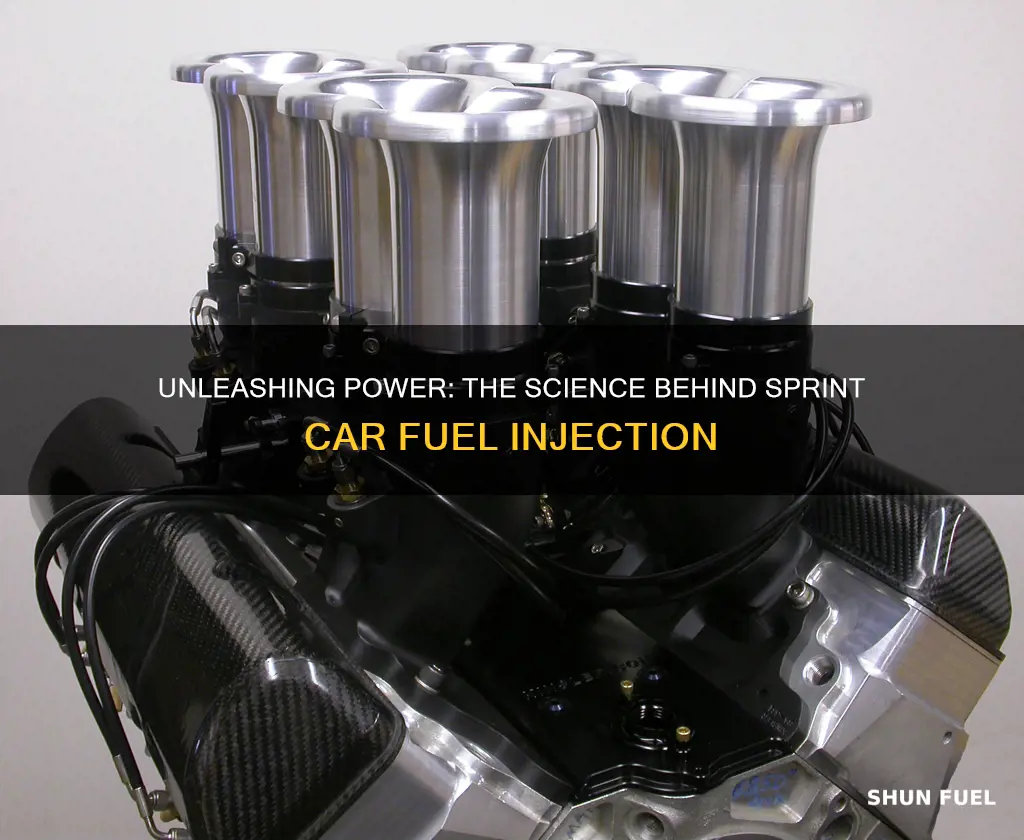
Sprint car fuel injection is a sophisticated system that plays a crucial role in optimizing engine performance. It involves precise control of fuel delivery, ensuring that the engine receives the right amount of fuel at the right time. This technology enhances power output, improves fuel efficiency, and reduces emissions, making it a key component in the high-performance world of sprint cars.
What You'll Learn
- Fuel Delivery: Fuel is pumped from the tank to the injectors via a high-pressure line
- Sensor Input: Engine sensors provide data on speed, load, and temperature to adjust fuel
- Fuel Atomization: Injectors spray fuel into the intake manifold as a fine mist
- Timing Control: Injection timing is precise, synchronized with engine cycles for optimal performance
- EPC Management: Engine Control Unit (ECU) uses data to calculate and control fuel injection
Fuel Delivery: Fuel is pumped from the tank to the injectors via a high-pressure line
In the world of sprint cars, fuel delivery is a critical component of the engine's performance. The process begins with the fuel tank, which stores the gasoline that powers the engine. When the driver engages the throttle, a series of precise actions are initiated to deliver the fuel to the injectors.
The heart of this system is the fuel pump, a high-pressure unit designed to push fuel from the tank to the injectors. This pump is typically located near the engine and is powered by a small electric motor. When the engine is running, the pump operates at a specific speed and pressure, ensuring a consistent and controlled fuel flow. The high-pressure line is a crucial element here; it is a robust, flexible hose that connects the pump to the injectors, capable of withstanding the extreme forces and temperatures within the engine bay.
As the fuel is pumped, it travels through this high-pressure line, which is designed to minimize fuel loss and maintain the integrity of the fuel-air mixture. The line is often made of durable materials to handle the pressure and temperature variations. The injectors are strategically positioned to receive the fuel, and they are responsible for precisely metering and injecting the fuel into the engine's cylinders. This process is highly controlled, ensuring that the correct amount of fuel is delivered at the right time, optimizing combustion and power output.
The design and placement of the fuel injectors are critical to the engine's performance. They are typically located close to the intake valves, allowing for rapid fuel injection and ensuring a quick response to throttle inputs. This proximity also helps in maintaining a consistent fuel-air mixture, which is essential for efficient combustion. The injectors use precise solenoid-controlled valves to regulate the fuel flow, opening and closing at specific times to deliver the required amount of fuel for each cylinder.
In summary, the fuel delivery system in a sprint car is a complex yet finely tuned process. It involves a high-pressure fuel pump, a robust high-pressure line, and strategically placed injectors, all working in harmony to provide the engine with the precise fuel-air mixture needed for optimal performance. This system's efficiency is a testament to the engineering prowess required to meet the demanding needs of high-performance racing.
Running on Empty: The Risks of Low Fuel
You may want to see also
Sensor Input: Engine sensors provide data on speed, load, and temperature to adjust fuel
In the high-performance world of sprint cars, fuel injection systems play a critical role in optimizing power and efficiency. At the heart of this process is a sophisticated network of sensors that provide real-time data to the engine's computer. These sensors are strategically placed throughout the engine bay and are designed to measure various parameters, ensuring the engine operates at its peak performance.
One of the primary sensors is the speed sensor, which monitors the engine's rotational speed. This sensor provides critical information about the engine's RPM (revolutions per minute), allowing the fuel injection system to calculate the precise fuel-air mixture required for optimal combustion. By adjusting the fuel injection timing based on speed, the system ensures that the engine receives the right amount of fuel at different operating conditions, maximizing power output while maintaining efficiency.
Additionally, load sensors are employed to measure the engine's load or the amount of power being demanded. These sensors provide feedback on factors such as throttle position and pedal pressure, indicating how much power the driver is requesting from the engine. With this data, the fuel injection system can make fine-tuned adjustments to the fuel-air mixture, ensuring that the engine delivers the required power output while maintaining stability and responsiveness.
Temperature sensors are another crucial component of this system. They monitor the engine's temperature, including intake and exhaust temperatures, as well as the ambient air temperature. By providing temperature data, these sensors enable the fuel injection system to compensate for changes in air density and engine heat. This compensation is vital for accurate fuel calculation, especially during high-speed or high-load conditions, where temperature variations can significantly impact engine performance.
The engine's computer processes the data from these sensors and uses it to calculate the ideal fuel-air mixture. It adjusts the fuel injection accordingly, ensuring that the engine receives the precise amount of fuel required for efficient combustion at any given speed, load, and temperature. This real-time feedback loop allows for rapid adjustments, optimizing performance and responsiveness, which are essential characteristics of sprint car racing.
Fuel Efficiency Standards: The Hidden Cost of Greener Cars
You may want to see also
Fuel Atomization: Injectors spray fuel into the intake manifold as a fine mist
The process of fuel atomization is a critical aspect of fuel injection systems in sprint cars, ensuring that the fuel is broken down into extremely small droplets for optimal combustion. When the injectors spray fuel into the intake manifold, they create a fine mist, which is a result of precise engineering and careful design. This mist-like fuel dispersion is essential for several reasons. Firstly, it increases the surface area of the fuel, allowing for more efficient mixing with the air-fuel mixture. This is crucial for complete combustion, as it ensures that the fuel vaporizes quickly and thoroughly, providing the necessary energy for the engine to operate efficiently.
The atomization process is achieved through the use of specialized injectors that are designed to create a high-pressure spray. These injectors are positioned strategically within the intake manifold, ensuring that the fuel is sprayed directly into the air stream. The high-pressure spray breaks the fuel into tiny droplets, which are then carried by the airflow into the combustion chamber. This fine mist of fuel is critical for achieving the correct air-fuel ratio, which is essential for optimal engine performance and power output.
The design of the injectors plays a significant role in this process. They are typically made with precision nozzles that control the fuel's exit velocity and the droplet size. By adjusting the nozzle's orifice size and shape, engineers can fine-tune the atomization process. Smaller droplets mean better atomization, as they have a larger surface area, allowing for more efficient mixing with the surrounding air. This results in a more homogeneous air-fuel mixture, which is crucial for maintaining consistent engine performance during high-speed racing.
Furthermore, the timing of the fuel injection is critical. The injectors must spray the fuel at the precise moment when the intake valves are open, allowing the air-fuel mixture to enter the combustion chamber. This timing ensures that the fuel is atomized and mixed with the incoming air, creating a powerful and efficient combustion event. The coordination between the fuel injection timing, engine speed, and load conditions is a complex task, requiring sophisticated engine control units to manage the process effectively.
In summary, fuel atomization is a key component of sprint car fuel injection systems, where injectors spray fuel as a fine mist into the intake manifold. This process increases the fuel's surface area, allowing for efficient mixing with air, and ensures complete combustion. The design and precision of the injectors, along with careful timing, contribute to achieving the optimal air-fuel ratio, resulting in powerful engine performance on the race track.
Turbocharged Engine Maintenance: Fuel System Cleaner Compatibility
You may want to see also
Timing Control: Injection timing is precise, synchronized with engine cycles for optimal performance
The precision of timing control in fuel injection systems is a critical aspect of optimizing performance in sprint cars. This system ensures that fuel is injected into the engine's cylinders at the exact moment when the engine's internal components are most capable of utilizing it. This timing is crucial because it directly impacts the engine's power output and efficiency. When the fuel is injected too early or too late, it can lead to a loss of power and potential engine damage.
In a sprint car, the engine operates at extremely high RPMs, often exceeding 9,000 revolutions per minute (RPM). At these speeds, the engine requires a highly responsive fuel injection system to maintain optimal performance. The timing control system ensures that the fuel is injected precisely when the engine's pistons are at the top of their stroke, creating the ideal conditions for combustion. This synchronization maximizes the power output and ensures that the engine operates efficiently, even under extreme conditions.
The timing control mechanism typically involves a series of sensors and actuators. Engine speed and position sensors provide real-time data to the engine control unit (ECU). The ECU then calculates the optimal injection timing based on this data. When the engine's RPM increases, the ECU adjusts the timing to ensure that the fuel is injected at the correct moment. This dynamic adjustment allows the engine to maintain its power output across a wide range of speeds.
Additionally, the timing control system can be further refined with advanced technologies. For instance, some fuel injection systems use camshaft position sensors to provide even more precise timing information. This allows the ECU to make minute adjustments to the injection timing, ensuring that the fuel is delivered with millisecond-level accuracy. Such precision is essential for maximizing performance and maintaining control over the engine's operation.
In summary, timing control is a critical feature of fuel injection systems in sprint cars. It ensures that fuel is injected precisely, synchronized with the engine's cycles, to achieve optimal performance. This level of precision is made possible through a combination of sensors, actuators, and advanced control algorithms, all working together to provide the engine with the perfect fuel-air mixture at the right moment.
Navigating the Road: When Your Fuel Gauge Acts Up
You may want to see also
EPC Management: Engine Control Unit (ECU) uses data to calculate and control fuel injection
The Engine Control Unit (ECU) is the brain of a sprint car's fuel injection system, playing a crucial role in optimizing performance and ensuring efficient fuel usage. This sophisticated unit processes a vast amount of data from various sensors and systems within the engine, making real-time calculations to precisely control fuel injection. By doing so, it aims to achieve the ideal air-fuel mixture for combustion, maximizing power output while maintaining optimal engine operation.
At the heart of this process is the ECU's ability to interpret data from sensors such as the mass airflow (MAF) sensor, manifold absolute pressure (MAP) sensor, and oxygen sensors. The MAF sensor measures the volume of air entering the engine, while the MAP sensor provides information about the engine's intake manifold pressure. These sensors feed critical data to the ECU, allowing it to make informed decisions about fuel injection.
The ECU's calculations are based on a complex algorithm that considers factors like engine speed, load, temperature, and the desired air-fuel ratio. It uses this data to determine the exact amount of fuel required for efficient combustion at any given moment. For instance, during high-load conditions, the ECU might inject more fuel to meet the increased power demand while still maintaining optimal performance.
One of the key advantages of this system is its ability to adapt to varying driving conditions. The ECU continuously monitors the engine's performance and adjusts the fuel injection accordingly. For example, when the driver rapidly accelerates, the ECU increases the fuel injection rate to provide the necessary power surge. Conversely, during steady cruising, it reduces the fuel injection to optimize fuel efficiency.
In summary, the ECU's role in fuel injection management is vital for sprint car performance. By processing sensor data and making real-time calculations, it ensures that the engine receives the precise amount of fuel required for efficient combustion. This level of control allows for optimal power delivery, improved fuel economy, and enhanced overall engine performance, making it a critical component in the world of high-performance racing.
Unleashing the Power: Does Your Car Burn Fossil Fuels?
You may want to see also
Frequently asked questions
Fuel injection in sprint cars is a sophisticated system designed to optimize fuel delivery to the engine, ensuring efficient combustion and maximum power output. It replaces the traditional carburetor, which can be less precise in mixing air and fuel, especially at high speeds and RPMs.
The fuel injection system in sprint cars operates by precisely metering and injecting fuel into the engine's cylinders based on real-time engine data. This is achieved through a combination of sensors, an electronic control unit (ECU), and injectors. The ECU processes data from sensors like the mass airflow meter, manifold absolute pressure sensor, and engine speed sensor to calculate the optimal fuel-air mixture. It then activates the injectors to spray the precise amount of fuel required for efficient combustion.
Fuel injection offers several advantages over traditional carburetors in sprint cars. Firstly, it provides better performance consistency by delivering a precise fuel-air mixture, ensuring optimal power output across a wide RPM range. This results in improved throttle response and acceleration. Secondly, fuel injection allows for more efficient fuel usage, as the system can adjust the fuel-air mixture based on engine load, reducing fuel consumption and potential emissions. Additionally, the system's ability to adapt to varying conditions, such as altitude or temperature changes, ensures that the engine performs optimally in different racing environments.