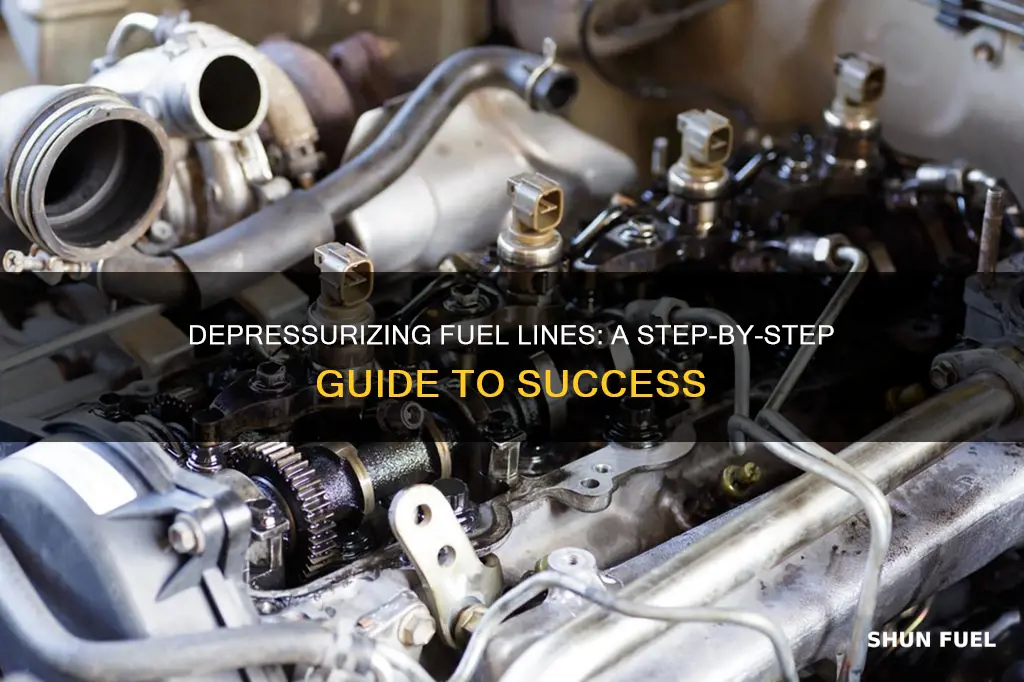
Depressurizing a fuel line is a crucial step in maintaining the performance and safety of a vehicle's fuel system. This process involves releasing excess pressure from the fuel lines to ensure optimal fuel flow and prevent potential issues such as fuel pump damage or engine misfires. By depressurizing the fuel line, you can ensure that the fuel system operates efficiently, providing the engine with the necessary fuel for optimal performance. This guide will provide a step-by-step process to depressurize the fuel line, ensuring your vehicle's fuel system remains in top condition.
What You'll Learn
- Fuel Line Material: Choose the right material for the fuel line to avoid corrosion and degradation
- Line Diameter: Ensure the fuel line diameter matches the engine's requirements for optimal flow
- Installation Technique: Proper installation techniques prevent leaks and ensure a secure connection
- Pressure Testing: Regularly test fuel lines for leaks and pressure to maintain safety
- Environmental Factors: Consider temperature and UV exposure to prevent fuel line damage
Fuel Line Material: Choose the right material for the fuel line to avoid corrosion and degradation
When it comes to fuel lines, selecting the appropriate material is crucial to ensure the longevity and performance of your vehicle's fuel system. The fuel line is responsible for transporting fuel from the tank to the engine, and using the right material can prevent corrosion, degradation, and potential fuel leaks. Here's a guide to help you choose the right material for your fuel line:
- Rubber or Synthetic Materials: Traditional fuel lines are often made of rubber, which is a cost-effective and flexible material. Natural rubber has been a standard choice for many years due to its durability and resistance to fuel-related chemicals. However, it's important to note that natural rubber can degrade over time, especially when exposed to certain types of fuel, such as ethanol blends. Synthetic rubber compounds, like EPDM (Ethylene Propylene Diene Monomer), offer improved resistance to fuel degradation and temperature changes. These synthetic materials are less prone to cracking and can provide a longer-lasting solution for fuel lines.
- Reinforced Construction: To enhance the durability of the fuel line, consider materials with reinforced construction. This involves adding layers or braiding the material to provide extra strength. For example, a braided fuel line uses a steel or stainless steel wire core surrounded by a rubber or synthetic layer. This construction method makes the fuel line more flexible while also providing structural integrity, reducing the risk of damage from impacts or vibrations. Reinforced fuel lines are particularly useful in high-performance vehicles or those with modified engines.
- Temperature and Chemical Resistance: Fuel lines should be able to withstand the temperature fluctuations and chemical properties of the fuel they carry. Some fuels, especially those with higher alcohol content, can be corrosive and accelerate the degradation of certain materials. Look for fuel lines made from materials like nylon, which offers excellent chemical resistance and can handle a wide range of temperatures. Nylon fuel lines are known for their durability and ability to resist fuel-related degradation.
- Compatibility and Standards: Ensure that the chosen material is compatible with the type of fuel your vehicle uses. Different fuels have varying properties, and some materials may not be suitable for all types. Additionally, check for industry standards and certifications. For instance, SAE (Society of Automotive Engineers) J1728 is a standard for fuel line materials, providing guidelines for performance and durability. Adhering to these standards ensures that the fuel line meets the required specifications.
In summary, selecting the right material for your fuel line is essential to maintain the integrity of your vehicle's fuel system. Consider the type of fuel, temperature range, and the specific requirements of your vehicle. By choosing materials like synthetic rubber, reinforced nylon, or braided options, you can ensure that your fuel lines remain corrosion-free, flexible, and capable of withstanding the demands of your engine's fuel delivery system.
Fuel Line Removal: Mustang 2007 Fuel Pump Access Guide
You may want to see also
Line Diameter: Ensure the fuel line diameter matches the engine's requirements for optimal flow
When it comes to maintaining your vehicle's fuel system, one crucial aspect often overlooked is the fuel line diameter. Ensuring the correct diameter of the fuel line is essential for optimal engine performance and longevity. Here's why it matters and how to ensure you get it right.
The fuel line, also known as the fuel line hose, is responsible for transporting fuel from the tank to the engine. The diameter of this line is critical because it directly impacts the flow rate of fuel. If the line is too small, it can restrict fuel flow, leading to potential performance issues. Conversely, a line that is too large may cause unnecessary pressure and potentially lead to fuel wastage.
Engine manufacturers design their engines with specific fuel flow requirements in mind. These requirements are carefully calculated to ensure the engine operates efficiently and safely. When the fuel line diameter matches these specifications, it allows for the optimal flow of fuel, ensuring that the engine receives the precise amount of fuel it needs at any given moment. This results in improved performance, better fuel efficiency, and reduced emissions.
To ensure the correct fuel line diameter, it is essential to consult your vehicle's owner's manual or the manufacturer's specifications. These resources will provide detailed information about the recommended fuel line size for your specific engine. Measure the existing fuel line (if any) or use the provided specifications to choose the appropriate replacement line. Remember, using the correct diameter ensures a seamless fit and optimal performance.
In summary, paying attention to the fuel line diameter is a simple yet crucial step in maintaining your vehicle's fuel system. By matching the line's diameter to the engine's requirements, you can optimize fuel flow, enhance performance, and ensure your engine operates efficiently and reliably. Always refer to the manufacturer's guidelines for accurate specifications.
GTO Fuel Line Routing: Unraveling the Optimal Length
You may want to see also
Installation Technique: Proper installation techniques prevent leaks and ensure a secure connection
When dealing with fuel lines, proper installation is crucial to prevent leaks and ensure a secure connection. Here's a detailed guide on the installation technique:
Preparation: Before beginning the installation, ensure you have the necessary tools and materials, including the fuel line itself, fittings, and any required seals or gaskets. Inspect the fuel line for any signs of damage or wear. If any issues are found, replace the affected section before proceeding.
Clamping and Securing: Start by identifying the points where the fuel line needs to be clamped and secured. Use appropriate-sized clamps or fittings that are compatible with the fuel line material. Tighten the clamps securely, ensuring they are neither too loose nor too tight. Over-tightening can damage the fuel line, while under-tightening may lead to leaks. Use a wrench or a specialized tool for this step to achieve the correct torque.
Connection Technique: When connecting the fuel line to fittings or other components, employ a proper connection technique. Start by inserting the fuel line into the fitting until it is fully seated. Then, tighten the fitting using a wrench, again ensuring you don't overtighten. The connection should be snug, with no visible gaps or movement. Consider using thread seal tape or pipe compound on the threads to enhance the seal and prevent leaks.
Testing for Leaks: After the installation, it's crucial to test for any potential leaks. Start the engine and listen for any unusual noises, especially hissing or roaring sounds, which could indicate a fuel leak. Check for any signs of fuel dripping or pooling around the connections. If any leaks are detected, immediately disconnect the fuel line and inspect the connections. Tighten or re-tighten the fittings as necessary and retest.
Final Adjustments: Once you've confirmed there are no leaks, make any final adjustments to ensure a secure and tight installation. Double-check that all clamps and fittings are secure and that the fuel line is properly aligned and positioned. Ensure that there are no sharp bends or kinks in the line, as these can cause pressure buildup and potential leaks over time.
Remember, proper installation techniques are essential to maintain the integrity of the fuel system and prevent costly repairs or safety hazards. Always follow manufacturer guidelines and best practices for your specific fuel line and vehicle.
Fuel Line Hose Connections: The Ultimate Guide to Choosing the Right Method
You may want to see also
Pressure Testing: Regularly test fuel lines for leaks and pressure to maintain safety
Pressure testing fuel lines is a critical aspect of vehicle maintenance that ensures the safety and efficiency of your engine. Over time, fuel lines can develop leaks or pressure issues, which can lead to engine misfires, reduced performance, and even potential fires. Regular pressure testing allows you to identify these problems early on, preventing costly repairs and ensuring your vehicle operates optimally.
The process of pressure testing involves using specialized equipment to measure the pressure within the fuel lines. This is typically done by connecting a pressure gauge to the fuel line and applying a controlled amount of pressure. The gauge will then display the pressure reading, which should be within a specific range for your vehicle's make and model. If the pressure is too high or too low, it indicates a potential issue that needs to be addressed.
When performing pressure tests, it's essential to look for any signs of leaks. A leak can be identified by checking for fuel residue or moisture around the fuel line connections, as well as by using a soapy water solution to create a foam. If you notice any bubbles forming, it suggests a leak, and you should investigate further. Leaks can occur due to worn-out rubber components, corrosion, or improper installation, and they should be repaired or replaced immediately to prevent fuel contamination and potential engine damage.
In addition to checking for leaks, pressure testing also helps in identifying pressure drops. A pressure drop can occur when the fuel pump fails to maintain the required pressure, leading to reduced engine performance. This issue is often caused by a clogged fuel filter or a faulty fuel pump, and it can be resolved by replacing these components. Regular testing ensures that any pressure drops are caught early, allowing for prompt repairs and maintaining the engine's optimal performance.
To ensure the best results, it is recommended to consult your vehicle's manual for specific pressure range guidelines. Different vehicles may have varying acceptable pressure limits, and testing against these standards will help you identify any deviations. Regular pressure testing, ideally performed annually or every 10,000 miles, can significantly contribute to the longevity and reliability of your vehicle's fuel system. By taking this proactive approach to maintenance, you can avoid potential breakdowns and keep your engine running smoothly.
Understanding Impulse Fuel Lines: Powering Chainsaws Efficiently
You may want to see also
Environmental Factors: Consider temperature and UV exposure to prevent fuel line damage
When it comes to maintaining your vehicle's fuel system, it's crucial to understand the impact of environmental factors, particularly temperature and ultraviolet (UV) exposure, on the fuel lines. These factors can significantly contribute to the degradation and potential damage of fuel lines, leading to costly repairs and performance issues. Here's a detailed guide on how to protect your fuel lines from environmental damage:
Temperature Extremes: Fuel lines are designed to withstand a certain range of temperatures, but prolonged exposure to extreme conditions can be detrimental. In cold climates, fuel can become thick and difficult to flow, causing pressure buildup in the fuel lines. This may lead to cracks or leaks, especially if the fuel lines are made of rubber. To prevent this, consider using a fuel line insulator or a fuel line heater, especially during winter months. Insulators provide an extra layer of protection against temperature fluctuations, while heaters can maintain a consistent temperature, ensuring the fuel remains in a usable state. On the other hand, hot environments can cause fuel lines to expand and contract rapidly, potentially leading to cracks or separation from the fuel tank. Park your vehicle in shaded areas or use sunshades to minimize direct UV exposure, which can accelerate the aging process of fuel lines.
UV Radiation and Sun Damage: Ultraviolet (UV) radiation from the sun is a significant contributor to the deterioration of fuel lines, especially those made of rubber. UV rays can cause the rubber to become brittle and crack over time. This damage is often noticeable as small, white cracks or splits along the length of the fuel line. To mitigate this risk, park your vehicle in shaded areas or use a car cover, especially during extended periods of sun exposure. Additionally, consider applying a UV-resistant coating or sealant to the fuel lines, which can provide an extra layer of protection against the sun's harmful rays. Regularly inspecting the fuel lines for any signs of damage and replacing them if necessary is essential to maintaining a healthy fuel system.
Preventative Measures: To ensure the longevity of your fuel lines, it's essential to take preventative measures. Park your vehicle in a cool, shaded area whenever possible, especially during hot summer days. If you live in an area with extreme temperature variations, consider using a fuel line protectant or a fuel system cleaner to maintain optimal performance. These products can help lubricate the fuel lines, prevent clogs, and reduce the risk of damage from temperature extremes. Additionally, keep an eye on the fuel line connections and ensure they are secure and free from corrosion. Regularly checking and tightening loose connections can prevent fuel leaks and potential engine damage.
By considering the environmental factors of temperature and UV exposure, you can take proactive steps to protect your fuel lines and ensure the overall health of your vehicle's fuel system. Remember, proper maintenance and awareness of these environmental influences can save you from potential headaches and costly repairs down the road.
Optimizing Performance: Choosing the Right Fuel Line Size for Trans Lines
You may want to see also
Frequently asked questions
Depressurizing a fuel line is a crucial step in any fuel system maintenance or repair process. It involves releasing the built-up pressure in the fuel line to ensure safe and efficient fuel delivery to the engine. This process helps to prevent fuel line damage, leaks, and potential engine issues caused by excessive pressure.
There are a few signs that may indicate the need for depressurization. These include fuel pump noise, hard starts, frequent stalling, or a noticeable decrease in engine performance. If you experience any of these symptoms, it's essential to inspect the fuel system and consider depressurization as a potential solution.
The tools and materials needed can vary depending on the vehicle and fuel system design. Generally, you will require a fuel pressure gauge, a fuel line depressurizer tool (if applicable), a wrench or socket set, and possibly a fuel filter. It's recommended to consult the vehicle's manual or seek professional advice to determine the specific tools required for your make and model.
While some basic depressurization techniques can be performed by vehicle owners, it is often best to seek professional assistance, especially for complex fuel systems. Depressurizing a fuel line incorrectly can lead to fuel leaks, engine damage, or other hazardous situations. It's advisable to consult a qualified mechanic or refer to the vehicle's manual for guidance on performing this task safely.
Yes, there are risks involved if not done correctly. Releasing fuel pressure too quickly can cause a backflow of fuel, potentially leading to spills or engine damage. Additionally, working with fuel systems requires caution to avoid contact with hot surfaces or electrical components. Always ensure the engine is cool and disconnected before performing any fuel system maintenance.