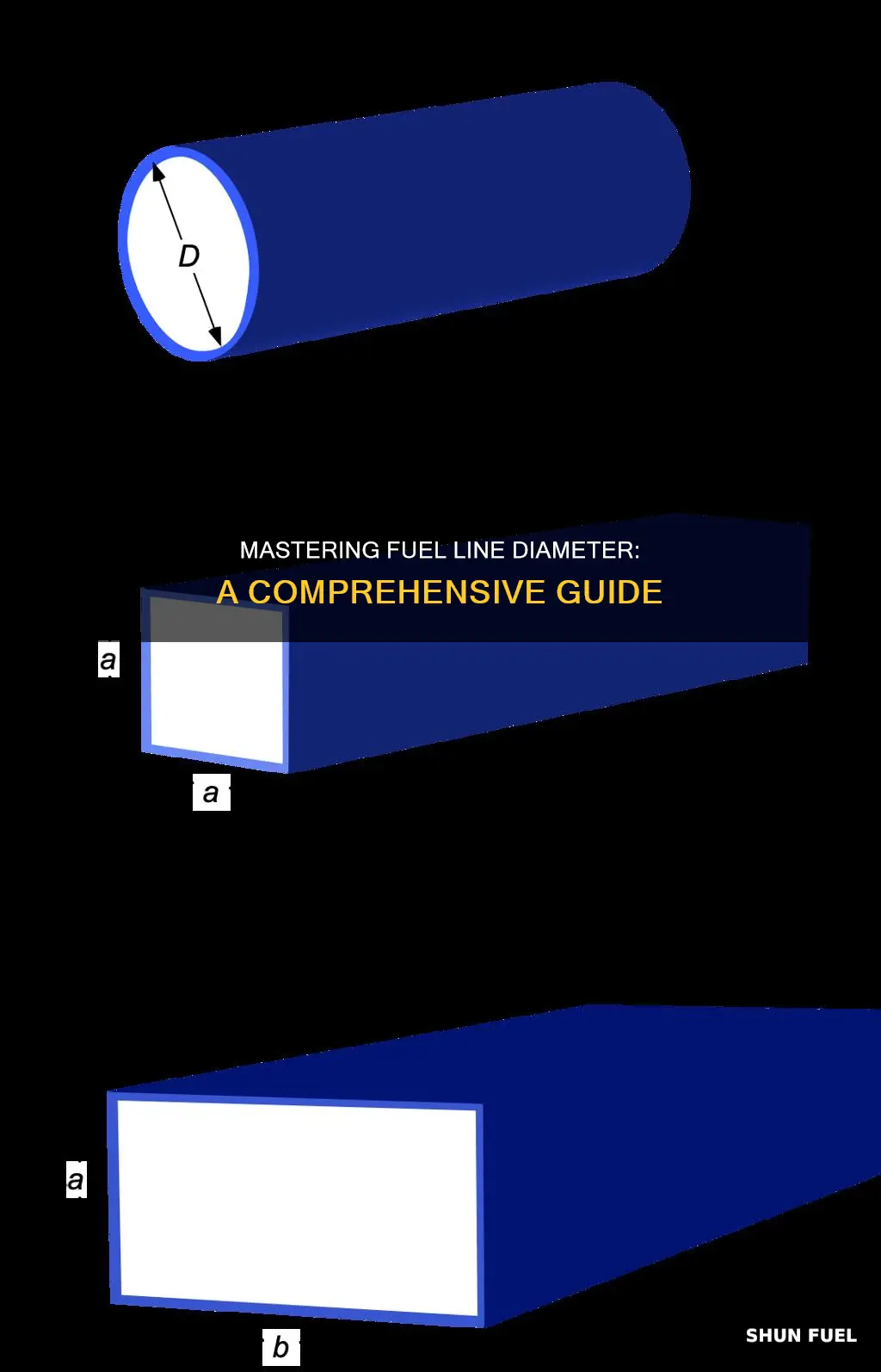
Figuring out the diameter of fuel lines is an important step in ensuring the proper functioning and safety of a vehicle's fuel system. The diameter of a fuel line determines the flow rate of fuel, which directly impacts the engine's performance and efficiency. To determine the diameter, one can use a few methods. A common approach is to measure the inside diameter of the fuel line using a caliper, which provides an accurate measurement in inches or millimeters. Another method involves using a fuel line gauge, a specialized tool designed to measure the diameter of fuel lines. Additionally, consulting the vehicle's manual or manufacturer's specifications can provide the correct diameter for a particular make and model. Understanding the diameter is crucial for selecting the appropriate fuel line and ensuring a reliable fuel supply to the engine.
What You'll Learn
- Fuel Line Diameter Calculation: Use fuel flow rate, pressure, and line length to determine diameter
- Fuel Line Size Selection: Choose diameter based on flow rate, pressure drop, and system requirements
- Fuel Line Material Impact: Different materials affect diameter; consider factors like temperature and corrosion resistance
- Fuel Line Diameter Standards: Refer to industry standards and vehicle specifications for diameter guidelines
- Fuel Line Diameter Testing: Use pressure testing and flow testing to verify diameter and performance
Fuel Line Diameter Calculation: Use fuel flow rate, pressure, and line length to determine diameter
To determine the diameter of a fuel line, you can use a formula that takes into account the fuel flow rate, pressure, and the length of the line. This calculation is crucial in ensuring efficient and safe fuel delivery systems, especially in high-performance engines or aircraft. Here's a step-by-step guide on how to calculate the fuel line diameter:
Understanding the Variables:
- Fuel Flow Rate (Q): This is the volume of fuel flowing through the line per unit of time, typically measured in gallons per minute (GPM) or liters per second (L/s). Higher flow rates require larger diameters to maintain adequate pressure.
- Pressure (P): The pressure in the fuel system is essential as it determines the force required to push fuel through the line. It is measured in pounds per square inch (psi) or pascals (Pa). Higher pressure may necessitate a larger diameter to prevent excessive wear and tear.
- Line Length (L): The length of the fuel line is a critical factor. Longer lines require larger diameters to account for the increased resistance to flow.
Formula for Diameter Calculation:
The formula to calculate the diameter (D) is derived from the principles of fluid dynamics and can be expressed as:
D = (4 * Q * P) / (π * L * μ)
Where:
- D is the diameter of the fuel line.
- Q is the fuel flow rate.
- P is the pressure in the fuel system.
- L is the length of the fuel line.
- Μ (mu) is the dynamic viscosity of the fuel, which depends on the specific fuel type.
Steps to Calculate:
- Gather the necessary data: Measure or specify the fuel flow rate, pressure, and line length. Ensure you have the dynamic viscosity of the fuel, which can be found in fuel specifications or tables.
- Plug the values into the formula: Substitute the measured or specified values into the equation.
- Perform the calculation: Solve for 'D' to find the diameter. Ensure the units are consistent throughout the calculation.
- Consider Safety Factors: In real-world applications, it's essential to add a safety margin to the calculated diameter. This accounts for potential variations in fuel properties and system performance.
By following this method, you can accurately determine the required diameter for fuel lines, ensuring optimal fuel delivery and system efficiency. This calculation is particularly important in high-performance applications where precision and reliability are critical.
Mastering the Art of Fuel Line Removal: A Guide to HFMC
You may want to see also
Fuel Line Size Selection: Choose diameter based on flow rate, pressure drop, and system requirements
When selecting the diameter of fuel lines, it's crucial to consider the specific requirements of your fuel system. The flow rate, pressure drop, and overall system design play significant roles in determining the appropriate line size. Here's a detailed guide to help you make the right choice:
Flow Rate Considerations: The flow rate, measured in gallons per minute (GPM) or liters per second (L/s), is a critical factor. A larger diameter fuel line can accommodate a higher flow rate, ensuring that the system can supply fuel efficiently without restrictions. For high-performance applications or systems with multiple fuel-hungry components, a larger line diameter is often necessary. For example, a racing car engine might require a larger diameter line to meet the demands of multiple injectors or a high-output engine.
Pressure Drop and Line Length: The length of the fuel line and the pressure drop across it are essential factors. Longer lines or those with more bends and fittings can experience increased pressure drop, which may require a larger diameter to maintain optimal performance. The pressure drop is directly related to the line's resistance to flow. A longer line with multiple fittings might need a larger diameter to ensure the fuel can flow smoothly without excessive pressure loss.
System Requirements and Compatibility: Understanding the system's requirements is key. Different fuel systems have unique specifications, and the line diameter should match these needs. For instance, a small, low-pressure system might not require a large diameter, while a high-pressure, high-flow system will demand a more substantial line. Compatibility with other components is also vital; the fuel line should fit seamlessly into the overall system design without causing interference or performance issues.
To determine the appropriate diameter, you can use flow rate calculations and pressure drop formulas, which are widely available online. These calculations will provide a theoretical basis for your decision. Additionally, consulting the manufacturer's guidelines or seeking advice from fuel system experts can offer valuable insights tailored to your specific application.
In summary, selecting the right fuel line diameter involves a careful analysis of flow rate, pressure drop, and system-specific requirements. By considering these factors, you can ensure that the fuel lines are sized appropriately, optimizing performance and reliability in your fuel system. This approach will help prevent issues like fuel starvation, pressure fluctuations, and system inefficiencies.
Plastic Fuel Line: Compatibility and Installation Guide for Trucks
You may want to see also
Fuel Line Material Impact: Different materials affect diameter; consider factors like temperature and corrosion resistance
The diameter of fuel lines is a critical aspect of fuel delivery systems, especially in vehicles and machinery that rely on precise fuel flow. When determining the appropriate diameter, it's essential to consider the material used for the fuel lines, as different materials have varying effects on performance and longevity. The material selection is crucial because it directly impacts the fuel line's ability to withstand temperature fluctuations, chemical exposure, and mechanical stress.
One of the primary factors to consider is temperature resistance. Fuel lines are exposed to varying temperatures, especially in engines, where they can experience rapid temperature changes. Materials like rubber or silicone offer excellent temperature flexibility, allowing the fuel lines to expand and contract without compromising integrity. In contrast, materials such as steel or aluminum may become brittle or lose their shape at extreme temperatures, making them less suitable for fuel lines. For high-temperature applications, materials with superior thermal stability, such as certain types of synthetic rubber or specialized polymers, are preferred.
Corrosion resistance is another critical aspect, especially when dealing with fuels that contain additives or impurities. Materials that are susceptible to corrosion can lead to fuel line degradation over time. For instance, steel fuel lines may corrode when exposed to certain fuels, causing internal damage and reduced flow capacity. In such cases, materials like stainless steel or specialized coatings can be employed to enhance corrosion resistance. Rubber or plastic fuel lines, often made from materials like EPDM (ethylene propylene diene monomer) rubber, offer good resistance to corrosion and chemical attack, ensuring the longevity of the fuel system.
The choice of material also influences the fuel line's flexibility and ease of installation. Flexible materials like rubber or silicone provide the necessary pliability to navigate through tight spaces and engine compartments without kinking or bending. However, extreme flexibility may lead to premature wear and potential leaks. On the other hand, rigid materials like steel or aluminum offer excellent structural integrity but require careful installation to avoid damage. A balance between flexibility and strength is often sought, ensuring the fuel lines can withstand the rigors of the engine environment.
In summary, the material selection for fuel lines is a critical decision that directly impacts performance and durability. Engineers and technicians must consider temperature resistance, corrosion susceptibility, and the overall flexibility required for the application. By choosing the right material, the fuel lines can effectively manage fuel flow, ensuring optimal engine performance while maintaining the integrity of the fuel system over its operational lifespan. This consideration of material properties is essential in the design and maintenance of fuel delivery systems.
Safe and Effective Methods to Thaw Frozen Car Fuel Lines
You may want to see also
Fuel Line Diameter Standards: Refer to industry standards and vehicle specifications for diameter guidelines
When determining the diameter of fuel lines, it's crucial to consult industry standards and vehicle specifications to ensure compatibility and safety. These guidelines provide essential information to help you select the appropriate fuel line size for your application.
Industry standards, such as those set by the Society of Automotive Engineers (SAE), offer recommendations for fuel line diameters based on vehicle type and engine requirements. These standards take into account factors like fuel pressure, flow rate, and system efficiency. For instance, high-performance vehicles with larger engines may require larger fuel lines to accommodate increased fuel flow and pressure.
Vehicle specifications are another critical source of information. Each vehicle model has specific requirements for fuel line diameter, which can be found in the vehicle's service manual or technical documentation. These specifications are tailored to the vehicle's engine design, fuel system configuration, and performance characteristics. It's essential to refer to these documents to ensure that the fuel lines meet the manufacturer's recommendations.
When selecting fuel lines, it's important to consider the trade-off between flow rate and pressure drop. Thicker fuel lines can handle higher pressure and provide a more efficient fuel supply, but they may also restrict flow rate. On the other hand, thinner lines offer better flow rate but may not withstand high pressure. Finding the right balance is key to optimizing engine performance.
Additionally, it's worth noting that fuel line diameter can also depend on the material used. Different materials have varying levels of flexibility and pressure resistance, which can influence the recommended diameter. For example, steel fuel lines may require larger diameters compared to flexible rubber or plastic lines. Understanding these material-specific considerations is vital for making informed choices.
Understanding the 3 Gas Lines: Marine Fuel Pump Basics
You may want to see also
Fuel Line Diameter Testing: Use pressure testing and flow testing to verify diameter and performance
Fuel line diameter is a critical aspect of vehicle performance and safety, especially in high-performance engines where fuel efficiency and power output are maximized. Accurately determining the diameter of fuel lines is essential to ensure optimal fuel delivery, minimize pressure drops, and prevent potential issues like fuel starvation or inefficient combustion. While there are various methods to measure fuel line diameter, pressure testing and flow testing are two of the most effective and reliable techniques.
Pressure testing is a fundamental method to assess fuel line performance and diameter. This process involves applying a controlled amount of pressure to the fuel line and measuring the resulting pressure drop across the line. The pressure drop is directly related to the diameter of the fuel line, as well as the length and condition of the line. By using a calibrated pressure gauge, you can accurately determine the diameter of the fuel line. The formula for calculating the pressure drop is based on the Darcy-Weisbach equation, which takes into account the fluid's properties, the line's diameter, and the flow rate. This method is particularly useful for identifying restrictions or blockages in the fuel line, as an increase in pressure drop may indicate a narrowing or obstruction.
Flow testing is another crucial technique to verify fuel line diameter and performance. This test measures the actual flow rate of fuel through the line under various conditions. By using a flow meter, you can calculate the volume of fuel passing through the line per unit of time. The flow rate is influenced by the diameter of the fuel line, as well as the pressure and temperature of the fuel. Comparing the measured flow rate with the expected flow rate based on the line's diameter and pressure can help identify any discrepancies. Flow testing is especially valuable for ensuring that the fuel line can deliver the required amount of fuel to the engine, especially during high-load conditions.
To perform these tests, you'll need specialized equipment and tools. Pressure testing requires a calibrated pressure gauge, a source of controlled pressure, and a method to measure the pressure drop. Flow testing involves using a flow meter, which can be a mass flow meter or a volumetric flow meter, depending on the application. It's important to ensure that the testing equipment is compatible with the fuel type and system being tested. Additionally, proper safety precautions should be taken when working with pressurized fuel systems.
By combining pressure testing and flow testing, you can gain a comprehensive understanding of fuel line performance and diameter. These methods provide valuable insights into the fuel system's efficiency and help identify potential issues before they cause significant problems. Regular testing and maintenance of fuel lines are essential, especially in high-performance vehicles, to ensure optimal engine operation and longevity.
Amoutlander Fuel Line Diagram: A Comprehensive Guide
You may want to see also
Frequently asked questions
Measuring the diameter of fuel lines can be done using a few methods. One common approach is to use a caliper, which is a precision measuring tool. Place the caliper across the fuel line, ensuring it's centered, and take the reading. This will give you the inside diameter. If you have access to a fuel line that is not in use, you can also measure the outside diameter by wrapping a flexible measuring tape around the line and reading the measurement.
Yes, if you don't have a caliper, you can estimate the diameter by comparing the fuel line to known objects of various diameters. For example, you can use a ruler or measuring tape to measure the length of the fuel line and then use a conversion chart or online resources to estimate the diameter based on the length and the material of the line.
When measuring fuel lines, it's important to consider the specific application and vehicle. Different vehicles may have varying fuel line sizes and configurations. Measure multiple points along the line to ensure accuracy, as fuel lines can sometimes have slight variations in diameter due to manufacturing tolerances. Additionally, check for any bends or restrictions in the line, as these can affect the flow rate and overall performance.
Absolutely! There are numerous online resources, forums, and vehicle-specific guides that provide fuel line diameter information. These resources often include diagrams and tables with different vehicle models and their corresponding fuel line sizes. You can search for your vehicle's make and model to find relevant data and ensure you get the correct diameter for your fuel lines.