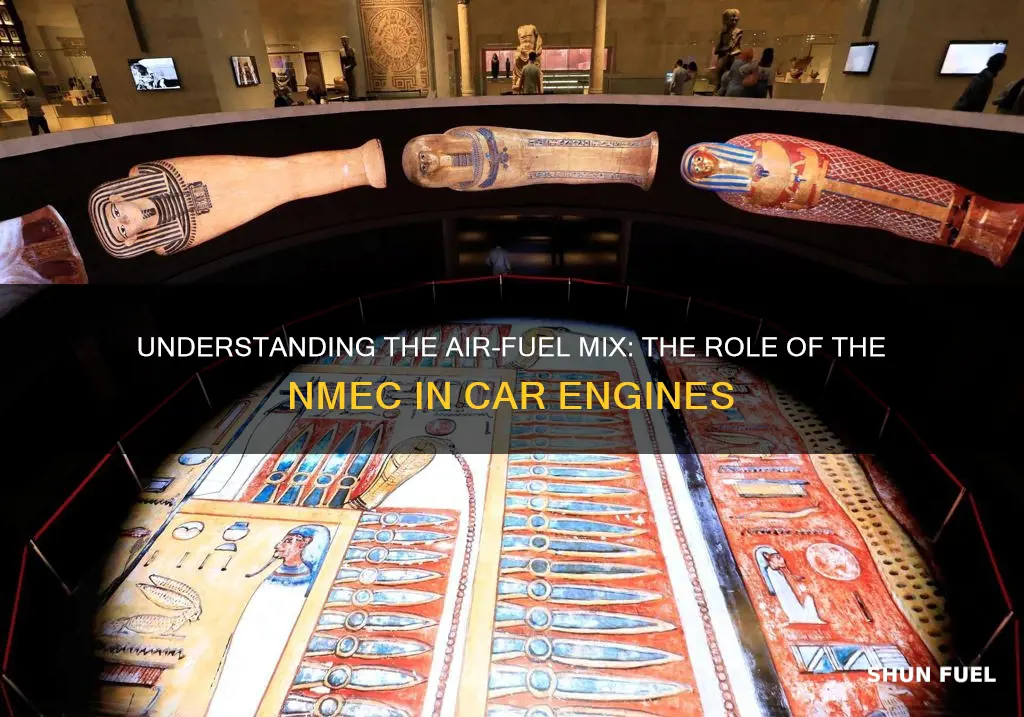
In the world of automotive engineering, understanding the intricate mechanisms that power our vehicles is crucial. One such system, the Negative-Displacement Mechanical Engine Control (NMECh) system, plays a vital role in delivering air to the fuel bowl, a critical component in the combustion process. This paragraph aims to delve into the fascinating process of how NMECh cars facilitate the flow of air to the fuel bowl, ensuring optimal engine performance and efficiency.
What You'll Learn
- Engine Design: The engine's layout and components facilitate air intake and fuel delivery
- Air Intake System: Filters and ducts direct air to the engine's combustion chamber
- Fuel Injection: Precision in fuel injection ensures optimal air-fuel mixture for combustion
- Vacuum System: A vacuum pump creates a low-pressure environment to draw fuel into the bowl
- Fuel Bowl Structure: The bowl's design and placement optimize fuel distribution and combustion
Engine Design: The engine's layout and components facilitate air intake and fuel delivery
The engine design of an Nmec (Natural Mechanical Engine Conversion) vehicle plays a crucial role in ensuring efficient air intake and fuel delivery to the engine's combustion chamber. This intricate process begins with the engine's layout, which is carefully designed to optimize airflow. The engine block, typically positioned at the front of the vehicle, houses the cylinders and various components that work in harmony to facilitate the combustion process.
One key component is the air intake system, which is responsible for drawing air into the engine. This system often consists of an air filter, intake manifold, and throttle body. The air filter captures dust and debris, ensuring clean air enters the engine. The intake manifold, a network of passages, distributes the air evenly to each cylinder. Throttle body, a crucial element, regulates the air-fuel mixture by controlling the amount of air entering the engine based on the driver's input.
The fuel system is another critical aspect of engine design. It delivers the precise amount of fuel required for combustion. In an Nmec setup, the fuel bowl, also known as the carburetor, is a central component. It mixes air and fuel, creating a combustible mixture. The carburetor's design and positioning are essential to ensure an even distribution of the air-fuel mixture across all cylinders. This process is further enhanced by the engine's layout, which often includes a series of passages and channels to guide the mixture efficiently.
Engineers also consider the engine's cylinder arrangement and head design. The layout of cylinders can impact airflow and fuel injection. For instance, a V-shaped engine configuration provides better access to the front and rear cylinders, allowing for efficient air intake and fuel distribution. Additionally, the engine head, which houses the valves and spark plugs, is designed to optimize combustion by controlling the air-fuel mixture's entry into the cylinders.
Furthermore, the engine's layout may incorporate features like a supercharger or turbocharger to increase power output. These forced induction systems compress the air-fuel mixture, allowing for more efficient combustion. The design of these components requires precise engineering to ensure optimal performance and reliability. In summary, the engine design of an Nmec vehicle is a complex process that involves careful consideration of airflow, fuel delivery, and component placement to ensure the engine operates efficiently and effectively.
Hydrogen Fuel Cell Cars: Explosive Truths or Myths?
You may want to see also
Air Intake System: Filters and ducts direct air to the engine's combustion chamber
The air intake system plays a crucial role in the engine's performance, ensuring a steady supply of fresh air to the combustion chamber. This system is designed to optimize the engine's breathing, allowing for efficient fuel-air mixture creation. Here's a breakdown of how it works:
Air Intake System Components:
The air intake system consists of several key components. Firstly, the air filter, often made of a fine mesh or paper material, is designed to trap dirt, dust, and other contaminants from the incoming air. This filter is crucial to protect the engine from potential damage caused by foreign particles. Secondly, the air duct or intake manifold directs the filtered air to the engine's combustion chamber. It is typically a metal or plastic tube that ensures a smooth and controlled airflow.
Air Filtration:
As air enters the engine bay, it passes through the air filter. This filter is strategically positioned to capture any debris, pollen, or other small particles that could negatively impact engine performance. By removing these impurities, the filter ensures that only clean, high-quality air reaches the engine. This process is vital for maintaining optimal engine operation and longevity.
Air Ducting and Manifold:
The air ducts or intake manifold are responsible for guiding the air to the engine's cylinders. These ducts are carefully designed to provide a smooth and controlled airflow, ensuring that the air enters the combustion chamber at the right pressure and velocity. The manifold, often a cast aluminum component, distributes the air evenly to multiple cylinders, promoting efficient combustion. This design allows for a precise and consistent fuel-air mixture, which is essential for optimal power output and fuel efficiency.
Engine Performance and Efficiency:
An efficient air intake system directly contributes to the engine's performance. By providing a constant supply of clean air, it enables the engine to produce more power and improve fuel efficiency. The system's design ensures that the engine receives the necessary oxygen for complete combustion, resulting in reduced emissions and improved overall engine health. Additionally, proper air intake management can enhance throttle response and acceleration, making the vehicle more responsive and enjoyable to drive.
Does Better Fuel Mean Better Engine Efficiency?
You may want to see also
Fuel Injection: Precision in fuel injection ensures optimal air-fuel mixture for combustion
Fuel injection is a critical component in modern engines, especially those with electronic fuel injection (EFI) systems, which are commonly found in vehicles like the Nmec. This system ensures precise control over the fuel-air mixture, leading to efficient combustion and improved engine performance. The process begins with the fuel pump, which delivers fuel at a regulated pressure to the fuel rail or injectors. This pressure is carefully calibrated to match the engine's requirements, ensuring that the fuel is atomized into a fine mist for optimal mixing with air.
The precision of fuel injection lies in its ability to meter and deliver the exact amount of fuel required for each cylinder. This is achieved through a sophisticated electronic control unit (ECU) that monitors various engine parameters, such as speed, load, and temperature. The ECU calculates the ideal air-fuel ratio, which is crucial for efficient combustion and power output. By adjusting the fuel injection timing and amount, the system can create a leaner or richer mixture, optimizing performance and fuel efficiency.
In the context of an Nmec car, the air-fuel mixture is directed to the engine's combustion chambers through the intake valves. The precision of fuel injection ensures that the air and fuel are mixed in the correct proportions, creating a homogeneous mixture. This mixture is then ignited by the spark plugs, resulting in a controlled and efficient combustion process. The timing and quantity of fuel injection are critical, as they directly impact the engine's performance, power, and fuel economy.
One of the key advantages of fuel injection is its ability to adapt to varying driving conditions. The ECU continuously adjusts the fuel-air mixture based on real-time data, ensuring that the engine operates optimally regardless of speed, load, or altitude. This dynamic control allows for better throttle response, improved acceleration, and reduced emissions. Additionally, fuel injection systems can provide a more consistent power output, making the engine more reliable and responsive.
The precision of fuel injection technology has revolutionized engine performance and efficiency. It enables engines to produce more power while consuming less fuel, contributing to better fuel economy and reduced environmental impact. Furthermore, the system's ability to fine-tune the air-fuel mixture allows for better control over emissions, ensuring that the vehicle meets strict environmental regulations. This level of precision in fuel injection is a testament to the advancements in automotive engineering, providing drivers with a more efficient and responsive driving experience.
Boost Your Car's Fuel Efficiency: Tips and Tricks
You may want to see also
Vacuum System: A vacuum pump creates a low-pressure environment to draw fuel into the bowl
The vacuum system in an N-series ME (NME) engine is a crucial component that ensures efficient fuel delivery to the engine's air-fuel bowls. This system utilizes a vacuum pump to create a low-pressure environment, which is essential for drawing fuel into the bowls and mixing it with air for combustion. Here's a detailed explanation of how this process works:
When the engine is running, the vacuum pump, often driven by a belt connected to the engine's crankshaft, begins to operate. This pump creates a partial vacuum, which is a region of low pressure compared to the atmospheric pressure outside the engine. The pump's role is to extract air from the engine's intake manifold and create a suction effect. As the pump operates, it generates a low-pressure area in the intake manifold, which is connected to the fuel bowl via a series of passages and passages.
The fuel bowl, also known as the carburetor, is designed to hold a precise amount of fuel, which is then atomized and mixed with air for combustion. The vacuum created by the pump pulls fuel from the fuel tank through a fuel line and into the bowl. This process is similar to how a household vacuum cleaner works, where the low pressure at the intake creates suction, drawing in the desired substance. In this case, the fuel is drawn into the bowl due to the pressure difference between the low-pressure area created by the pump and the higher pressure in the fuel tank.
Once the fuel enters the bowl, it is mixed with air supplied by the intake manifold. The vacuum system ensures that the fuel and air are properly combined in the correct ratio, which is critical for optimal engine performance. The atomization of fuel droplets is facilitated by the air flow, creating a fine mist that can be easily ignited in the engine's cylinders.
The vacuum pump's efficiency is vital to the engine's overall performance. It ensures that the fuel bowl receives a steady supply of fuel, maintaining the engine's power output and responsiveness. Additionally, the vacuum system helps to prevent fuel starvation by ensuring that the fuel bowl never runs completely dry, even during high-load conditions. This is achieved by the pump's ability to maintain a consistent low-pressure environment, allowing for efficient fuel delivery.
Flex Fuel Cars: Mileage Boost or Just a Myth?
You may want to see also
Fuel Bowl Structure: The bowl's design and placement optimize fuel distribution and combustion
The fuel bowl structure is a critical component in the fuel injection system of an N-series NEC (New Engine Concept) car, designed to ensure efficient and precise fuel distribution to the engine's cylinders. This system is a key innovation in modern engine technology, optimizing combustion and performance. The fuel bowl's design and placement are carefully engineered to achieve optimal fuel distribution, which is essential for the engine's overall efficiency and power output.
The fuel bowl is typically located in close proximity to the engine's intake manifold, often integrated into the manifold itself. This strategic placement allows for a direct and efficient path for fuel to travel from the bowl to the engine's cylinders. The design of the bowl often features a series of intricate passages and channels that guide the fuel, ensuring an even and consistent distribution. These passages are meticulously engineered to control the flow rate and pressure of the fuel, allowing for precise control over the fuel-air mixture.
One of the key design considerations is the use of a fuel bowl with a unique shape and surface texture. The bowl's interior often features a series of raised ridges or dimples that help to atomize the fuel as it exits the bowl. This atomization process ensures that the fuel is broken down into tiny droplets, which then mix thoroughly with the incoming air. The result is a more efficient combustion process, as the finely dispersed fuel droplets ignite more readily, leading to improved power and performance.
Additionally, the fuel bowl's structure may include a fuel level sensor, which is crucial for monitoring the fuel level and ensuring the engine operates within the optimal range. This sensor provides feedback to the engine control unit (ECU), allowing it to adjust the fuel injection timing and quantity accordingly. By incorporating this sensor, the system can maintain the correct fuel level, preventing engine starvation or excessive fuel consumption.
In summary, the fuel bowl structure in an N-series NEC car is a sophisticated design that optimizes fuel distribution and combustion. Its placement near the intake manifold and intricate internal passages ensure efficient fuel delivery. The unique shape and surface features of the bowl promote fuel atomization, leading to improved combustion. Furthermore, the inclusion of a fuel level sensor enhances the engine's ability to maintain optimal performance by precisely managing the fuel-air mixture. This intricate design showcases the engineering prowess behind modern engine technology.
Uncovering the Fuel Cost: Does Starting a Car Burn More Gas?
You may want to see also
Frequently asked questions
In a NEMA car, the air-fuel mixture is typically delivered to the engine through a system called the intake manifold. This manifold is designed to evenly distribute the mixture to each cylinder, ensuring optimal combustion.
The fuel bowl, also known as the carburetor, is a crucial component. It mixes the fuel with air, creating the desired air-fuel ratio. The bowl then channels this mixture through a series of passages and into the intake manifold.
NEMA engines often use a throttle body or a carburetor with a float bowl design to regulate the air-fuel ratio. The throttle body controls the amount of air entering the engine, while the carburetor adjusts the fuel injection to maintain the optimal ratio.
Absolutely! The air filter is essential for cleaning the air before it enters the engine. It traps dust, dirt, and other contaminants, ensuring that only clean air reaches the fuel bowl and the rest of the engine, thus improving performance and longevity.
An improper air-fuel mixture can lead to poor engine performance, reduced power, and even engine damage. If the mixture is too rich (more fuel than air), it can cause misfires and carbon buildup. Conversely, a lean mixture (more air than fuel) may result in inefficient combustion and potential engine knocking.