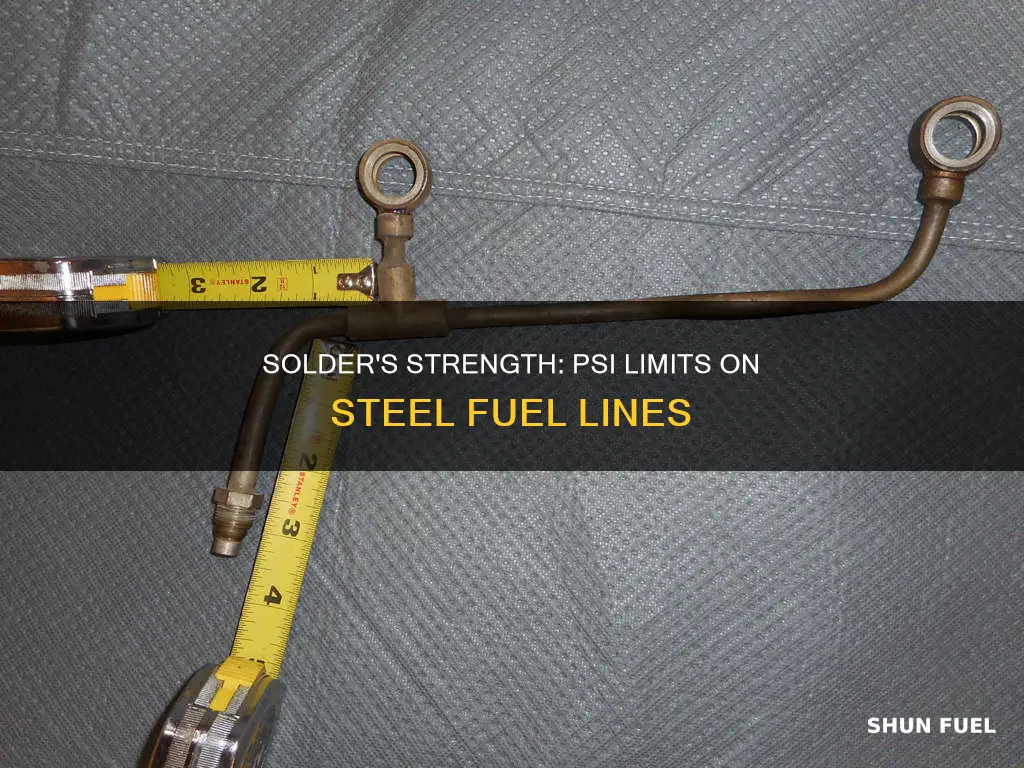
When it comes to steel fuel lines, understanding the pressure capacity, or psi, that solder can withstand is crucial for ensuring the integrity and safety of the fuel system. Solder, a material commonly used to join fuel lines, must be able to handle the pressure exerted by the fuel to prevent leaks and potential hazards. This paragraph aims to explore the psi limits of solder on steel fuel lines, providing insights into the factors that influence its performance and the importance of adhering to recommended specifications.
What You'll Learn
- Fuel Line Material: Steel fuel lines can withstand higher psi compared to other materials
- Solder Application: Proper soldering technique ensures a strong bond, allowing for higher psi
- Line Thickness: Thicker fuel lines can handle more psi without compromising integrity
- Temperature Limits: Extreme temperatures can affect psi capacity; soldering should be done within safe limits
- Pressure Testing: Rigorous testing is essential to ensure soldered joints can handle expected psi levels
Fuel Line Material: Steel fuel lines can withstand higher psi compared to other materials
When it comes to fuel lines, the choice of material is crucial for ensuring the safety and efficiency of your vehicle's fuel system. Among the various options available, steel fuel lines stand out for their exceptional ability to withstand high-pressure environments. This is particularly important in applications where fuel lines are exposed to varying psi (pounds per square inch) levels, which can be significantly higher than those encountered in other automotive systems.
The strength of steel lies in its robust composition, making it an ideal candidate for fuel lines that require durability and reliability. Unlike some other materials, steel can handle the intense pressure that fuel systems often experience, especially during acceleration or when the engine is under load. This is a critical factor to consider, as fuel lines must be able to transmit fuel efficiently while maintaining structural integrity under these demanding conditions.
In terms of psi capacity, steel fuel lines can typically handle much higher pressures compared to alternatives like rubber or plastic. While rubber and plastic fuel lines are commonly used and offer good flexibility, they may not be suitable for high-pressure applications. Steel, on the other hand, provides a robust solution, ensuring that the fuel lines remain intact and functional even when subjected to increased psi. This is especially relevant in high-performance vehicles or those with modified engines, where psi levels can be significantly elevated.
The use of steel fuel lines is particularly advantageous in racing or modified vehicles, where engine power and performance are maximized. In these scenarios, the psi levels can be much higher, and steel lines provide the necessary reinforcement to handle such conditions without compromising the overall system's integrity. Additionally, steel's durability ensures a longer lifespan for the fuel lines, reducing the need for frequent replacements and potential maintenance issues.
In summary, when considering fuel line material, steel emerges as the superior choice for applications requiring high psi tolerance. Its inherent strength and ability to withstand intense pressure make it an excellent option for vehicles with demanding fuel systems. By selecting steel fuel lines, you can ensure a reliable and efficient fuel supply, even in the most challenging automotive environments.
Understanding Dirt Bike Fuel Lines: Metric or Not?
You may want to see also
Solder Application: Proper soldering technique ensures a strong bond, allowing for higher psi
When it comes to soldering steel fuel lines, understanding the proper application of solder is crucial to ensure a secure and reliable connection. The process involves more than just melting the solder and allowing it to cool; it requires a specific technique to create a strong bond that can withstand high-pressure environments.
The key to achieving a robust soldered joint is to use the right type of solder and flux. Solder for steel fuel lines is typically a lead-based alloy, which provides excellent wetting and bonding properties. It is essential to choose a solder with the appropriate melting point, ensuring it can melt at a temperature that is not too high or too low for the steel's base metal. A common practice is to use a solder with a melting point around 350-400°F (177-204°C), which is suitable for most steel fuel lines.
Flux is another critical component of the soldering process. It is applied to the steel surface to remove oxides and provide a clean, corrosion-free area for the solder to bond. A good flux should be compatible with the solder and steel, ensuring a strong and durable joint. It is recommended to use a rosin-based flux, which is widely used in plumbing and automotive applications. This type of flux is non-corrosive and leaves a protective layer on the joint, promoting a strong bond.
The soldering technique itself is just as important as the materials used. It involves a series of steps to ensure a proper connection. First, the steel surfaces to be joined should be cleaned and prepared, removing any dirt, grease, or old solder. Then, a small amount of flux is applied to the steel, ensuring complete coverage. Next, the solder is carefully added to the fluxed area, allowing it to melt and flow, forming a bead. The solder should be applied in a controlled manner, ensuring it is not too thick or too thin, as this can affect the joint's strength.
As the solder melts, it should create a smooth, continuous bead that fills the gap between the steel surfaces. This bead must be free of any air bubbles, which can weaken the joint. The temperature of the soldering iron should be adjusted to ensure the solder melts at the correct rate, allowing for precise control during the application. Once the solder is melted, it is essential to hold the iron still for a few seconds to ensure the solder remains in place, forming a strong bond.
By following these proper soldering techniques, you can create a joint that can withstand the high-pressure requirements of a steel fuel line. The result is a secure connection that provides peace of mind, knowing that your fuel system is reliable and safe. Remember, the key to success in soldering is attention to detail and the use of the right materials and techniques.
Choosing the Right Fuel Line for Your Lawn Mower: A Guide
You may want to see also
Line Thickness: Thicker fuel lines can handle more psi without compromising integrity
When it comes to fuel lines, the thickness of the line is a critical factor in determining its ability to withstand pressure. Thicker fuel lines are designed to handle higher psi (pounds per square inch) without compromising their structural integrity. This is especially important in high-performance vehicles or those with modified engines, where increased psi is often required to meet the demands of enhanced power output.
The relationship between line thickness and psi capacity is directly proportional. As the thickness of the fuel line increases, its ability to withstand higher pressure also increases. This is because thicker walls provide more material to distribute the force exerted by the psi, reducing the risk of damage or failure. For instance, a 3/8-inch fuel line can typically handle more psi compared to a 1/4-inch line, assuming all other factors, such as material quality, are equal.
In the context of soldering, it is essential to consider the joint's strength and reliability. When soldering steel fuel lines, the joint must be able to withstand the psi it will encounter during operation. Thicker lines offer more surface area for the solder to bond, increasing the joint's strength. This is particularly crucial in high-pressure applications, where a weak joint could lead to leaks or even catastrophic failure.
Engineers and mechanics often recommend using thicker fuel lines to ensure optimal performance and safety. For example, a 3/8-inch fuel line might be preferred over a 1/4-inch line in high-performance applications, even though the latter could technically handle the psi. This is because thicker lines provide a safety margin, reducing the chances of damage or failure over time.
In summary, when considering the psi capacity of soldered steel fuel lines, line thickness plays a pivotal role. Thicker fuel lines offer improved psi handling without sacrificing integrity, making them a preferred choice for high-performance vehicles and modified engines. Understanding this relationship is essential for anyone working with fuel systems, ensuring optimal performance and safety.
Mastering the Art of Fuel Line Removal: A Step-by-Step Guide
You may want to see also
Temperature Limits: Extreme temperatures can affect psi capacity; soldering should be done within safe limits
Extreme temperatures can significantly impact the psi capacity of a solder joint on a steel fuel line. When soldering, it is crucial to understand and adhere to the safe temperature limits to ensure the integrity and reliability of the connection. High temperatures can cause the solder to melt and lose its structural integrity, leading to potential leaks or failure. Conversely, low temperatures can make the solder brittle and less pliable, hindering its ability to form a strong bond.
The ideal temperature range for soldering steel fuel lines is typically between 300°F and 400°F (149°C and 204°C). At these temperatures, the solder and the steel base material can form a strong, durable joint. However, it is essential to exercise caution and avoid exceeding these limits.
During the soldering process, it is recommended to use a controlled heat source, such as a soldering gun or a heat gun, to maintain a consistent temperature. Applying excessive heat can quickly raise the temperature beyond the safe range, causing the solder to become weak and susceptible to cracking. Similarly, using a lower temperature might not provide enough heat to melt the solder, resulting in an inadequate bond.
To ensure the best results, it is advised to preheat the steel fuel line and the solder joint before applying the heat source. This step helps to bring the temperature within the safe range and ensures that the solder melts evenly and forms a strong connection. Additionally, allowing the joint to cool gradually after soldering is essential to prevent any sudden temperature changes that could affect the psi capacity.
In summary, when working with steel fuel lines and soldering, it is critical to respect the temperature limits to maintain the psi capacity and overall performance of the joint. By understanding and adhering to these safe limits, technicians can ensure a reliable and long-lasting connection.
Fixing the 1997 Corolla's Fuel Line: A Step-by-Step Guide
You may want to see also
Pressure Testing: Rigorous testing is essential to ensure soldered joints can handle expected psi levels
Pressure testing is a critical process in the automotive industry, especially when it comes to ensuring the integrity of fuel lines. Soldering is a common method used to join steel fuel lines, but it's essential to understand the limits of this technique under pressure. When dealing with fuel systems, the pressure can vary significantly, and it's crucial to test the soldered joints to ensure they can withstand the expected psi levels. This rigorous testing process is a standard practice to prevent potential failures and ensure the safety of the vehicle.
The psi (pounds per square inch) that a soldered joint can handle depends on various factors, including the quality of the solder, the cleanliness of the surfaces, and the specific design of the joint. Generally, soldered joints on steel fuel lines should be able to withstand a minimum of 100 psi, but this can vary. For high-performance vehicles or those with modified fuel systems, the psi requirements might be even higher, reaching up to 300 psi or more. Achieving these psi levels in a controlled environment is essential to ensure the joints can handle the real-world conditions they will encounter.
To perform pressure testing, a specialized setup is required. This typically involves a pressure vessel or a test rig that can simulate the psi levels found in the fuel system. The soldered joint is then subjected to this pressure, and its performance is carefully monitored. If the joint fails under pressure, it indicates a potential issue with the soldering process or the materials used. This failure analysis is crucial for improving the overall quality and reliability of the fuel line connections.
During the testing process, various parameters are measured, such as pressure drop, flow rate, and joint integrity. The pressure is gradually increased, and any leaks or signs of failure are noted. If the joint passes the test, it demonstrates its ability to handle the expected psi levels, providing peace of mind to both the manufacturer and the vehicle owner. This level of scrutiny is essential to meet industry standards and ensure the safety of the vehicle's fuel system.
In summary, pressure testing is a vital step in the manufacturing process of steel fuel lines. It ensures that soldered joints can withstand the psi levels encountered in real-world driving conditions. By subjecting these joints to rigorous testing, manufacturers can identify potential weaknesses and improve the overall quality, ultimately providing a safer and more reliable fuel system for vehicles. This process is a testament to the importance of attention to detail in automotive engineering.
Unraveling the Mystery: 1971 Jeep Fuel Line Fitting Secrets
You may want to see also
Frequently asked questions
The psi capacity of a solder joint on a steel fuel line depends on various factors, including the quality of the solder, the thickness of the steel, and the specific application. Generally, a well-executed solder joint can handle pressures up to 150-200 psi, which is suitable for most fuel line applications.
It's not recommended to use regular solder for fuel lines. Regular solder is not designed for high-pressure applications and may not provide a reliable seal. Instead, use a fuel-line specific solder or a flux-core solder designed for steel and fuel line connections.
Steel fuel lines typically have a working pressure range of 100-150 psi. However, it's crucial to consider the design and thickness of the line, as thinner lines may have lower pressure limits. Always refer to the manufacturer's specifications for your specific fuel line.
To achieve a robust solder joint, ensure proper surface preparation by cleaning the steel and removing any oxide layer. Use a flux to prevent oxidation and promote a strong bond. Apply the solder evenly, and heat the joint adequately to allow the solder to melt and create a secure connection.
Yes, there are alternative methods like crimping, clamp-on fittings, or welding, depending on the specific requirements and accessibility. Each method has its advantages and limitations, so it's essential to choose the most suitable technique based on the project's needs and the expertise of the installer.