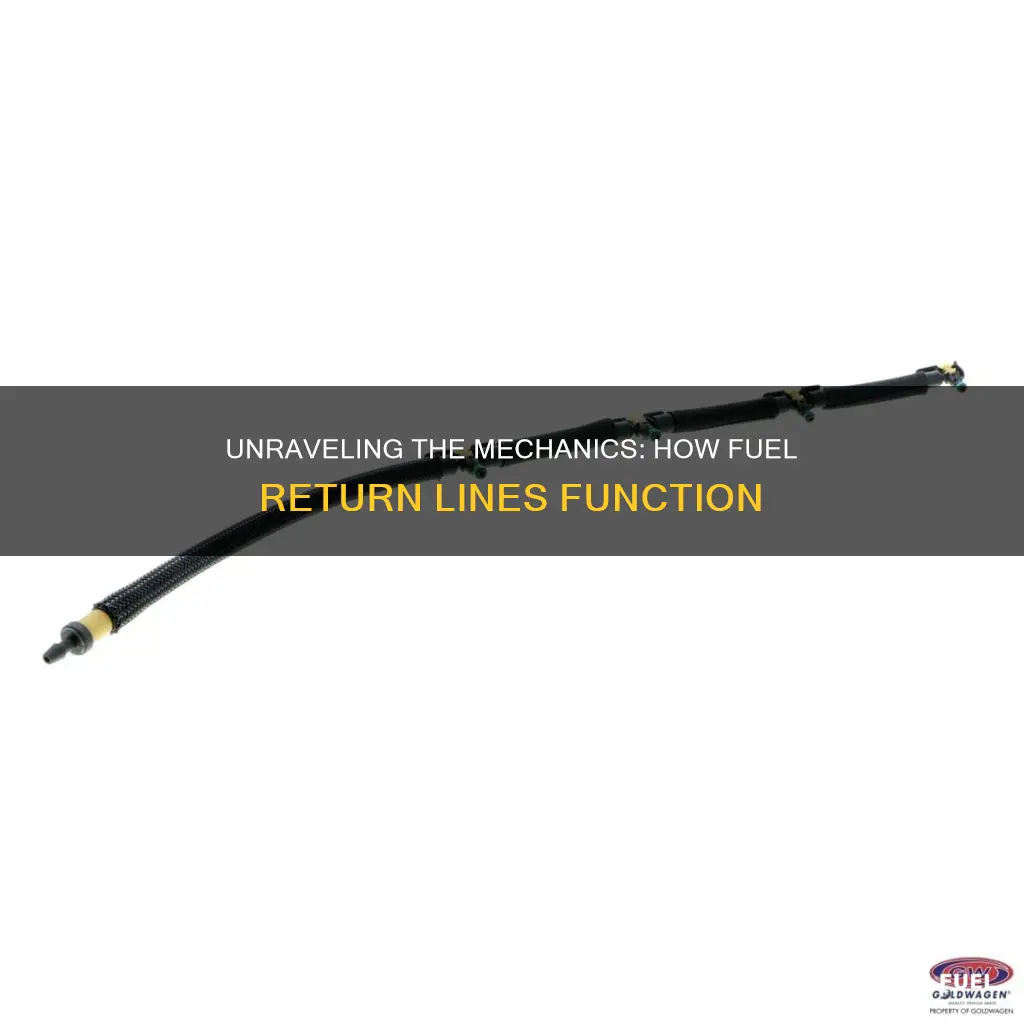
The fuel return line is a crucial component in the fuel system of an engine, responsible for managing the flow of fuel back to the tank after it has been used. This system ensures that fuel is efficiently recycled, reducing waste and optimizing performance. When an engine operates, it draws fuel from the tank through the main line, which then passes through the injectors or carburetor to power the engine. After the fuel has done its job, it returns to the tank via the return line, which is designed to handle the fuel's pressure and temperature changes. Understanding how this system works is essential for maintaining the engine's health and ensuring it runs smoothly and efficiently.
What You'll Learn
- Fuel Return Line Design: The line's design ensures efficient fuel flow back to the tank
- Pressure Regulation: It controls pressure to prevent fuel surges and ensure steady supply
- Filter and Venting: Filters and vents prevent contamination and maintain line integrity
- Flexibility and Routing: The line's flexibility allows for various engine positions and routing options
- Material and Durability: High-quality materials ensure durability and resistance to fuel degradation
Fuel Return Line Design: The line's design ensures efficient fuel flow back to the tank
The fuel return line is a critical component in any fuel system, especially in vehicles and marine applications, where efficient fuel management is essential. Its primary function is to facilitate the smooth and controlled flow of fuel back to the tank, ensuring optimal performance and preventing potential issues related to fuel accumulation. The design of this line is crucial to its functionality, as it directly impacts the overall efficiency and reliability of the fuel system.
In the design phase, engineers focus on creating a line that is both robust and flexible. The material used for the construction of the return line is carefully selected to withstand the corrosive nature of fuel and the varying temperatures it might encounter. Common materials include high-density polyethylene (HDPE) or specialized rubber compounds that offer excellent resistance to fuel degradation. The line's diameter is also an important consideration; it should be large enough to handle the expected fuel flow rate without causing excessive pressure drop, which could lead to inefficient operation.
One key aspect of the fuel return line design is the incorporation of a filter. This filter is strategically placed to capture any contaminants or debris that might have entered the system, ensuring that the fuel returning to the tank is clean and free from potential damage-causing particles. The filter's design often includes a mesh or screen that allows fuel to pass through while effectively trapping larger particles. Regular maintenance, such as replacing the filter element, is necessary to maintain the system's performance.
Additionally, the line's routing is critical to its effectiveness. It should be designed to avoid sharp bends and kinks, as these can restrict fuel flow and create areas of turbulence. A smooth, gradual curve is ideal, allowing the fuel to flow seamlessly back to the tank. Proper routing also helps to minimize the risk of damage to the line itself, ensuring a long-lasting and efficient fuel return system.
In summary, the design of the fuel return line is a meticulous process that requires careful consideration of materials, dimensions, and routing. By ensuring efficient fuel flow back to the tank, this design prevents fuel accumulation, reduces the risk of system failures, and contributes to the overall performance and longevity of the vehicle or equipment it serves. Proper maintenance and regular inspections are also vital to keeping the fuel return line in optimal condition.
Understanding Fuel Line Direction: The Switch's Crucial Role
You may want to see also
Pressure Regulation: It controls pressure to prevent fuel surges and ensure steady supply
The fuel return line is a critical component in the fuel system of an engine, and its primary function is to regulate pressure and ensure a steady supply of fuel. This is especially important in engines where fuel is supplied under pressure, such as in many modern vehicles. The line acts as a pressure regulator, preventing sudden surges in fuel pressure that could lead to engine misfires, reduced performance, and potential damage.
When fuel is injected into the engine, it is typically done so at a precise pressure to ensure optimal combustion. If this pressure is not carefully controlled, it can lead to a variety of issues. For instance, excessive pressure can cause fuel to spray too finely, leading to incomplete combustion and increased emissions. Conversely, insufficient pressure can result in poor atomization, causing fuel to 'soak' the spark plug and potentially leading to misfires.
The fuel return line helps to maintain a consistent pressure by allowing excess fuel to return to the fuel tank or reservoir. This is achieved through a series of valves and passages that direct the fuel flow. When the engine is running and fuel is being injected, the return line ensures that any excess fuel that is not immediately used by the engine is returned to the tank, thus preventing a buildup of pressure.
This pressure regulation is particularly important during acceleration or when the engine is under load. In these situations, the demand for fuel increases, and the return line must quickly adjust to provide a steady supply without causing a surge in pressure. The line's design and construction are crucial, as they determine how effectively it can handle the varying pressures and volumes of fuel.
In summary, the fuel return line is a vital part of the engine's fuel system, responsible for maintaining the correct pressure to ensure efficient and reliable operation. By controlling the flow of fuel and managing pressure, it prevents surges and ensures a consistent supply, contributing to the overall performance and longevity of the engine. Understanding its function is key to appreciating the intricate workings of modern engine systems.
Understanding the Car's Fuel Line: A Comprehensive Guide
You may want to see also
Filter and Venting: Filters and vents prevent contamination and maintain line integrity
The fuel return line is a critical component in the fuel system of an engine, and its proper functioning is essential for optimal performance and longevity. One of the key aspects of maintaining this line's integrity is the use of filters and vents, which play a vital role in preventing contamination and ensuring the smooth flow of fuel.
Filters are designed to trap contaminants and impurities that may be present in the fuel. Over time, fuel can accumulate dirt, water, and other debris, especially in older vehicles or those exposed to harsh conditions. These contaminants can cause significant issues, such as clogging the fuel injectors, leading to poor engine performance, reduced power, and even potential engine damage. By installing filters along the fuel return line, you create a barrier that captures these unwanted particles, ensuring that only clean fuel reaches the engine. Regular maintenance, including filter replacement, is crucial to keep this system effective.
Vents serve a different but equally important purpose. They are strategically placed in the fuel return line to allow air to escape. When fuel flows back into the tank, it creates a vacuum effect, pulling air into the system. This air can carry moisture, which can condense and lead to corrosion inside the fuel lines. Vents prevent this by releasing the air and any accumulated moisture, ensuring that the fuel remains dry and free from water-related issues. This is particularly crucial in environments with high humidity, where moisture in the fuel can cause rapid deterioration of the fuel system.
The combination of filters and vents forms a robust defense mechanism against contamination and corrosion. Filters capture solid particles, while vents manage the air-fuel mixture, keeping the fuel system clean and dry. This dual-protection system is essential for maintaining the fuel return line's integrity, ensuring that the fuel flows efficiently and reaches the engine without any detrimental effects. Regular inspection and maintenance of these components are recommended to guarantee the overall health of the vehicle's fuel system.
Supercharge Your Chainsaw: Exploring Enhanced Fuel Line Options
You may want to see also
Flexibility and Routing: The line's flexibility allows for various engine positions and routing options
The fuel return line is a critical component in the fuel system of an engine, and its flexibility is a key feature that enables efficient and adaptable fuel management. This flexibility is designed to accommodate various engine configurations and positioning, ensuring optimal fuel flow and system performance.
One of the primary advantages of the fuel return line's flexibility is its ability to adapt to different engine layouts. Engines can be positioned in various ways, such as horizontally, vertically, or even in a V-shape. The flexible nature of the return line allows it to be routed around obstacles, through tight spaces, and to conform to the engine's overall design. This adaptability is crucial, especially in compact or custom-built engines where space is limited and traditional fuel lines may not fit.
Engineers and designers can optimize fuel system performance by taking advantage of this flexibility. For instance, in an engine with a low-mounted design, the fuel return line can be strategically routed to ensure a consistent and efficient flow of fuel back to the tank or fuel pump. This routing can be tailored to minimize fuel pressure loss and maintain a steady supply, even when the engine is positioned at an angle.
Furthermore, the flexibility of the fuel return line enables various routing options, allowing for customization based on specific engine requirements. In some cases, the line may need to cross over other engine components or pass through different compartments. The flexible material can bend and adjust to these constraints, ensuring a secure and efficient connection without compromising the engine's overall structure. This adaptability is essential for maintaining a clean and organized engine bay, which is often a priority in high-performance or racing applications.
In summary, the flexibility of the fuel return line is a game-changer in engine design, offering the freedom to experiment with different engine positions and routing strategies. This feature ensures that fuel systems can be tailored to meet the unique demands of various engine configurations, ultimately contributing to improved performance, efficiency, and reliability.
Unraveling the Mystery: What's Beneath the Fuel Line in Elite: Dangerous
You may want to see also
Material and Durability: High-quality materials ensure durability and resistance to fuel degradation
The fuel return line is a critical component in the fuel system of an engine, and its design and construction are essential for optimal performance and longevity. When considering the material and durability of this component, high-quality materials play a pivotal role in ensuring its effectiveness and reliability.
One of the primary materials used in the construction of fuel return lines is stainless steel. This material is renowned for its exceptional corrosion resistance, making it ideal for fuel systems. Stainless steel can withstand the corrosive nature of fuel, especially in the presence of ethanol or other additives, which are common in modern gasoline blends. By using stainless steel, the fuel return line can maintain its structural integrity over time, preventing degradation and ensuring a consistent flow of fuel back to the engine.
In addition to stainless steel, some manufacturers also incorporate other high-quality materials to enhance durability. For instance, the use of braided stainless steel or reinforced rubber can provide additional strength and flexibility. Braided stainless steel is particularly useful in areas where the fuel return line needs to withstand high pressure and movement, such as in high-performance engines or vehicles with rough terrain. The braiding technique allows for a more flexible line while maintaining the structural integrity required to handle fuel pressure.
The choice of material also impacts the overall resistance to fuel degradation. High-quality materials, such as those mentioned above, can prevent fuel-related issues like phase separation, where fuel and its additives separate over time. This separation can lead to engine performance problems and potential damage. By using materials that resist fuel degradation, the fuel return line ensures that the fuel remains stable and ready for combustion, optimizing engine efficiency.
Furthermore, the durability of the fuel return line is crucial for its long-term performance. A well-constructed line should be able to withstand the rigors of the engine environment, including temperature fluctuations, vibration, and mechanical stress. High-quality materials, when combined with precise manufacturing techniques, can ensure that the fuel return line remains intact and functional over the life of the vehicle. This durability is essential to maintain the overall health of the engine and prevent costly repairs or replacements.
Unveiling the Secrets: Red Line Fuel System Explained
You may want to see also
Frequently asked questions
A fuel return line is a crucial component in fuel systems, especially in engines that use a fuel injection system. It is a dedicated line that allows unused or excess fuel to be returned from the injectors back to the fuel tank or reservoir. This process ensures that the fuel system remains properly pressurized and that the engine operates efficiently.
When the engine is running, the fuel injection system delivers the required amount of fuel to the engine's cylinders based on the engine control unit's (ECU) calculations. The fuel return line acts as a bypass, allowing any excess fuel that is not injected into the cylinders to be directed back to the fuel tank. This prevents fuel accumulation in the lines, which could lead to issues like engine misfires or reduced performance.
Clogging or blockage in the fuel return line can cause significant problems. When the line is blocked, excess fuel cannot be returned to the tank, leading to a buildup of pressure in the fuel system. This may result in fuel starvation to the engine, causing it to run poorly or even stall. Regular maintenance and checking for any blockages are essential to ensure the engine's optimal performance.
Yes, fuel return lines can be adapted or modified to suit various engine designs and requirements. Different engines may have unique fuel system configurations, and the return line can be customized to fit these setups. For example, in some high-performance applications, the return line might be designed to handle higher flow rates or incorporate filters to ensure clean fuel delivery.