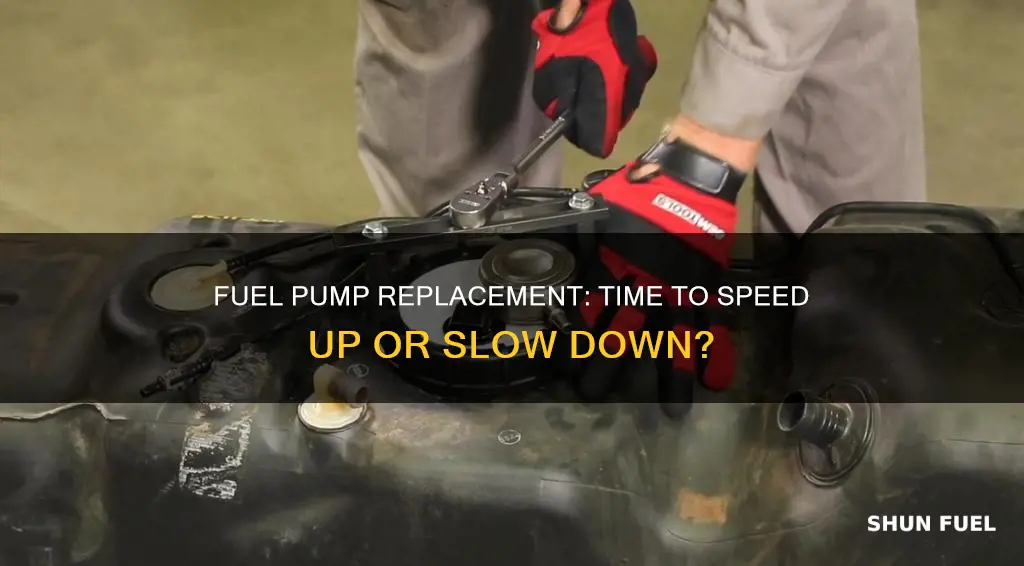
Replacing a fuel pump is a crucial repair for vehicle owners, as it ensures the car can run smoothly and efficiently. The time it takes to replace a fuel pump can vary depending on several factors, including the make and model of the vehicle, the accessibility of the pump, and the mechanic's experience. Generally, the process involves removing the old pump, installing the new one, and conducting a series of tests to ensure proper functionality. This task often requires specialized tools and knowledge, making it a job best handled by professional mechanics. Understanding the timeline for this repair is essential for vehicle owners to plan their schedules and ensure their cars are back on the road as quickly as possible.
Characteristics | Values |
---|---|
Time Duration | 1-2 hours (for a professional mechanic) |
Complexity | Moderate to difficult, requires some mechanical knowledge |
Tools Required | Wrenches, socket set, fuel pump removal tool, new fuel pump |
Vehicle Access | Easy to moderate, depending on vehicle model and design |
Safety Precautions | Disconnect the battery, drain fuel, and use safety gear |
Common Issues | Fuel pump failure, fuel leaks, engine misfires |
Cost | Parts: $100 - $300, Labor: $100 - $200 (varies by location) |
DIY Difficulty | Advanced, requires experience and specialized tools |
What You'll Learn
- Diagnosis: Identify fuel pump issues through visual inspection and diagnostic tests
- Accessing the Pump: Locate and remove the old pump, ensuring proper access
- Installation: Carefully install the new pump, following manufacturer instructions
- Testing: Verify pump functionality with a fuel pressure gauge
- Safety Precautions: Ensure engine is off and fuel system is isolated before replacement
Diagnosis: Identify fuel pump issues through visual inspection and diagnostic tests
When diagnosing fuel pump issues, a thorough visual inspection and diagnostic testing are essential to identify the problem accurately. Here's a step-by-step guide to help you through this process:
Visual Inspection: Start by examining the fuel pump and its surroundings. Look for any visible signs of damage, such as cracks, leaks, or corrosion around the pump housing. Inspect the fuel lines for any signs of wear, cracks, or damage. Check for any loose connections or fittings that might indicate a potential issue. Pay attention to the fuel tank and ensure there are no signs of contamination or excessive fuel accumulation, as this could affect the pump's performance. If you notice any physical damage or unusual wear, it could be an indication of a failing or faulty fuel pump.
Diagnostic Tests:
- Fuel Pressure Test: Use a fuel pressure gauge to measure the pressure in the fuel system. Compare the readings to the manufacturer's specifications. Low fuel pressure can indicate a pump issue, as it may struggle to deliver the required fuel volume.
- Continuity Test: Test the fuel pump's electrical connections and the pump itself using a multimeter. Check for continuity to ensure the pump is receiving power and functioning correctly.
- Engine Diagnostics: Start the engine and monitor for any error codes using an OBD (On-Board Diagnostics) scanner. Engine-specific codes can provide valuable insights into potential fuel pump problems.
- Fuel Flow Measurement: Measure the fuel flow rate using a specialized tool. Compare it to the expected value to determine if the pump is delivering the correct amount of fuel.
During the inspection, it's crucial to consider the vehicle's age, mileage, and maintenance history. Older vehicles or those with high mileage might be more susceptible to fuel pump issues. Additionally, look for any warning signs or symptoms reported by the vehicle's owner, such as difficulty starting, poor engine performance, or unusual noises during operation.
By combining a visual inspection with these diagnostic tests, you can effectively identify fuel pump problems and determine the necessary course of action, whether it's repairing or replacing the pump. This process ensures a more accurate diagnosis, saving time and resources in the long run.
Replacing the Fuel Pump in a 1996 Jeep Cherokee
You may want to see also
Accessing the Pump: Locate and remove the old pump, ensuring proper access
To replace a fuel pump, the first step is to gain access to the old pump. This process requires a systematic approach to ensure you locate the correct components and safely remove the existing pump. Here's a detailed guide on how to access and remove the fuel pump:
Locate the Fuel Pump: The fuel pump is typically located near the fuel tank, often in the engine compartment. It is usually positioned close to the tank's rear or side, depending on your vehicle's design. Consult your vehicle's manual or online resources to identify the exact location. The pump is often secured with brackets or clips, so you may need to remove these to access it.
Prepare the Vehicle: Before starting, ensure the vehicle is parked on a level surface and the engine is cool. This is important for safety and to prevent any accidental starting of the engine during the process. Engage the parking brake to secure the vehicle.
Remove the Fuel Tank (if necessary): In some cases, you might need to remove the fuel tank to gain complete access to the pump. This step is more common in older vehicles or those with a complex engine layout. If you need to remove the tank, carefully drain the fuel and disconnect the fuel lines. Then, lift the tank away from the vehicle, being cautious of any sharp edges.
Access the Pump: Once you have located the fuel pump, you'll need to remove any panels or covers that might be in the way. This could include engine bay panels, fender liners, or even the air intake system, depending on your vehicle. Carefully pry open or remove these panels, setting them aside in a secure place. Then, locate the pump's mounting brackets or screws and carefully remove them.
Remove the Old Pump: With the pump now accessible, you can proceed to take it out. This might involve sliding it out of its housing or unscrewing it from the mounting points. Be gentle but firm to avoid damaging any surrounding components. If the pump is particularly stubborn, you may need to use a small pry bar or a similar tool to carefully lift it out. Ensure you have a clear view of the pump's connections and take note of their positions for easier reinstallation.
Replacing the Fuel Pump in Your 1996 Chrysler Cirrus
You may want to see also
Installation: Carefully install the new pump, following manufacturer instructions
When replacing a fuel pump, the installation process requires careful attention to detail and adherence to manufacturer guidelines. This is a crucial step to ensure the new pump functions correctly and safely. Here's a step-by-step guide to help you through the installation:
Preparation: Before you begin, ensure you have the necessary tools and equipment, including the new fuel pump, a wrench or socket set, and possibly a fuel filter if it needs replacement. It's essential to work in a well-ventilated area and wear protective gear, such as gloves and goggles, to avoid any potential hazards.
Locate the Old Pump: Identify the old fuel pump, which is typically located near the fuel tank. Carefully inspect the pump for any signs of damage or wear. Take note of the connections and any unique features of the old pump, as these details will be crucial for the installation of the new one.
Remove the Old Pump: Start by draining any remaining fuel from the tank to prevent spills. Then, carefully disconnect the electrical connections and fuel lines from the old pump. Loosen the bolts or fasteners securing the pump in place, being mindful of any specific torque requirements. Gently pull the old pump out of the vehicle, setting it aside for inspection or disposal.
Install the New Pump: Now, carefully follow the manufacturer's instructions for installing the new fuel pump. This process may vary depending on the vehicle make and model. Typically, you'll need to align the new pump with the mounting points, secure it with the appropriate fasteners, and reconnect the electrical wiring and fuel lines. Ensure all connections are tight and secure.
Final Steps: After installing the new pump, double-check all connections and secure any loose components. Reinstall the fuel tank, ensuring it is properly aligned and secured. Test the vehicle's fuel system by starting the engine and monitoring for any leaks or unusual noises. If everything is functioning correctly, you've successfully replaced the fuel pump.
Remember, each vehicle may have unique installation requirements, so always refer to the manufacturer's instructions for the most accurate and safe procedure.
Replacing Fuel Lines: 2007 Dodge Caliber Step-by-Step Guide
You may want to see also
Testing: Verify pump functionality with a fuel pressure gauge
When replacing a fuel pump, it's crucial to verify its functionality to ensure the vehicle operates safely and efficiently. One effective method for testing the pump is using a fuel pressure gauge. This tool measures the pressure of the fuel in the system, allowing you to confirm that the pump is delivering the correct amount of fuel to the engine. Here's a step-by-step guide on how to test the pump's functionality using a fuel pressure gauge:
Preparation: Before beginning the test, ensure you have the necessary tools and equipment, including a fuel pressure gauge, a set of wrenches or sockets, and a fuel line connector. It is also recommended to wear protective gear, such as gloves and safety goggles, to prevent any potential fuel-related hazards. Locate the fuel pump, which is typically found near the engine or in the fuel tank, and identify the fuel line connections.
Step-by-Step Process:
- Disconnect the Fuel Line: Carefully disconnect the fuel line from the fuel pump. This step requires patience and a gentle approach to avoid damaging the fuel line or pump. Take note of the fuel line's position and orientation for future reassembly.
- Attach the Gauge: Securely attach the fuel pressure gauge to the disconnected fuel line. Ensure a tight connection to guarantee accurate readings. The gauge should have clear markings indicating the pressure range you expect to measure.
- Start the Engine: Turn on the vehicle's engine and allow it to idle for a few minutes. This step is essential to ensure the engine's temperature reaches a stable level, which can affect fuel pressure readings.
- Read the Pressure: Observe the fuel pressure gauge and record the reading. The ideal pressure will vary depending on the vehicle's specifications and engine type. Consult the vehicle's manual or a reliable source for the recommended pressure range. If the measured pressure is within the expected range, it indicates that the fuel pump is functioning correctly.
- Check for Leaks: After the initial reading, turn off the engine and check for any fuel leaks around the connections. Leaks can occur due to damaged fuel lines or improper connections, and they should be addressed before reassembling the system.
Troubleshooting: If the measured pressure is below the expected range, it may indicate a faulty fuel pump or a restricted fuel line. In such cases, further investigation is required. Check for any clogs or restrictions in the fuel line and ensure the pump is receiving the correct voltage and ground. If the issue persists, consider consulting a professional mechanic for a thorough diagnosis.
By following these steps, you can effectively test the fuel pump's functionality and ensure a successful replacement process. Remember, proper testing is essential to avoid potential issues and ensure the vehicle's overall performance and safety.
Replacing the Fuel Pump in a 2006 Ford Focus ZX3
You may want to see also
Safety Precautions: Ensure engine is off and fuel system is isolated before replacement
Safety is paramount when working on any vehicle, and replacing a fuel pump is no exception. Before you begin the replacement process, it is crucial to prioritize safety and ensure that the engine is in a secure and controlled state. The first and most critical step is to turn off the engine and allow it to cool down. This simple action is often overlooked, but it is essential for your safety and the success of the repair. Running the engine while working on it can lead to dangerous situations, such as sudden bursts of fuel pressure or the risk of fire.
Once the engine is off, the next step is to isolate the fuel system. This involves disconnecting the fuel pump and any associated fuel lines to prevent the flow of fuel. Fuel is a highly flammable and volatile substance, and any spark or heat source could result in a dangerous explosion. By isolating the fuel system, you create a safe working environment, reducing the risk of accidents and injuries. It is recommended to use a fuel pump disconnect tool or a similar device to safely release any remaining pressure in the system.
When working with fuel, it is essential to exercise caution and wear appropriate personal protective equipment (PPE). This includes gloves to protect your hands from potential fuel spills and eye protection to shield your eyes from any splashes. Ensure that you are working in a well-ventilated area to avoid inhaling any fumes, which can be harmful if inhaled. Additionally, keep a fire extinguisher nearby as a precaution against any potential fire hazards.
After ensuring the engine is off and the fuel system is isolated, it is a good practice to double-check for any remaining fuel pressure. You can use a pressure gauge to verify that the system is depressurized. This step is crucial to prevent any unexpected fuel release during the replacement process. By taking these safety precautions, you create a controlled environment, allowing you to focus on the task at hand without compromising your well-being or the integrity of the repair.
Remember, taking the time to properly isolate the fuel system and ensure the engine is off is not just a safety measure but also a best practice in automotive repair. It demonstrates your commitment to safety and can prevent potential hazards, making the replacement process smoother and more efficient. Always prioritize safety, and the rest of the replacement process will become more manageable.
Replacing Fuel Injectors in a 2000 Ford Ranger: Step-by-Step Guide
You may want to see also
Frequently asked questions
The time required to replace a fuel pump can vary depending on several factors, including the vehicle's make and model, the accessibility of the pump, and the mechanic's experience. On average, it can take anywhere from 1 to 4 hours for a professional mechanic to complete this task.
While some vehicle owners with mechanical knowledge and experience might attempt to replace the fuel pump themselves, it is generally recommended to have this task performed by a qualified mechanic. Fuel pumps are located in various positions within the vehicle, and improper installation can lead to fuel leaks, electrical issues, or even engine damage.
There are several indicators that your fuel pump may need replacement. These include difficulty starting the engine, frequent stalling, reduced engine performance, unusual noises coming from the fuel tank, or a strong odor of gasoline in the vehicle. If you experience any of these symptoms, it's advisable to have the fuel pump inspected by a professional.
The cost of replacing a fuel pump can vary widely depending on the vehicle, the location of the pump, and the mechanic's labor rates. On average, you can expect to pay anywhere from $200 to $800 for the parts and labor. Some luxury or high-performance vehicles may have more expensive fuel pumps and labor costs.
In some cases, if the fuel pump is failing but not completely dead, there might be temporary fixes to get you to a mechanic's shop. This could include using a fuel pump relay adapter or a temporary fuel pump relay to bypass the faulty pump. However, these solutions are not permanent and should be followed by a proper replacement to ensure the long-term reliability of your vehicle's fuel system.