence of air or fuel leaks.
Troubleshooting: If you detect leaks, you'll need to address them. Start by tightening any loose connections and ensuring all components are properly secured. If leaks persist, consider replacing damaged parts or seeking professional assistance. For air bubbles, you can use a vacuum pump or a specialized fuel system bleeding tool to remove them.
Record and Repeat: Document the pressure and any issues found during this test. If leaks or air bubbles are present, repeat the process until the system is free from these problems. This iterative approach ensures a thorough inspection. Remember, pressure testing is an essential maintenance task to keep your diesel engine running efficiently and reliably.
Understanding Touareg Fuel Filter: Input vs. Output Lines
You may want to see also
Fuel Filter Replacement: New filters can trap air bubbles and prevent contamination
When replacing a fuel filter in a diesel engine, it's crucial to understand the role of the filter in maintaining the health of the engine. One of the primary functions of a fuel filter is to trap air bubbles and prevent contamination, ensuring that only clean, contaminant-free fuel reaches the engine. This is especially important in diesel systems, where air bubbles can cause significant issues.
During the replacement process, it's essential to follow a systematic approach to eliminate any air bubbles that may have accumulated in the fuel line. Start by turning off the engine and allowing it to cool down, as this will make the fuel line easier to access and work with. Locate the old fuel filter and carefully remove it, taking note of the direction of the fuel flow to ensure proper installation of the new filter.
The next step is to inspect the fuel line for any signs of contamination or damage. If you notice any debris or contaminants, it's crucial to clean the line thoroughly before proceeding. You can use a fuel line cleaner or a compressed air source to blow out any debris. Ensure that the fuel line is completely dry before continuing.
Now, it's time to install the new fuel filter. Start by threading the filter onto the fuel line, ensuring a tight connection. Use a fuel filter adapter or a similar tool to help with the installation, as this will make the process easier and more secure. Once the filter is in place, check for any leaks around the connections. If you notice any, tighten the connections further or use a suitable sealant to prevent leaks.
After the new filter is installed, it's essential to bleed the fuel system to remove any air bubbles. Start the engine and allow it to idle for a few minutes. During this time, check for any unusual noises or vibrations, which could indicate the presence of air bubbles. If you hear any hissing or bubbling sounds, it's a sign of air in the system. Turn the engine off and repeat the bleeding process until the sounds subside. This step is critical to ensure that the engine operates efficiently and without any performance issues caused by air bubbles.
Optimizing Fuel Line Safety: Where to Install the Check Valve
You may want to see also
Line Inspection: Visually inspect for damage or blockages that may trap air
When inspecting the diesel fuel line, a thorough visual examination is crucial to identify any potential issues that could be causing air retention. Start by checking the line for any visible damage, such as cracks, punctures, or signs of corrosion. These issues can lead to air entering the system, especially if the line is compromised. Look for any signs of wear and tear, especially at connections and bends, as these areas are more susceptible to damage. Ensure that all fittings and valves are securely tightened to prevent any potential leaks or blockages.
Pay close attention to the condition of the fuel line itself. Inspect for any kinks, folds, or sharp bends that might restrict the flow of fuel and allow air to accumulate. A smooth, straight line is ideal to ensure optimal fuel delivery. Check for any debris or contaminants that may have entered the line, as these can cause blockages and air pockets. Keep an eye out for any signs of rust or oxidation, especially in older systems, as these can lead to internal corrosion and restrict fuel flow.
The inspection should also cover the fuel tank and its connections. Look for any signs of moisture or condensation, as these can indicate a problem with the fuel's vapor pressure, potentially leading to air retention. Ensure that the tank's breathing system is functioning correctly, allowing air to enter and escape as needed. Any blockages or restrictions in the breathing system can trap air inside the tank.
In addition to visual cues, listen for any unusual noises during the inspection. Air bubbles can create a distinct sound, often described as a 'whooshing' or 'sucking' noise, especially when the engine is running. These sounds may indicate the presence of air in the system, requiring further investigation and potential resolution.
Remember, a comprehensive visual inspection is a critical step in identifying and resolving air-related issues in the diesel fuel line. It allows for the early detection of potential problems, ensuring optimal engine performance and longevity.
Dodge Hemi Fuel Line Disconnect: A Step-by-Step Guide
You may want to see also
Frequently asked questions
To eliminate air from a diesel fuel line, you can start by checking the fuel filter and replacing it if it's clogged or dirty. This can often be a source of air bubbles. Next, ensure that the fuel tank is full; air tends to accumulate in empty tanks. You can also try running the engine and letting it idle for a while, as this will help the fuel system expel any trapped air.
Air in diesel fuel lines can be caused by several factors. One common reason is a faulty fuel pump, which may not be able to deliver fuel at the right pressure, leading to air being drawn into the system. Additionally, loose or damaged fuel lines can allow air to seep in. Over time, fuel lines can develop small holes or cracks, especially if they are made of lower-quality materials.
While fuel additives are often marketed to improve fuel performance and cleanliness, they are not typically designed to remove existing air bubbles. However, some additives can help prevent the formation of air bubbles by reducing the water content in the fuel and maintaining the fuel's stability. It's always a good idea to consult the manufacturer's guidelines for any specific fuel additives you plan to use.