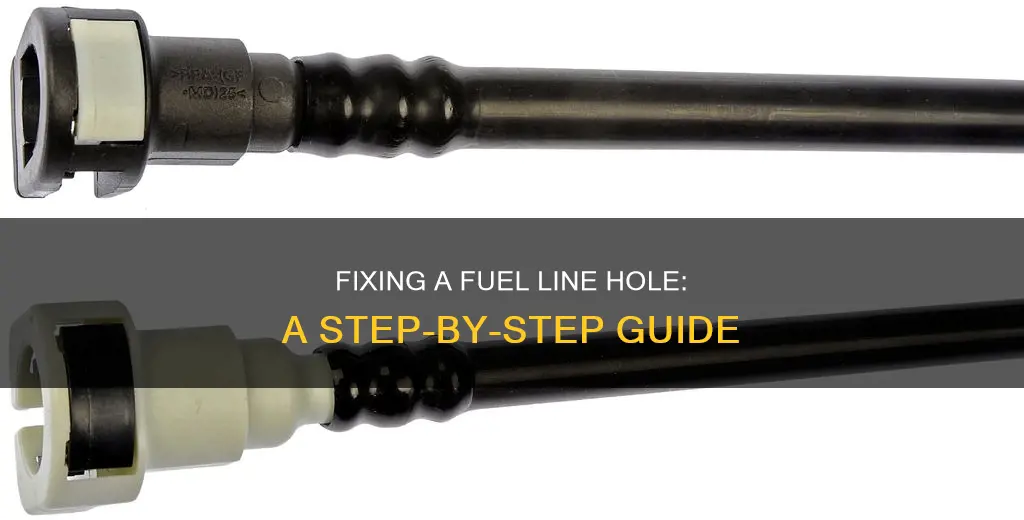
Fixing a hole in a fuel line can seem daunting, but with the right tools and a bit of know-how, it's a manageable task. Whether you're dealing with a small puncture or a larger tear, the process involves identifying the damage, preparing the area, and applying a suitable repair method. This guide will walk you through the essential steps to ensure your fuel line is back to working order, keeping your vehicle running smoothly and safely.
What You'll Learn
Locate the damaged section of the fuel line
When dealing with a damaged fuel line, the first crucial step is to accurately locate the affected area. This process requires a methodical approach to ensure you identify the precise spot where the fuel line has been compromised. Start by inspecting the vehicle's undercarriage, as this is where fuel lines are typically routed. Look for any visible signs of damage, such as tears, punctures, or kinks in the line. These visual cues can provide an initial indication of the problem area. If you're unable to spot the damage with the naked eye, consider using a flashlight to illuminate the area and get a better view.
Once you've identified a potential issue, it's essential to confirm the damage. Feel the fuel line along its length, paying close attention to any areas where it might be thinner or more fragile. This tactile inspection can help you pinpoint the exact location of the hole or tear. Additionally, you can use a stethoscope to listen for any fuel escaping from the line, which would indicate a breach. Remember, the goal is to isolate the damaged section so that you can proceed with the necessary repairs or replacements.
If the fuel line is accessible, you might be able to identify the damage more easily. Look for any signs of corrosion, rust, or debris that could have caused the issue. In some cases, the damage might be more subtle, such as a small crack or a slight bulge. Take your time to inspect the line thoroughly, as even a small hole can lead to significant problems if left unattended.
When you've located the damaged section, it's important to document the position and any relevant details. Mark the spot with tape or a temporary marker to ensure you don't accidentally cut or damage the line further while working on it. This step is crucial for ensuring that you make the necessary repairs in the correct location.
In summary, locating the damaged section of the fuel line is a critical initial step in the repair process. It requires a careful and systematic approach to identify the problem area accurately. By following these steps, you can ensure that you address the issue effectively and prevent further complications.
BMW 750i Fuel Line Disconnection: A Step-by-Step Guide
You may want to see also
Clean and inspect the area around the hole
When dealing with a fuel line hole, it's crucial to start by thoroughly cleaning and inspecting the affected area. This initial step is essential to ensure a successful repair and prevent further issues. Begin by gathering the necessary tools and materials, including a fuel line cleaner, a soft-bristled brush, a rag, and a small container for cleaning solutions.
Locate the fuel line and identify the precise location of the hole. Carefully remove any debris or dirt from the surrounding area using the soft-bristled brush. Pay close attention to the edges of the hole, as dirt and grime can accumulate here, making it more challenging to seal the repair. Rinse the area with clean water to remove any remaining dirt and ensure a clear view of the damage.
Next, apply the fuel line cleaner to the hole and its immediate vicinity. Follow the product instructions for the appropriate application time, typically a few minutes, allowing the cleaner to penetrate and dissolve any contaminants. Use the rag to wipe away the cleaner, ensuring a thorough clean. This process is vital to create a smooth surface for the repair material and prevent any residue from affecting the sealing process.
After cleaning, inspect the area closely. Check for any remaining debris, corrosion, or signs of further damage. Look for any signs of fuel leakage, which could indicate a more severe issue. If you notice any significant damage or if the hole is large, it might be best to consult a professional mechanic for guidance, as they can provide expert advice and ensure a proper repair.
By taking the time to clean and inspect the area, you'll have a clear understanding of the extent of the damage and can make informed decisions about the next steps in the repair process. This thorough approach is key to ensuring a successful and long-lasting fix for your fuel line.
Fuel Line Placement: Expert Tips for Optimal Performance
You may want to see also
Use a fuel line repair kit for a quick fix
If you're dealing with a small hole or tear in your fuel line, a fuel line repair kit can be a convenient and effective solution. These kits are designed to provide a temporary or even permanent fix, depending on the severity of the damage. Here's a step-by-step guide on how to use a fuel line repair kit for a quick and efficient repair:
Step 1: Prepare the Area
Start by ensuring you have a well-ventilated workspace. Fuel lines can be located in various parts of the engine compartment, so it's essential to work in a safe and controlled environment. Gather the necessary tools, including the fuel line repair kit, a pair of gloves, and a small rag or cloth. Clean the area around the hole to remove any dirt or debris that might interfere with the repair process.
Step 2: Inspect the Damage
Carefully examine the fuel line to determine the size and location of the hole. This assessment will help you choose the appropriate repair method. For small holes, a temporary fix might be sufficient, while larger tears may require a more permanent solution.
Step 3: Apply the Repair Kit
Most fuel line repair kits come with a variety of components, including a sealing compound, a reinforcing sleeve, and a primer. Follow the instructions provided with the kit:
- Clean the fuel line thoroughly at the damaged area.
- Apply a thin layer of primer to the fuel line and the surrounding area.
- Insert the reinforcing sleeve over the hole, ensuring it covers the entire damaged section.
- Secure the sleeve in place using the provided clips or tape.
- Apply the sealing compound generously, following the kit's instructions for the correct amount.
- Allow the compound to cure according to the manufacturer's guidelines.
Step 4: Test and Reinstall
Once the repair is complete and the compound has cured, it's time to test the fix. Start the vehicle and check for any leaks. If the repair is successful, you can reinstall the fuel line, ensuring it is securely attached to the engine and other components.
Remember, while a fuel line repair kit can provide a quick solution, it is essential to address any underlying issues that may have caused the hole in the first place. Regular maintenance and inspections can help prevent such damage in the future.
Fuel Line Size for Predator Generators: A Quick Guide
You may want to see also
Consider replacing the entire fuel line if necessary
If you've identified a hole or significant damage in the fuel line, it's crucial to consider replacing the entire line rather than attempting a temporary fix. Fuel lines are designed to withstand specific pressure and temperature conditions, and a compromised line can lead to fuel leaks, engine performance issues, and potential safety hazards. Here's why replacing the fuel line is often the best course of action:
Safety and Reliability: Fuel lines are critical components in your vehicle's fuel system. A damaged line can lead to fuel leakage, which, when combined with ignition sources, poses a serious fire hazard. Additionally, a compromised line may not effectively deliver fuel to the engine, resulting in poor performance, stalling, or even engine damage. Replacing the entire fuel line ensures a safe and reliable fuel supply, minimizing the risk of accidents and costly engine repairs.
Long-Term Solution: Temporary fixes, such as patching a hole or using a sealant, might provide short-term relief but often fail over time. The fuel line's material and structure may not be compatible with the sealant, leading to further deterioration. A replacement fuel line, made from appropriate materials, ensures a long-lasting solution, reducing the likelihood of future issues.
Complexity of Repair: Repairing a fuel line can be complex, especially if the damage is extensive. It requires specialized tools and knowledge of the fuel system's layout. Attempting a DIY repair might lead to further complications, especially if you're not experienced in automotive repairs. Opting for a replacement ensures a professional-grade solution, saving you time and potential frustration.
Cost-Effectiveness: While replacing a fuel line might seem expensive upfront, it can be more cost-effective in the long run. A damaged fuel line can lead to various engine problems, which may be costly to repair. By replacing the line, you address the root cause, potentially avoiding multiple subsequent repairs. Moreover, a replacement line ensures your vehicle's performance and longevity, providing peace of mind.
In summary, when dealing with a hole or significant damage in a fuel line, replacing the entire line is a recommended approach. It ensures safety, reliability, and long-term performance, avoiding the potential risks and costs associated with temporary fixes or further engine complications. Always consult a professional mechanic if you're unsure about the extent of the damage or the appropriate course of action.
Understanding 6AN and 3/8 Fuel Line Compatibility
You may want to see also
Test the fuel system to ensure proper functionality
Before attempting any repairs, it's crucial to ensure the fuel system is functioning correctly to prevent further damage or safety hazards. Testing the fuel system involves a systematic approach to identify and address any issues. Here's a step-by-step guide:
Step 1: Inspect the Fuel Lines and Connections: Start by visually inspecting the fuel lines for any visible damage, including holes, cracks, or leaks. Check all connections, fittings, and clamps for tightness and signs of corrosion or deterioration. Pay close attention to areas where the fuel lines are most susceptible to damage, such as under the vehicle or near the engine.
Step 2: Check for Fuel Pressure: Fuel pressure is essential for proper engine operation. Use a fuel pressure gauge to measure the pressure at the fuel rail or injectors. Compare the reading to the manufacturer's specifications. If the pressure is significantly lower than the recommended range, it could indicate a restricted fuel flow or a problem with the fuel pump.
Step 3: Perform a Fuel Flow Test: This test helps determine if the fuel is flowing correctly from the tank to the engine. Start by removing the fuel line connection near the fuel tank. Securely attach the fuel pressure gauge to the exposed fuel line. Turn on the ignition and listen for the fuel pump to prime. Then, start the engine and monitor the fuel pressure. If the pressure drops or remains low, it suggests a potential issue with the fuel pump, filter, or lines.
Step 4: Inspect the Fuel Injectors: If the fuel system is functioning, the next step is to inspect the fuel injectors. Remove one injector at a time and use a fuel pressure tester to check for proper fuel spray. A faulty injector may not deliver the correct fuel volume or pressure, leading to poor engine performance.
Step 5: Listen for Fuel Pump Operation: With the engine off, listen to the fuel pump's operation. It should prime for a few seconds when you turn the ignition on. If you don't hear the pump running, it could indicate a problem with the electrical connection or the pump itself.
Step 6: Check for Leaks and Vacuum: Inspect the fuel system for any signs of vacuum leaks, as these can affect fuel pressure and engine performance. Use a smoke machine or soapy water to identify any leaks.
By following these testing procedures, you can ensure that the fuel system is operating as intended, allowing you to proceed with the necessary repairs or replacements with confidence.
Nylon's Flexibility: Can It Handle Fuel Lines with Rubber?
You may want to see also
Frequently asked questions
For a temporary fix, you can use a fuel line clamp or a rubber band to seal the hole. This will prevent fuel leakage, but it's important to note that this is a short-term solution. It's best to replace the damaged section of the fuel line as soon as possible.
While duct tape might seem like a quick fix, it is not recommended for fuel lines. Duct tape can lose its adhesive properties over time and may not provide a secure seal, leading to potential fuel leaks. It's always best to use specialized repair methods or replace the damaged part.
Repairing a fuel line typically requires a few essential tools. You'll need a fuel line cutter or a sharp knife to carefully cut away the damaged section. A fuel line crimping tool or a pair of pliers can be used to attach a new section of fuel line. Additionally, have some fuel line repair tape or a suitable adhesive to seal the new connection.
Preventing fuel line damage is crucial to avoid potential engine issues. Ensure that you use fuel lines made of high-quality materials that can withstand the fuel's pressure and temperature. Regularly inspect the fuel lines for any signs of wear, cracks, or damage, especially in areas where they are exposed to heat or vibration. Keep the fuel lines away from sharp edges and potential sources of impact.
If the hole in the fuel line is large, the line is severely damaged, or if you've attempted temporary fixes multiple times, it's best to replace the entire fuel line. Over time, fuel lines can deteriorate due to factors like age, fuel contamination, or external damage. Replacing the fuel line ensures optimal engine performance and prevents potential fuel leaks that could lead to engine misfires or other mechanical issues.