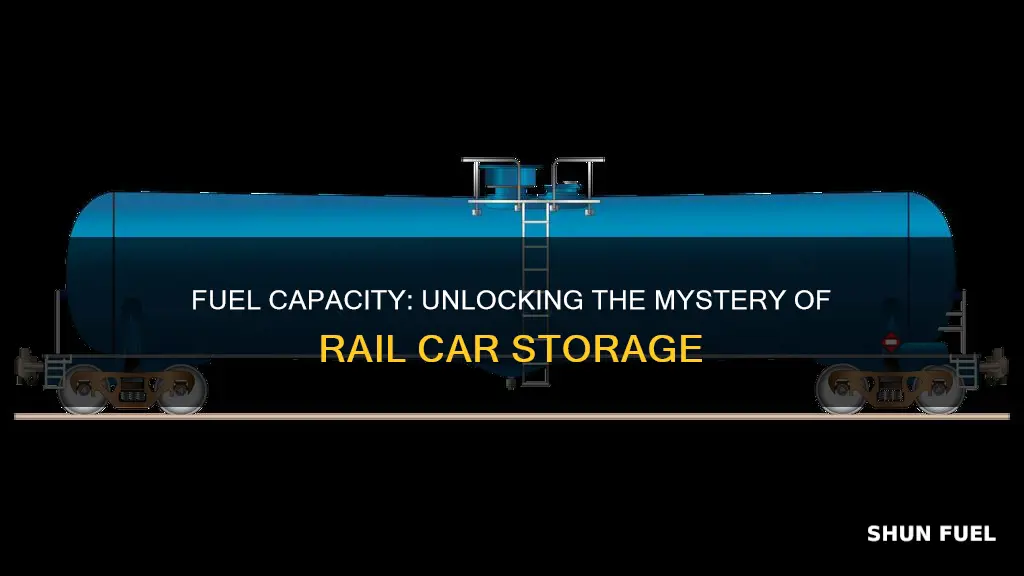
The transportation of fuel via rail cars is a critical aspect of the energy industry, and understanding the capacity of these vehicles is essential for efficient logistics. A single rail car can carry a significant amount of fuel, with the exact volume depending on the type and size of the car. Typically, a standard rail car can hold anywhere from 100,000 to 150,000 gallons of fuel, making it a crucial factor in the planning and management of fuel distribution networks. This capacity allows for the efficient movement of large quantities of fuel over long distances, ensuring a steady supply for various industries and applications.
What You'll Learn
- Fuel Capacity: Determine the volume of fuel a rail car can hold
- Tank Design: Understand the shape and size of fuel tanks
- Material Impact: Consider the impact of tank material on fuel capacity
- Safety Regulations: Adhere to regulations for fuel storage and transportation
- Efficiency Factors: Explore factors affecting fuel efficiency in rail transport
Fuel Capacity: Determine the volume of fuel a rail car can hold
The fuel capacity of a rail car is a critical aspect of its design and functionality, especially for long-haul transportation and logistics. Determining the volume of fuel a rail car can carry involves understanding the specific dimensions and configurations of the vehicle. Here's a detailed guide on how to calculate and assess fuel capacity:
Understanding Rail Car Dimensions:
Rail cars come in various types and sizes, each designed for specific purposes. The fuel capacity is often determined by the car's overall dimensions, including length, width, and height. For instance, a standard 40-foot long rail car might have a different fuel capacity compared to a 50-foot car. The width and height are crucial as they define the internal space available for fuel storage. Measurements should be precise, considering the car's overall structure, including any additional components like fuel tanks or fuel cells.
Calculating Fuel Volume:
The process of determining fuel capacity involves calculating the volume of the available space. This is typically done using the formula for the volume of a rectangular prism, which is length x width x height. For fuel storage, the internal dimensions of the rail car are of utmost importance. You would multiply the length, width, and height of the designated fuel compartment to find the cubic feet or cubic meters of space available for fuel. This calculation provides a precise volume measurement.
Converting to Gallons:
Once you have the volume in cubic feet or cubic meters, the next step is to convert it into gallons, as fuel capacity is often expressed in gallons. The conversion factor depends on the type of fuel. For example, one cubic meter is approximately 264.172 gallons. Multiply the calculated volume by the appropriate conversion factor to determine the fuel capacity in gallons. This step ensures that the fuel capacity is communicated in a standard unit, making it easier for transportation companies and fuel suppliers to understand and utilize.
Considering Fuel Tank Design:
In some cases, rail cars may have specialized fuel tank designs, which can significantly impact fuel capacity. These tanks might be integrated into the car's structure or located in specific compartments. Understanding the arrangement and design of these tanks is essential. Engineers and designers often optimize the placement of fuel tanks to maximize capacity while ensuring structural integrity and safety. This might involve complex calculations and simulations to determine the most efficient fuel storage configuration.
Regulatory Compliance:
It's important to note that fuel capacity calculations must adhere to industry standards and regulations. Different regions and transportation authorities may have specific requirements for fuel storage on rail cars. These regulations ensure safety, environmental protection, and compliance with international standards. Therefore, any fuel capacity determination should be in line with these guidelines to ensure the safe and legal operation of the rail car.
Can Flex-Fuel Cars Run on Diesel? Exploring the Limits of Flexibility
You may want to see also
Tank Design: Understand the shape and size of fuel tanks
When designing fuel tanks for rail cars, understanding the optimal shape and size is crucial for maximizing storage capacity and ensuring efficient transportation. The primary goal is to fit as much fuel as possible while adhering to the physical constraints of the rail car's structure. This involves a careful consideration of various factors, including the available space, the type of fuel, and the necessary safety measures.
The shape of the tank plays a significant role in determining its capacity. Typically, rectangular or cylindrical tanks are used due to their structural integrity and ease of manufacturing. Rectangular tanks offer a flat bottom and sides, allowing for a straightforward design that can be easily integrated into the rail car's frame. These tanks are often used for liquid fuels like diesel or gasoline, providing a practical and cost-effective solution. On the other hand, cylindrical tanks, with their curved walls and circular bases, offer a more compact design, especially when space is limited. This shape is commonly used for fuels like liquefied petroleum gas (LPG) or compressed natural gas (CNG), which require specialized storage due to their unique properties.
Size matters when it comes to fuel tank capacity. The volume of a tank is directly proportional to the amount of fuel it can hold. Engineers must carefully calculate the dimensions to accommodate the required fuel volume while ensuring the tank's weight and center of gravity are within safe limits. For instance, a larger tank might be necessary for long-haul freight trains carrying substantial fuel reserves, whereas shorter routes may only require smaller, more compact tanks.
Additionally, the design must consider the fuel's properties and the environmental conditions it will encounter. Different fuels have varying densities and expansion characteristics, which influence the tank's shape and size. For instance, fuels with higher densities may require thicker walls to withstand the pressure, while those with lower densities might need additional insulation to prevent freezing in colder climates.
In summary, tank design for rail cars involves a meticulous process of selecting the right shape and size to optimize fuel storage. This includes considering the available space, fuel type, and safety factors. By understanding these principles, engineers can create efficient and reliable fuel systems for various rail applications, ensuring safe and cost-effective transportation of fuels over long distances.
European Cars: Unlocking Fuel Efficiency Secrets
You may want to see also
Material Impact: Consider the impact of tank material on fuel capacity
The material of the fuel tank plays a critical role in determining the capacity and overall performance of a rail car's fuel storage system. Different materials offer unique advantages and considerations when it comes to fuel capacity and safety. For instance, steel tanks are commonly used due to their durability and strength, making them suitable for transporting large volumes of fuel over long distances. The thickness of the steel can vary, and thicker gauges provide better protection against corrosion and external impacts, ensuring the fuel remains secure during transit. However, steel tanks may be heavier, which can impact the overall weight capacity of the rail car.
In contrast, aluminum tanks offer a lighter alternative, reducing the overall weight of the rail car and potentially allowing for increased fuel capacity. Aluminum is known for its excellent corrosion resistance, which is crucial for maintaining the quality of the fuel over time. This material is often chosen for its ability to provide a lightweight, yet robust, solution for fuel storage. Additionally, aluminum tanks can be designed with advanced welding techniques, ensuring a seamless and leak-proof structure.
Another consideration is the use of composite materials, which have gained popularity in the transportation industry. Composite tanks offer a balance between strength and weight, often providing a higher fuel capacity compared to traditional metal tanks. These materials are known for their resistance to corrosion and impact, making them ideal for long-haul rail operations. The composite structure can also be designed to withstand extreme temperatures, ensuring the fuel remains stable and secure.
The choice of tank material directly influences the overall efficiency and safety of the fuel transportation process. Materials like stainless steel and high-density polyethylene (HDPE) are often employed for their superior corrosion resistance, ensuring the fuel's integrity. HDPE, in particular, is lightweight and offers excellent chemical resistance, making it a popular choice for fuel tanks in various industries. The impact of material selection on fuel capacity is significant, as it determines the amount of fuel that can be carried, which, in turn, affects the rail car's operational range and efficiency.
In summary, the material impact on fuel capacity is a critical aspect of rail car design. Engineers and designers must carefully consider the properties of different materials to optimize fuel storage solutions. By selecting the appropriate tank material, it is possible to achieve a balance between capacity, weight, and safety, ensuring efficient and reliable fuel transportation by rail. This consideration is essential for meeting the demands of various industries and contributing to sustainable transportation practices.
Aging Fuel: Does It Still Work in Your Car?
You may want to see also
Safety Regulations: Adhere to regulations for fuel storage and transportation
The transportation and storage of fuel, especially in large quantities, require strict adherence to safety regulations to prevent accidents and mitigate potential hazards. When it comes to rail cars, the capacity for fuel storage is a critical factor to consider, and it is essential to understand the regulations governing this aspect.
One of the primary regulations is the limitation on the volume of fuel that can be transported in a single rail car. This is typically standardized and varies depending on the type of fuel and the country's regulations. For instance, in the United States, the Department of Transportation (DOT) has set specific guidelines for the maximum capacity of fuel tanks on rail cars. These guidelines ensure that the storage and transportation of fuel are safe and do not pose a risk to the environment or public health. It is crucial for transportation companies and fuel suppliers to be aware of these limits to ensure compliance.
Rail cars used for fuel transportation are designed with specific safety features to prevent leaks and minimize the risk of fire. These include double-walled tanks, emergency shut-off valves, and spill containment systems. Adhering to these design standards is essential to ensure that any potential hazards are mitigated. Regular inspections and maintenance of these rail cars are mandated to identify and rectify any issues promptly.
Furthermore, the transportation process must follow strict protocols. This includes proper labeling and marking of the rail cars to indicate the type and volume of fuel being transported. Proper documentation and paperwork are also required to track the movement of fuel, ensuring that all legal and safety requirements are met.
In summary, adhering to safety regulations is paramount when it comes to fuel storage and transportation on rail cars. Understanding and complying with the volume limitations, implementing safety-designed infrastructure, and following transportation protocols are essential to prevent accidents and protect the environment and public safety. It is a responsibility shared by all stakeholders in the fuel industry to ensure a secure and efficient system.
Car Blower Fuel Efficiency: Fact or Fiction?
You may want to see also
Efficiency Factors: Explore factors affecting fuel efficiency in rail transport
The efficiency of fuel usage in rail transport is a critical aspect of the industry, and several factors contribute to optimizing this process. One key factor is the design and technology of the rolling stock itself. Modern trains, especially those designed for high-speed rail networks, incorporate advanced aerodynamics to minimize air resistance, which directly impacts fuel consumption. For instance, the sleek and streamlined design of bullet trains significantly reduces drag, allowing them to achieve higher speeds with less fuel expenditure. Additionally, the use of lightweight materials in construction can further enhance efficiency by reducing the overall weight of the train, thereby decreasing the power required to accelerate and maintain speed.
Another crucial element is the maintenance and condition of the rail infrastructure. Efficient rail transport relies on well-maintained tracks, bridges, and signaling systems. Smooth and properly aligned tracks ensure that the train's wheels roll with minimal resistance, reducing energy loss and improving fuel efficiency. Regular maintenance also includes checking and replacing worn-out components such as bearings, gears, and brakes, which can significantly impact fuel consumption. Well-maintained infrastructure also includes efficient signaling systems, allowing trains to run closer together and optimize their schedules, thereby reducing the overall fuel usage for a given number of passengers or freight carried.
The operational strategies employed by rail operators play a significant role in fuel efficiency. Efficient scheduling and route planning can minimize unnecessary stops and starts, which are major fuel consumers. For example, implementing a centralized traffic management system can optimize train schedules, reducing delays and the associated fuel wastage. Additionally, adopting advanced traction control systems can ensure that the train's motors provide the precise amount of power required, further enhancing efficiency.
The type of fuel used is another critical factor. While diesel has traditionally been the primary fuel for rail transport, the industry is increasingly transitioning towards more sustainable alternatives. Electric trains, powered by overhead lines or third rails, offer a cleaner and often more efficient option. These trains can be particularly effective when integrated with renewable energy sources, such as solar or wind power, for charging. Moreover, the use of biofuels or hydrogen fuel cells in rail transport is gaining traction, offering even lower carbon emissions and improved efficiency.
Lastly, the weight and volume of cargo carried also impact fuel efficiency. Efficient loading and unloading practices, as well as proper cargo securing, ensure that the train's weight is optimized for the journey. Overloading or improperly secured cargo can increase rolling resistance and require more fuel to maintain speed. Therefore, rail operators should adhere to loading guidelines and employ efficient cargo management strategies to maximize fuel efficiency.
Mastering the Art of Fuel Transfer: A Guide to Siphoning Gas from Your New Car
You may want to see also
Frequently asked questions
The capacity of a rail car for fuel can vary significantly depending on its type and purpose. For example, a typical tank car used for transporting petroleum products can hold anywhere between 20,000 to 30,000 gallons (75,000 to 113,000 liters). However, some specialized rail cars designed for high-capacity fuel transportation can carry even more, up to 100,000 gallons (378,541 liters) or more.
The fuel capacity of a rail car is influenced by several factors, including the type of fuel being transported, the car's design, and regulatory requirements. Different fuels have varying densities and volumes, so the capacity is often determined by the specific fuel's properties and the car's internal dimensions. Additionally, transportation regulations set by organizations like the American Association of Railroads (AAR) and the International Union of Railways (UIC) dictate the maximum allowable capacity for different types of rail cars.
Absolutely, safety is a critical aspect of fuel transportation by rail. Rail cars designed for fuel storage must adhere to strict safety standards and regulations to prevent accidents and environmental hazards. These include measures such as double-walled tanks to minimize the risk of leaks, emergency venting systems, and advanced monitoring technologies to detect and respond to potential issues. Regular inspections and maintenance are also essential to ensure the safe operation of fuel rail cars.