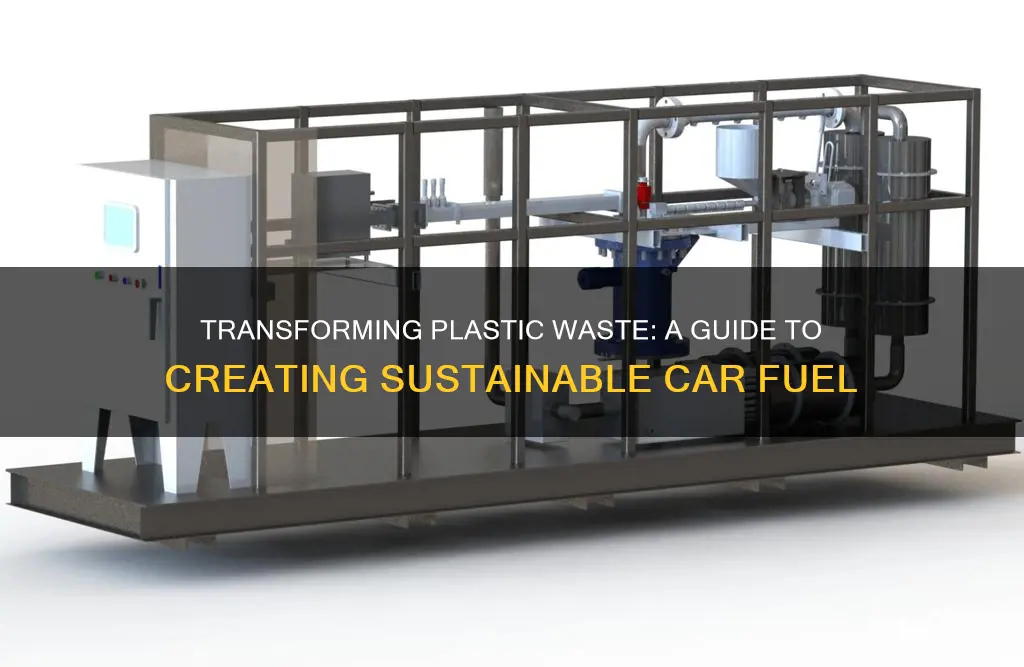
Creating car fuel from plastic is an innovative process that offers a sustainable alternative to traditional fossil fuels. This method involves breaking down plastic waste through chemical processes to produce valuable byproducts like synthetic crude oil, which can then be refined into various fuels, including gasoline, diesel, and jet fuel. The process not only helps reduce plastic waste but also provides a renewable energy source, contributing to a more environmentally friendly and sustainable future.
What You'll Learn
- Feedstock Selection: Choose suitable plastics for fuel production, considering purity and composition
- Pyrolysis Process: Heat plastic to high temperatures, breaking it down into usable fuel
- Catalysts and Additives: Enhance fuel quality and performance with specific chemicals
- Distillation Techniques: Separate fuel components through fractional distillation for optimal output
- Environmental Impact: Assess the sustainability and emissions of plastic-to-fuel conversion methods
Feedstock Selection: Choose suitable plastics for fuel production, considering purity and composition
Feedstock selection is a critical step in the process of converting plastic waste into usable car fuel. The choice of plastic feedstock directly impacts the quality and efficiency of the final fuel product. When selecting plastics for fuel production, several key factors should be considered to ensure optimal results.
Firstly, the purity of the plastic feedstock is of utmost importance. Impurities such as additives, fillers, and contaminants can negatively affect the performance and quality of the resulting fuel. It is essential to choose plastics that are free from these impurities and have a high degree of purity. High-density polyethylene (HDPE) and polypropylene (PP) are often preferred due to their relatively pure nature and low levels of additives. These plastics are commonly used in packaging and can be an excellent source of feedstock for fuel production.
The composition of the plastic is another critical aspect. Different plastics have varying molecular structures and densities, which influence the fuel's properties. For instance, plastics with a higher molecular weight and more complex structure may require specific processing techniques to break down and convert them into fuel. Polyethylene terephthalate (PET) and polystyrene (PS) are examples of plastics that might need additional treatment due to their unique compositions. PET, commonly found in beverage bottles, can be a valuable feedstock but may require advanced processes to ensure complete conversion.
Additionally, the choice of plastic feedstock should consider the availability and abundance of the material. Some plastics, like HDPE and PP, are widely used and readily available, making them more accessible for fuel production. This factor is crucial for establishing a sustainable and cost-effective process. Furthermore, the selection process should also take into account the environmental impact of the chosen plastics. Opting for plastics with a lower environmental footprint can contribute to a more sustainable and eco-friendly fuel production process.
In summary, feedstock selection for plastic-to-fuel conversion requires careful consideration of purity, composition, and availability. By choosing plastics with high purity, suitable compositions, and easy accessibility, the production of car fuel from plastic waste can be optimized. This approach ensures that the final fuel meets the required standards and contributes to a more sustainable energy solution.
Car Fans: Fuel Efficiency and Power
You may want to see also
Pyrolysis Process: Heat plastic to high temperatures, breaking it down into usable fuel
The pyrolysis process is a fascinating and efficient method to convert plastic waste into valuable car fuel. This technique involves heating plastic materials to extremely high temperatures, typically in the range of 400-700 degrees Celsius, in the absence of oxygen. By doing so, the plastic undergoes a thermal decomposition process, resulting in the production of various useful byproducts.
In this process, the plastic feedstock is fed into a pyrolysis reactor, which is a specialized vessel designed to withstand extreme temperatures. As the plastic is heated, it begins to break down into smaller fragments and eventually vaporizes. This vaporization is a critical step, as it allows for the separation of different compounds present in the plastic. The vaporized products are then cooled and condensed to separate the liquid and gaseous fractions.
The liquid fraction, often referred to as pyrolysis oil or bio-oil, is a dark, viscous liquid containing a mixture of hydrocarbons, including aromatic and aliphatic compounds. This oil can be further refined and processed to produce high-quality diesel, gasoline, or even jet fuel. The gaseous fraction, on the other hand, consists of a mixture of gases, including methane, ethylene, and other hydrocarbons. These gases can be utilized as a source of energy or further processed to create valuable chemicals.
One of the key advantages of the pyrolysis process is its ability to handle various types of plastics. Different plastics have distinct chemical compositions, and the pyrolysis process can be tailored to target specific polymers. For instance, polyethene terephthalate (PET), commonly used in beverage bottles, can be effectively converted into valuable fuel components. Additionally, the process can be optimized to minimize the production of harmful byproducts, making it an environmentally friendly alternative to traditional plastic waste management methods.
To ensure optimal results, the pyrolysis process requires precise control over temperature, pressure, and residence time within the reactor. Advanced technologies, such as computer-aided process control systems, can be employed to monitor and adjust these parameters in real-time. Furthermore, the use of catalysts can enhance the efficiency of the process by promoting specific chemical reactions and improving the yield of desired fuel components.
Neutral Gear: Fuel-Saving Myth or Reality?
You may want to see also
Catalysts and Additives: Enhance fuel quality and performance with specific chemicals
The process of converting plastic waste into a viable car fuel involves several key steps, and catalysts and additives play a crucial role in enhancing the quality and performance of the final product. One of the primary methods to achieve this is through a process known as pyrolysis, where plastic is heated in the absence of oxygen to produce a liquid fuel known as pyrolysis oil or bio-oil. This oil can then be further refined and upgraded to meet the standards of automotive fuel.
Catalysts are essential in this process as they facilitate the breakdown of plastic into smaller, more valuable molecules. One commonly used catalyst is a metal oxide, such as zinc oxide or magnesium oxide, which can be incorporated into the pyrolysis reactor. These catalysts lower the activation energy required for the decomposition process, allowing for a more efficient and rapid conversion of plastic into fuel. The choice of catalyst depends on the specific type of plastic being used and the desired properties of the final fuel.
Additives are another critical component in fuel production from plastic. These are substances added in small amounts to the fuel to improve its performance, stability, and overall quality. One important additive is a detergent, which helps in the removal of impurities and ensures the fuel's cleanliness. Detergents can be derived from various sources, including natural oils or synthetic compounds, and they play a vital role in preventing the formation of deposits in the engine, thus improving fuel efficiency and reducing emissions.
Additionally, antioxidants are often included in the fuel formulation to prevent oxidation and ensure long-term stability. Oxidation can lead to the degradation of the fuel, affecting its performance and shelf life. By adding antioxidants, such as BHT (butylated hydroxytoluene) or BHA (butylated hydroxyanisole), the fuel's resistance to oxidation is enhanced, making it more suitable for long-term storage and transportation.
Furthermore, the use of specific additives can also improve the octane rating of the fuel, which is a measure of its resistance to engine knock or pinging. Octane boosters, such as tetraethyl lead or other organic compounds, can be added to the pyrolysis oil to enhance its performance in high-performance engines. These additives work by increasing the fuel's ability to withstand higher compression ratios without causing engine knock, thus improving the overall power and efficiency of the vehicle.
Hydrogen Fuel Cell Refill: A Comprehensive Guide to Recharging Your Car
You may want to see also
Distillation Techniques: Separate fuel components through fractional distillation for optimal output
The process of converting plastic into a usable car fuel involves several intricate steps, and distillation is a critical technique employed to achieve this transformation. Fractional distillation is a methodical approach to separate the various components present in the plastic feedstock, allowing for the production of a refined fuel product. This technique is particularly useful as it enables the isolation of specific hydrocarbons, ensuring the final fuel meets the required quality standards for automotive use.
In the context of plastic-to-fuel conversion, distillation works by heating the plastic material to a specific temperature, causing it to vaporize. The vaporized compounds then undergo fractional distillation, where the different components are separated based on their boiling points. This process is carried out in a specialized apparatus, often a fractionating column, which is designed to facilitate the separation of these components. As the vapor rises, it cools and condenses, forming distinct liquid fractions at different levels of the column. Each fraction represents a different hydrocarbon chain length and molecular weight, contributing to the final fuel's composition.
The key to successful distillation is precise control over temperature and pressure. By adjusting these parameters, operators can guide the distillation process to favor the separation of specific fuel components. Longer-chain hydrocarbons, which are less volatile, tend to condense at lower temperatures, while shorter chains, being more volatile, require higher temperatures for condensation. This selective separation ensures that the final fuel product contains a balanced mix of hydrocarbons, providing the desired octane rating and combustion characteristics.
Furthermore, the efficiency of the distillation process is enhanced by the use of specialized packing materials within the fractionating column. These packings promote efficient mass transfer, allowing for better separation of the fuel components. Different packing designs, such as random or structured packings, can be employed to optimize the contact between the vapor and the condensing liquid, thereby improving the overall separation efficiency.
In summary, distillation techniques, particularly fractional distillation, play a pivotal role in the conversion of plastic to car fuel. By carefully controlling temperature, pressure, and utilizing specialized column designs, operators can effectively separate and isolate the desired fuel components. This meticulous process ensures the production of a high-quality, refined fuel that meets the performance expectations of modern vehicles.
Nitro Fuel Mystery: Solving the 16 Car Fuel Conundrum
You may want to see also
Environmental Impact: Assess the sustainability and emissions of plastic-to-fuel conversion methods
The process of converting plastic waste into usable fuel, often referred to as plastic-to-fuel or waste-to-energy conversion, has been a subject of interest for its potential to address plastic pollution and provide an alternative energy source. However, it is crucial to evaluate the environmental impact of these methods to ensure they are sustainable and do not introduce new environmental challenges.
One common method is pyrolysis, which involves heating plastic waste in the absence of oxygen to produce a liquid fuel known as pyrolysis oil or synthetic crude oil. This process can be further refined to create gasoline, diesel, or jet fuel. Pyrolysis offers several environmental benefits. Firstly, it can divert plastic waste from landfills or incineration, reducing the environmental impact of plastic disposal. By converting plastic into fuel, this method can also help decrease the demand for fossil fuels, potentially lowering greenhouse gas emissions associated with their extraction and combustion. However, the process of pyrolysis itself can release volatile organic compounds (VOCs) and other pollutants, which, if not properly controlled, can contribute to air pollution and smog formation. Advanced pyrolysis technologies, such as those using catalytic cracking, can help mitigate these emissions.
Another approach is gasification, where plastic waste is heated with limited oxygen to produce a synthesis gas (syngas) that primarily consists of carbon monoxide and hydrogen. This syngas can be further processed to generate electricity, heat, or transportation fuels. Gasification offers the advantage of producing a cleaner-burning fuel compared to conventional petroleum-based fuels. The process can also capture carbon dioxide (CO2) for potential reuse or storage, which is a significant environmental benefit. However, the energy input required for gasification can be substantial, and the overall efficiency of the process needs careful consideration to ensure it remains environmentally advantageous.
The sustainability of plastic-to-fuel conversion also depends on the feedstock and the overall waste management system. Using mixed plastic waste streams can be challenging due to the variability in composition and potential contamination. Sorted and cleaned plastic waste, preferably from single-material sources, is ideal for maximizing the efficiency and environmental benefits of the conversion process. Additionally, the infrastructure for collecting, sorting, and transporting plastic waste plays a critical role in the sustainability of these methods.
In summary, while plastic-to-fuel conversion methods offer a potential solution to plastic waste management and provide an alternative energy source, they must be carefully evaluated for their environmental impact. Pyrolysis and gasification techniques each have their advantages and challenges, and the overall sustainability depends on various factors, including feedstock quality, waste management practices, and process efficiency. To ensure a positive environmental impact, these methods should be implemented as part of a comprehensive strategy that includes waste reduction, recycling, and the development of a circular economy for plastics.
Solar Energy Cars: The Fossil Fuel-Free Future
You may want to see also
Frequently asked questions
The process typically involves a method called pyrolysis, where plastic waste is heated in the absence of oxygen to produce a liquid fuel known as pyrolysis oil or synthetic crude oil. This oil can then be refined further to create various fuel products.
Not all plastics are suitable for this process. Typically, only certain types of plastic, such as polyolefins (including polyethylene and polypropylene) and polystyrene, are used due to their chemical properties and ease of processing. Other plastics like PET (polyethylene terephthalate) may require additional steps for effective conversion.
The fuel produced from plastic can be a drop-in replacement for gasoline, meaning it can be used in standard internal combustion engines without modifications. It has a similar energy content to gasoline, but its composition and properties might vary slightly, and further research is ongoing to ensure optimal performance and minimize any potential environmental impact.
This process offers several potential advantages. Firstly, it provides a way to recycle and utilize plastic waste, reducing the amount of plastic ending up in landfills or the environment. Secondly, it can help decrease our reliance on fossil fuels and contribute to a more sustainable energy system. However, it is essential to ensure that the entire process, from waste collection to fuel production, is implemented with proper environmental regulations and practices.
One of the primary challenges is the availability and collection of suitable plastic waste. The process requires a consistent supply of high-quality feedstock, which can be difficult to source and transport. Additionally, the energy-intensive nature of pyrolysis and the need for specialized equipment pose technical and economic challenges. Further research and development are necessary to optimize the process, reduce costs, and make it more accessible for widespread adoption.