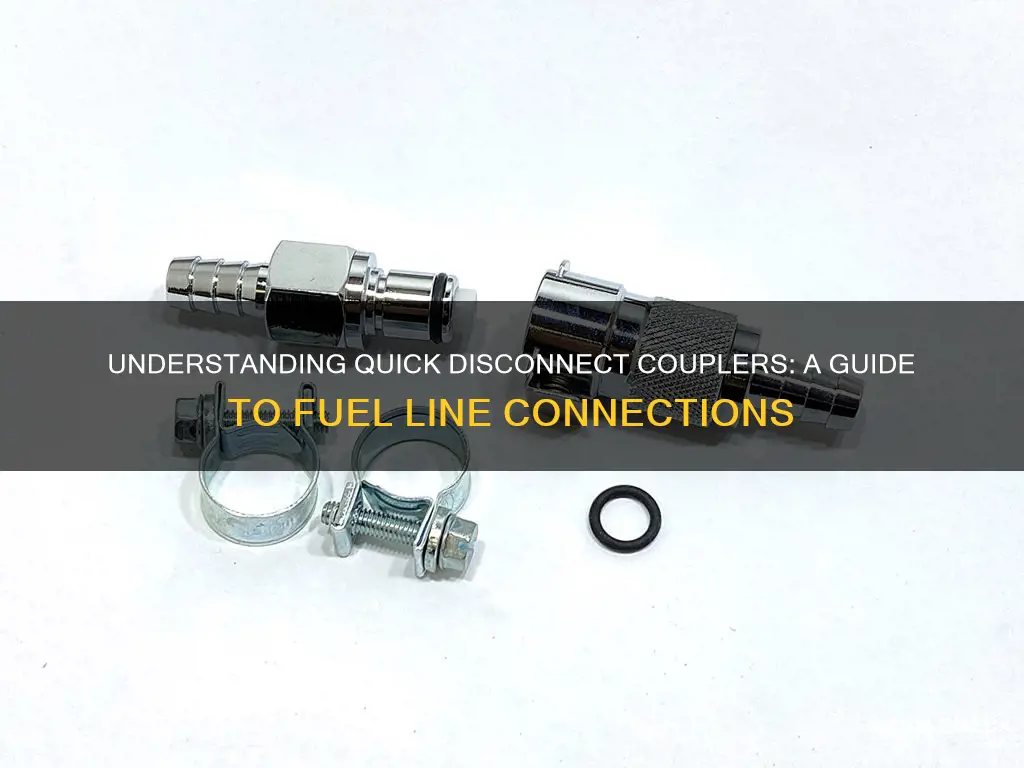
Fuel line quick disconnect couplers are essential components in the automotive industry, providing a safe and efficient way to connect and disconnect fuel lines. These couplers are designed to make the process of fueling vehicles faster and easier, eliminating the need for traditional fuel lines and reducing the risk of fuel leaks. This paragraph will explore the inner workings of these couplers, their benefits, and how they ensure a secure and reliable fuel supply.
Characteristics | Values |
---|---|
Function | Allow for quick and secure connections and disconnections of fuel lines without the need for tools or excessive force. |
Design | Typically consist of a male and female end, with a locking mechanism to ensure a tight seal. |
Materials | Made from durable materials like brass, stainless steel, or high-impact plastic to withstand fuel pressure and temperature changes. |
Sealing | Utilize O-rings or seals to create a leak-tight connection, ensuring no fuel leakage during operation. |
Pressure Rating | Designed to handle specific fuel pressures, often rated for high-pressure applications. |
Compatibility | Available in various sizes and thread types to fit different fuel lines and systems. |
Ease of Use | Feature a simple push-to-connect or twist-to-lock mechanism for quick installation and removal. |
Durability | Built to last, withstanding vibration, temperature fluctuations, and fuel contamination. |
Safety | Help prevent fuel spills, leaks, and potential fire hazards by ensuring secure connections. |
Applications | Commonly used in automotive, marine, and aviation industries for fuel tanks, injectors, and distribution systems. |
What You'll Learn
- Design and Structure: Quick disconnects use a spring-loaded mechanism to create a secure, temporary seal
- Pressure Release: Built-in pressure relief valves prevent damage during disconnection by releasing excess pressure
- Material and Durability: Couplers are made from durable materials like brass or stainless steel for long-lasting performance
- Sealing Technology: Advanced sealing materials ensure a tight connection, preventing fuel leaks and contamination
- Safety Features: Quick disconnects often include safety locks to prevent accidental disconnections during operation
Design and Structure: Quick disconnects use a spring-loaded mechanism to create a secure, temporary seal
Quick disconnect couplers are an essential component in various fluid and gas transfer systems, offering a convenient and efficient way to connect and disconnect lines without the need for threading or welding. The design and structure of these couplers are crucial to their functionality, ensuring a secure and reliable connection. One of the key elements in their design is the use of a spring-loaded mechanism, which plays a vital role in creating a temporary and secure seal.
The spring-loaded mechanism in quick disconnect couplers typically consists of a spring-loaded pin or ball, often referred to as a 'ball valve' or 'pin valve'. This component is designed to be biased in a closed position, meaning it naturally returns to this state when not engaged. When the coupler is connected, the pin or ball is forced into an open position, allowing fluid or gas to pass through. This action creates a temporary seal, as the pin or ball seals against a corresponding groove or seat within the coupling.
The design of this mechanism is critical to its performance. The spring must be strong enough to hold the pin or ball in the closed position when not in use, ensuring a secure seal. Simultaneously, it needs to be flexible and responsive enough to allow the pin or ball to move into the open position when the coupler is engaged. This balance is achieved through careful material selection and spring rate calibration. Common materials used for these springs include stainless steel and carbon steel, chosen for their durability and ability to withstand the pressures and temperatures encountered in various applications.
When the quick disconnect is connected, the force applied by the user compresses the spring, allowing the pin or ball to move and seal against the coupling's internal surface. This action creates a tight, temporary seal, ensuring that no fluid or gas escapes until the coupler is intentionally disconnected. The spring's bias then takes over, pushing the pin or ball back into the closed position, ready for the next connection.
The spring-loaded mechanism's design also considers the ease of disconnection. When the coupler is disconnected, the spring's force acts to quickly and reliably open the pin or ball, allowing the connection to be released without the need for excessive force. This feature is particularly useful in applications where frequent connections and disconnections are required, such as in fuel systems for vehicles or industrial machinery.
Optimizing Performance: Choosing the Right Fuel Line Size for Your 3/8 Inline Filter
You may want to see also
Pressure Release: Built-in pressure relief valves prevent damage during disconnection by releasing excess pressure
Quick disconnect couplers are an essential component in fuel line systems, providing a convenient and efficient way to connect and disconnect fuel sources. One of the key features that ensures the longevity and reliability of these couplers is the built-in pressure relief valves. These valves play a critical role in preventing potential damage that could occur during the disconnection process.
When a fuel line is disconnected, there is often a sudden release of pressure, which can be significant, especially in high-pressure fuel systems. This rapid pressure release can lead to several issues, including the formation of air bubbles, which can cause cavitation and damage to the fuel pump and other components. To mitigate these risks, quick disconnect couplers are equipped with pressure relief valves that act as a safety mechanism.
The pressure relief valves are designed to open and release excess pressure when the fuel line is disconnected. This action allows the pressure to dissipate safely, preventing any sudden and potentially harmful spikes. As a result, the fuel pump and other connected components are protected from the adverse effects of rapid pressure changes. The valves are typically made of durable materials that can withstand the high-pressure environment, ensuring their effectiveness over time.
During the disconnection process, the coupler's mechanism triggers the pressure relief valves. This can be achieved through various designs, such as a spring-loaded valve that opens when the fuel line is pulled away or a solenoid-operated valve that responds to electrical signals. The valves' response time is crucial, as it needs to be fast enough to prevent any significant pressure buildup. Once the fuel line is disconnected, the valves close, sealing the system and maintaining the integrity of the fuel supply.
In summary, the built-in pressure relief valves in quick disconnect couplers are a vital safety feature. They ensure that the fuel system remains protected even during the disconnection process, which can be a critical aspect of maintaining the overall health and longevity of the fuel line and associated components. Understanding and appreciating the role of these valves can help users and maintenance personnel appreciate the importance of proper installation and care of quick disconnect couplers.
Trailblazer Fuel Line: Unveiling the 2000 Model's Mystery
You may want to see also
Material and Durability: Couplers are made from durable materials like brass or stainless steel for long-lasting performance
The construction of fuel line quick disconnect couplers is a critical aspect of their functionality and longevity. These couplers are designed with durability in mind, ensuring they can withstand the rigors of everyday use in automotive applications. The primary materials used for these couplers are brass and stainless steel, both renowned for their exceptional properties.
Brass, an alloy of copper and zinc, offers a unique combination of strength and malleability. It is highly resistant to corrosion, making it ideal for fuel line couplers as it can withstand the corrosive effects of gasoline and diesel. Additionally, brass's malleable nature allows for easier manufacturing, enabling the creation of intricate designs and precise connections. This material is often preferred for its cost-effectiveness and ease of maintenance, ensuring that the coupler remains reliable over extended periods.
Stainless steel, on the other hand, is an alloy of iron, chromium, and other elements. Its primary advantage is its superior corrosion resistance, making it an excellent choice for fuel lines that carry corrosive fuels. Stainless steel couplers are known for their exceptional strength and durability, capable of withstanding high-pressure environments without compromising performance. This material is often more expensive than brass but is highly valued for its longevity and resistance to wear and tear, ensuring a long service life even in demanding conditions.
The choice of material significantly impacts the overall performance and reliability of quick disconnect couplers. By utilizing brass or stainless steel, manufacturers ensure that these couplers can maintain a tight seal, preventing fuel leaks and ensuring efficient fuel transfer. The durability of these materials also means that the couplers can withstand frequent connections and disconnections without showing signs of wear, providing a reliable and consistent performance over the life of the vehicle.
In summary, the use of durable materials like brass and stainless steel in fuel line quick disconnect couplers is essential for their long-term performance and reliability. These materials offer the necessary strength, corrosion resistance, and malleability to ensure a secure and efficient connection, contributing to the overall safety and efficiency of fuel systems in various vehicles.
Mercury Outboard Fuel Line Sizing: 1992 150 HP Guide
You may want to see also
Sealing Technology: Advanced sealing materials ensure a tight connection, preventing fuel leaks and contamination
The heart of any fuel line quick disconnect coupler's functionality lies in its sealing mechanism, which employs advanced sealing materials to ensure a tight and secure connection. This critical component is designed to prevent fuel leaks and contamination, which could have severe consequences for the engine's performance and longevity. The sealing technology used in these couplers is a sophisticated process that involves the careful selection and application of specific materials to create a robust and reliable seal.
Advanced sealing materials, such as fluoropolymers, rubber compounds, and silicone-based gaskets, are utilized to create a tight seal between the male and female connectors. These materials are engineered to provide excellent resistance to fuel chemicals, temperature fluctuations, and mechanical stress, ensuring that the connection remains secure and leak-free. The design of the sealing surface is crucial; it often features a series of intricate grooves, ridges, or textured patterns that increase the surface area in contact, thereby enhancing the sealing effect.
One of the key advantages of modern sealing technology is the ability to maintain a tight seal even under high-pressure conditions. This is particularly important in fuel systems, where fuel is often under pressure to ensure efficient delivery to the engine. The sealing materials are chosen for their ability to withstand these pressures without compromising the integrity of the seal, thus preventing any potential fuel loss or contamination.
Furthermore, the sealing technology in quick disconnect couplers often incorporates a self-cleaning mechanism. This feature helps to maintain the seal's effectiveness by preventing the accumulation of dirt, debris, or fuel residue, which could otherwise weaken the seal over time. The design may include a slight angle or a series of small channels that direct any contaminants away from the sealing area, ensuring a clean and reliable connection.
In summary, the sealing technology in fuel line quick disconnect couplers is a critical aspect that ensures the safe and efficient operation of fuel systems. By utilizing advanced sealing materials and innovative design features, these couplers provide a tight, leak-resistant connection, contributing to the overall reliability and performance of the engine. This level of sealing technology is essential in maintaining the integrity of the fuel supply, preventing potential engine damage, and ensuring a smooth and efficient power delivery.
Propane Engine Fueling: Rubber Fuel Line Compatibility Explained
You may want to see also
Safety Features: Quick disconnects often include safety locks to prevent accidental disconnections during operation
Quick disconnect couplers are essential components in fuel line systems, offering a convenient and efficient way to connect and disconnect fuel sources without the need for complex threading or welding. These couplers are designed with a focus on safety, ensuring that fuel lines remain secure and leak-free during operation. One of the key safety features of quick disconnect couplers is the inclusion of safety locks or mechanisms.
These safety locks are typically designed to engage when the coupler is fully connected, creating a secure physical barrier that prevents accidental disconnections. When the fuel line is properly attached, the safety lock mechanism locks into place, ensuring that the connection cannot be accidentally pulled apart. This is particularly important in high-pressure fuel systems, where the force of a disconnection could lead to fuel spillage, potential fire hazards, or damage to the fuel system components.
The design of these safety locks varies depending on the manufacturer and the specific application. Some couplers use a simple pin or clip that slides into a slot when the coupler is connected, while others employ more complex cam-lock systems. In some cases, the safety lock may be integrated into the quick disconnect mechanism itself, ensuring that the fuel line remains secure as long as the coupler is properly engaged.
To ensure the safety of your fuel system, it is crucial to understand and follow the manufacturer's instructions regarding the use of quick disconnect couplers. This includes properly aligning the fuel line and coupler, engaging the safety lock mechanism, and avoiding any force that could potentially dislodge the connection. Regular inspection of the coupler and fuel line connections is also recommended to identify any signs of wear or damage that may compromise the safety of the system.
In summary, quick disconnect couplers are designed with safety in mind, incorporating safety locks to prevent accidental disconnections. These locks are a critical component in maintaining the integrity of fuel lines and ensuring the overall safety of the fuel system. By understanding and properly utilizing these safety features, users can operate their fuel systems with confidence, knowing that the quick disconnect couplers provide a secure and reliable connection.
Black Smoke: Fuel Line Obstruction's Impact on Engine Performance
You may want to see also
Frequently asked questions
A fuel line quick disconnect coupler is a specialized fitting designed to securely and quickly connect and disconnect fuel lines. It allows for easy and efficient fueling of vehicles, especially in situations where frequent fueling is required, such as in racing or emergency response scenarios.
These couplers utilize a locking mechanism, often a bayonet or a twist-lock design, to create a tight seal between the fuel line and the coupler. When connected, the locking mechanism ensures that the fuel line is firmly attached, preventing any leaks or spills. The connection is typically made by inserting the fuel line into the coupler and rotating it until the locking mechanism engages.
Absolutely! Safety is a critical aspect of these couplers. They are designed with overfill protection to prevent excessive fuel from being dispensed, which could lead to engine damage. Additionally, some couplers have a built-in pressure relief valve to release any built-up pressure in the fuel line, ensuring safe operation. It is essential to inspect the coupler for any signs of damage or wear before and after each use to maintain safety standards.