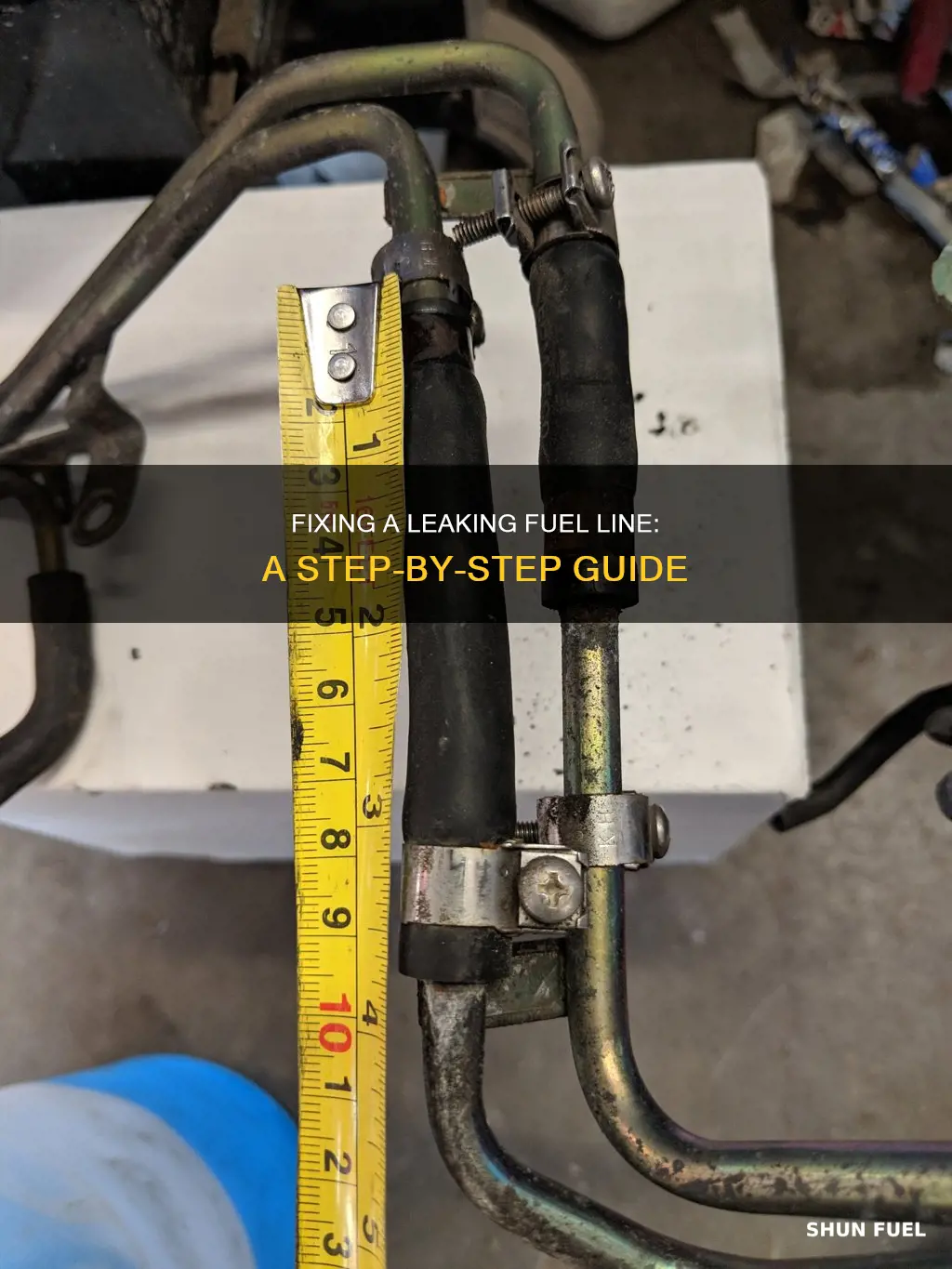
Fixing a leaking fuel line connector can be a straightforward process if you follow the right steps. Start by identifying the source of the leak, which could be a damaged or worn-out gasket, a loose connection, or a crack in the fuel line itself. Gather the necessary tools and materials, including a new gasket, fuel line, and any required connectors or clamps. Ensure you have a clean and dry work area to prevent further contamination. Carefully disconnect the old fuel line, taking note of the connections and their positions. Replace the gasket and reassemble the fuel line, ensuring a tight and secure fit. Finally, test the system to ensure there are no further leaks, and make any necessary adjustments to ensure optimal performance and safety.
What You'll Learn
- Locate the Connector: Identify the leaking fuel line connector using a visual inspection
- Prepare Tools: Gather necessary tools: wrench, pliers, fuel line repair kit
- Disassemble Carefully: Carefully disconnect the connector, avoiding damage to surrounding components
- Inspect and Clean: Examine the connector and fuel line for damage, then clean the surfaces
- Reassemble and Test: Reattach the connector, ensuring proper alignment, and test for leaks
Locate the Connector: Identify the leaking fuel line connector using a visual inspection
When dealing with a leaking fuel line connector, the first step is to locate the specific connector that is causing the issue. This requires a thorough visual inspection of the fuel system in your vehicle. Start by accessing the fuel lines, which are typically located under the hood and along the engine compartment. Look for any visible signs of damage, such as cracks, corrosion, or frayed insulation around the fuel lines. These issues could indicate a potential leak.
Pay close attention to the connections, as these are common problem areas. The fuel line connectors are small components that join the fuel lines to the engine or other fuel system parts. Inspect these connectors for any signs of leakage. Leaks may appear as small droplets or puddles of fuel around the connector, or you might notice a hissing sound if the fuel is under pressure. Over time, these connectors can become loose or damaged due to vibration and heat, leading to leaks.
Look for any discolored or wet areas around the fuel lines and connectors. Fuel is highly flammable, so any signs of leakage should be addressed immediately to prevent potential hazards. Additionally, check for any fuel stains or residue on the engine bay or surrounding areas, as these could indicate a leaking connector.
If you're unsure about the location of the connector, refer to your vehicle's manual or seek guidance from a professional mechanic. They can provide valuable insights into the specific fuel system layout of your car. Remember, a thorough visual inspection is crucial in identifying the leaking connector before attempting any repairs.
Fuel Injector Cleaning: Unclogging Fuel Lines for Optimal Performance
You may want to see also
Prepare Tools: Gather necessary tools: wrench, pliers, fuel line repair kit
Before you begin any fuel line repair, it's crucial to have the right tools on hand to ensure a successful and safe fix. Here's a breakdown of the essential tools you'll need:
Wrench: A wrench is a fundamental tool for any automotive repair. You'll need a wrench that fits the size of the fuel line connector bolts. These bolts are typically small and require a precise fit. Having a adjustable wrench or a set of socket wrenches can be helpful as they allow you to adjust the grip to match the bolt size.
Pliers: Pliers are indispensable for gripping and manipulating small components. You'll use them to tighten or loosen the fuel line connector and potentially remove any damaged parts. Needle-nose pliers are particularly useful for reaching into tight spaces and grasping small fuel line components.
Fuel Line Repair Kit: This is a specialized kit designed specifically for fuel line repairs. It typically includes a variety of components such as fuel line connectors, clamps, and sealing compounds. A fuel line repair kit will provide you with everything you need to effectively repair the leaking connector. Look for a kit that includes the appropriate size connectors for your fuel line.
Having these tools ready will ensure you have the necessary equipment to tackle the repair process efficiently. Remember to inspect each tool for any signs of damage or wear before starting the repair to guarantee a smooth and successful fix.
Fuel Line Hose Connections: The Ultimate Guide to Choosing the Right Method
You may want to see also
Disassemble Carefully: Carefully disconnect the connector, avoiding damage to surrounding components
When dealing with a leaking fuel line connector, it's crucial to approach the disassembly process with precision and care. Start by identifying the specific connector that is leaking. These connectors are typically located along the fuel line, often near the engine or fuel tank. Once identified, locate the appropriate tools for disconnection. A set of adjustable wrenches or a fuel line disconnect tool can be useful for this task.
Before proceeding, ensure you have a clean and well-lit workspace. This will help you avoid any potential hazards and make the process more efficient. Carefully inspect the connector to understand its design and the connections it makes. Look for any visible signs of damage, corrosion, or debris that might have contributed to the leak. This initial assessment will guide your next steps and ensure you have a clear understanding of the issue.
Now, begin the disassembly process. Locate the retaining clips or fasteners that secure the connector. These could be small screws, clips, or even a quick-release mechanism. Carefully remove these fasteners, setting them aside in a secure place. Be gentle to avoid losing any small parts. Once the fasteners are removed, you should be able to gently pull the connector away from the fuel line. Take your time here, as forcing the connector can damage surrounding components.
As you disconnect the connector, observe the condition of the fuel line and the connector itself. Look for any signs of damage, such as cracks or holes, which could indicate a more serious issue. Also, check for any debris or contaminants that might have caused the leak. This step is essential for understanding the root cause of the problem and ensuring a thorough repair.
Remember, the key to successfully fixing a leaking fuel line connector is patience and attention to detail. Take your time, work systematically, and avoid any rushed movements that could lead to mistakes. By carefully disconnecting the connector and inspecting the components, you'll be well on your way to resolving the leak and ensuring the safe and efficient operation of your vehicle's fuel system.
Softening Blower Fuel Line: A Step-by-Step Guide to Smooth Operation
You may want to see also
Inspect and Clean: Examine the connector and fuel line for damage, then clean the surfaces
When dealing with a leaking fuel line connector, a crucial step in the repair process is to thoroughly inspect and clean the affected components. This initial step ensures that you identify any potential issues and prepare the surfaces for effective sealing. Here's a detailed guide on how to approach this task:
Examination: Begin by visually inspecting the fuel line connector and the surrounding areas. Look for any visible signs of damage, such as cracks, corrosion, or debris accumulation. Check for any frayed or damaged fuel lines that might be causing the leak. Pay close attention to the connector's threads, ensuring they are intact and not stripped. If you notice any damage, it's essential to address it before proceeding with cleaning.
Cleaning the Connector and Fuel Line: Start by disconnecting the fuel line from the engine and the connector. Use a fuel line cleaner or a suitable solvent to carefully clean the interior of the fuel line. This step helps remove any built-up fuel, debris, or contaminants that could interfere with the sealing process. Rinse the fuel line thoroughly to ensure no residue remains. Next, clean the fuel line connector. Use a brush or a cleaning tool to remove any dirt or corrosion from the threads and surfaces. Ensure that you reach all the nooks and crannies of the connector.
For a more thorough clean, consider using a fuel system cleaner, which can be sprayed directly onto the connector and left to sit for a few minutes before being wiped away. This process helps dissolve any stubborn deposits. After cleaning, inspect the connector and fuel line again to ensure no contaminants remain.
Preparation for Repair: Once the inspection and cleaning are complete, you'll have a clear understanding of the extent of the damage. If there is significant wear or damage, you might need to replace the fuel line or connector. However, if the issue is minor, you can proceed with sealing the connector. Ensure that all surfaces are dry before applying any sealing compound or tape. This step is vital to guarantee a successful repair and prevent further leaks.
Black Fuel Line: Is It Superior to Yellow?
You may want to see also
Reassemble and Test: Reattach the connector, ensuring proper alignment, and test for leaks
Reassembling and testing a fuel line connector after repairs is a crucial step to ensure the system's integrity and prevent further issues. Here's a detailed guide on how to approach this task:
Reattachment and Alignment: Begin by carefully reattaching the fuel line connector to the fuel line. Ensure that the connector is properly aligned with the fuel line, as misalignment can lead to improper sealing. Pay close attention to the O-rings or gaskets within the connector, as these provide the primary seal. Gently push the connector onto the fuel line until it is fully seated, ensuring that all components are in the correct position. Double-check the alignment to guarantee a secure connection.
Tightening and Securing: After reattachment, secure the connector using the appropriate fasteners or clips. Tighten these fasteners by hand first, ensuring they are snug. Then, use a wrench or the appropriate tool to tighten them further, but be cautious not to over-tighten, as this can damage the connector or fuel line. The goal is to achieve a firm, yet gentle, hold to prevent any damage during the testing phase.
Visual Inspection: Before testing, perform a thorough visual inspection of the reassembled connector. Check for any visible signs of damage, such as cracks or tears in the O-rings or gaskets. Ensure that there are no kinks or bends in the fuel line that could affect the connector's performance. Any visible damage should be addressed before proceeding.
Leak Testing: The critical step is to test for leaks. Start by applying a small amount of fuel or a suitable sealant to the connector's O-rings or gaskets. This step helps to identify potential leaks more easily. Then, use a leak detection method, such as a soapy water solution or a specialized fuel line leak detector, to identify any areas where fuel is escaping. Inspect the connector and the surrounding area for bubbles or foam, indicating a leak. If a leak is detected, carefully disassemble the connector and address the issue, ensuring proper sealing before reattaching.
Final Testing: Once you are confident that the connector is leak-free, it's time for final testing. Start the engine and monitor for any unusual noises or vibrations, especially around the fuel lines. Check for any fuel leaks at the connector and ensure that the fuel system operates smoothly. If no issues are found, your reassembly and testing process has been successful, and you can proceed with further vehicle operation.
Thawing Frozen Fuel Lines: A Guide to Winter Car Care
You may want to see also
Frequently asked questions
A leaking fuel line connector can be identified by the presence of fuel residue or stains around the connector, especially if you've recently noticed a drop in fuel levels or an increase in engine misfires. You might also hear a hissing sound or see fuel droplets around the engine bay.
Fuel line connectors can leak due to several reasons. Common causes include corrosion or damage to the rubber gasket, which seals the connection. Over time, the gasket can dry out, crack, or become brittle, leading to fuel leaks. Additionally, physical damage, such as being struck by a tool or a sharp object, can also cause leaks.
Yes, you can fix a leaking fuel line connector yourself. Here's a simple step-by-step guide: First, locate the leaking connector and disconnect the fuel line. Inspect the connector and the surrounding area for any signs of damage or corrosion. Clean the connector and the fuel line if necessary. Then, replace the rubber gasket or o-ring with a new one. Ensure a tight seal by applying a small amount of fuel line tape or a similar sealing compound around the connector. Finally, reattach the fuel line and secure it in place.
While it's not recommended to use a temporary fix as a long-term solution, you can temporarily plug the leak by inserting a small piece of rubber or a similar material into the connector to block the opening. However, this is only a temporary measure and should be replaced with a proper repair as soon as possible to prevent further fuel leaks and potential engine damage.