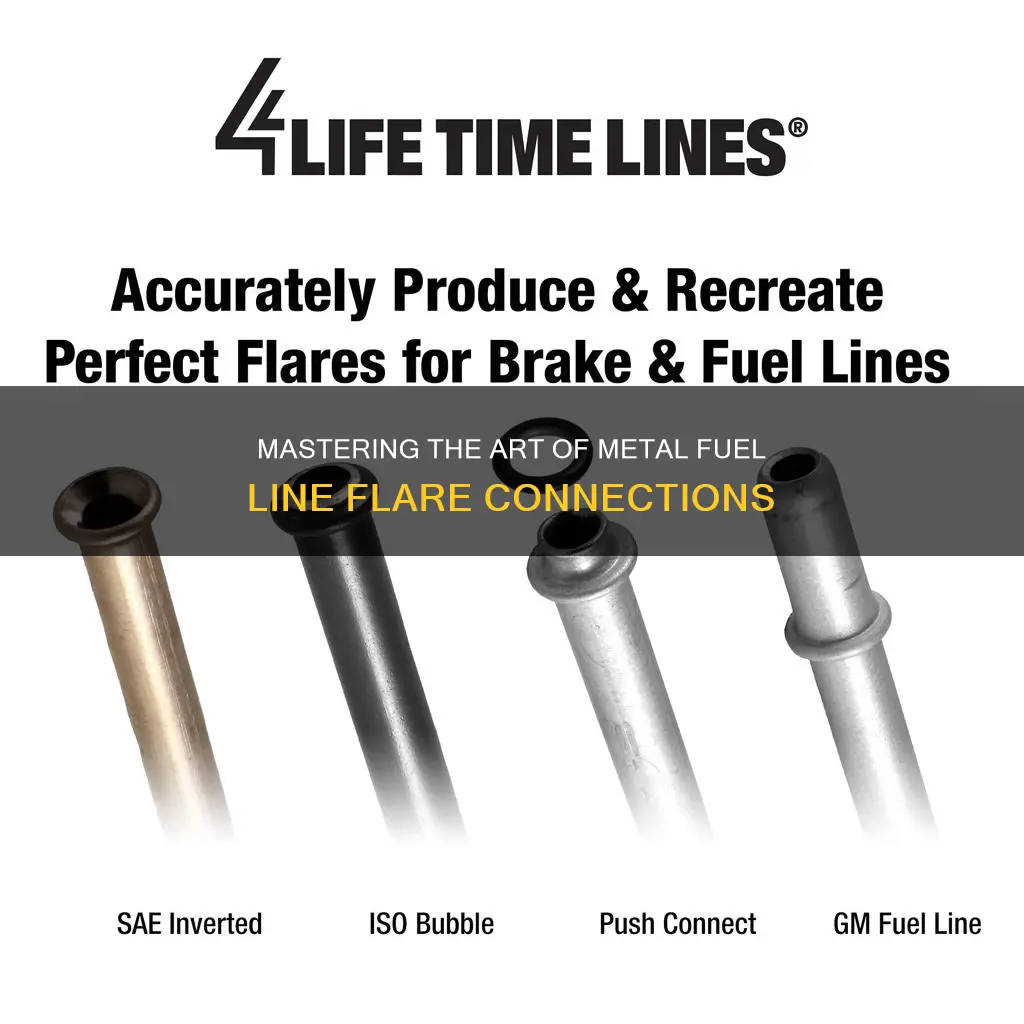
Flaring a metal fuel line is a crucial process in ensuring a safe and efficient fuel system in various applications, from automotive to industrial settings. This technique involves creating a controlled burn at the end of the fuel line to prevent fuel leaks and ensure a secure connection. The process requires precision and knowledge of the specific tools and techniques to achieve a successful flare. This guide will provide a step-by-step approach to mastering the art of flaring a metal fuel line, covering essential safety measures, equipment, and the flare creation process.
What You'll Learn
- Preparation: Gather tools: fuel line flare kit, torque wrench, safety gear
- Line Inspection: Ensure line is straight, free of damage, and clean
- Flaring Tool: Select appropriate flare tool for line size
- Flare Process: Follow steps: cut, deburr, flare, inspect, torque
- Safety Measures: Wear protective gear, work in well-ventilated area, follow manufacturer guidelines
Preparation: Gather tools: fuel line flare kit, torque wrench, safety gear
Before you begin the process of flaring a metal fuel line, it's crucial to ensure you have the necessary tools and safety equipment. This preparation step is essential to guarantee a safe and successful outcome. Here's a detailed guide on what you need to gather:
Fuel Line Flare Kit: This is the primary tool you'll use for the flaring process. A fuel line flare kit typically includes a variety of flare dies, which are designed to create a smooth and secure connection between the fuel line and the fitting. The kit should have different sizes and types of flare dies to accommodate various fuel line diameters and fitting types. Make sure to inspect the kit for any signs of damage or wear, and replace it if necessary.
Torque Wrench: A torque wrench is an essential tool for applying the correct amount of force during the flaring process. It ensures that the flare is tightened to the manufacturer's specifications, providing a secure and reliable connection. You should have a torque wrench that covers the range of torque values required for your specific fuel line and fitting. Calibrate the torque wrench if needed to ensure accurate readings.
Safety Gear: Working with metal fuel lines can involve potential hazards, so it's imperative to prioritize safety. Here's what you should consider:
- Goggles: Protect your eyes from any potential sparks, debris, or fuel splashes. Choose safety goggles that fit comfortably and provide adequate coverage.
- Glove: Wear heat-resistant gloves to protect your hands from burns and to provide a better grip during the flaring process.
- Respiratory Protection: If you're working in an enclosed area or with fuel, consider a respirator to avoid inhaling fumes.
- Earmuffs or Earplugs: Protect your hearing from any loud noises that may occur during the work.
Having these tools and safety gear ready will ensure that you are well-prepared for the flaring process, allowing you to work efficiently and safely. It's always better to be over-prepared when dealing with potential hazards.
Fuel Line Disconnect: A Step-by-Step Guide to Removing Injectors Safely
You may want to see also
Line Inspection: Ensure line is straight, free of damage, and clean
When inspecting a metal fuel line, it's crucial to ensure it is in optimal condition to prevent any potential issues. Here's a step-by-step guide to inspecting the line:
- Visual Inspection: Begin by visually examining the fuel line. Look for any visible signs of damage, such as cracks, corrosion, or bends. Check for any signs of wear and tear, especially at the connections and fittings. Ensure that the line is not kinked or twisted, as this can affect its functionality. A straight and intact line is essential for efficient fuel delivery.
- Straightness and Alignment: Verify that the fuel line is straight and properly aligned. It should follow a smooth path from the fuel source to the engine. Any deviations or sharp bends can restrict fuel flow and potentially cause damage over time. Use a straightedge or a ruler to measure and ensure the line's straightness, especially at critical points like the engine bay and fuel tank.
- Damage Assessment: Carefully inspect the metal fuel line for any signs of damage. Check for holes, punctures, or any other openings that could lead to fuel leakage. Inspect the fittings and connections for tightness and integrity. Ensure that all bolts and fasteners are secure and tightened to the manufacturer's specifications. Any damaged or compromised connections should be addressed immediately.
- Cleaning and Debris Removal: Keep the fuel line clean and free of debris. Over time, fuel lines can accumulate dirt, rust, or other contaminants. Use a soft brush or a compressed air gun to remove any built-up material. Ensure that no debris or foreign objects remain inside the line, as they can cause blockages or damage the internal surfaces. Cleaning the line regularly is essential for maintaining its performance and longevity.
- Documentation and Records: Maintain detailed records of the inspection process. Note any issues, damages, or areas of concern. Documentation will help track the line's condition and identify potential problems early on. Regular inspections and maintenance can significantly extend the life of the fuel line and ensure the overall reliability of the fuel system.
By following these inspection procedures, you can guarantee that the metal fuel line is in excellent condition, minimizing the risk of fuel-related issues and ensuring optimal engine performance. Regular maintenance and attention to these details are vital for the longevity of any fuel system.
Understanding Homelite 4620 Chainsaw Fuel Line Setup
You may want to see also
Flaring Tool: Select appropriate flare tool for line size
When it comes to flaring metal fuel lines, selecting the right flaring tool is crucial for a successful and safe job. The size of the fuel line will determine the type of flaring tool you need to ensure a proper fit and a secure connection. Here's a guide on how to choose the appropriate flaring tool based on line size:
Understanding Line Sizes: Before selecting a flaring tool, it's essential to understand the different sizes of fuel lines. Fuel lines are typically measured in inches or millimeters, and the size can vary depending on the application. Common sizes range from 1/4-inch to 2-inch diameters. Smaller lines are often used for lighter applications, while larger sizes are designed for heavier-duty requirements.
Flaring Tools for Different Sizes: The flaring process involves shaping the end of the fuel line to create a smooth, conical flare that can be easily connected to fittings. Here's a breakdown of the flaring tools available:
- Hand-held Flaring Tools: For smaller fuel lines (1/4-inch to 3/8-inch), hand-held flaring tools are commonly used. These tools are portable and allow for precise control during the flaring process. They often come with interchangeable dies to accommodate various line sizes. Hand-held tools are suitable for DIY enthusiasts and small-scale projects.
- Pneumatic or Hydraulic Flaring Tools: When dealing with larger fuel lines (1/2-inch to 2-inch), pneumatic or hydraulic flaring tools are preferred. These tools provide more power and force, making it easier to flare thicker lines. Pneumatic tools are powered by compressed air, while hydraulic tools use pressurized fluid. They offer faster flaring capabilities and are ideal for professional mechanics and large-scale installations.
- Flaring Dies: In addition to the flaring tool itself, you'll need the appropriate flaring dies for the specific line size. Flaring dies are inserts that fit into the tool and shape the line during the process. Ensure you have the correct dies for the line size you are working with.
Selecting the Right Tool: When choosing a flaring tool, consider the following:
- Line Diameter: Always refer to the fuel line's diameter to determine the required flaring tool size.
- Tool Capacity: Select a tool that can handle the thickness of the line. Thicker lines may require more robust tools.
- Application: Consider the nature of your project. For lighter applications, a hand-held tool might suffice, while more demanding tasks may call for pneumatic or hydraulic equipment.
Remember, using the correct flaring tool for the line size is essential for a professional-looking connection and ensures the fuel line's integrity. Always follow the manufacturer's guidelines and safety instructions when operating any flaring equipment.
Understanding Fuel Tank Liners: Protection for Your Vehicle's Fuel System
You may want to see also
Flare Process: Follow steps: cut, deburr, flare, inspect, torque
The process of flaring a metal fuel line is a crucial step in ensuring a secure and leak-free connection. Here's a detailed guide on how to flare a metal fuel line, covering the essential steps:
Cutting: Begin by carefully cutting the metal fuel line to the desired length. Use a sharp, clean-cut tool to ensure a precise and clean cut. The cut should be straight and square to facilitate a proper flare. Take your time and measure twice to avoid any mistakes, as an incorrect cut can lead to issues during the flaring process.
Deburring: After cutting, it's essential to deburr the edges of the metal line. This step removes any sharp edges or burrs that could cause damage or create a weak point in the flare. Use a deburring tool or a file to smooth out the cut edges, ensuring they are free of any protruding metal. Deburring is crucial for a clean and safe flare.
Flaring: Now, you'll perform the flaring process, which involves shaping the metal line to create a smooth, rounded end. Here's a breakdown:
- Place the metal line on a flaring tool or mandrel, ensuring it is centered.
- Use a hammer or a flaring tool to shape the line, applying pressure and working the metal. The goal is to create a smooth, continuous curve without any sharp bends.
- Take your time and work the metal evenly to avoid distorting the flare.
- Continue flaring until the desired flare radius is achieved. This step requires precision and patience.
Inspection: Once flaring is complete, a thorough inspection is vital. Check the flare for any defects, such as cracks, uneven bends, or sharp edges. Use a magnifying glass or a bright light to ensure you catch any potential issues. The flare should be smooth, continuous, and free of any visible defects. If any problems are found, carefully adjust and re-flare the connection.
Torquing: Finally, torque the flare to ensure a secure and tight connection. Use a torque wrench to apply the specified torque value, typically in inch-pounds. Over-torquing can damage the flare, while under-torquing may result in a weak connection. Follow the manufacturer's guidelines for the correct torque value. After torquing, inspect the connection again to ensure it is intact and secure.
Remember, flaring a metal fuel line requires precision and attention to detail. Take your time, use the right tools, and follow these steps for a successful and safe flare. This process is essential for maintaining the integrity of your fuel system and preventing leaks.
Fuel Line: Can It Run by Transmission?
You may want to see also
Safety Measures: Wear protective gear, work in well-ventilated area, follow manufacturer guidelines
When working with metal fuel lines, it's crucial to prioritize safety to prevent accidents and ensure a successful outcome. Here are the essential safety measures to keep in mind:
Protective Gear: Before beginning any flaring process, it is imperative to don the appropriate protective equipment. This includes heat-resistant gloves to shield your hands from potential burns and eye protection, such as safety goggles or a face shield, to safeguard your eyes from sparks and debris. Additionally, consider wearing a respirator or a dust mask to protect your respiratory system from inhaling any fumes or hazardous particles that may be present during the process.
Well-Ventilated Area: Flaring metal fuel lines can generate fumes and release potentially hazardous gases. Therefore, it is crucial to conduct this work in a well-ventilated area or even outdoors if possible. Ensure that the workspace has proper ventilation to allow fresh air to circulate and minimize the buildup of harmful fumes. If working indoors, use exhaust fans or ventilation systems to remove any toxic gases and maintain a safe environment.
Manufacturer's Guidelines: Every fuel line and flaring tool has specific instructions provided by the manufacturer. It is imperative to follow these guidelines to the letter. Manufacturers often include detailed safety information, including recommended personal protective equipment, ventilation requirements, and step-by-step instructions for the flaring process. Adhering to these guidelines ensures that you are using the equipment correctly and safely, reducing the risk of accidents and damage to the fuel line.
Additionally, familiarize yourself with the specific tools and techniques required for flaring metal fuel lines. This may include understanding the proper use of flare guns, the importance of precise measurements, and the correct assembly of fittings. By following the manufacturer's instructions, you can ensure a professional and safe completion of the task.
Remember, safety should always be the top priority when working with fuel lines. Taking these precautions will help prevent accidents, protect yourself and those around you, and ensure the successful and safe completion of your flaring project.
Chevy Fuel Line or Return? Spot the Difference
You may want to see also
Frequently asked questions
Flaring a metal fuel line is a crucial process in plumbing and automotive applications to ensure a secure and leak-free connection. It involves creating a precise, controlled flame to melt and fuse the ends of the metal pipe, forming a strong bond.
Before flaring, ensure the metal line is clean and free of any debris or contaminants. Use a wire brush or a specialized cleaning tool to remove any old fittings or corrosion. It's essential to have the correct flare tool for the specific size and type of fuel line to achieve a proper flare.
There are two primary types of flares: the compression flare and the ring flare. Compression flares are created by bending the end of the pipe to form a small, flat ring, while ring flares involve bending the pipe to create a larger, ring-shaped flare. The choice depends on the application and the desired connection type.
Reusing a flared metal fuel line is generally not recommended. Flaring is a one-time process that permanently alters the pipe's structure. Reusing a flared line may lead to reduced performance, potential leaks, and compromised safety. It's best to replace the line if it has been flared previously.