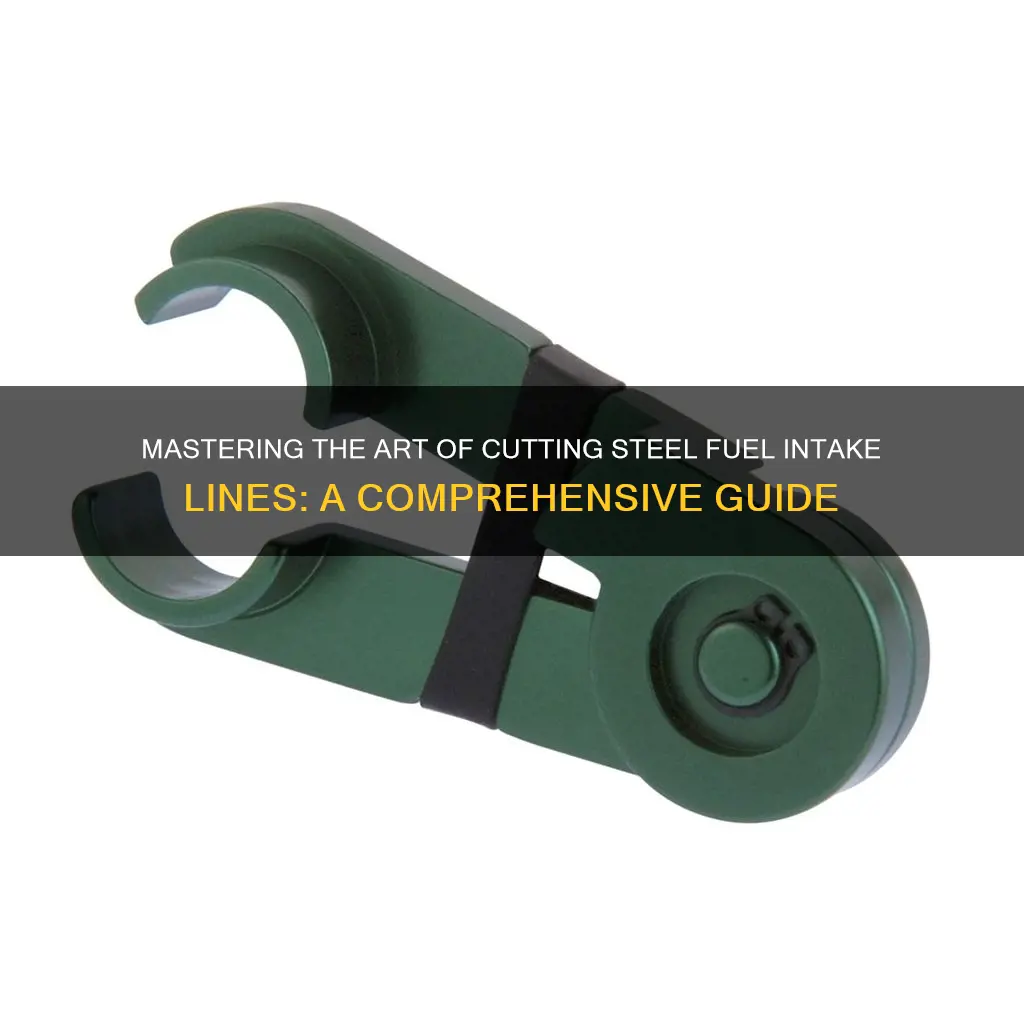
Cutting and installing a steel fuel intake line requires precision and care to ensure a safe and efficient setup. This process involves accurately measuring and marking the steel line, using appropriate cutting tools, and ensuring a secure connection to the fuel source and engine. It's crucial to follow safety guidelines, wear protective gear, and have a thorough understanding of the vehicle's fuel system to avoid any potential hazards. Proper preparation and attention to detail will contribute to a successful installation.
What You'll Learn
- Safety Gear: Wear gloves, goggles, and a respirator to protect yourself from sharp edges and fumes
- Line Inspection: Check for damage, bends, and kinks using a flashlight and your hands
- Cutting Tools: Use a steel cutting torch or a band saw for clean, precise cuts
- Pipe Cutter: Consider using a pipe cutter for larger fuel lines, ensuring a tight fit
- Welding: If necessary, use a small welder to join ends, ensuring a strong bond
Safety Gear: Wear gloves, goggles, and a respirator to protect yourself from sharp edges and fumes
When working with steel fuel intake lines, it's crucial to prioritize your safety and that of those around you. The process of cutting steel can involve sharp edges and potentially hazardous fumes, so it's essential to take the necessary precautions. Here's a detailed guide on the safety gear you should consider wearing:
Gloves: Protecting your hands is of utmost importance. When cutting steel, you'll be handling sharp tools and materials. Wear heavy-duty gloves made from durable materials like leather or synthetic blends designed for industrial use. These gloves should provide a secure grip and protect your hands from cuts, punctures, and burns. Look for gloves with reinforced fingertips and palms for added durability.
Goggles: Eye protection is critical to prevent injuries from flying debris and sparks. Choose safety goggles that offer full coverage, ensuring that your eyes and the surrounding areas are shielded. Goggles should be impact-resistant and provide clear vision without distortion. Consider wearing a face shield in addition to goggles for extra protection, especially when working in close proximity to the cutting area.
Respirator: Cutting steel can release harmful fumes and particles into the air. Inhaling these fumes can be dangerous and may lead to respiratory issues. Wear a respirator mask that is suitable for the task at hand. Look for a mask with a high filtration efficiency, preferably one that can filter out both solid particles and fumes. Ensure a proper fit to prevent air leakage, and consider the comfort and ease of breathing to encourage extended use.
Additionally, it is recommended to wear a dust mask or a surgical mask to cover your nose and mouth, providing an extra layer of protection against inhaling small particles and dust. Remember, proper safety gear not only protects you but also ensures that your work environment remains safe for others. Always assess the potential risks and choose the appropriate safety gear accordingly.
Unclogging Toro 500 Series Fuel Lines: A Step-by-Step Guide
You may want to see also
Line Inspection: Check for damage, bends, and kinks using a flashlight and your hands
When inspecting a steel fuel intake line, it's crucial to thoroughly examine its condition to ensure optimal performance and safety. Here's a step-by-step guide on how to inspect the line for damage, bends, and kinks using basic tools:
Flashlight Inspection: Begin by using a flashlight to illuminate the interior of the fuel line. This is especially important if the line is located in a dark or confined space. Shine the light along the entire length of the line, paying close attention to any areas where the line changes direction or where it might be more susceptible to damage. Look for any signs of corrosion, rust, or pitting, as these can compromise the line's integrity. Also, check for any visible cracks or splits in the steel material.
Physical Examination: After the initial visual inspection, use your hands to feel the fuel line. Run your fingers along the length, checking for any bumps, ridges, or uneven surfaces. These could indicate bends or kinks that might restrict fuel flow or cause damage over time. Ensure you inspect all accessible areas, including areas where the line connects to other components like the fuel pump or the engine.
Bends and Kinks: Carefully examine the line for any sharp bends or kinks. These can occur due to installation issues or previous repairs. Bends should be gradual and not sharp, as sharp bends can lead to stress concentrations and potential failure points. Kinks, where the line changes direction abruptly, can also cause issues. If you find any significant bends or kinks, it may be necessary to adjust or straighten the line carefully to ensure a smooth and continuous path.
Damage Assessment: During the physical examination, be on the lookout for any signs of damage, such as cuts, punctures, or tears. These could be caused by various factors, including road debris, tool damage, or previous repairs. If you identify any damage, it's essential to address it promptly. In some cases, minor damage might be repairable, but severe damage may require replacing the entire fuel intake line.
Remember, regular inspections are vital to maintaining the health of your fuel system. By following these steps and paying close attention to detail, you can identify potential issues early on and take the necessary actions to ensure the fuel intake line functions correctly and safely.
Boost Engine Performance: Inline Fuel Pump Upgrade for Optimal Power
You may want to see also
Cutting Tools: Use a steel cutting torch or a band saw for clean, precise cuts
When it comes to cutting a steel fuel intake line, using the right tools is crucial for a clean and precise cut. One of the most effective methods is to employ a steel cutting torch, which is specifically designed for cutting through metal. This tool utilizes a high-temperature flame to melt and separate the metal, allowing for a smooth and accurate cut. The torch's precision is key, as it enables you to carefully guide the flame along the desired cut line, ensuring minimal damage to the surrounding area. It's important to choose a torch with an appropriate tip size and heat output for the thickness of the fuel intake line you're working with.
Another reliable option for cutting steel fuel intake lines is a band saw. This power tool is known for its ability to make clean, straight cuts on various materials, including steel. The band saw's circular blade provides a smooth and precise cut, especially when compared to a standard hacksaw. The band saw's design allows for better control and accuracy, making it ideal for cutting through the fuel intake line without causing any unnecessary damage or distortion. When using a band saw, ensure that the blade is sharp and properly tensioned to achieve the best results.
To begin the cutting process, position the fuel intake line securely on a stable work surface. For the torch method, hold the torch at a slight angle to the line, maintaining a consistent flame contact along the cut path. Practice good flame control to avoid overheating or burning the surrounding areas. When using a band saw, set the blade depth and speed according to the line's thickness, and slowly guide the saw along the desired cut path.
Both the steel cutting torch and the band saw offer advantages in terms of precision and control. The torch provides a more focused heat source, allowing for intricate cuts, while the band saw offers a continuous cut with minimal effort. Choose the method that best suits your skill level and the specific requirements of the project. Remember, taking the time to select the right cutting tool and technique will result in a professional-looking finish and ensure the longevity of the fuel intake line.
Will Heet Unfreeze Fuel Line? A Comprehensive Guide
You may want to see also
Pipe Cutter: Consider using a pipe cutter for larger fuel lines, ensuring a tight fit
When dealing with larger fuel lines, especially those made of steel, using a pipe cutter is a reliable method to ensure a precise and tight fit. This technique is particularly useful for maintaining the structural integrity of the fuel system and preventing potential leaks. Here's a step-by-step guide on how to effectively use a pipe cutter for this purpose:
Understanding the Process:
Before you begin, it's crucial to understand the mechanics of cutting steel fuel lines. Steel is a harder material compared to copper or brass, so the cutting process requires more precision and force. Pipe cutters are designed to provide a clean and accurate cut, ensuring that the ends of the pipe are smooth and free from any burrs that could cause damage or interference.
Gathering the Tools:
For this task, you'll need a few essential tools. Firstly, a high-quality pipe cutter suitable for steel is essential. These cutters often have adjustable jaws to accommodate different pipe sizes. Additionally, you'll require a pair of pliers or a pipe wrench to apply the necessary force during the cutting process. It's also recommended to have a file or a deburring tool to smooth out any rough edges after the cut.
Preparation and Safety:
Safety should always be a priority when working with tools and fuel lines. Ensure that you are wearing appropriate personal protective equipment, such as gloves and safety goggles, to protect your hands and eyes from any potential hazards. Before starting, inspect the fuel line to identify the desired cut point. Mark the location with a pencil or a piece of tape to guide your cutting process.
Cutting Process:
Place the pipe cutter around the marked section of the fuel line. Ensure that the cutter's jaws are properly aligned and adjusted to the desired pipe diameter. Apply firm pressure and rotate the handles of the pipe cutter in a smooth, controlled motion. Cut through the steel until the desired length is achieved. For larger fuel lines, multiple cuts may be necessary, and each cut should be precise to maintain the integrity of the fuel system.
Finishing and Fitting:
Once the cutting is complete, inspect the ends of the pipe for any roughness or burrs. Use the file or deburring tool to smooth out these edges, ensuring a clean and safe connection. After finishing, you can now fit the cut ends together, ensuring a tight and secure connection. This method guarantees a professional-grade finish and minimizes the risk of fuel leaks.
By following these steps, you can effectively use a pipe cutter to cut and fit larger steel fuel lines, ensuring a reliable and safe fuel system. Remember, precision and patience are key when working with steel, and the right tools will make the process much more manageable.
Polaris Sportsman Fuel Line Sizes: A Comprehensive Guide
You may want to see also
Welding: If necessary, use a small welder to join ends, ensuring a strong bond
When dealing with steel fuel intake lines, welding can be a crucial step to ensure a secure and long-lasting repair or modification. Here's a detailed guide on how to approach this task:
Preparation: Before you begin welding, it's essential to prepare the work area and the steel fuel intake line. Ensure you have a well-ventilated workspace and proper safety gear, including welding gloves, goggles, and a respirator. Clean the surfaces where you'll be welding to remove any dirt, grease, or debris. This preparation step is vital to ensure a strong bond between the welded parts.
Welding Technique: If you need to join the ends of the fuel intake line, a small welder can be the perfect tool for the job. Here's a step-by-step process: Start by clamping the two ends securely together, ensuring they are aligned properly. Use a small, handheld welder with a suitable welding rod for steel. Apply the rod to the joint, maintaining a consistent arc and a steady hand. Keep the welding speed controlled to avoid overheating the metal. After the initial pass, add more filler material and continue the welding process, ensuring the bead is smooth and continuous.
Ensuring a Strong Bond: The key to a successful weld is creating a strong bond between the steel components. Here are some tips to achieve this: Use a suitable welding rod with a composition that matches the base steel to ensure compatibility. Apply the correct amount of filler material, neither too much nor too little, to avoid defects. Practice good welding techniques, such as maintaining an even heat input and avoiding excessive spatter. After welding, inspect the joint for any defects like porosity or cracks, and re-weld if necessary.
Post-Welding: Once the welding is complete, allow the joint to cool slowly to prevent warping or stress. After cooling, perform a thorough inspection to ensure the weld is strong and aesthetically pleasing. Consider using a non-destructive testing method like ultrasonic testing to verify the integrity of the weld. If the weld meets your standards, you can proceed with further modifications or installations.
Remember, welding steel fuel intake lines requires precision and attention to detail. Always follow safety protocols and consider seeking guidance from experienced welders if you're new to this process. Proper preparation and technique will result in a robust and reliable repair.
Mastering Carb Fuel Lines: A Comprehensive Guide
You may want to see also
Frequently asked questions
To cut a steel fuel intake line, you will need a good-quality steel-cutting torch or plasma cutter. A pair of sharp, heat-resistant cutting pliers or a wire cutter can also be useful for making precise cuts. Additionally, safety gear like heat-resistant gloves, goggles, and a respirator is essential to protect yourself during the cutting process.
Achieving a clean cut is crucial to prevent damage to the fuel system. Start by marking the cutting points with a permanent marker or chalk. Use the cutting torch or plasma cutter at a steady pace, maintaining an even flame or plasma arc. Keep the tool at a slight angle to the line to create a smooth cut. Avoid applying excessive force, as it may distort the line. Practice and patience are key to getting a professional finish.
Absolutely! Working with steel and high-temperature tools carries risks. Always ensure you are in a well-ventilated area to avoid inhaling fumes. Wear protective clothing, including heat-resistant aprons and sleeves, to shield your skin. Keep a fire extinguisher nearby, and have a fire blanket readily available in case of emergencies. It's also a good practice to work with an assistant who can help with holding and guiding the line.
If the line is damaged, carefully assess the extent of the damage. For small tears or punctures, you might be able to repair it using a steel welding rod and a small torch. For more severe damage or kinks, it's best to replace the affected section with a new piece of steel line. Ensure you follow proper welding techniques and safety protocols during any repair or replacement process.
While a saw can be used for cutting steel, it is generally not the most efficient or precise method for fuel intake lines. A torch or plasma cutter is recommended as they provide a clean, straight cut and can handle the thickness of steel fuel lines. However, if you are working with thin-walled lines, a saw might be sufficient, but always prioritize safety and precision.