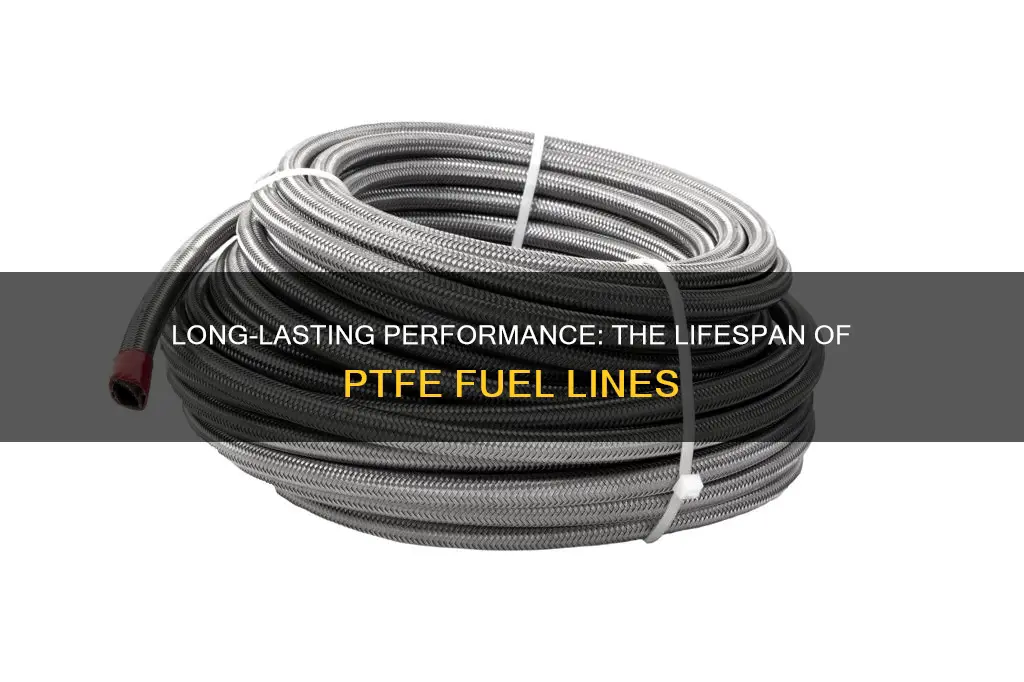
PTFE (polytetrafluoroethylene) fuel lines are known for their exceptional durability and resistance to wear and tear, making them a popular choice for many applications. However, the lifespan of these fuel lines can vary depending on several factors, including the quality of the material, the environment in which they are used, and the maintenance they receive. This article will explore the factors that influence the longevity of PTFE fuel lines and provide insights into how long they can typically last under different conditions.
Characteristics | Values |
---|---|
Lifespan | Up to 20 years |
Temperature Resistance | -60°C to 260°C (-76°F to 520°F) |
Chemical Resistance | Excellent resistance to fuels, oils, and solvents |
Flexibility | Highly flexible, allowing for easy installation and routing |
Durability | Resistant to UV radiation and ozone, ensuring long-term stability |
Compatibility | Compatible with a wide range of materials, including metals and plastics |
Color | Typically black or white |
Cost | Higher initial cost compared to some alternatives, but provides long-term savings |
Installation | Easy to install and replace due to its flexibility and durability |
What You'll Learn
- Durability: PTFE fuel lines are highly durable and resistant to wear and tear
- Temperature Tolerance: They can withstand extreme temperatures, making them suitable for various climates
- Chemical Resistance: Resistant to most chemicals, including fuels, oils, and solvents
- Flexibility: Flexible and can bend without kinking, ensuring smooth fuel flow
- Longevity: With proper care, PTFE fuel lines can last 10-15 years or more
Durability: PTFE fuel lines are highly durable and resistant to wear and tear
PTFE (polytetrafluoroethylene) fuel lines are renowned for their exceptional durability and resistance to wear and tear, making them a popular choice for fuel delivery systems in various applications. This material is engineered to withstand the rigors of fuel transportation and is particularly useful in high-performance vehicles, marine engines, and industrial machinery. The durability of PTFE fuel lines can be attributed to several key factors. Firstly, PTFE is an extremely strong and flexible material, capable of withstanding significant pressure and movement without compromising its structural integrity. This flexibility allows the fuel lines to navigate through tight spaces and absorb vibrations, ensuring a secure and reliable connection without the risk of damage.
The resistance of PTFE to wear and tear is another critical aspect of its durability. PTFE fuel lines are designed to resist the effects of fuel, including its corrosive properties and potential to cause degradation over time. The material's non-stick surface prevents the accumulation of fuel contaminants, such as varnish and sludge, which can lead to blockages and reduced performance. Additionally, PTFE is highly resistant to temperature fluctuations, ensuring that the fuel lines can maintain their structural integrity in a wide range of environmental conditions. This resistance to wear and tear is particularly important in applications where fuel lines are exposed to extreme temperatures, such as in high-altitude environments or during rapid acceleration and deceleration.
The durability of PTFE fuel lines also extends to their ability to resist chemical corrosion. PTFE is inherently inert and does not react with most chemicals, including fuels and lubricants. This property ensures that the fuel lines remain stable and do not degrade or become compromised over time, even when exposed to harsh chemicals. As a result, PTFE fuel lines can provide long-lasting performance and reliability, reducing the need for frequent replacements and minimizing downtime in critical applications.
Furthermore, the manufacturing process of PTFE fuel lines involves precise engineering and quality control measures. The material is carefully selected and processed to ensure consistency and adherence to strict specifications. This attention to detail contributes to the overall durability and performance of the fuel lines, making them a trusted choice for professionals in various industries. In summary, PTFE fuel lines offer a high level of durability and resistance to wear and tear, making them an excellent solution for fuel delivery systems that require long-lasting performance and reliability.
In conclusion, the durability of PTFE fuel lines is a result of their exceptional strength, flexibility, and resistance to wear and tear. These lines are engineered to withstand the challenges of fuel transportation and provide a secure, reliable connection without compromising performance. The material's non-stick properties, temperature resistance, and chemical inertness further enhance its durability, ensuring that PTFE fuel lines can deliver consistent results in a wide range of applications. With their long-lasting performance and minimal maintenance requirements, PTFE fuel lines are a valuable investment for anyone seeking a reliable and robust fuel delivery system.
F150 Fuel Line: Understanding Proper Ratings and Safety
You may want to see also
Temperature Tolerance: They can withstand extreme temperatures, making them suitable for various climates
PTFE (Polytetrafluoroethylene) fuel lines are renowned for their exceptional temperature tolerance, which is a critical factor in their longevity and versatility. This unique property allows them to perform reliably across a wide range of climates and environmental conditions.
The temperature resistance of PTFE is attributed to its chemical structure. The material is known for its stability and resistance to degradation, even under extreme heat and cold. It can withstand temperatures as low as -450°F (-268°C) and as high as 500°F (260°C), making it suitable for a variety of applications. This wide temperature range ensures that PTFE fuel lines can be used in diverse environments, from the frigid Arctic to the scorching deserts.
In cold climates, where temperatures can drop significantly below freezing, PTFE fuel lines remain flexible and functional. This is crucial for maintaining the flow of fuel in vehicles and equipment, ensuring that the system operates efficiently even in extreme cold. The material's ability to resist brittleness and cracking at low temperatures is a significant advantage in such harsh conditions.
Conversely, in hot climates, where temperatures can soar, PTFE fuel lines excel. They can withstand the heat without softening or degrading, which is essential for preventing fuel leaks and maintaining the integrity of the fuel system. This temperature tolerance is particularly important in high-performance applications, where fuel lines are subjected to rapid temperature fluctuations.
The temperature tolerance of PTFE fuel lines also contributes to their overall durability. By withstanding extreme temperatures, they are less likely to suffer from material fatigue or degradation over time, ensuring a longer lifespan. This makes PTFE fuel lines a reliable choice for both short-term and long-term applications, providing consistent performance and peace of mind to users.
PTFE Tape: A Reliable Seal for Automotive Fuel Lines?
You may want to see also
Chemical Resistance: Resistant to most chemicals, including fuels, oils, and solvents
PTFE (polytetrafluoroethylene) fuel lines are renowned for their exceptional chemical resistance, making them a popular choice for various applications, especially in the automotive and marine industries. This unique property ensures that the fuel lines can withstand exposure to a wide range of chemicals, including fuels, oils, and solvents, without compromising their structural integrity. The resistance to these substances is a result of the material's molecular structure, which is highly stable and resistant to degradation.
In the context of fuel lines, chemical resistance is a critical factor in ensuring the longevity and reliability of the system. Fuels, oils, and solvents often contain various additives and impurities that can be corrosive to other materials. However, PTFE's inert nature means it remains unaffected by these substances, providing a protective barrier between the fuel and the line material. This resistance is particularly important in high-temperature environments, where the fuel lines are exposed to extreme conditions, ensuring that the material does not break down or become brittle over time.
The chemical resistance of PTFE fuel lines is not just limited to the prevention of corrosion but also ensures that the lines can maintain their flexibility and durability. Unlike some other materials that may become stiff or brittle when exposed to certain chemicals, PTFE remains pliable, allowing for easy bending and installation without the risk of cracking or fragmentation. This flexibility is essential for the fuel lines' ability to withstand the dynamic forces and vibrations encountered during vehicle operation.
Furthermore, the resistance to fuels and oils is particularly advantageous in automotive applications. Fuel lines made from PTFE can be used in high-performance engines without the fear of degradation or performance loss. This is especially important in racing or high-demand vehicles where fuel lines must endure rapid acceleration, high temperatures, and varying pressure conditions. The chemical resistance ensures that the fuel lines remain intact, providing a reliable supply of fuel to the engine.
In summary, the chemical resistance of PTFE fuel lines is a key factor in their longevity and performance. This resistance to fuels, oils, and solvents allows for their use in a wide range of applications, ensuring that the fuel lines remain intact and functional over extended periods. As a result, PTFE fuel lines are a reliable and durable solution for various industries, offering peace of mind to users and professionals alike.
F250 Fuel Line Disconnect: Choosing the Right Tool Size
You may want to see also
Flexibility: Flexible and can bend without kinking, ensuring smooth fuel flow
The flexibility of PTFE (Polytetrafluoroethylene) fuel lines is one of its most notable advantages, especially in automotive applications. This material is renowned for its ability to bend and twist without kinking, which is crucial for maintaining a consistent and smooth fuel flow throughout the engine's system. Unlike traditional rubber hoses, PTFE lines offer a more pliable and durable alternative, ensuring that the fuel supply remains uninterrupted even in tight spaces or under various vehicle angles. This flexibility is particularly beneficial in high-performance engines where fuel efficiency and power output depend on the precision and reliability of the fuel delivery system.
When it comes to installation, the flexibility of PTFE fuel lines simplifies the process, allowing mechanics to navigate around obstacles and fit the lines into complex engine compartments with ease. This feature is especially advantageous in classic car restoration projects or when modifying a vehicle's fuel system to accommodate high-performance upgrades. The material's pliability reduces the risk of damage during installation, ensuring a neat and secure setup.
Furthermore, the flexibility of PTFE fuel lines contributes to their longevity. The material's ability to withstand repeated bending and twisting without permanent deformation ensures that the fuel lines maintain their structural integrity over time. This is particularly important in high-vibration environments, where traditional fuel lines might suffer from wear and tear, leading to potential fuel leaks or system failures.
In summary, the flexibility of PTFE fuel lines is a key factor in their durability and performance. This characteristic ensures a consistent fuel flow, simplifies installation processes, and provides long-term reliability, making PTFE fuel lines an excellent choice for both automotive enthusiasts and professionals seeking a robust and efficient fuel delivery system. With proper care and maintenance, these fuel lines can provide a reliable and long-lasting solution for various engine applications.
Mastering the Art of Welding: Safe Techniques for Auto Fuel Lines
You may want to see also
Longevity: With proper care, PTFE fuel lines can last 10-15 years or more
PTFE (Polytetrafluoroethylene) fuel lines are renowned for their exceptional durability and longevity, making them a popular choice for various applications, especially in the automotive and marine industries. When properly maintained and installed, these fuel lines can offer a long-lasting solution for transporting fuel efficiently and safely.
The longevity of PTFE fuel lines is attributed to the material's inherent properties. PTFE is a synthetic fluoropolymer known for its exceptional resistance to heat, chemicals, and abrasion. This makes it highly suitable for fuel transport as it can withstand the corrosive nature of gasoline, diesel, and other fuels. Additionally, PTFE's non-stick surface reduces the risk of fuel contamination and ensures a smooth flow, contributing to its long-term reliability.
Proper care and maintenance are crucial to maximizing the lifespan of PTFE fuel lines. Regular inspections should be conducted to identify any signs of damage, such as cracks, punctures, or swelling. Early detection can prevent further deterioration and ensure the lines remain intact. It is also essential to use compatible lubricants when installing or replacing PTFE fuel lines to avoid any potential damage.
In terms of installation, following manufacturer guidelines is essential. Properly securing the fuel lines, using appropriate clamps, and ensuring a tight fit can prevent leaks and extend the lines' life. Additionally, avoiding sharp bends or kinks that could compromise the material's integrity is vital.
With regular maintenance and responsible usage, PTFE fuel lines can easily last 10 to 15 years or even longer. This longevity makes them a cost-effective and reliable solution for fuel transport, especially in applications where traditional rubber or plastic lines may not be suitable. Proper care ensures that these fuel lines remain a dependable component of any fuel system, providing efficient and safe operation over an extended period.
Fuel Line Fixes: A Guide to Common Issues and Solutions
You may want to see also
Frequently asked questions
The lifespan of a PTFE fuel line can vary depending on several factors, including the quality of the material, installation, and environmental conditions. However, when properly installed and maintained, a high-quality PTFE fuel line can last for many years, often exceeding 10 years or more.
Several factors can influence the longevity of PTFE fuel lines. These include the operating temperature range, exposure to sunlight or UV radiation, chemical compatibility with the fuel, and the presence of contaminants or debris in the fuel. Proper selection of the PTFE material grade and ensuring a secure installation can also contribute to a longer-lasting fuel line.
Yes, PTFE fuel lines are commonly used in outdoor applications due to their excellent resistance to weathering and UV radiation. They can withstand exposure to sunlight, rain, and temperature fluctuations, making them suitable for above-ground fuel lines, such as those used in boats, recreational vehicles, or outdoor power equipment.
Regular inspection of PTFE fuel lines is recommended to ensure their continued performance and longevity. It is advised to inspect the lines at least once a year or more frequently if the vehicle or equipment is used regularly or in harsh conditions. Inspecting for any signs of damage, cracks, or degradation will help identify potential issues early on and prevent costly repairs or replacements.
Proper maintenance can significantly contribute to the longevity of PTFE fuel lines. It is essential to keep the fuel clean and free of contaminants, as debris or moisture can compromise the line's performance. Regularly checking the fuel line for any signs of damage and ensuring a tight, secure connection can also help prevent leaks and extend the life of the fuel line.