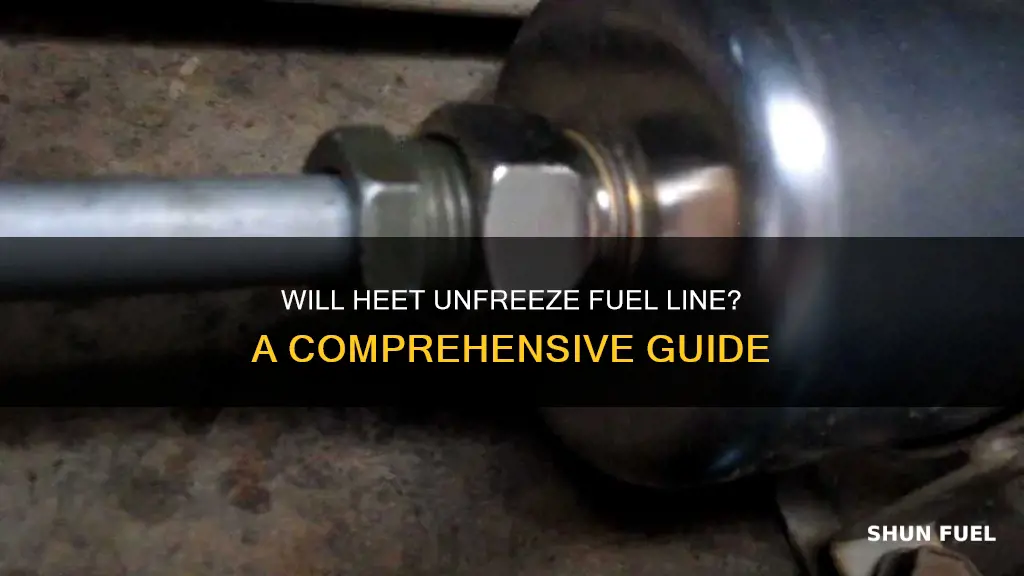
The process of unfreezing fuel lines in a vehicle can be a challenging task, especially when dealing with a will heater. This specialized tool is designed to melt ice and frost from fuel lines, ensuring a smooth and efficient flow of fuel to the engine. Understanding the proper use and safety precautions of a will heater is crucial for any vehicle owner, as it can prevent costly repairs and ensure optimal engine performance during colder months.
What You'll Learn
- Fuel Line Material: Different materials affect flexibility and resistance to fuel degradation
- Temperature Sensitivity: Fuel performance varies with temperature extremes, impacting flow and quality
- Pressure Regulation: Maintaining optimal pressure ensures consistent fuel delivery and engine performance
- Vibration Resistance: Fuel lines must withstand engine vibrations without leaking or breaking
- Compatibility: Fuel line compatibility with fuel type and engine system is crucial for reliability
Fuel Line Material: Different materials affect flexibility and resistance to fuel degradation
The choice of material for fuel lines is a critical aspect of vehicle maintenance, as it directly impacts the performance and longevity of the fuel system. Different materials offer varying levels of flexibility, durability, and resistance to fuel degradation, which are essential considerations for ensuring a reliable and efficient fuel supply.
One of the most common materials used for fuel lines is rubber, which is known for its flexibility and ability to withstand the corrosive effects of fuel. Natural rubber, in particular, has been a traditional choice due to its inherent properties. It can accommodate slight movements and vibrations within the engine bay, providing a flexible connection between the fuel tank and the engine. However, natural rubber may not be as resistant to fuel degradation as some other materials. Over time, certain fuels, especially those containing ethanol, can cause rubber to degrade, leading to cracks and leaks.
To address this issue, manufacturers often use synthetic rubbers, such as neoprene or EPDM (ethylene propylene diene monomer) rubber. These synthetic materials offer improved resistance to fuel degradation and are less susceptible to cracking. They are more flexible than natural rubber, allowing for easier installation and better accommodation of engine vibrations. Additionally, synthetic rubbers can maintain their integrity over a wider temperature range, making them suitable for various climates.
Another material gaining popularity in fuel lines is polyurethane. This material is highly resistant to fuel degradation and offers excellent flexibility. Polyurethane fuel lines are known for their durability and ability to withstand harsh engine environments. They are less prone to cracking and can provide a long-lasting solution for fuel delivery. The flexibility of polyurethane ensures that the fuel lines can move with the engine components without becoming stiff or brittle over time.
In contrast, some materials may not be ideal for fuel lines due to their lack of flexibility or resistance to fuel degradation. For example, rigid materials like steel or aluminum can be used in specific applications but are generally not suitable for the majority of fuel lines. These materials offer little flexibility and can become stiff and brittle, making them prone to cracking and failure. Additionally, certain plastics, if not properly selected, may not withstand the chemical properties of fuels, leading to premature degradation.
In summary, the material selection for fuel lines is crucial to ensure optimal performance and longevity. Natural and synthetic rubbers provide flexibility but may vary in resistance to fuel degradation. Polyurethane stands out for its superior resistance and flexibility. Understanding the properties of different materials allows vehicle owners and mechanics to make informed decisions when replacing or upgrading fuel lines, ensuring a reliable fuel supply for the vehicle's operation.
Silverado Fuel Line Sizes: An In-Depth Guide for 2003 Models
You may want to see also
Temperature Sensitivity: Fuel performance varies with temperature extremes, impacting flow and quality
The performance of fuel in engines is significantly influenced by temperature, and this relationship is particularly critical when considering the impact of extreme temperatures on fuel flow and quality. Temperature sensitivity in fuel systems is a well-documented phenomenon, and understanding its effects is essential for maintaining optimal engine performance and longevity.
In cold climates, fuel can become more viscous and thicker, leading to reduced flow rates through fuel lines and injectors. This temperature-induced thickening can result in inadequate fuel supply to the engine, causing poor performance, reduced power, and even starting difficulties. The process of 'unfreezing' fuel lines, as suggested by the search term, is a common practice to address this issue. By applying heat to the fuel lines, often through the use of electric heaters or warm fuel, the fuel's viscosity is reduced, ensuring a smoother flow and improved engine operation.
Conversely, high temperatures can also have detrimental effects on fuel quality. Over time, fuel can degrade when exposed to elevated temperatures, leading to the formation of varnish and sludge within the fuel system. These deposits can clog fuel injectors, reducing their efficiency and potentially causing engine misfires or poor acceleration. Additionally, high temperatures can accelerate the oxidation of fuel, resulting in the formation of water and ethanol, which can further contaminate the fuel system and lead to performance issues.
To mitigate these temperature-related problems, fuel systems often incorporate various design features and additives. Fuel lines with flexible materials that can withstand temperature fluctuations help maintain fuel flow. Some engines also use fuel heaters to ensure that the fuel reaches the engine at an optimal temperature, especially in cold environments. Furthermore, fuel stabilizers and antioxidants are added to prevent degradation and maintain fuel quality over a wide range of temperatures.
In summary, temperature sensitivity in fuel performance is a critical aspect of engine maintenance. Extreme temperatures can impact fuel flow and quality, affecting engine operation and longevity. By understanding these temperature-related challenges, engineers and vehicle owners can implement appropriate measures to ensure consistent and reliable fuel delivery, thereby optimizing engine performance across various environmental conditions.
Mastering the Art of Fuel Line Wrenching: A Comprehensive Guide
You may want to see also
Pressure Regulation: Maintaining optimal pressure ensures consistent fuel delivery and engine performance
Pressure regulation is a critical aspect of fuel system management, especially in cold climates where fuel lines can become frozen and block fuel flow. Maintaining optimal pressure ensures that the engine receives a consistent and steady supply of fuel, which is essential for optimal performance and longevity. When the fuel pressure is regulated properly, it ensures that the fuel pump operates efficiently, delivering the correct amount of fuel to the engine at the right time. This is particularly important in cold weather conditions, as low temperatures can cause fuel to thicken and restrict flow, leading to engine misfires, reduced power, and potential starting difficulties.
The process of pressure regulation involves monitoring and adjusting the fuel pressure to a specific range, typically between 40 and 60 psi (pounds per square inch) for most automotive applications. This range is ideal for ensuring that the engine operates efficiently and that the fuel system functions optimally. When the pressure is too low, the engine may not receive enough fuel, resulting in poor performance and potential damage. Conversely, excessive pressure can lead to fuel spray issues, engine misfires, and even fuel pump failure over time.
To maintain optimal pressure, fuel pressure regulators are employed in the fuel system. These regulators are designed to control the pressure of the fuel as it enters the engine. They work by reducing the pressure of the fuel to the desired level before it reaches the engine's intake system. This ensures that the fuel is delivered at the correct pressure, allowing for efficient combustion and optimal engine performance. Regular maintenance and inspection of the fuel pressure regulator are essential to ensure its proper functioning.
In addition to the fuel pressure regulator, other components contribute to pressure regulation. These include the fuel pump, which draws fuel from the tank and delivers it to the regulator, and the fuel injectors or carburetor, which meter and spray the fuel into the engine's cylinders. Proper calibration and maintenance of these components are crucial to achieving the desired pressure and ensuring consistent fuel delivery.
By maintaining optimal pressure through careful regulation, you can ensure that your engine receives a consistent and reliable supply of fuel, even in cold weather conditions. This results in improved engine performance, reduced wear and tear, and a more efficient and dependable vehicle overall. Regular checks and adjustments of the fuel pressure can help prevent issues related to fuel delivery, ensuring a smooth and powerful driving experience.
Dodge Truck Fuel Line Sizes: A Comprehensive Guide
You may want to see also
Vibration Resistance: Fuel lines must withstand engine vibrations without leaking or breaking
The fuel lines in an engine are crucial components that deliver fuel from the tank to the engine's combustion chamber. They must be designed to withstand the intense vibrations and stresses encountered during engine operation. Vibration resistance is a critical aspect of fuel line design, ensuring that these lines remain intact and functional over the life of the vehicle.
Engine vibrations can cause fuel lines to flex and move, potentially leading to leaks or even breaks. This is especially critical in high-performance vehicles or those operating in rough terrain, where the engine experiences more extreme vibrations. To address this, fuel lines are often constructed with flexible materials that can absorb and distribute the energy from vibrations. These materials may include rubber, silicone, or specialized synthetic compounds that provide a certain level of elasticity.
One effective method to enhance vibration resistance is by incorporating a protective layer or coating around the fuel line. This protective layer can be made of materials like steel braiding or a durable plastic, which adds strength and flexibility. The braiding technique, for instance, involves weaving a steel wire around the fuel line, creating a sturdy yet flexible structure. This design ensures that the fuel line can move with the engine while maintaining its structural integrity.
Additionally, the design of the fuel line's connectors and fittings plays a vital role in vibration resistance. These connections should be secure and robust to prevent any movement or dislodging during operation. Engineers often use specialized fasteners and seals to ensure a tight and vibration-resistant bond between the fuel line and other engine components.
In summary, achieving vibration resistance in fuel lines is essential for the reliable operation of an engine. By utilizing flexible materials, protective coatings, and well-designed connectors, engineers can ensure that fuel lines withstand the rigors of the engine's environment, providing a consistent and safe fuel supply to the engine's combustion chamber. This attention to detail in fuel line design contributes to the overall performance and longevity of the vehicle.
Understanding Impulse Fuel Lines: Powering Chainsaws Efficiently
You may want to see also
Compatibility: Fuel line compatibility with fuel type and engine system is crucial for reliability
The compatibility of fuel lines with the type of fuel and the engine system is an essential aspect of vehicle maintenance that cannot be overlooked. When it comes to fuel lines, using the right components is critical to ensure optimal performance and long-term reliability. This is especially true for vehicles that operate on different types of fuel, such as gasoline, diesel, or alternative fuels like ethanol blends.
Fuel lines are responsible for transporting fuel from the tank to the engine, and their material and design must be compatible with the specific fuel being used. For instance, gasoline fuel lines are typically made of materials that can withstand the volatility of gasoline, which may include rubber or synthetic compounds. In contrast, diesel fuel lines often require materials that can handle the higher pressure and lubricating properties of diesel fuel, such as braided hoses or specialized rubber compounds.
Engine systems also play a significant role in determining fuel line compatibility. Modern engines, especially those with electronic fuel injection systems, require precise fuel delivery to ensure optimal combustion and performance. The fuel lines must be able to handle the pressure and temperature changes that occur during the fuel injection process. For example, in a gasoline engine, the fuel lines should be able to withstand the high pressure and temperature fluctuations associated with direct injection systems.
Using incompatible fuel lines can lead to several issues. One common problem is fuel leakage, which can result from materials that are not resistant to the corrosive properties of certain fuels. Over time, this can cause engine misfires, reduced performance, and even engine damage. Additionally, incompatible fuel lines may not provide the necessary flexibility and durability required for the specific engine system, leading to premature wear and potential failure.
To ensure reliability, it is crucial to consult the vehicle's manual or seek professional advice when selecting fuel lines. Manufacturers often provide specific recommendations for fuel line materials and types based on the engine's design and fuel requirements. By choosing the right fuel lines, vehicle owners can maintain the integrity of their fuel system, optimize engine performance, and avoid potential issues related to fuel incompatibility.
Fuel Line Routing: Understanding the Path to the Engine
You may want to see also
Frequently asked questions
Unfreezing fuel lines is a process to ensure that the fuel in your vehicle remains fluid and functional during cold weather. Fuel can become thick and gel-like when temperatures drop, which can lead to engine starting issues and reduced performance. By unfreezing the fuel lines, you prevent the fuel from clogging the system and ensure a smooth flow of fuel to the engine.
Unfreezing fuel lines can be done using a few simple methods. One common approach is to use a fuel line unfreezer product, which is typically a concentrated liquid that can be poured into the fuel tank. These products are designed to lower the freezing point of the fuel, allowing it to flow freely. Alternatively, you can use a fuel stabilizer, which can be added to the fuel tank to prevent gelling in the first place.
While unfreezing fuel lines is generally safe, it is important to take certain precautions. Always ensure that you are working in a well-ventilated area when using any chemicals. Wear protective gear, such as gloves and goggles, to avoid skin and eye irritation. Additionally, be cautious when handling fuel, as it is flammable. It is recommended to consult a professional mechanic if you are unsure about the process or if your vehicle has specific requirements.
Yes, there are several preventative measures you can take to minimize the need for unfreezing fuel lines. One effective method is to use a fuel stabilizer regularly, as mentioned earlier. This can be added to your fuel tank before winter to ensure the fuel remains stable and flowable. Additionally, keeping your vehicle in a garage or using a fuel-preserving additive can help maintain the fuel's quality and prevent gelling. Regularly checking and replacing old fuel filters can also contribute to a healthier fuel system.