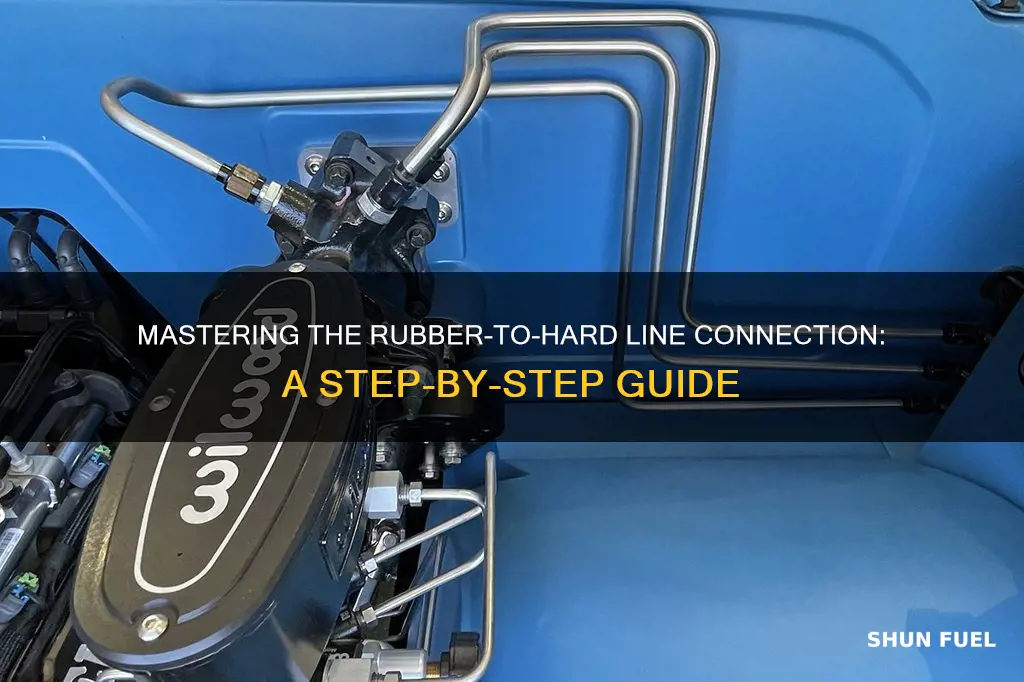
Connecting a rubber fuel line to a hard line is a common task in automotive maintenance, and it requires careful attention to ensure a secure and leak-free connection. This process involves preparing the ends of both lines, using the appropriate tools and techniques to join them, and ensuring that the connection is tight and sealed properly. By following a step-by-step guide, you can ensure a reliable fuel supply system, which is crucial for the safe and efficient operation of your vehicle.
Characteristics | Values |
---|---|
Connection Type | Clamps or Fittings |
Material | Rubber (for fuel line), Hard Plastic or Metal (for hard line) |
Size Compatibility | Ensure the fuel line and hard line sizes match or use adapters |
Flexibility | Rubber fuel lines offer more flexibility, while hard lines are rigid |
Durability | Hard lines are more durable and less prone to damage from fuel leaks |
Installation | Clean and prepare both lines, align the ends, and secure with clamps or fittings |
Leak Prevention | Tighten connections securely to prevent fuel leaks |
Temperature Resistance | Choose materials that can withstand fuel temperature ranges |
Vibration Resistance | Hard lines are generally more vibration-resistant |
Cost | Rubber lines are often cheaper, while hard lines may require additional fittings |
What You'll Learn
- Preparation: Ensure both lines are clean, dry, and free of debris
- Fitting Selection: Choose the right size and type of fitting for a secure connection
- Clamping: Tighten clamps firmly, but avoid over-tightening to prevent damage
- Bending: Route the rubber line to avoid sharp bends, which can cause leaks
- Testing: Use a pressure test to verify the connection's integrity before use
Preparation: Ensure both lines are clean, dry, and free of debris
When preparing to connect a rubber fuel line to a hard line, it is crucial to ensure that both lines are in optimal condition to facilitate a secure and leak-free connection. The first step in this process is to thoroughly clean both lines. Over time, fuel lines can accumulate dirt, grime, and other contaminants, which can compromise the integrity of the connection. Use a mild detergent or a specialized fuel line cleaner to remove any built-up debris. Apply the cleaner generously to the interior surfaces of both lines, ensuring that you cover the entire length. Allow the cleaner to work for a few minutes to loosen and dissolve any stubborn deposits.
After cleaning, it is essential to dry the lines completely. Moisture can cause the rubber to become brittle and prone to cracking, leading to potential leaks. Use a clean cloth or a soft brush to wipe down the lines, removing any remaining cleaner and excess moisture. Pay close attention to the joints and connections, as these areas are more susceptible to moisture absorption. Ensure that the lines are completely dry before proceeding to the next step.
In addition to cleaning and drying, it is important to inspect the lines for any signs of damage or wear. Look for cracks, tears, or any other visible defects in the rubber fuel line. Similarly, check the hard line for any bends, kinks, or signs of corrosion. If any damage is found, it is best to replace the affected line to ensure a proper connection. This step is crucial to prevent potential fuel leaks and maintain the safety of your vehicle.
Once both lines are clean, dry, and free of any visible defects, you can proceed with the connection process. Ensure that the lines are aligned properly, with the ends positioned correctly for a seamless join. This preparation step is vital as it sets the foundation for a successful and long-lasting connection between the rubber and hard fuel lines. By taking the time to thoroughly clean and inspect the lines, you are minimizing the risk of issues that may arise during the connection process.
Fuel Line Tubing: Top Sources for Your Car's Needs
You may want to see also
Fitting Selection: Choose the right size and type of fitting for a secure connection
When connecting a rubber fuel line to a hard line, selecting the appropriate fitting is crucial for a secure and reliable connection. The right fitting ensures that the fuel line remains intact, prevents leaks, and maintains the structural integrity of the fuel system. Here's a detailed guide on how to choose the right fitting for this task:
Understanding the Fitting Options:
There are various types of fittings available for joining rubber and hard lines, each with its own advantages and use cases. Common options include compression fittings, quick-connect fittings, and clamp-style fittings. Compression fittings use a ferrule that compresses around the pipe, creating a tight seal. Quick-connect fittings offer a convenient snap-on design, ideal for temporary connections. Clamp-style fittings secure the line with a screw-on clamp, providing a strong hold. Understanding these options is the first step in making an informed choice.
Size Matters:
The size of the fitting should match the diameter of your fuel lines. Measure the inside diameter of both the rubber and hard lines to ensure a proper fit. Fittings that are too small may restrict fuel flow, while oversized fittings can lead to unnecessary bulk and potential leaks. It's essential to get the size right to maintain optimal performance and safety.
Material Compatibility:
Consider the materials of both the fuel line and the hard line. Ensure that the chosen fitting is compatible with these materials to avoid degradation or damage. For example, if your fuel line is made of rubber, select a fitting designed for rubber-to-metal connections. Material compatibility ensures the longevity of the connection.
Application and Environment:
The type of fitting you choose should align with the specific application and environmental conditions. If the connection is for a high-pressure system or requires frequent disconnections, quick-connect fittings might be preferable. In contrast, for permanent installations, compression fittings could provide a more secure hold. Consider factors like temperature, vibration, and the overall design of the fuel system to make the best selection.
Quality and Reliability:
Invest in high-quality fittings from reputable manufacturers. Well-made fittings will provide a secure seal and withstand the demands of the fuel system. Check for any signs of damage or wear, especially if reusing fittings. Ensuring the quality of the fittings is essential for the overall safety and performance of the fuel line connection.
By carefully considering the size, material compatibility, application, and quality of the fittings, you can ensure a secure and reliable connection between the rubber fuel line and the hard line, contributing to the efficient and safe operation of your vehicle's fuel system.
Unleash Power: Turbocharged Secrets for Car Performance Without Fuel Return Line
You may want to see also
Clamping: Tighten clamps firmly, but avoid over-tightening to prevent damage
When connecting a rubber fuel line to a hard line, proper clamping is essential to ensure a secure and leak-free connection. The process involves using specialized clamps designed to fit the specific dimensions of both the rubber and hard lines. These clamps are typically made of durable materials like metal or reinforced plastic to withstand the pressure and movement that can occur during operation.
To begin, locate the clamp and position it over the end of the hard line. Ensure that the clamp is aligned correctly, with the opening facing towards the rubber fuel line. Slide the clamp onto the hard line, allowing it to grip the surface. This initial step is crucial to create a foundation for the secure connection.
Next, carefully feed the rubber fuel line through the clamp's opening. You may need to adjust the clamp's position slightly to accommodate the fuel line's diameter. Once the fuel line is positioned, firmly tighten the clamp by hand. This initial tightening ensures that the clamp is in place and ready for further adjustments.
The key to successful clamping is finding the right balance between tightness and damage prevention. Over-tightening can lead to the clamp crushing the fuel line or causing damage to the hard line. It is important to tighten the clamp firmly, but with controlled force. Use your fingers or a tool to apply pressure, ensuring that the clamp is snug against both the fuel line and the hard line.
After tightening the clamp, inspect it to ensure it is secure. The clamp should be tight enough to prevent any movement or leakage but not so tight that it causes damage. If you notice any gaps or the clamp feels loose, further tightening is required. However, if the clamp is too tight, you may need to carefully adjust it by loosening the screws or releasing the clamp's grip on the lines. This step requires patience and a gentle touch to avoid causing any harm to the fuel lines.
94 Plymouth Voyager Fuel Line Removal: A Step-by-Step Guide
You may want to see also
Bending: Route the rubber line to avoid sharp bends, which can cause leaks
When connecting a rubber fuel line to a hard line, proper bending techniques are crucial to ensure a secure and leak-free installation. The primary goal is to avoid sharp bends, as these can compromise the integrity of the rubber material and lead to potential fuel leaks. Here's a detailed guide on how to achieve this:
Start by visualizing the path you want the rubber line to take. Plan the route carefully, ensuring it is as straight as possible. Sharp bends can create stress points on the rubber, making it more susceptible to damage. Aim for a smooth, gradual curve, especially when transitioning from the rubber line to the hard line. This gradual curve will help distribute the force evenly and reduce the risk of cracks or tears.
As you begin bending the rubber line, use your hands or a soft tool to apply gentle pressure. Avoid forcing the bend, as this can cause the rubber to stretch or distort. Instead, work with the material, allowing it to conform to the desired shape. Take your time and make small adjustments until you achieve the required angle and curvature. Remember, the goal is to create a smooth, continuous bend without any sharp kinks.
When routing the line, consider the natural flexibility of the rubber. Allow it to move and adjust as needed. If you encounter resistance or need to make a turn, do so gradually and with control. Avoid sudden movements that might cause the rubber to twist or crimp. By working with the material's flexibility, you can ensure a more secure connection without causing unnecessary stress on the rubber.
Additionally, pay attention to the connection point between the rubber and hard lines. Here, a slight bend in the hard line can help guide the rubber line into place. Ensure that the bend in the hard line is gentle and not sharp, as this could damage the rubber. By carefully bending and positioning the lines, you create a seamless transition, reducing the chances of leaks or fuel spillage.
In summary, when connecting rubber fuel lines to hard lines, focus on creating smooth, gradual bends. Avoid sharp turns that can compromise the rubber's integrity. Take your time, work with the material's flexibility, and plan the route to ensure a secure and leak-free installation. Following these steps will help you achieve a professional-grade connection.
Flare Stainless Steel Fuel Lines: A Comprehensive Guide
You may want to see also
Testing: Use a pressure test to verify the connection's integrity before use
When connecting a rubber fuel line to a hard line, it is crucial to ensure the integrity of the connection to prevent any potential leaks or failures. One effective method to verify the strength and reliability of the connection is by conducting a pressure test. This test involves applying pressure to the joined section of the fuel lines to check for any signs of leakage or damage.
Here's a step-by-step guide on how to perform this pressure test:
- Preparation: Gather the necessary tools and materials, including the fuel lines, a pressure gauge, a source of compressed air or water, and a clean workspace. Ensure that the fuel lines are properly cleaned and free from any debris or contaminants that could interfere with the test.
- Connection Setup: Securely attach the rubber fuel line to the hard line using the appropriate fittings and clamps. Make sure the connection is tight and secure, as any looseness could affect the test results. Consider using a torque wrench to ensure the fittings are tightened to the recommended specifications.
- Pressure Application: Connect the pressure gauge to the fuel line connection. Gradually increase the pressure in the system using compressed air or water until it reaches a predetermined level, typically a few pounds above the system's operating pressure. This pressure should be maintained for a specified duration, usually a few minutes.
- Inspection: During and after the pressure application, closely observe the connection for any signs of leakage. Check for any visible wet spots or drips around the fittings. Additionally, listen for any hissing sounds, which could indicate a leak. If any issues are detected, immediately release the pressure and inspect the connection further.
- Documentation: Record the pressure used, the duration of the test, and any observations made during the inspection. This documentation will be valuable for future reference and can help identify potential issues with the connection.
By following these steps and conducting a thorough pressure test, you can ensure that the connection between the rubber fuel line and the hard line is secure and leak-free. This practice is essential in maintaining the safety and efficiency of fuel systems, especially in applications where fuel lines are exposed to varying temperatures and pressures. Regular testing and maintenance will contribute to the overall reliability of the fuel system.
Small Engine Fuel Line: Top Stores and Online Sources
You may want to see also
Frequently asked questions
Connecting a rubber fuel line to a hard line is often done to ensure a secure and leak-free fuel transfer between two different types of fuel lines. Rubber lines are flexible and commonly used for their ability to absorb vibrations, while hard lines are stiffer and provide a more rigid connection. This connection is crucial in fuel systems to maintain the integrity of the fuel supply and prevent any potential leaks.
Before connecting, ensure both lines are clean and free of any debris or contaminants. Use a fuel line cleaner or a mild solvent to remove any old fuel or residue. Inspect the lines for any damage or cracks, especially at the connection points. If any issues are found, replace the affected sections before making the connection.
You will typically need a fuel line coupling or fitting that is compatible with both the rubber and hard lines. This coupling should have male threads on one end for the hard line and a female section for the rubber line. Additionally, you might require a fuel line clamp or ferrule to secure the connection. Have these tools ready before starting the process.
It's important to use the correct type of coupling for the specific fuel lines you are working with. Different materials and diameters may require specialized couplings. Always check the specifications of your fuel lines and choose a coupling that is designed to fit both types. Using the wrong coupling can lead to leaks or damage to the lines.
Yes, when connecting the rubber fuel line to the hard line, apply firm and even pressure when tightening the coupling. Use the fuel line clamp or ferrule to secure the connection, ensuring it is tight enough to prevent any movement but not so tight that it causes damage to the lines. Test the connection by applying slight pressure and checking for any leaks.