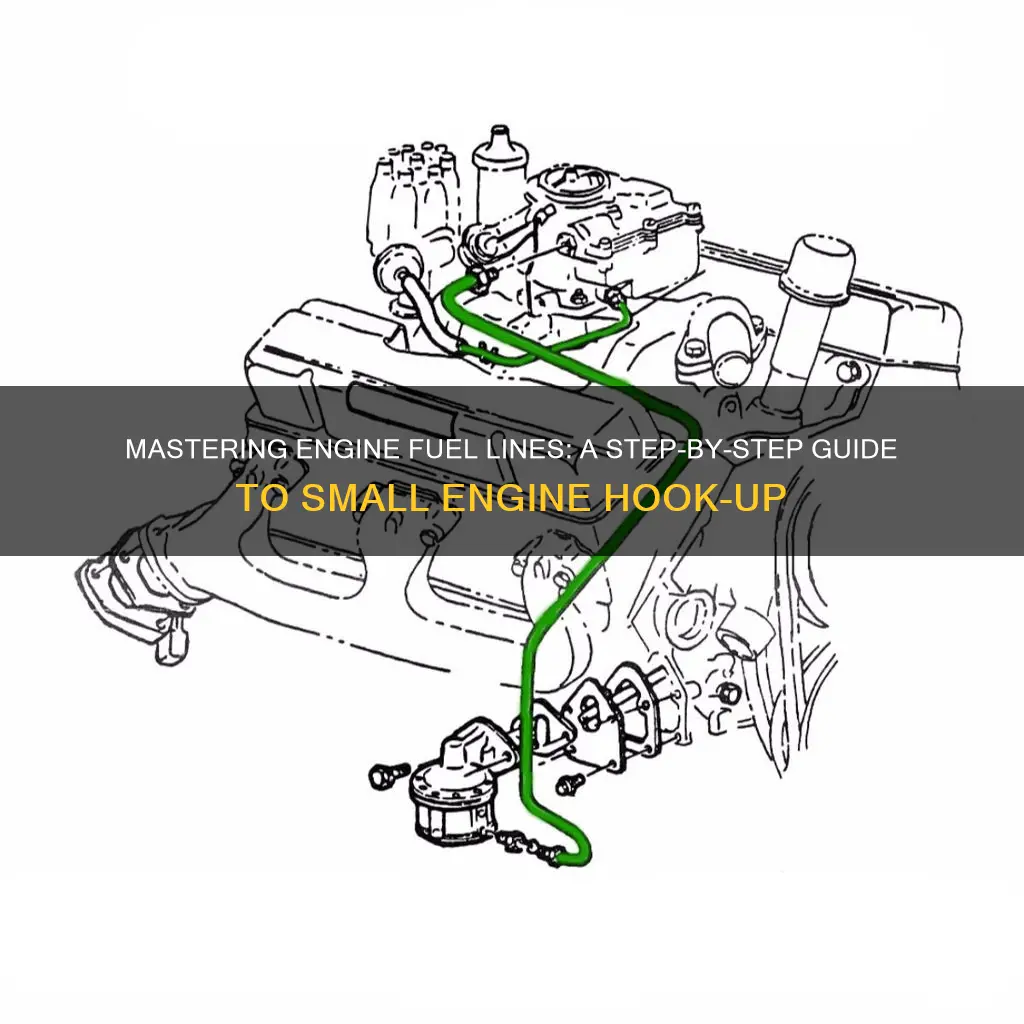
Hooking up the fuel lines for a small engine can seem daunting, but with a few simple steps, you can have it done efficiently. This guide will walk you through the process, ensuring you understand the importance of proper connections and how to avoid common pitfalls. Whether you're a seasoned mechanic or a DIY enthusiast, knowing how to connect fuel lines correctly is essential for a smooth-running engine. Let's dive into the details and make your engine purr with confidence!
What You'll Learn
- Fuel Tank Connection: Attach fuel line to tank, ensuring a secure, leak-free fit
- Fuel Filter Installation: Place filter in line, filtering fuel for engine
- carburetor Link: Connect fuel line to carburetor, ensuring proper fuel-air mixture
- Engine Mounting: Secure fuel lines to engine, using clamps or brackets
- Testing and Adjustments: Check for leaks, ensure proper fuel flow, and make necessary adjustments
Fuel Tank Connection: Attach fuel line to tank, ensuring a secure, leak-free fit
When connecting the fuel line to the tank, it's crucial to ensure a tight and leak-free seal. Start by identifying the fuel tank's inlet port, which is typically a small opening on the side or bottom of the tank. Locate the fuel line, which is usually a flexible hose with a quick-connect fitting or a threaded adapter at one end. The other end of the fuel line should be connected to the engine's fuel system.
Begin the connection process by aligning the fuel line with the tank's inlet port. Ensure that the fuel line is positioned correctly, with the quick-connect fitting or adapter facing the appropriate direction. Most fuel tanks have a specific orientation, so pay attention to this detail. Insert the fuel line into the port, pushing it firmly until it is fully seated. You should feel a distinct click or hear a small snap, indicating a secure connection.
For an even more secure fit, consider using a fuel line clamp. These clamps are designed to provide an additional layer of protection against leaks. Wrap the clamp around the fuel line, ensuring it is snug and tight. Start at the tank end and work your way towards the engine, making sure the clamp is not too tight, as it can restrict fuel flow. A properly tightened clamp will prevent any potential leaks and provide a reliable connection.
After securing the fuel line, it's essential to check for any signs of leakage. Turn on the engine and listen for any unusual noises, such as hissing or roaring sounds, which could indicate a fuel leak. Additionally, inspect the area around the fuel line connections for any signs of fuel seepage. If you notice any leaks, carefully tighten the connections or consider replacing the fuel line to ensure a safe and efficient fuel supply to the engine.
Remember, proper fuel line installation is vital for the reliable operation of your small engine. By following these steps and paying attention to detail, you can ensure a secure and leak-free fuel tank connection, contributing to the overall performance and longevity of your equipment.
Braided Fuel Line: Essential or Overkill?
You may want to see also
Fuel Filter Installation: Place filter in line, filtering fuel for engine
When it comes to maintaining your small engine, ensuring that the fuel system is in top shape is crucial. One essential component often overlooked is the fuel filter. Installing a fuel filter is a relatively simple process that can significantly improve your engine's performance and longevity. Here's a step-by-step guide to help you with the installation:
Step 1: Prepare the Tools and Materials
Before you begin, gather the necessary tools and materials. You'll need a fuel filter, which can be purchased from your local hardware store or online. Ensure it is compatible with your engine model. Additionally, have a wrench or pliers, a fuel line connector kit, and some rags or paper towels ready. It's always a good idea to have some fuel line cleaner and a funnel for any potential fuel line maintenance.
Step 2: Locate the Fuel Lines
Locate the fuel lines that supply fuel to your engine. These lines typically run from the fuel tank to the engine's carburetor or fuel injection system. Identify the correct lines and their respective connections. It's important to note the positions of these lines to ensure proper reattachment later.
Step 3: Remove the Old Filter (if applicable)
If you're replacing an existing fuel filter, carefully remove it. You might need to disconnect the fuel lines from the old filter and unscrew or unclip it from its mounting position. Take note of any specific tools or techniques required for your engine model. Be cautious not to spill any fuel during this process.
Step 4: Install the New Fuel Filter
Now, it's time to install the new fuel filter. Start by placing the filter in the line, ensuring it is positioned correctly and securely. Use the fuel line connector kit to attach the filter to the fuel lines. Tighten the connections securely, but be careful not to overtighten, as it may damage the lines. Double-check that the filter is firmly in place and there are no leaks.
Step 5: Test and Reattach Connections
After installing the filter, it's crucial to test the system. Start the engine and observe for any unusual noises or behavior. Check for any fuel leaks at the connections. If everything looks good, reattach the fuel lines to the engine and secure them in place. Ensure all connections are tight and properly aligned.
By following these steps, you can effectively install a fuel filter and ensure your small engine receives clean and filtered fuel. Regular maintenance of the fuel system will contribute to better engine performance and reliability. Remember to consult your engine's manual for specific instructions tailored to your model.
Understanding Fuel Line Hose Clamp Sizes: A Comprehensive Guide
You may want to see also
carburetor Link: Connect fuel line to carburetor, ensuring proper fuel-air mixture
When dealing with small engine fuel lines, one crucial step is connecting the fuel line to the carburetor, ensuring a precise fuel-air mixture for optimal engine performance. This process requires careful attention to detail to avoid potential issues. Here's a step-by-step guide to help you through this task:
Start by locating the carburetor on your small engine. It is typically a small, cylindrical component attached to the engine's intake manifold. Identify the fuel inlet, which is usually a small opening or port on the carburetor body. This is where the fuel line will connect. Ensure you have the correct fuel line size and type for your engine; using the wrong size can lead to improper fuel flow.
Next, inspect the fuel line for any damage or signs of wear. The fuel line should be in good condition, free from cracks, leaks, or any obstructions. If you notice any issues, replace the fuel line to guarantee a reliable connection. Clean the fuel line and carburetor ports to remove any debris or contaminants that may affect the fuel-air mixture. This step is essential for maintaining engine performance and longevity.
Now, it's time to connect the fuel line. Take the fuel line and insert one end into the fuel inlet of the carburetor. Ensure a secure and tight connection by pushing the line firmly into the port. You should feel a slight resistance when the line is correctly positioned. Then, connect the other end of the fuel line to the fuel supply, which could be a fuel tank or a fuel pump, depending on your engine setup. Make sure the connection is tight and secure to prevent any fuel leaks.
After the connections are made, it's crucial to verify the fuel-air mixture. Adjust the carburetor's air-fuel mixture screw to fine-tune the engine's performance. A properly adjusted screw will ensure the engine runs smoothly and efficiently. Test the engine to confirm that it starts easily and operates without any issues related to fuel delivery.
By following these steps, you can successfully connect the fuel line to the carburetor, ensuring a well-balanced fuel-air mixture for your small engine. Remember, proper maintenance and attention to detail are key to keeping your engine in optimal condition.
Understanding the Fuel Pump Pulse Line: A Vital Component
You may want to see also
Engine Mounting: Secure fuel lines to engine, using clamps or brackets
When it comes to engine mounting and securing fuel lines, the use of clamps or brackets is a practical and effective method. This process ensures that the fuel lines are properly attached to the engine, providing a secure and reliable fuel supply. Here's a step-by-step guide to help you through this task:
Start by locating the fuel lines on your small engine. These lines are typically made of rubber or flexible material and are connected to the fuel tank and various engine components. Identify the specific points where the fuel lines need to be secured to the engine block or frame. This could be at the fuel pump, carburetor, or any other area where the lines are exposed and require support.
Next, gather the necessary tools and materials. You will need fuel line clamps or brackets, which are designed to grip the fuel lines tightly. Ensure you have the appropriate size and type of clamps or brackets for your specific fuel line diameter. It's important to use the right hardware to avoid any potential leaks or damage. Additionally, have a set of tools like screwdrivers, wrenches, or pliers to assist with the installation process.
Now, carefully position the fuel lines against the engine and apply the clamps or brackets. Start at the point closest to the fuel tank and work your way towards the engine. Tighten the clamps securely, ensuring they are snug and won't come loose over time. You can use the clamps to create a firm grip on the fuel lines, preventing any movement or potential damage during operation. Consider the engine's layout and choose mounting points that provide easy access for maintenance and future adjustments.
Remember, the goal is to create a stable and secure setup for the fuel lines. Brackets can be especially useful for longer fuel lines, as they provide additional support and keep the lines in place. Ensure that the clamps or brackets are positioned in a way that doesn't restrict any engine components or moving parts. Regularly inspect the fuel line connections to ensure they remain tight and secure, especially after any maintenance or repairs.
By following these steps, you can effectively secure the fuel lines to the engine using clamps or brackets, ensuring a reliable fuel supply and a well-maintained engine setup. This process is an essential part of engine maintenance and will contribute to the overall performance and longevity of your small engine.
Fixing Fuel Lines: Can JB Weld Be a Lifeline?
You may want to see also
Testing and Adjustments: Check for leaks, ensure proper fuel flow, and make necessary adjustments
Before you can test the fuel system, ensure that the engine is properly prepared. This includes allowing the engine to cool down if it has been running recently, as hot surfaces can cause fuel to vaporize and lead to inaccurate leak checks. Additionally, make sure the engine is in a secure and controlled environment to prevent any accidental starting or movement that could cause damage during the testing process.
The first step in testing is to check for leaks. Start by inspecting all the fuel lines for any signs of damage, cracks, or deterioration. Look for any areas where the lines might be rubbing against other components, such as the frame or other engine parts, as these areas are prone to developing leaks over time. Use a soapy water solution to test for leaks. Apply the solution to the connections and observe for any bubbles. Bubbles indicate the presence of a leak, and you should investigate further to identify the source. If you find any leaks, you may need to replace the affected lines or make temporary repairs to ensure the engine runs safely.
Next, ensure that the fuel flow is adequate and consistent. Start the engine and listen for any unusual noises, such as a roaring or hissing sound, which could indicate a restriction in the fuel flow. Check the fuel filter for any signs of clogging or contamination. A clogged filter can restrict fuel flow, so it may need to be replaced. If the filter is clean, inspect the fuel pump for any signs of damage or wear. The fuel pump is responsible for delivering fuel from the tank to the engine, and any issues with it can result in poor performance. If the pump is functioning correctly, check the fuel pressure using a gauge. Proper fuel pressure is crucial for efficient engine operation, and adjustments may be necessary if the pressure is too low or too high.
Adjustments to the fuel system may include tightening loose connections, replacing worn-out components, or fine-tuning the fuel mixture. If you find any issues during the testing process, make the necessary adjustments carefully. For example, if the fuel pressure is too low, you might need to adjust the pressure regulator or replace the fuel pump. Always refer to the engine's manual for specific instructions and recommended adjustments. It is important to make these changes gradually and test the engine after each adjustment to ensure the problem is resolved without causing further complications.
Remember, proper testing and adjustments are crucial to ensuring the engine runs smoothly and efficiently. By following these steps, you can identify and address any issues with the fuel lines and system, ultimately improving the overall performance of the small engine.
Top Fuel Line Hose Retailers: Your Ultimate Guide
You may want to see also
Frequently asked questions
Before connecting the fuel lines, ensure you have the necessary tools and materials, including the correct size of fuel lines, fittings, and a fuel filter. Inspect the lines for any damage or leaks, and if any issues are found, replace the affected parts.
Start by locating the fuel tank and identifying the fuel inlet port. Clean the port and the fuel line connector to ensure a proper connection. Slide the fuel line over the port and secure it with the appropriate fitting, typically a quick-connect coupling or a threaded fitting, depending on your engine's design.
It is crucial to use the correct type of fuel line for your engine. Small engines usually require low-pressure fuel lines made of materials like rubber or vinyl. Check the engine's manual or specifications to determine the required fuel line diameter, material, and any specific requirements for flexibility or heat resistance.
When routing the fuel lines, ensure they are not pinched or kinked, as this can restrict fuel flow. Use fuel line clips or ties to secure the lines to the engine, keeping them away from moving parts. Allow enough length for the lines to reach the carburetor or fuel injection system without excessive bending.
Clean the carburetor's fuel inlet and the fuel line connector thoroughly. Slide the fuel line onto the carburetor's inlet, ensuring a snug fit. Tighten the connection using the appropriate tool, being careful not to overtighten, as this can damage the fuel line or carburetor. Test the connection by starting the engine and checking for any leaks.