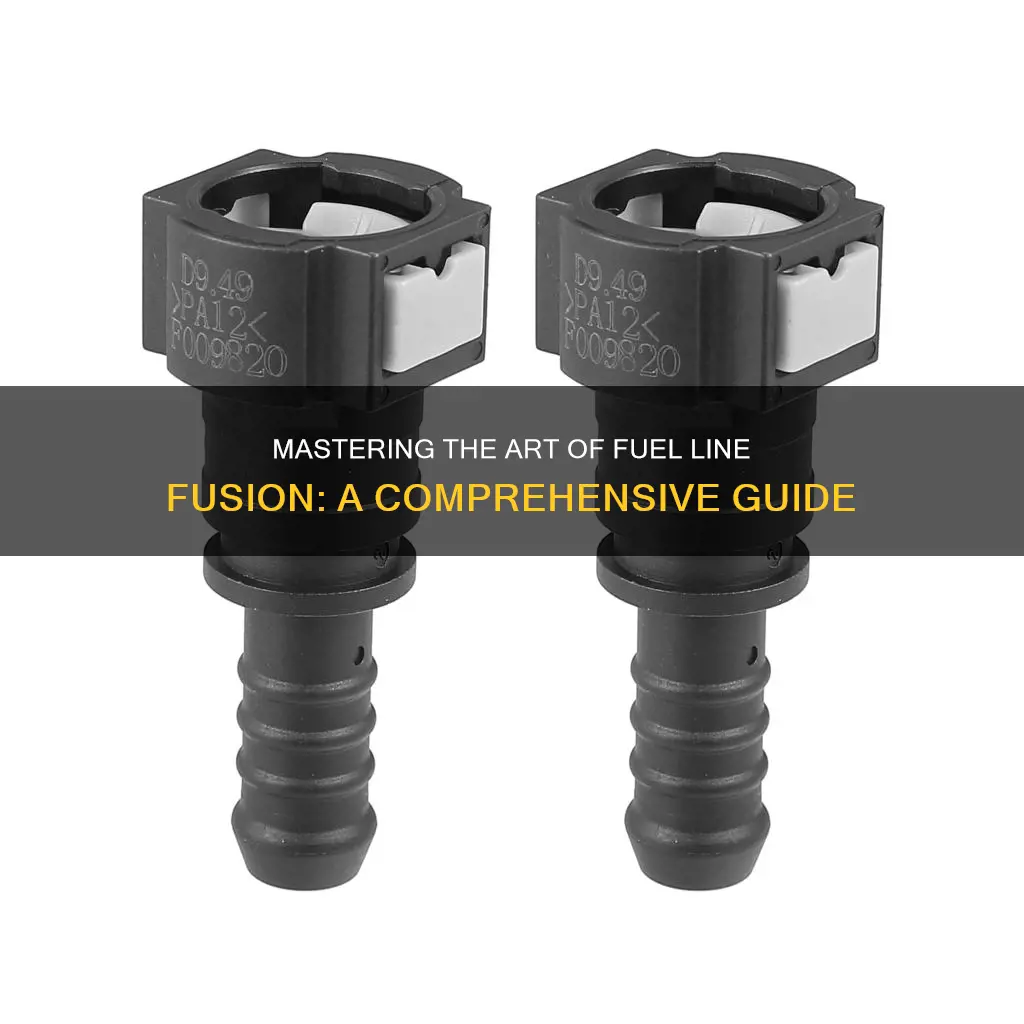
Connecting two fuel lines is a crucial step in any vehicle's maintenance or repair process, ensuring the efficient and safe transfer of fuel from the tank to the engine. This process requires careful attention to detail and adherence to specific steps to avoid potential hazards. By following a structured approach, you can ensure a secure and reliable connection, minimizing the risk of fuel leaks and optimizing engine performance. This guide will provide a comprehensive overview of the steps involved, offering a clear and concise method to achieve a successful fuel line connection.
What You'll Learn
- Preparation: Ensure both lines are clean, straight, and free of debris
- Clamps: Use the right type of fuel line clamp for a secure fit
- Alignment: Align the lines properly to avoid kinks and blockages
- Fittings: Connect using fuel line fittings for a leak-free seal
- Testing: Verify the connection by checking for leaks and proper flow
Preparation: Ensure both lines are clean, straight, and free of debris
Before attempting to connect two fuel lines, it is crucial to ensure that both lines are in optimal condition. Start by thoroughly cleaning each fuel line to remove any dirt, debris, or contaminants that may be present. This step is essential to prevent any blockages or contamination issues in the future. Use a suitable cleaning agent or solvent recommended for fuel lines, and ensure you follow the manufacturer's instructions. Rinse the lines thoroughly to eliminate any residue and allow them to dry completely.
Next, inspect the fuel lines for any signs of damage, such as cracks, leaks, or kinks. Straighten any bent lines carefully to avoid putting unnecessary pressure on the material. Ensure that both lines are of the correct size and compatible with the fuel system you are working on. Misaligned or incompatible lines can lead to improper fuel flow and potential safety hazards.
Pay close attention to the condition of the fuel line connectors as well. Clean and inspect the connectors to ensure they are free from corrosion or damage. If any connectors are worn out or damaged, replace them with new ones to guarantee a secure and reliable connection.
Additionally, check the fuel lines for any existing connections or fittings. Ensure that these are tight and secure, as loose connections can lead to fuel leaks and potential safety risks. Use the appropriate tools to tighten the fittings, following the manufacturer's guidelines for torque specifications.
By taking the time to thoroughly prepare and clean the fuel lines, you can ensure a proper connection and maintain the overall health of your fuel system. This preparation step is often overlooked but is vital to the success and safety of the fuel line connection process.
Optimizing Fuel Flow: Choosing the Right Fuel Line for Your Gas Stove
You may want to see also
Clamps: Use the right type of fuel line clamp for a secure fit
When connecting two fuel lines, ensuring a secure and leak-free fit is crucial to prevent any potential hazards. One of the key components to achieving this is using the appropriate type of fuel line clamp. Clamps play a vital role in holding the fuel lines in place and maintaining a tight seal, so it's essential to choose the right one for the job.
The first step is to identify the type of fuel line clamp that suits your specific application. There are various types available, including steel, stainless steel, and aluminum clamps, each with its own advantages. For instance, steel clamps offer excellent strength and durability, making them ideal for high-pressure applications. Stainless steel clamps, on the other hand, provide superior corrosion resistance, which is beneficial in environments with harsh conditions. Aluminum clamps are lightweight and offer good heat resistance, making them suitable for certain automotive applications.
When selecting a clamp, consider the diameter of the fuel lines and the material they are made of. Different clamps are designed to fit specific sizes and types of fuel lines. For example, a 1/4-inch fuel line clamp will not work for a 3/8-inch line. Additionally, ensure that the clamp material is compatible with the fuel line material to avoid any potential chemical reactions or degradation over time.
Proper installation is critical to the clamp's effectiveness. Start by cleaning the fuel lines and the clamp's surfaces to ensure a clean and secure connection. Apply a thin layer of thread lock or pipe compound to the threads of the fuel line fittings to prevent leaks. Then, insert the fuel lines into the clamp, ensuring they are aligned correctly. Tighten the clamp securely using a wrench, being careful not to overtighten, as this can damage the fuel lines. A good rule of thumb is to apply firm pressure, but stop when you feel resistance, indicating a secure fit.
Regular inspection and maintenance of the fuel line clamps are essential. Over time, clamps can loosen due to vibration and movement, so it's important to check them periodically. Look for any signs of damage, corrosion, or wear, and replace the clamps if necessary. This simple maintenance practice will help ensure the long-term reliability and safety of your fuel system.
Road King Fuel Line Removal: A Step-by-Step Guide
You may want to see also
Alignment: Align the lines properly to avoid kinks and blockages
When connecting two fuel lines, proper alignment is crucial to ensure a secure and efficient connection. Here's a detailed guide on how to achieve this:
- Preparation: Before you begin, ensure you have the necessary tools and materials, including the two fuel lines, connectors, and any required tools for tightening. Clean the ends of the fuel lines to remove any dirt or debris that might interfere with the connection.
- Visual Inspection: Carefully examine the ends of the fuel lines. Look for any bends, kinks, or damage that could affect the alignment. Ensure that the lines are straight and free from any obstructions. Proper alignment ensures that the fuel flows smoothly without any restrictions.
- Alignment Technique: To align the fuel lines, you can use a few methods. One approach is to hold the lines by their middle sections and gently pull them to create a straight line. Avoid pulling too hard, as this might cause damage. Alternatively, you can use a straight edge or a ruler to guide the lines into a straight position. The goal is to ensure that the lines are parallel and aligned with each other.
- Connecting the Lines: Once aligned, carefully connect the fuel lines using the appropriate connectors. Ensure that the connectors are the right size and type for the fuel lines. Tighten the connectors securely, but be careful not to overtighten, as this can damage the lines. Check for any leaks around the connection points.
- Final Check: After connecting the lines, inspect the entire setup. Look for any signs of kinks or misalignment. Ensure that the fuel lines are secure and that there are no obstructions that could cause blockages. Proper alignment at this stage is essential to prevent any issues with fuel flow and potential engine problems.
Remember, taking the time to align the fuel lines correctly will contribute to a reliable and safe fuel system in your vehicle. Always follow manufacturer guidelines for specific instructions related to your vehicle's fuel lines.
Mastering the Art of Removing Dormant Fuel Line Connectors: A Comprehensive Guide
You may want to see also
Fittings: Connect using fuel line fittings for a leak-free seal
When connecting two fuel lines, using the right fittings is crucial to ensure a secure and leak-free seal. Here's a step-by-step guide on how to achieve this:
Step 1: Prepare the Fittings and Lines
Start by cleaning the ends of both fuel lines. Remove any dirt, debris, or old fuel residue using a cloth or a fuel line cleaner. Ensure the surfaces are dry before proceeding. Measure and cut the fuel lines to the desired length, allowing for a slight overlap when connecting.
Step 2: Choose the Appropriate Fitting
Select the fitting that best suits your fuel line connection. Common types include compression fittings, quick-connect fittings, and clamp-style fittings. Compression fittings are widely used and provide a tight seal by compressing the fuel line around the fitting. Quick-connect fittings offer convenience but may not be as secure as compression types. Clamp-style fittings use a clamp to secure the connection.
Step 3: Assemble the Fitting
Follow the manufacturer's instructions for the chosen fitting. Typically, you'll insert the fuel line into the fitting, ensuring it's centered. For compression fittings, you'll need to screw the fitting onto the line, tightening it securely but avoiding over-tightening to prevent damage. Quick-connect fittings usually involve pushing the line into the fitting and securing it with a clip or nut. Clamp-style fittings require you to position the line and then tighten the clamp.
Step 4: Ensure a Tight Connection
Double-check the connection to ensure it is tight and secure. Apply firm pressure to the fitting and feel for any play or movement. If using a compression fitting, check that the fuel line is compressed evenly and that there are no gaps. For quick-connect or clamp-style fittings, ensure the line is firmly held in place.
Step 5: Test for Leaks
After assembly, it's essential to test the connection for any leaks. Turn on the fuel supply and observe for any signs of fuel escaping around the fitting. You can also use a soapy water solution to apply around the connection and look for bubbles, indicating a potential leak. If any leaks are detected, tighten the fitting or re-assemble the connection as needed.
By following these steps and using the appropriate fittings, you can create a reliable and leak-free connection between two fuel lines, ensuring optimal performance and safety in your vehicle's fuel system.
Chevy Silverado Fuel Line: 2008 Model Size Guide
You may want to see also
Testing: Verify the connection by checking for leaks and proper flow
When connecting two fuel lines, it is crucial to ensure that the process is done correctly and safely. After completing the physical connection, the next step is to thoroughly test the assembly to confirm its integrity and functionality. This testing phase involves a series of checks to verify that the fuel lines are properly connected and free from any leaks, ensuring that the fuel system operates efficiently without any potential hazards.
The first step in testing is to inspect the connections for any visible signs of damage or contamination. Look for any bends, kinks, or cracks in the fuel lines, as these could compromise the system's integrity. Additionally, check for any signs of corrosion or debris around the fittings and ensure that all components are clean and free from contaminants. This initial inspection provides a baseline for further testing and helps identify any potential issues early on.
To check for leaks, start by applying a small amount of fuel or a suitable leak detection fluid to the connections. Carefully observe the areas around the fittings and joints for any signs of fuel escaping. Leaks can occur at the connection points, where the fuel lines meet, or along the length of the lines. If a leak is detected, it is essential to identify the source immediately. This may require further investigation, such as removing the connections and inspecting the lines for damage or using specialized tools to pinpoint the leak.
Proper flow testing is another critical aspect of the verification process. It ensures that the fuel is being delivered efficiently to the engine. Start the engine and monitor its performance while fueling. Check for any unusual noises, vibrations, or changes in engine behavior. A properly connected fuel system should allow the engine to run smoothly and consistently. If the engine stumbles, misfires, or exhibits erratic behavior, it may indicate a problem with the fuel flow, requiring further investigation into the connections and lines.
In addition to visual inspections and engine performance checks, consider using pressure testing equipment to measure the fuel pressure at different points in the system. This can help identify any restrictions or blockages in the lines that might affect flow. By combining these testing methods, you can ensure that the fuel lines are securely connected, leak-free, and capable of delivering fuel efficiently to the engine, minimizing the risk of fuel-related issues and ensuring optimal engine performance.
Mercury Outboard Fuel Line Motor Fitting: A Step-by-Step Guide
You may want to see also
Frequently asked questions
To ensure a tight and leak-free connection, you should use a fuel line coupling or a quick-connect fitting. Start by cleaning the ends of the fuel lines and ensuring they are free of any debris. Then, align the lines and insert the coupling or fitting over both ends, tightening it securely with a wrench. Make sure the connection is tight but not overtightened to avoid damage.
While it is possible to connect fuel lines by hand, using the right tools can make the process easier and more reliable. You will need a fuel line coupling or fitting, a wrench or socket for tightening, and possibly a fuel line cleaner to ensure a good seal. With the appropriate tools, you can achieve a secure connection without excessive force, reducing the risk of damage to the lines.
If the fuel lines have different diameters, you might need to use adapters or reducers to ensure a proper connection. These adapters are available in various sizes and can be slipped over the larger line and then connected to the smaller line using a coupling or fitting. It's important to choose adapters that match the fuel line material to ensure compatibility and a secure seal.
Absolutely, safety is crucial when working with fuel lines. Always wear protective gear, such as gloves and safety goggles, to avoid skin contact and potential splashes. Ensure you are in a well-ventilated area, and if possible, work outdoors to minimize the risk of fuel inhalation. Additionally, double-check all connections and ensure they are tight to prevent fuel leaks, which can be dangerous and cause fires.