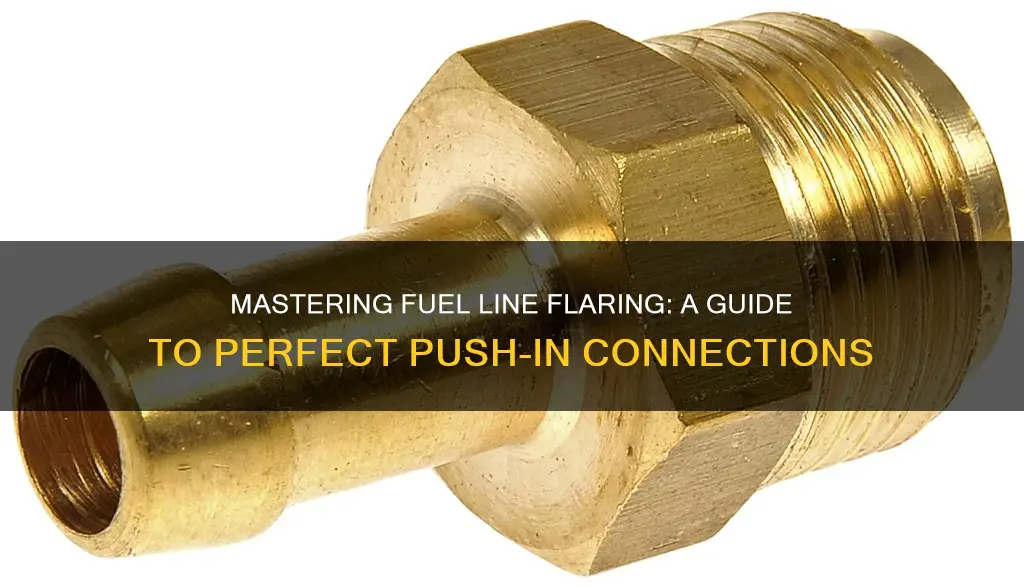
Flaring fuel lines for a push-in connector is a crucial step in ensuring a secure and reliable fuel system in vehicles. This process involves shaping the end of the fuel line to create a precise fit with the connector, allowing for a tight seal and preventing fuel leaks. By following a series of steps, including preparing the fuel line and connector, using the right tools, and applying the correct techniques, you can achieve a professional-grade flare that meets industry standards. This guide will provide a detailed overview of the process, ensuring that you can effectively flare fuel lines and maintain a safe and efficient fuel system in your vehicle.
What You'll Learn
- Prepare Tools: Gather necessary tools: fuel line, push-in connector, crimping tool, and fuel line cleaner
- Clean Line: Ensure fuel line is clean and free of debris using fuel line cleaner
- Connect Line: Slide fuel line into connector, ensuring proper alignment and size match
- Crimp Connection: Use crimping tool to secure connector firmly onto fuel line
- Test Connection: Verify connection by checking for leaks and proper fuel flow
Prepare Tools: Gather necessary tools: fuel line, push-in connector, crimping tool, and fuel line cleaner
Before you begin the process of flaring a fuel line for a push-in connector, it's crucial to ensure you have all the necessary tools and materials ready. This preparation will make the task more efficient and help you avoid any unnecessary complications. Here's a detailed guide on what you need to gather:
Fuel Line: The primary component you'll be working with is the fuel line itself. It's essential to choose the correct size and type of fuel line that matches your vehicle's specifications. Ensure it is in good condition and free from any damage or leaks. Having a spare length of fuel line can be beneficial in case adjustments are needed during the process.
Push-In Connector: This connector is designed to securely attach the fuel line to the vehicle's fuel system. Select a connector that is compatible with your fuel line size and vehicle's requirements. Push-in connectors typically have a flared end that fits over the fuel line, creating a tight seal. Make sure you have the appropriate size to accommodate your fuel line.
Crimping Tool: A crimping tool is essential for creating a secure connection between the fuel line and the push-in connector. This tool will compress the connector onto the fuel line, ensuring a leak-proof seal. Look for a crimping tool that is compatible with the connector type you've chosen. It should provide enough force to create a reliable connection without damaging the fuel line.
Fuel Line Cleaner: Cleaning the fuel line and the connector is a critical step to ensure a proper connection. Fuel line cleaner is used to remove any contaminants, such as dirt, grease, or old fuel residue, that might interfere with the sealing process. It helps create a clean and smooth surface for the connector to flare onto the fuel line. Ensure you have a sufficient supply of cleaner to cover the entire length of the fuel line you intend to work on.
Having these tools and materials ready will set you up for a successful flaring process. It's always a good practice to double-check the compatibility of the connectors and fuel lines with your vehicle's specifications to ensure a safe and effective repair or modification.
Wind Chill's Impact: Protecting Fuel Lines from Frost
You may want to see also
Clean Line: Ensure fuel line is clean and free of debris using fuel line cleaner
To ensure optimal performance and longevity of your fuel system, it's crucial to maintain a clean fuel line, especially when dealing with push-in connectors. Over time, fuel lines can accumulate debris, contaminants, and varnish, which can lead to reduced fuel flow, engine performance issues, and even potential damage to the fuel system. Here's a step-by-step guide on how to ensure your fuel line is clean and free of debris using fuel line cleaner:
Step 1: Prepare the Necessary Tools and Materials:
Before you begin, gather the required tools and materials. You will need a fuel line cleaner, preferably a specialized cleaner designed for fuel systems. Common choices include fuel system cleaners or ethanol-free gasoline. Additionally, have a fuel line brush, a funnel, and a container for the cleaner. Ensure you have the necessary safety gear, such as gloves and eye protection, to avoid any skin or eye irritation during the cleaning process.
Step 2: Locate the Fuel Line:
Identify the fuel line that connects to the push-in connector. This line typically runs from the fuel tank to the engine. Carefully inspect the fuel line for any visible signs of contamination, such as varnish or debris buildup. Take note of any restrictions or bends in the line, as these areas may require extra attention during cleaning.
Step 3: Drain the Fuel Line (Optional but Recommended):
For optimal cleaning, consider draining the fuel line to remove any contaminants that may have settled at the bottom. This step is especially important if the fuel line has been idle for an extended period. Locate the fuel drain valve, usually found near the fuel tank, and open it to allow the fuel to drain into a suitable container. Once drained, close the valve and prepare for the cleaning process.
Step 4: Apply the Fuel Line Cleaner:
Pour the recommended amount of fuel line cleaner into the fuel line using a funnel to ensure it reaches all areas. Start at the push-in connector and work your way along the fuel line, allowing the cleaner to sit for the specified time according to the product instructions. This process helps to dissolve and loosen any debris or varnish.
Step 5: Brush and Rinse:
Using the fuel line brush, gently scrub the inside of the fuel line to dislodge any stubborn debris. Pay attention to the areas where the line bends or has restrictions. After brushing, rinse the fuel line with clean fuel or water to remove the cleaner and any dislodged contaminants. Ensure that no debris or cleaner residue remains inside the line.
Step 6: Reassemble and Test:
Once the cleaning process is complete, reassemble the fuel line and push-in connector. Start the engine and monitor its performance. Listen for any unusual noises and check for proper fuel flow. If the engine runs smoothly and efficiently, your fuel line cleaning was successful. If any issues persist, further investigation may be required.
Remember, regular maintenance and cleaning of the fuel line can prevent potential problems and ensure your engine operates at its best. Always follow the manufacturer's guidelines for your specific fuel system and cleaner product.
Is Your Car's Fuel Line Clogged? Signs and Solutions
You may want to see also
Connect Line: Slide fuel line into connector, ensuring proper alignment and size match
When connecting a fuel line to a push-in connector, it's crucial to ensure a secure and reliable attachment. Here's a step-by-step guide to help you achieve this:
Start by preparing the fuel line and connector. Slide the fuel line into the connector, ensuring that it is aligned properly. The fuel line should fit snugly into the connector's opening, with no gaps or misalignment. Check the size of the fuel line and connector to ensure they match. If the fuel line is too large, it may not fit properly, and if it's too small, it might not provide a secure connection.
Gently push the fuel line into the connector until it is fully inserted. Apply even pressure to ensure a tight fit. You should feel a slight resistance when the fuel line is fully seated. Avoid forcing the fuel line, as this can damage the connector or the fuel line itself. Take your time and ensure a proper connection.
Once the fuel line is inserted, check for any signs of leakage. Tighten the connector's locking mechanism, if present, to ensure a secure seal. This step is essential to prevent fuel leaks and ensure the safety of your vehicle. Make sure the connector is properly tightened without over-tightening, as this can damage the fuel line or connector.
After the connection is made, inspect the assembly for any visible damage or imperfections. Ensure that the fuel line is not kinked or pinched, as this can affect the flow of fuel and potentially cause issues. A proper connection should allow for smooth fuel flow without any restrictions.
Remember, taking the time to align and insert the fuel line correctly is essential for a reliable and safe fuel system. Always refer to the manufacturer's guidelines for specific instructions, as different connectors may have unique requirements.
Unclog Fuel Lines: The Ultimate Gas Additive Guide
You may want to see also
Crimp Connection: Use crimping tool to secure connector firmly onto fuel line
When it comes to connecting fuel lines to a push-in connector, a secure and reliable crimp connection is essential to ensure optimal performance and safety. This method involves using a crimping tool to firmly attach the connector to the fuel line, creating a strong and permanent bond. Here's a step-by-step guide to achieving a successful crimp connection:
Preparation: Begin by gathering the necessary tools and materials. You'll need a crimping tool specifically designed for the type of connector you're using, along with the appropriate-sized crimping dies. Ensure that the fuel line is clean and free of any debris or contaminants. Prepare the connector by cleaning it and ensuring it is free of any damage or debris that might interfere with the crimping process.
Crimping Process: Locate the crimping area on the connector, which is typically a raised section or a series of notches. Take the fuel line and insert it into the connector, ensuring it is aligned properly. Apply firm pressure to the crimping tool, positioning it over the crimping area. Squeeze the tool's handles together, applying force evenly and firmly. The goal is to create a visible deformation on the connector, indicating a successful crimp. Repeat this process for each connector you need to attach.
Finishing Touches: After crimping all the connectors, inspect the connections for any signs of damage or imperfections. Ensure that the fuel line is securely held in place and that there are no gaps or spaces between the connector and the line. If any adjustments are needed, carefully use the crimping tool to refine the crimp, ensuring a neat and precise connection.
Safety and Quality Control: Crimp connections should be performed with precision to guarantee a tight and secure bond. Inadequate crimping may result in fuel leaks, which can be dangerous and cause engine performance issues. Always follow the manufacturer's guidelines for the specific connector and fuel line you are working with. Regularly inspect the crimp connections during and after the installation process to ensure they remain intact and functional.
By following these steps and paying attention to detail, you can create a robust crimp connection for your fuel line and push-in connector, ensuring a reliable and safe fuel system. Remember, proper crimping is a critical aspect of maintaining the integrity of your vehicle's fuel system.
Cub 3235 Fuel Line Size: Expert Guide
You may want to see also
Test Connection: Verify connection by checking for leaks and proper fuel flow
When you've completed the flaring process for your fuel line and push-in connector, it's crucial to verify the connection to ensure it's secure and leak-free. This step is essential to prevent fuel leaks, which can be dangerous and cause engine issues. Here's a detailed guide on how to test the connection:
Leak Testing:
- Start by applying a small amount of soapy water or a fuel-safe leak detection fluid around the connection area. Common choices include dish soap or a specialized fuel line leak detection kit.
- Inspect the connection thoroughly. Look for any bubbles forming on the surface, which indicate a potential leak. Pay close attention to the flare and the connector, as these areas are critical.
- If you notice bubbles, it's a clear sign of a leak. Disassemble the connection and re-flare the fuel line if necessary. Ensure you follow the manufacturer's instructions for flaring.
- For added safety, you can also use a pressure gauge to check for leaks. Connect the gauge to the fuel line and apply pressure. If there's a leak, you'll hear hissing or see bubbles.
Fuel Flow Verification:
- After ensuring there are no leaks, it's time to check the fuel flow. Start the engine and allow it to idle.
- Monitor the fuel gauge to ensure it's steady and within the expected range. A properly connected fuel line should provide a consistent fuel supply to the engine.
- Listen for any unusual noises, such as hissing or roaring, which could indicate a restriction or leak in the system.
- If the engine is equipped with a fuel pressure gauge, check the reading. It should be within the specified range for your vehicle.
- If the fuel flow seems inconsistent or the engine stalls, it might indicate a problem with the connection or the fuel line itself. In this case, further investigation is required.
Remember, proper flaring and connection verification are critical to maintaining a safe and efficient fuel system in your vehicle. Always refer to the manufacturer's guidelines for specific instructions and safety precautions.
Mastering the Art of Cutting PTFE Fuel Lines: A Comprehensive Guide
You may want to see also
Frequently asked questions
A push-in connector is a type of fuel line fitting designed for a quick and secure connection. It features a cylindrical body with a spring-loaded collar that expands when the fuel line is inserted, creating a tight seal. This connector is commonly used in fuel systems to join fuel lines to fuel tanks, pumps, or other components.
Before connecting, ensure the fuel line is clean and free of any debris or contaminants. Use a fuel line cleaner or a solvent-based cleaner to remove any old fuel or deposits. Cut the fuel line to the appropriate length, typically leaving a few inches extra for the connector. Then, deburr the end of the fuel line to create a smooth surface for a proper connection.
Start by aligning the fuel line with the connector's center. Push the fuel line into the connector until the end of the line is flush with the connector's base. Ensure the line is fully seated by checking if there is a visible gap between the line and the connector's collar. If not, the connector might need to be tightened slightly, but be careful not to overtighten to avoid damage.
While you can install a push-in connector by hand, using a fuel line crimping tool can make the process easier and ensure a secure connection. This tool helps to apply the necessary force to the connector, expanding the collar and creating a tight seal. It's important to follow the manufacturer's instructions for the specific tool and connector type you are using.