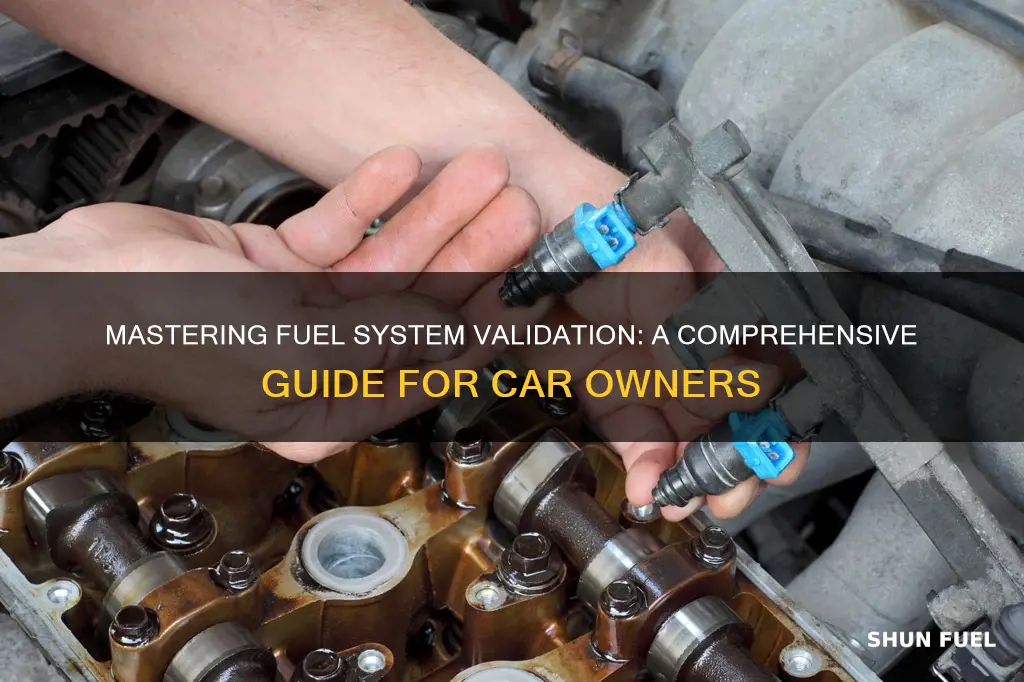
Validating the fuel system in cars is a critical process that ensures the vehicle's performance, safety, and efficiency. It involves a series of tests and inspections to verify that the fuel system, including the fuel tank, lines, pumps, and injectors, is functioning correctly. This validation process helps identify and rectify any issues such as leaks, blockages, or component failures, ensuring that the fuel is delivered efficiently to the engine and that the vehicle operates optimally. By conducting thorough fuel system validation, mechanics and engineers can maintain the integrity of the vehicle's fuel supply, enhance its overall performance, and prevent potential problems that may arise from faulty fuel system components.
What You'll Learn
- Fuel Pump Testing: Check fuel pump's flow rate and pressure to ensure proper fuel delivery
- Fuel Filter Inspection: Examine for clogs or debris to maintain clean fuel flow
- Fuel Injector Calibration: Verify injector spray patterns and timing for optimal performance
- Pressure Regulation: Measure fuel pressure to ensure it meets manufacturer specifications
- Leak Detection: Inspect for fuel leaks at connections and hoses to prevent contamination
Fuel Pump Testing: Check fuel pump's flow rate and pressure to ensure proper fuel delivery
Fuel pump testing is a critical step in the validation process of a car's fuel system, ensuring that the engine receives the correct amount of fuel at the right pressure for optimal performance and longevity. This process involves checking the flow rate and pressure of the fuel pump to guarantee that it delivers fuel efficiently and effectively. Here's a detailed guide on how to perform this test:
When conducting fuel pump testing, the primary goal is to measure the pump's ability to deliver fuel under various conditions. Start by ensuring the vehicle is parked on a level surface and the engine is off. Locate the fuel pump, which is typically positioned near the fuel tank, and prepare the necessary tools, including a fuel pressure gauge and a flow meter. It is essential to have a basic understanding of the vehicle's fuel system layout to access the pump correctly.
The first step in the test is to measure the fuel pressure. Connect the fuel pressure gauge to the fuel pump's outlet port, ensuring a secure connection. Start the engine and allow it to idle for a few minutes to reach operating temperature. During this time, the fuel pump should be actively circulating fuel. Read the pressure gauge and record the value. The expected pressure can vary depending on the vehicle's make and model, but generally, it should fall within a specified range recommended by the manufacturer. If the pressure is too low, it may indicate a faulty pump or restricted fuel lines.
Next, measure the fuel flow rate. This test requires the use of a flow meter, which can be connected to the fuel pump's outlet. Start the engine and allow it to idle again. Measure the volume of fuel flowing through the system over a set period, typically one minute. The flow rate should be consistent and within the acceptable limits for the vehicle. A lower-than-expected flow rate could suggest a clogged filter, a faulty pump, or issues with the fuel injectors.
Additionally, it is beneficial to test the fuel pump's performance under different loads. This can be achieved by applying a load to the engine, such as using a dynamometer or simulating high-load conditions. During this test, measure the fuel pressure and flow rate again to ensure the pump can handle increased demand. The pump should maintain stable pressure and flow, providing sufficient fuel to the engine even under stressful conditions.
In summary, fuel pump testing is a comprehensive process that involves measuring pressure and flow rate to validate the pump's functionality. By following these steps, mechanics and car enthusiasts can ensure that the fuel system is delivering fuel efficiently, promoting optimal engine performance and reliability. Regular maintenance and testing of the fuel pump can help prevent issues related to fuel delivery, ultimately saving time and money in the long run.
Powering the Future: Unlocking Hydrogen Fuel Cell Car Secrets
You may want to see also
Fuel Filter Inspection: Examine for clogs or debris to maintain clean fuel flow
A crucial aspect of maintaining a car's fuel system is ensuring that the fuel filter is in good condition. Over time, dirt, dust, and other contaminants can accumulate in the fuel filter, leading to potential issues with fuel flow and engine performance. Regular inspection and maintenance of the fuel filter are essential to prevent these problems.
To inspect the fuel filter, start by locating it, which is typically found under the car's hood, often near the engine. The filter is usually a cylindrical component with a mounting bracket holding it in place. Carefully remove the filter by unscrewing or unclipping the mounting bracket, taking note of the orientation to ensure proper reinstallation.
Once the filter is removed, examine it for any signs of clogging or debris accumulation. A clogged fuel filter will appear dirty or discolored, often with a buildup of fine particles or a greasy residue. If the filter is heavily clogged, it may be necessary to replace it immediately to prevent further contamination of the fuel system.
For a quick assessment, you can also check the fuel line connected to the filter for any visible signs of contamination. If the fuel line is clean and free of debris, it indicates that the filter is likely functioning correctly. However, if you notice any dirt or contamination in the fuel line, it suggests that the filter may need attention or replacement.
In addition to visual inspection, you can also use a fuel filter pressure tester to check for proper fuel flow. This tool measures the pressure drop across the filter, indicating its efficiency. A significant pressure drop suggests a clogged or restricted filter, requiring further investigation or replacement. Regularly inspecting and maintaining the fuel filter is vital to ensure optimal engine performance and longevity.
Electric Motors: Cheaper Than Gasoline? Unveiling the Cost Comparison
You may want to see also
Fuel Injector Calibration: Verify injector spray patterns and timing for optimal performance
Fuel injector calibration is a critical process in ensuring that your vehicle's fuel system operates efficiently and delivers the correct amount of fuel to the engine at the right time. This process involves verifying the spray patterns and timing of fuel injectors to optimize engine performance and maintain fuel economy. Here's a detailed guide on how to perform this calibration:
Understanding the Process:
Fuel injectors are responsible for spraying a precise amount of fuel into the engine's intake manifold or directly into the cylinders. The timing and pattern of this spray are crucial for efficient combustion. Calibration ensures that the injectors deliver the right fuel-air mixture, promoting optimal power output and engine health. This process is especially important in modern vehicles with electronic fuel injection systems, where the engine control unit (ECU) makes real-time adjustments to fuel delivery.
Tools and Equipment:
To perform fuel injector calibration, you'll need a few essential tools. Firstly, a fuel pressure gauge is essential to measure the pressure of the fuel being delivered to the injectors. This gauge will help you identify any pressure drops or inconsistencies. Additionally, a fuel flow meter can be used to measure the volume of fuel being injected, ensuring it aligns with the engine's requirements. A spray pattern tester or a high-speed camera can be employed to visually inspect the injector's spray pattern, allowing you to identify any deviations from the ideal spray shape.
Step-by-Step Calibration:
- Fuel Pressure Check: Start by checking the fuel pressure at idle and under various engine loads. Compare the readings with the manufacturer's specifications. Any significant deviations may indicate a problem with the fuel pump or pressure regulator.
- Injector Spray Pattern Inspection: Use the spray pattern tester or high-speed camera to examine the fuel spray. The ideal spray pattern should be consistent, with a uniform distribution of fuel droplets. Look for any clumping, missing droplets, or uneven distribution, as these issues can affect engine performance. Adjust the injector's position or flow rate if necessary to achieve the desired spray pattern.
- Timing Verification: Ensure that the fuel injectors are firing at the correct timing. This timing is often controlled by the ECU, which adjusts it based on engine speed and load. You can use an oscilloscope or a specialized tool to monitor the injector's firing signals and verify that they align with the engine's requirements. Adjust the timing if needed to optimize power and fuel efficiency.
- Flow Rate Testing: Measure the fuel flow rate through each injector to confirm it meets the engine's specifications. This can be done using the fuel flow meter. Any discrepancies may indicate a faulty injector or a problem with the fuel delivery system.
Troubleshooting and Adjustments:
If any issues are identified during the calibration process, troubleshooting steps should be taken. This may include cleaning or replacing clogged injectors, adjusting the fuel pressure, or recalibrating the ECU. Fine-tuning the injector's spray pattern and timing can significantly improve engine performance and fuel consumption.
By following these steps, you can ensure that your vehicle's fuel injectors are calibrated correctly, resulting in optimal engine performance, improved fuel efficiency, and reduced emissions. Regular calibration checks are essential to maintain the longevity and reliability of your car's fuel system.
Fuel Filters: Do New Cars Still Need Them?
You may want to see also
Pressure Regulation: Measure fuel pressure to ensure it meets manufacturer specifications
Pressure regulation is a critical aspect of fuel system validation in automobiles, as it ensures that the fuel pressure delivered to the engine meets the precise requirements specified by the manufacturer. This process involves measuring the fuel pressure at various points within the system to verify its accuracy and performance. Here's a detailed guide on how to approach pressure regulation for fuel system validation:
Fuel Pressure Measurement: Begin by identifying the specific fuel pressure that the manufacturer recommends for your vehicle's engine. This value is typically found in the vehicle's service manual or can be obtained from the manufacturer's website. You will need a fuel pressure gauge, which is a specialized tool designed to measure the pressure of fuel in a system. Connect the gauge to the fuel rail or the fuel pump outlet, ensuring a secure and leak-free connection. Start the engine and allow it to idle, then read the fuel pressure value displayed on the gauge.
Comparison with Specifications: Compare the measured fuel pressure with the manufacturer's specified value. If the measured pressure is significantly lower or higher than the recommended range, it indicates a potential issue with the fuel system. For instance, low fuel pressure might suggest a problem with the fuel pump or delivery system, while high pressure could be due to a restricted fuel line or pump malfunction.
Testing at Different Engine Speeds: Fuel pressure requirements can vary with engine speed and load. Therefore, it is essential to measure pressure under different operating conditions. Accelerate the engine to higher RPMs and observe the fuel pressure changes. A well-functioning fuel system should maintain the required pressure across various engine speeds and loads. If the pressure drops significantly during acceleration, it may indicate a problem with the fuel pump's ability to handle increased demand.
Checking for Leaks and Restrictions: While measuring pressure, also inspect the fuel system for any visible leaks or restrictions. Even a small leak can lead to a pressure drop, affecting engine performance. Check all fuel lines, connections, and components for any signs of damage or contamination. Ensure that the fuel tank and lines are properly sealed to prevent vaporization and potential engine misfires.
Adjustments and Calibrations: If the measured fuel pressure deviates from the manufacturer's specifications, adjustments or calibrations may be necessary. This could involve modifying the fuel pump settings, replacing faulty components, or recalibrating the engine control unit (ECU) to optimize fuel pressure. It is crucial to follow the manufacturer's guidelines and recommendations during these adjustments to ensure the system's reliability and performance.
Electric Car Charging: The Fossil Fuel Connection
You may want to see also
Leak Detection: Inspect for fuel leaks at connections and hoses to prevent contamination
Leak detection is a critical step in the process of validating a car's fuel system, as it helps identify potential issues that could lead to contamination and performance problems. When inspecting for fuel leaks, it's essential to pay close attention to the connections and hoses, as these are common areas where leaks can occur. Start by examining the fuel tank and its connections to the engine. Look for any signs of corrosion or damage around the fuel lines and fittings. Over time, fuel lines can deteriorate due to heat, vibration, or chemical exposure, leading to cracks or weakened seals. Inspect the lines for any visible damage, such as splits, punctures, or kinks. If you notice any issues, it's crucial to replace the affected lines immediately to prevent fuel from escaping.
Next, focus on the fuel pump and its connections. The fuel pump is responsible for delivering fuel from the tank to the engine, and any malfunction can result in reduced performance or even engine failure. Check the pump's electrical connections to ensure they are clean and securely attached. Corroded or loose connections can cause fuel delivery issues. Additionally, inspect the fuel pump module, as it houses the pump and related components. Look for any signs of moisture or corrosion inside the module, as these can lead to short circuits or pump failure.
Hoses play a vital role in the fuel system, and their integrity is essential to prevent leaks. Inspect all fuel hoses for cracks, brittleness, or signs of deterioration. Hoses can crack or become brittle due to age, heat, or chemical exposure. Pay attention to areas where hoses connect to the fuel tank, fuel pump, and engine. Ensure that all connections are tight and secure. Over time, hoses can develop small holes or leaks, allowing fuel to escape. If you find any damaged hoses, they should be replaced to maintain a safe and efficient fuel system.
When inspecting for leaks, it's also important to use the right tools and techniques. One common method is to use a fuel pressure gauge to measure the pressure in the system. Low fuel pressure can indicate a leak or restriction in the fuel lines. Additionally, you can use a fuel leak detector, which is a specialized tool that releases a small amount of vapor into the fuel system. If a leak is present, the vapor will condense, indicating the location of the leak. This method is particularly useful for hard-to-reach areas.
In summary, leak detection is a crucial aspect of validating a car's fuel system. By carefully inspecting connections, hoses, and fuel components, you can identify potential leaks and prevent contamination. Regular maintenance and timely repairs are essential to ensure the fuel system operates efficiently and safely. Remember, any signs of fuel leaks should be addressed promptly to avoid performance issues and potential engine damage.
Maximizing Mileage: Can You Increase Your Car's Fuel Capacity?
You may want to see also
Frequently asked questions
Fuel system validation is a critical process in the automotive industry to ensure that the fuel delivery and injection systems in a vehicle function correctly and efficiently. It helps identify and rectify any issues related to fuel flow, pressure, and atomization, which are essential for optimal engine performance, fuel economy, and emissions control.
Validation is often carried out through a series of tests and inspections. This includes checking fuel pressure using specialized tools, inspecting fuel injectors for proper operation and spray patterns, and verifying the functionality of fuel pumps and return lines. Technicians may also use diagnostic equipment to read error codes and monitor fuel system parameters during engine operation.
This process can uncover various problems, such as clogged fuel filters, faulty fuel pumps, leaking fuel lines, or malfunctioning fuel injectors. It can also detect issues with the engine's electronic control unit (ECU) related to fuel management, ensuring that the engine receives the correct amount of fuel at the right time.
While professional technicians use specialized equipment, car owners can perform some basic checks. These include listening for unusual noises from the fuel pump, checking for leaks around fuel lines and connections, and using a fuel pressure gauge to measure pressure at the fuel rail. However, for comprehensive validation, it is recommended to consult a professional mechanic.