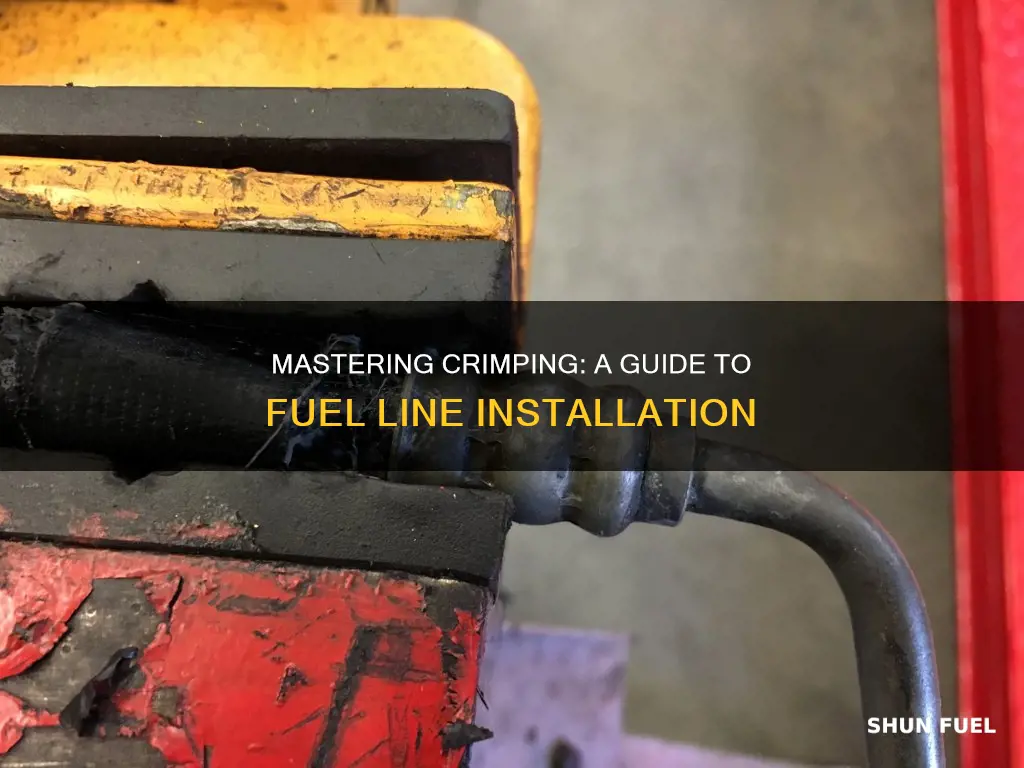
Crimping fuel lines is a crucial skill for anyone working on vehicles, especially when it comes to fuel system repairs or modifications. This process involves connecting fuel lines to various components, such as the fuel tank, pump, and engine, using specialized tools and techniques. By understanding the proper crimping methods, you can ensure a secure and leak-free connection, which is essential for maintaining the vehicle's performance and safety. This guide will provide a step-by-step overview of the crimping process, including the necessary tools, techniques, and safety precautions to ensure a successful and reliable fuel line installation.
What You'll Learn
- Prepare Tools: Gather crimping tools, fuel line, and cleaning supplies
- Clean Line: Remove dirt and debris from the fuel line using a solvent
- Cut Line: Measure and cut the fuel line to the desired length
- Crimp Fittings: Use a crimping tool to attach fittings securely
- Test Connection: Inspect the connection for leaks and ensure proper fit
Prepare Tools: Gather crimping tools, fuel line, and cleaning supplies
Before you begin the process of crimping a fuel line, it's crucial to ensure you have all the necessary tools and materials ready. This preparation will make the task more efficient and help you avoid any unnecessary complications. Here's a step-by-step guide on what you need to gather:
Crimping Tools:
- Crimping Tool: This is the primary instrument you'll use to connect the fuel line to the vehicle's system. It typically consists of a pair of dies or jaws that can be adjusted to fit different sizes of fuel line fittings. Look for a crimping tool that is compatible with the fuel line fittings you are working with.
- Pliers: A good pair of pliers is essential for gripping and holding the fuel line securely during the crimping process. Ensure they have a comfortable grip and are made of durable material.
- Wire Cutter/Stripper: You'll need this tool to cut and strip the fuel line's protective covering, exposing the inner hose. It should be capable of handling the thickness of the fuel line material.
- Crimping Dies: These are specific dies designed for the type of crimp you need to create. They come in various sizes and shapes, depending on the fuel line fitting. Make sure you have the appropriate dies for your project.
Fuel Line:
Ensure you have the correct length and diameter of fuel line that matches the specifications of your vehicle. Measure and cut the fuel line to the desired length, allowing for some extra material at the ends for crimping.
Cleaning Supplies:
- Cleaning the fuel line and surrounding areas is essential to ensure a proper crimp connection. Gather the following:
- Fuel Line Cleaner: Use a specialized cleaner designed for fuel lines to remove any contaminants or debris.
- Cleaning Brushes: Soft-bristled brushes can help scrub the fuel line and remove any built-up dirt.
- Rag or Cloth: Have a clean, lint-free cloth ready for wiping down the fuel line and tools.
- Lubricant: A small amount of lubricant can be applied to the fuel line fitting to ensure a smooth crimp connection.
By gathering these tools and supplies in advance, you'll be well-prepared to tackle the crimping process efficiently and effectively. Remember to work in a well-ventilated area and follow safety guidelines when handling fuel lines and cleaning agents.
Gas Line Holes: Fuel Pump Performance and Safety Concerns
You may want to see also
Clean Line: Remove dirt and debris from the fuel line using a solvent
To ensure optimal performance and longevity of your fuel system, it's crucial to keep the fuel lines clean and free from contaminants. One effective method to achieve this is by using a solvent to remove dirt and debris from the fuel line. Here's a step-by-step guide on how to perform this cleaning process:
Step 1: Gather the Necessary Materials
Before you begin, make sure you have the required tools and materials. You will need a suitable solvent, such as a fuel line cleaner or a mild detergent mixed with water. Ensure you have a small spray bottle or a container to hold the solvent. Additionally, have a clean rag or cloth ready for wiping and a pair of gloves to protect your hands.
Step 2: Locate the Fuel Line
Identify the fuel line that needs cleaning. It is typically located beneath the vehicle, running from the fuel tank to the engine. Carefully inspect the line for any visible dirt, rust, or debris accumulation.
Step 3: Prepare the Solvent
Pour or spray the chosen solvent into the fuel line. Start with a small amount and assess its effectiveness. You can use a funnel to carefully introduce the solvent into the line if it's difficult to access. Allow the solvent to sit for a few minutes, giving it time to loosen and dissolve any contaminants.
Step 4: Flush Out the Debris
After the solvent has had time to work, it's time to flush out the dirt and debris. Use a garden hose or a dedicated fuel line flush kit to run water through the line. Start at the engine end and work your way back to the fuel tank. Ensure you flush thoroughly to remove any remaining contaminants.
Step 5: Rinse and Dry
Once the flushing process is complete, rinse the fuel line with clean water to remove any residual solvent. Make sure to dry the line completely afterward to prevent moisture-related issues. You can use a towel or allow it to air dry naturally.
By following these steps, you can effectively clean the fuel line, ensuring a smooth and efficient fuel supply to your engine. Regular maintenance and cleaning will contribute to better engine performance and help prevent potential issues caused by dirt and debris accumulation.
Fuel Pump Maintenance: A Step-by-Step Guide to Removing the Center Fuel Line
You may want to see also
Cut Line: Measure and cut the fuel line to the desired length
When it comes to working with fuel lines, precision is key. Measuring and cutting the fuel line to the correct length is an essential step to ensure a proper installation. Here's a detailed guide on how to measure and cut the fuel line accurately:
Step 1: Gather the Necessary Tools and Materials
Before you begin, make sure you have all the required tools and materials ready. You'll need a tape measure or a flexible measuring tool, a sharp utility knife or a fuel line cutter, and a pair of gloves for protection. Additionally, have the fuel line itself, the crimping tool, and the appropriate crimping sleeves or fittings readily available.
Step 2: Locate the Fuel Line and Mark the Measurement
Locate the fuel line that you need to cut. It is typically a flexible rubber or plastic tube that carries fuel from the tank to the engine. Use your tape measure or flexible measuring tool to determine the desired length of the fuel line. Measure from the point where the fuel line connects to the fuel tank to the point where it needs to be connected to the engine or other fuel-fed component. Mark this measurement on the fuel line with a permanent marker or a piece of tape.
Step 3: Prepare the Fuel Line for Cutting
Ensure that the fuel line is straight and free of any kinks or bends that could affect the cutting process. If the fuel line has any bends, carefully straighten it by gently pulling and smoothing it out. Take note of any existing markings or indicators on the fuel line, as these can help you align the cut accurately.
Step 4: Make the Cut
Using your sharp utility knife or a fuel line cutter, carefully cut along the marked measurement. Apply steady pressure and make a clean, straight cut. It's important to cut the fuel line at a 90-degree angle to ensure a proper connection later. If you're using a fuel line cutter, follow the manufacturer's instructions for the best results.
Step 5: Verify the Cut
Once the fuel line is cut, inspect the cut end to ensure it is smooth and free of any damage. Check that the cut is straight and aligned with any existing markings. If the cut is uneven or damaged, carefully trim any excess material using a sharp blade.
Remember, accurate measurement and cutting are crucial steps in the fuel line installation process. Take your time and double-check your measurements to avoid any issues during the crimping and assembly stages.
Ariens Snowblower Fuel Line Cleaning: A Step-by-Step Guide
You may want to see also
Crimp Fittings: Use a crimping tool to attach fittings securely
Crimping fuel lines is a crucial process in vehicle maintenance, ensuring a secure and reliable connection for fuel delivery. When it comes to crimping fittings, using the right tools and following a systematic approach is essential. Here's a step-by-step guide to help you master the art of crimping:
Gather the Tools and Materials: Before you begin, ensure you have the necessary tools and materials. You'll need a crimping tool specifically designed for fuel line fittings, which typically comes with different-sized dies to accommodate various pipe sizes. The tool should be compatible with the type of fitting you are using (e.g., compression, quick-connect, or flare fittings). Additionally, have the fuel line itself, the appropriate crimping dies, and a pair of pliers or a wire cutter for any necessary adjustments.
Prepare the Fuel Line: Start by cutting the fuel line to the desired length, ensuring a clean and precise cut. Remove any debris or burrs from the cut end using a file or sandpaper. This step is crucial to ensure a proper crimp and prevent any damage to the fitting.
Crimping Process: Now, it's time to crimp the fitting onto the fuel line. Place the fuel line into the crimping tool, aligning it with the designated area for the fitting. Ensure the line is secure and centered. Then, using the crimping tool, apply firm pressure to the handle, following the manufacturer's instructions for the specific fitting type. The goal is to create a secure connection by deforming the fitting's metal body around the fuel line. Apply pressure evenly and consistently, being careful not to over-crimp, as it can damage the fitting or fuel line.
Final Adjustments: After crimping, inspect the fitting for any signs of slippage or uneven pressure. If necessary, use the pliers or wire cutter to make minor adjustments to the crimp. Ensure the fitting is tight and secure, providing a reliable seal. Repeat this process for each fitting you need to crimp.
Safety and Practice: Crimping requires precision and practice. Always work in a well-ventilated area when handling fuel lines to ensure safety. Take your time and be patient, as rushing can lead to mistakes. With practice, you'll develop a feel for the right amount of pressure to apply, ensuring a professional-quality crimp every time. Remember, a well-crimped fuel line fitting is essential for maintaining a vehicle's performance and preventing fuel leaks.
Can Plastic Air Lines Be Used for Fuel? Uncovering the Potential
You may want to see also
Test Connection: Inspect the connection for leaks and ensure proper fit
When working with fuel lines, it's crucial to test the connections to ensure they are secure and leak-free. Here's a step-by-step guide to inspecting and testing the connection:
- Prepare the Tools: Before you begin, gather the necessary tools. You'll need a soapy water solution, a clean cloth, and a leak detection kit. The leak detection kit typically includes a spray bottle with a specific chemical that reacts to leaks. Additionally, have a fuel line crimping tool ready, as you may need to re-crimp the connection if it's not secure.
- Inspect the Connection: Start by visually inspecting the connection. Look for any signs of damage, corrosion, or debris around the crimped area. Ensure that the fuel line is properly aligned and that there are no kinks or twists that could cause issues. Check for any visible signs of wear and tear, especially if the connection has been previously made and re-used.
- Apply Soapy Water: Spray the soapy water solution onto the connection and the surrounding area. This step helps to identify any potential leaks. If there are any cracks or imperfections, the soap will create a visible lather, indicating a possible leak path. Make sure to cover the entire connection and the area where the fuel line joins the fitting.
- Look for Leaks: After applying the soapy water, wait for a few minutes to allow the chemical reaction to occur. Then, inspect the area carefully. If you notice any bubbles or a soapy film forming around the connection, it indicates a leak. In such cases, you may need to re-crimp the connection or tighten the fitting further.
- Ensure Proper Fit: Along with checking for leaks, it's essential to verify that the connection is properly fitted. This includes ensuring that the fuel line is securely attached to the fitting and that there is no excessive movement or play in the connection. Use your hands to gently rock the fuel line back and forth to check for any looseness. If the connection feels loose, tighten it further using the crimping tool, being careful not to overtighten.
- Final Inspection: Once you've addressed any leaks or improper fits, give the connection a final visual inspection. Ensure that all components are clean, dry, and free from any contaminants. Verify that the connection is tight and secure, with no visible signs of damage or corrosion.
Remember, proper connection testing is vital for maintaining a safe and efficient fuel system. By following these steps, you can ensure that your fuel lines are correctly installed and minimize the risk of fuel leaks or system failures.
Quick Connect Fuel Line Fitting: A Step-by-Step Guide to Disconnection
You may want to see also
Frequently asked questions
Crimping fuel lines is a crucial process in plumbing and automotive applications to ensure a secure and leak-free connection. It involves using specialized tools to create a mechanical bond between two metal tubes, allowing for a tight seal and preventing fuel leaks.
To crimp fuel lines effectively, you will need a few essential tools. These include a crimping tool or die set, which applies pressure to the fuel line to create the crimp, and a pair of pliers or a wire cutter for any initial preparation of the fuel line. Additionally, a fuel line cutter and a fuel line protector or sleeve are useful for preparing the line and providing extra protection.
Before crimping, ensure the fuel line is clean and free of any debris or contaminants. Use a fuel line cleaner or solvent to remove any old connections or residues. Cut the fuel line to the desired length, ensuring you have enough material to work with. Then, apply a small amount of fuel line adhesive or tape to the inside of the line, providing a secure base for the crimp.
There are various crimp types used for fuel lines, including the compression crimp, which is the most common. This crimp type involves deforming the fuel line to fit inside the crimping tool, creating a tight seal. Other types include the flare crimp and the union crimp, each with specific applications and requirements. It's essential to choose the correct crimp type based on the fuel line's specifications and the system's design.