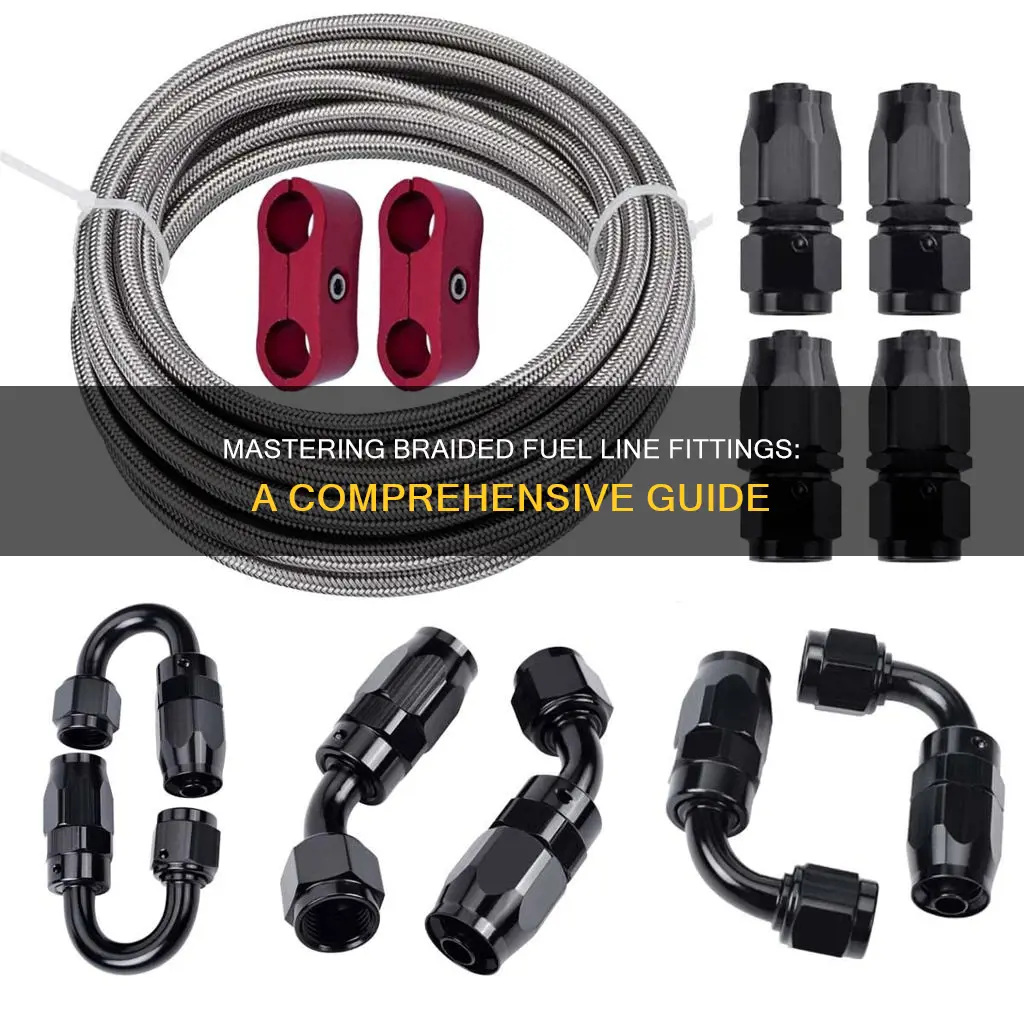
Braided fuel lines are a popular choice for vehicle owners seeking to improve fuel delivery efficiency and durability. However, proper installation is crucial to ensure optimal performance and safety. This guide will focus on the essential technique of fittings on braided fuel lines, providing a step-by-step approach to ensure a secure and leak-free connection. By following these instructions, you can effectively join braided fuel lines, enhancing the overall reliability of your vehicle's fuel system.
Characteristics | Values |
---|---|
Braided Fuel Line Material | Braided fuel lines are typically made from materials like rubber, silicone, or a composite blend, ensuring flexibility and durability. |
Fitting Types | Common fittings include quick-connect couplings, barbed fittings, and compression fittings. Quick-connects are popular for their ease of use, while barbed and compression fittings offer more secure connections. |
Size Compatibility | Fittings are available in various sizes to match the fuel line diameter, ensuring a proper fit. |
Temperature Resistance | Look for fittings that can withstand the temperature range of your fuel, especially if it contains ethanol or other additives. |
Pressure Rating | Check the pressure rating of the fittings to ensure they can handle the fuel system's pressure. |
Ease of Installation | Some fittings are designed for quick and simple installation, often requiring no tools or minimal assembly. |
Corrosion Resistance | Choose fittings made from materials that resist corrosion, especially in environments with moisture or harsh chemicals. |
Compatibility with Fuel Types | Ensure the fittings are compatible with the type of fuel used, considering factors like ethanol content and fuel volatility. |
Color-Coding | Some manufacturers use color-coding for different fuel line sizes and types, making identification easier. |
Length Options | Fittings are available in various lengths to accommodate different fuel line configurations. |
What You'll Learn
- Fuel Line Material: Choose the right material for your braided fuel line
- Fitting Types: Understand different fitting types for secure connections
- Braiding Techniques: Learn braiding techniques to reinforce fuel lines
- Clamping Methods: Explore various clamping methods for a tight fit
- Safety Precautions: Follow safety guidelines to prevent fuel leaks
Fuel Line Material: Choose the right material for your braided fuel line
When it comes to choosing the right material for your braided fuel line, several factors come into play to ensure optimal performance and longevity. The material selection is crucial as it directly impacts the fuel line's ability to withstand various conditions, including temperature fluctuations, fuel type, and environmental factors. Here's a guide to help you make an informed decision:
Braided fuel lines are commonly made from various materials, each with its own set of advantages and disadvantages. The most popular choices include rubber, silicone, and high-temperature nylon. Rubber is a traditional and cost-effective option, known for its flexibility and resistance to abrasion. It is suitable for most fuel types and can handle moderate temperature variations. However, rubber may become brittle over time, especially in low-temperature conditions, which could lead to cracking and fuel leaks. Silicone, on the other hand, offers improved flexibility and temperature resistance compared to rubber. It is an excellent choice for high-performance applications, as it can withstand extreme temperatures and is resistant to fuel degradation. This material is also less prone to cracking, making it a reliable long-term solution.
For those seeking an even more robust and versatile option, high-temperature nylon is an excellent choice. This material is known for its exceptional durability, flexibility, and resistance to chemicals and abrasion. Nylon can handle extreme temperatures, making it ideal for high-performance engines and racing applications. It is also lightweight, which can improve overall vehicle performance. However, it is worth noting that nylon may be more expensive than rubber or silicone, so it's essential to consider your specific needs and budget.
In addition to the material, the thickness and diameter of the braided fuel line should also be considered. Thicker lines provide better protection against fuel leaks and can handle higher pressure, but they may also be less flexible. The diameter should be chosen based on the fuel flow rate and pressure requirements of your vehicle. Consulting the manufacturer's specifications or seeking professional advice is recommended to ensure the correct size for your application.
When installing the braided fuel line, ensure that you use the appropriate fittings and connectors for the chosen material. Different materials may require specific types of fittings to ensure a secure and leak-free connection. Proper installation is crucial to maintaining the integrity of the fuel system and preventing potential issues.
In summary, selecting the right material for your braided fuel line is essential for optimal performance and longevity. Consider the specific requirements of your vehicle, including fuel type, temperature range, and performance needs. Rubber, silicone, and high-temperature nylon are popular choices, each offering unique advantages. By carefully evaluating these factors, you can make an informed decision and ensure a reliable fuel system for your vehicle.
Unleash the Power: A Guide to Removing Fuel Lines from the Pump
You may want to see also
Fitting Types: Understand different fitting types for secure connections
When working with braided fuel lines, it's crucial to understand the various fitting types available to ensure secure and reliable connections. These fittings play a vital role in maintaining the integrity of the fuel system, preventing leaks, and ensuring optimal performance. Here's an overview of the different fitting types and their applications:
- Compression Fittings: Compression fittings are commonly used for braided fuel lines due to their simplicity and effectiveness. These fittings consist of a ferrule, typically made of metal, that is compressed onto the fuel line. The process involves inserting the fuel line into the fitting and then using a tool to tighten the nut, which compresses the ferrule and creates a tight seal. This type of fitting is ideal for both high-pressure and low-pressure applications, providing a secure connection that can withstand various fuel system demands.
- Clamp-Style Fittings: Clamp-style fittings offer a versatile solution for connecting braided fuel lines. These fittings use a clamp mechanism to secure the line, providing a reliable seal. The process involves sliding the fuel line into the fitting, positioning it correctly, and then tightening the clamp using a tool. This type of fitting is often preferred for its ease of installation and removal, making it suitable for applications where frequent adjustments or maintenance might be required.
- Quick-Connect Fittings: As the name suggests, quick-connect fittings offer a rapid and convenient connection method. These fittings typically feature a male and female end, with a locking mechanism to ensure a secure seal. By simply inserting the male end into the female end and locking it into place, you can quickly establish a connection. Quick-connect fittings are excellent for temporary or emergency connections, providing a reliable seal without the need for complex tools or procedures.
- Swivel Fittings: Swivel fittings are designed to allow flexibility and movement, making them ideal for applications where the fuel line needs to accommodate various angles and positions. These fittings have a rotating mechanism, allowing the fuel line to swivel freely. This feature is particularly useful in engine compartments with limited space or when connecting fuel lines to moving components. Swivel fittings ensure that the connection remains secure while providing the necessary flexibility.
Understanding the different fitting types is essential for any fuel system installation or repair. Each fitting type offers unique advantages, and choosing the right one depends on factors such as pressure requirements, space constraints, and the overall design of the fuel system. By selecting the appropriate fitting, you can ensure a secure and reliable connection for your braided fuel line, contributing to the overall performance and longevity of your vehicle's fuel system.
Fuel Line Protests: Dakota's Burning Questions
You may want to see also
Braiding Techniques: Learn braiding techniques to reinforce fuel lines
Braiding fuel lines is a crucial step in ensuring the longevity and reliability of your vehicle's fuel system. By learning the proper braiding techniques, you can reinforce these lines, preventing potential leaks and ensuring a steady fuel supply to your engine. Here's a step-by-step guide to mastering the art of braiding:
Understanding the Basics: Before you begin, familiarize yourself with the materials involved. Braided fuel lines are typically made of a flexible, high-strength material like steel or Kevlar. The core of the line is often a metal tube, which is then braided around a protective layer. Understanding the construction of these lines is key to knowing how to handle and reinforce them effectively.
Gathering the Tools: You'll need a few essential tools for braiding. A pair of sharp scissors or a cutting tool is necessary to trim the fuel line to the desired length. A braiding tool, often a simple metal frame with a series of holes, will help you create the braided pattern. Additionally, have a supply of the appropriate adhesive or sealant to secure the braiding and ensure a leak-free connection.
Measuring and Cutting: Start by measuring the length of the fuel line you need to reinforce. Cut the line carefully, ensuring a precise length. This step is crucial to avoid any excess material that could interfere with the braiding process.
Creating the Braided Pattern: Now, it's time to get your hands dirty. Place the cut fuel line onto the braiding tool, ensuring it is centered. Begin braiding by wrapping the line around the tool, alternating the direction of the wrap to create a secure pattern. The goal is to create a tight, uniform braid that covers the entire length of the line. Practice and patience are key here; take your time to ensure a neat and secure braid.
Securing the Braid: Once you've completed the desired number of wraps, it's time to secure the braid. Carefully trim any excess material and apply the adhesive or sealant to the ends of the braid. This step is vital to prevent the braid from unraveling and to ensure a long-lasting reinforcement. Allow the adhesive to cure according to the manufacturer's instructions.
Finishing Touches: After the adhesive has set, carefully remove the braiding tool. Inspect the reinforced fuel line, ensuring the braid is secure and there are no sharp bends or kinks. Test the flexibility of the line to ensure it can withstand the rigors of the vehicle's operation.
Mastering braiding techniques is an essential skill for anyone working on fuel lines. By following these steps, you can reinforce your fuel lines, ensuring a reliable and efficient fuel supply to your engine. Remember, practice makes perfect, and with time, you'll be able to create professional-looking braids that will keep your vehicle's fuel system in top condition.
Mastering Metal Fuel Line Cutting: A Comprehensive Guide
You may want to see also
Clamping Methods: Explore various clamping methods for a tight fit
When working with braided fuel lines, ensuring a secure and tight fit is crucial to prevent fuel leaks and maintain optimal performance. Clamping is a fundamental technique to achieve this, and there are several methods to consider for different applications. Here's an overview of various clamping techniques:
- Compression Fittings: This method involves using specialized compression fittings designed for braided fuel lines. These fittings typically consist of a ferrule, which is a metal or composite sleeve, and a nut or clamp. The ferrule is inserted into the fuel line, and then the nut or clamp is tightened, compressing the ferrule and creating a secure seal. Compression fittings are widely used due to their simplicity and effectiveness. When using this method, ensure that the ferrule is the correct size for the fuel line diameter and that the fitting is tightened evenly to avoid damaging the line.
- Crimping: Crimping is a process where a special tool is used to apply pressure to a fitting, causing it to deform and create a tight seal. This method is often employed for high-pressure applications or when a more permanent connection is required. Crimping tools are designed to apply precise force, ensuring a secure fit. It's essential to follow the manufacturer's guidelines for the specific crimping tool and fitting to be used. Proper crimping ensures a reliable seal and can be a preferred choice for critical fuel system connections.
- Clamp-Style Fittings: As the name suggests, these fittings use a clamp to secure the fuel line. The clamp is typically made of durable materials like stainless steel or aluminum and is designed to apply uniform pressure around the line. This method is versatile and can be used in various fuel line configurations. When installing, ensure that the clamp is the right size for the line diameter and that it is tightened firmly but not excessively. Regularly inspect and adjust the clamp as needed to maintain a tight fit over time.
- Hose Clamps: Standard hose clamps can also be utilized for braided fuel lines, especially in situations where custom solutions are required. Hose clamps come in various sizes and materials, allowing for flexibility in design. When using hose clamps, ensure that the line is clean and free of debris, and then apply the clamp securely. It's important to use the appropriate size and material for the fuel line's specifications to ensure a tight and reliable connection.
Each clamping method has its advantages and is suited to specific applications. Understanding the unique requirements of your fuel line setup will help you choose the most appropriate clamping technique, ensuring a secure and long-lasting connection. Always refer to manufacturer guidelines and best practices for the best results.
Perfect Fuel Line Size for 50cc Mopeds: A Guide
You may want to see also
Safety Precautions: Follow safety guidelines to prevent fuel leaks
Before you begin any work on installing fittings onto a braided fuel line, it's crucial to prioritize safety to prevent any potential fuel leaks, which can be hazardous and costly. Here are some essential safety precautions to follow:
Prepare the Work Area: Ensure you have a well-ventilated and clear workspace. Remove any obstacles or trip hazards to create a safe environment. Gather all the necessary tools and equipment, including the braided fuel line, fittings, and any cutting or sealing tools required. Proper preparation minimizes the risk of accidents and makes the installation process more efficient.
Wear Protective Gear: Safety gear is essential to protect yourself from potential hazards. Wear gloves to prevent skin contact with fuel, which can be harmful, and consider wearing safety goggles or glasses to shield your eyes from any splashes or debris. Additionally, ensure you are wearing appropriate clothing that covers your skin to avoid direct contact with fuel and potential irritation.
Fuel Line Inspection: Before starting, inspect the braided fuel line for any visible damage, cracks, or signs of wear. Check for any existing leaks or weak points that might be exacerbated during the installation process. If you notice any issues, address them promptly and consider replacing the fuel line if it is beyond repair. Ensuring the integrity of the fuel line is crucial for safety.
Follow Manufacturer's Guidelines: Always refer to the manufacturer's instructions and guidelines for the specific braided fuel line and fittings you are using. Different materials and designs may require unique installation techniques. Adhering to these guidelines will ensure a proper and safe fit, reducing the chances of leaks or damage.
Secure Connections: When attaching fittings, ensure a tight and secure connection. Use the appropriate tools to crimp or clamp the fittings firmly onto the fuel line. Avoid overtightening, as it can damage the line, and always follow the manufacturer's recommendations for torque specifications. Properly secured connections minimize the risk of fuel escaping and potential hazards.
Test for Leaks: After completing the installation, test the system for any leaks. Use a soapy water solution or a specialized fuel line leak detector to identify any potential issues. Inspect all connections and fittings carefully. If any leaks are detected, immediately shut off the fuel source and address the problem before proceeding. Testing is a critical step to ensure the safety and functionality of your fuel system.
Ice in Fuel Lines: A Chilling Threat to Your Car's Performance
You may want to see also
Frequently asked questions
Fittings are essential components that connect the braided fuel line to the fuel tank, pump, or other fuel system components. They ensure a secure and leak-free connection, allowing for efficient fuel transfer while withstanding the pressure and temperature variations in the fuel system.
The choice of fitting depends on the specific fuel line diameter and the application. Common types include quick-connect fittings, compression fittings, and barbed fittings. Quick-connect fittings are user-friendly for on-the-go connections, while compression fittings offer a tight seal. Barbed fittings are ideal for high-pressure applications. Ensure the fitting's inner diameter matches the fuel line's diameter for a proper fit.
No, it's crucial to use fittings designed for fuel lines to avoid leaks and potential engine damage. Braided fuel lines require fittings that can withstand the fuel's properties, pressure, and temperature. Using the wrong fitting may lead to fuel leaks, reduced performance, or even engine failure.
Installing fittings typically requires basic tools like a wrench or pliers for compression fittings and a crimping tool for barbed fittings. Quick-connect fittings may need a specific tool for attachment. It's essential to have the correct tools to ensure a secure and tight connection.
Regularly inspect the fittings for any signs of wear, cracks, or corrosion. Clean the fittings and fuel lines periodically to remove debris and ensure optimal performance. Check for tight connections and replace any damaged or worn-out fittings to maintain a reliable fuel system.