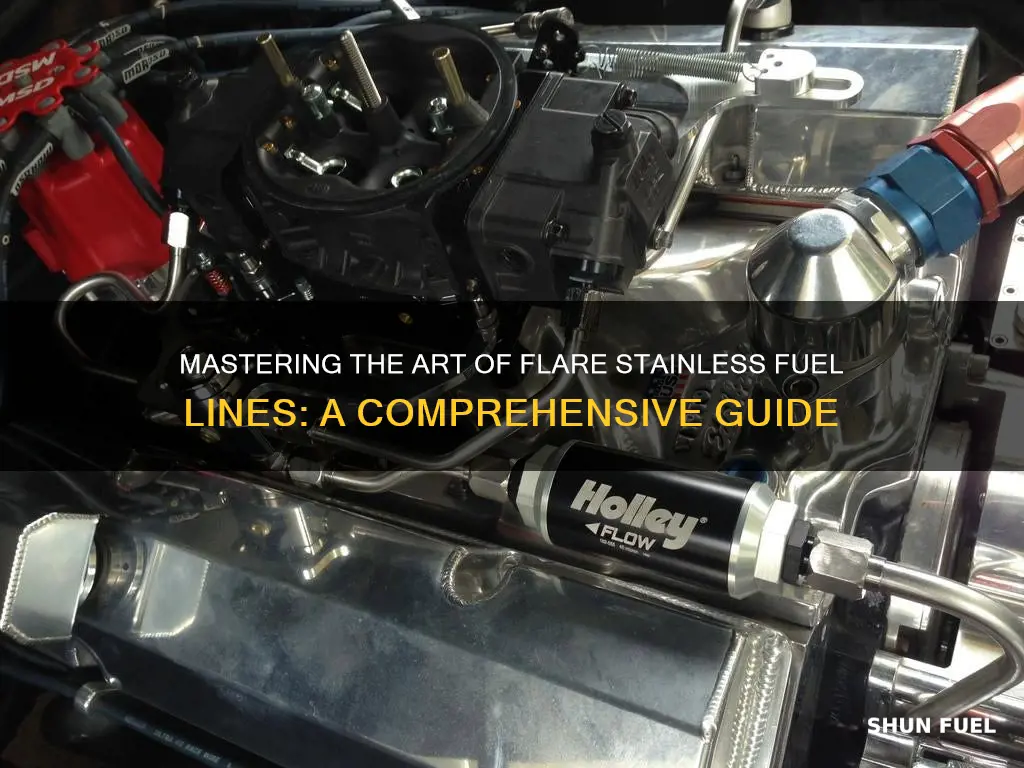
Flaring a stainless fuel line is a crucial process in ensuring the safe and efficient operation of fuel systems. This technique involves creating a controlled flame to remove excess fuel and prevent potential hazards. By following a step-by-step guide, you can master the art of flaring, ensuring a secure and effective method for managing fuel lines. This process is essential for maintaining the integrity of the fuel system and preventing potential fires or explosions.
What You'll Learn
- Prepare Tools: Gather necessary tools like flare guns, dies, and cleaning supplies
- Clean Line: Ensure the fuel line is free of debris and contaminants before flaring
- Measure and Mark: Accurately measure and mark the flare points on the fuel line
- Prepare Flare Gun: Adjust the flare gun to the appropriate size and angle for the job
- Flare and Secure: Carefully flare the fuel line, ensuring a tight seal, and secure it in place
Prepare Tools: Gather necessary tools like flare guns, dies, and cleaning supplies
When preparing to flare a stainless steel fuel line, it's crucial to have the right tools and equipment to ensure a successful and safe process. Here's a detailed guide on gathering the necessary tools:
Flaring Tools:
- Flare Guns: Invest in a high-quality flare gun specifically designed for stainless steel applications. Look for a gun with adjustable force settings to accommodate different thicknesses of fuel lines. Ensure it has a sturdy build and a comfortable grip for precision control during the flaring process.
- Dies: Flare dies are essential for creating the flare. Obtain a set of dies with various sizes and angles to accommodate different fuel line diameters and desired flare configurations. Common flare types include 45-degree, 60-degree, and 90-degree bends. Select dies made from durable materials like hardened steel to ensure longevity.
Additional Equipment:
- Cleaning Supplies: Maintain a clean work environment and fuel lines. Gather cleaning tools such as brushes, compressed air, and cleaning solvents. Remove any dirt, debris, or contaminants from the fuel line before flaring to ensure a strong bond during the welding process.
- Safety Gear: Prioritize safety by wearing appropriate personal protective equipment (PPE). This includes heat-resistant gloves, safety goggles, and a respirator to protect against fumes. Ensure you have a well-ventilated workspace to minimize exposure to potentially harmful substances.
- Welding Equipment: If you plan to use a welding process for the flare, gather the necessary welding gear. This may include a welding torch, shielding gas, and a welding helmet. Ensure you are familiar with welding techniques and safety protocols before proceeding.
Having these tools and equipment ready will ensure a well-prepared and efficient flaring process. It is essential to inspect and test the tools before use to guarantee their functionality and accuracy. Proper preparation will contribute to a successful and safe fuel line flare.
Understanding Jeep's Dual Action Fuel Pump: The Double Line Advantage
You may want to see also
Clean Line: Ensure the fuel line is free of debris and contaminants before flaring
Before you begin the flaring process for your stainless fuel line, it is crucial to ensure that the line is clean and free of any debris or contaminants. This step is often overlooked but is essential for a successful and safe flare job. Here's a detailed guide on how to achieve a clean fuel line:
Step 1: Identify the Fuel Line and Its Connections: Locate the stainless fuel line that you intend to flare. Make a note of any connections, fittings, or valves associated with this line. Understanding the layout will help you plan the cleaning process effectively.
Step 2: Remove Obstructions and Debris: Start by physically removing any visible debris or obstructions from the fuel line. This might include dirt, rust, or any foreign matter that has accumulated over time. Use a small brush or a compressed air gun to gently clean the interior of the line, ensuring you reach all areas. Pay close attention to bends and tight spaces where debris can hide.
Step 3: Flush the Line: After removing visible contaminants, it's time to flush the fuel line thoroughly. You can use a cleaning solution specifically designed for fuel lines, or a mixture of vinegar and water. Insert a cleaning wand or a small hose into one end of the line and flush it with the cleaning solution. This process helps to dislodge any remaining particles and ensures a clean surface for flaring. Make sure to follow the manufacturer's instructions for the cleaning agent and flush the line multiple times to ensure effectiveness.
Step 4: Inspect and Verify: Once the flushing process is complete, inspect the fuel line carefully. Check for any remaining debris, rust, or signs of contamination. Use a magnifying glass or a flashlight to ensure you don't miss any small particles. If any contaminants are found, repeat the cleaning process until the line is completely clear. This step is critical to ensure the longevity and performance of your flare job.
Step 5: Prepare for Flaring: After confirming that the fuel line is clean, you are now ready to proceed with the flaring technique. Ensure that all connections and fittings are also cleaned and free of any corrosion. This preparation ensures a smooth and successful flare, minimizing the risk of any issues during the process.
By following these steps, you can guarantee that your stainless fuel line is in optimal condition before flaring, leading to a more efficient and reliable system. Remember, taking the time to clean the line is an essential part of the process and will contribute to the overall success of your project.
Galvanized Piping: A Hazardous Choice for Diesel Fuel Lines
You may want to see also
Measure and Mark: Accurately measure and mark the flare points on the fuel line
To ensure a precise and successful flare job on your stainless fuel line, the initial step is to measure and mark the flare points accurately. This process is crucial as it guides the flaring process and ensures a tight, leak-free connection. Here's a detailed guide on how to measure and mark these flare points:
- Gather the Necessary Tools: Before you begin, ensure you have the right tools for the job. You'll need a tape measure, a pencil or marker, and a straight edge or ruler. Additionally, having a flare gauge can be helpful for double-checking the flare size.
- Locate the Flare Points: Identify the sections of the fuel line where you need to flare. Typically, these are the areas where the line connects to various components like the fuel tank, engine, or other accessories. Mark these points clearly with temporary markers or tape to ensure you don't miss any.
- Measure the Flare Length: Use your tape measure to determine the length of the flare required. The standard flare length for stainless steel fuel lines is usually around 1.5 to 2 inches, but this can vary depending on the application and local regulations. Measure from the end of the fuel line to the desired flare point, ensuring you include the length of the flare itself.
- Mark the Flare Points: With the flare length measured, mark the flare points on the fuel line. Use a pencil or marker to draw a line along the fuel line, starting from the end and moving towards the flare point. Ensure the line is straight and follows the measured length. You can also use a straight edge to guide your marking for added precision.
- Verify the Marks: Double-check your measurements and marks to ensure accuracy. Measure the marked length again to confirm it matches your initial measurement. This step is crucial to avoid any mistakes during the flaring process, which could lead to an improper fit or potential leaks.
- Consider the Material: When marking, keep in mind the type of stainless steel you are working with. Different grades of stainless steel may have slightly different properties, and this can influence the flare length and technique. Always refer to the manufacturer's guidelines or consult a professional if you're unsure about specific requirements for your material.
Accurate measurement and marking are fundamental to the success of your flaring project. Taking the time to get these steps right will result in a professional-looking connection that functions efficiently and safely.
Mastering the Art of Fuel Line Flare: A Comprehensive Guide
You may want to see also
Prepare Flare Gun: Adjust the flare gun to the appropriate size and angle for the job
When preparing to flare a stainless fuel line, it's crucial to ensure that your flare gun is properly adjusted to the specific requirements of the task at hand. This initial step is fundamental to achieving a successful and secure flare connection. Here's a detailed guide on how to adjust your flare gun for the job:
Assess the Line Diameter: Begin by examining the diameter of the stainless fuel line you intend to flare. Different flare guns are designed to work with various pipe sizes. Most flare guns have adjustable jaws or a range of sizes they can accommodate. Select the appropriate size that matches or slightly exceeds the diameter of your fuel line. This ensures a snug fit and prevents the flare from becoming too tight or too loose.
Adjust the Angle: The angle of the flare gun is another critical factor. The flare angle should match the desired flare style, which is typically a 45-degree angle for most applications. However, some systems might require a different angle, such as a 30-degree or 60-degree flare. Adjust the flare gun's angle until it aligns with the required measurement. This adjustment ensures that the flare is formed correctly and adheres to industry standards.
Practice and Precision: Before proceeding with the actual flaring, practice on a scrap piece of the same material to get a feel for the process. This practice will help you understand the force and technique required for the job. Precision is key; make small adjustments to the flare gun's position and pressure to achieve the desired flare shape. This step is essential to ensure the flare is clean, smooth, and free of any sharp edges that could compromise the connection's integrity.
Consider the Material: Stainless steel fuel lines may require slightly different techniques compared to other materials. The material's properties can influence the force and angle needed for a successful flare. Always refer to the manufacturer's guidelines or consult with experts if you're unsure about the specific requirements for your project.
By carefully adjusting the flare gun to match the line diameter and desired flare angle, you set the foundation for a successful and reliable flare connection. This attention to detail ensures the safety and efficiency of your fuel line system.
Fuel Line Disconnect: 2007 F-150 Guide
You may want to see also
Flare and Secure: Carefully flare the fuel line, ensuring a tight seal, and secure it in place
Flare and Secure: A Step-by-Step Guide to Flare and Secure a Stainless Fuel Line
Flare and secure a stainless fuel line is a crucial process in ensuring a tight seal and proper installation. Here's a detailed guide to help you through the process:
Preparation: Before you begin, ensure you have the necessary tools and materials, including the fuel line, flare tool, and appropriate flare nuts and washers. Clean the fuel line and the flare surfaces to remove any debris or contaminants. This step is essential for a proper connection.
Flare Process: Start by positioning the fuel line securely in the flare tool. The flare tool should be the correct size for the fuel line diameter. Apply firm pressure to the flare tool, ensuring the line is centered and aligned with the tool's jaws. Hold the pressure for the recommended time, typically a few seconds, allowing the metal to deform and create a tight seal. The flare should be a smooth, continuous curve without any sharp bends.
Ensuring a Tight Seal: After flaring, inspect the connection. The flare should be smooth and free of any sharp edges. Use a flare gauge or caliper to measure the flare depth, ensuring it meets the required specifications. A tight seal is crucial to prevent fuel leaks. If the flare is not tight enough, repeat the process, applying more pressure and holding it for a slightly longer duration.
Securing the Connection: Once you're satisfied with the flare, secure it in place. Tighten the flare nut and washer by hand, ensuring they are properly aligned. Use a wrench to tighten the nut further, but be careful not to overtighten, as this can damage the flare. The connection should be snug, but not overly tight, allowing for some flexibility.
Final Checks: After securing the flare, perform a visual inspection to ensure there are no visible signs of damage or distortion. Check for any leaks by applying a small amount of fuel to the connection and observing for any drips. If everything appears secure and leak-free, your flare and secure process is complete.
Remember, practice and attention to detail are key when flaring stainless fuel lines. Take your time, follow the manufacturer's guidelines, and ensure each step is executed precisely for a reliable and safe fuel system.
DUCATI MONSTER Fuel Line Maintenance: A Step-by-Step Guide
You may want to see also
Frequently asked questions
Flaring is a process used to create a smooth, controlled bend in a fuel line, which helps to prevent sharp turns and potential damage to the line. It also improves the flow of fuel and reduces the risk of leaks.
Stainless steel is an ideal material for fuel lines due to its durability, corrosion resistance, and ability to withstand high temperatures. It ensures a long-lasting and reliable fuel delivery system.
Before flaring, ensure the line is clean and free of any debris. Use a fuel line cleaner or a mild detergent to remove any contaminants. Then, cut the line to the desired length and ensure the ends are smooth and free of any sharp edges.
You will need a flaring tool or a mandrel bending machine, depending on the size and complexity of the bend. A heat source, such as a torch, may also be required to soften the metal and make the bending process easier.
Absolutely! Always work in a well-ventilated area and wear protective gear, including heat-resistant gloves and safety goggles. Be cautious when using heat sources and ensure you have a fire extinguisher nearby. It's crucial to follow safety guidelines to prevent accidents and injuries.