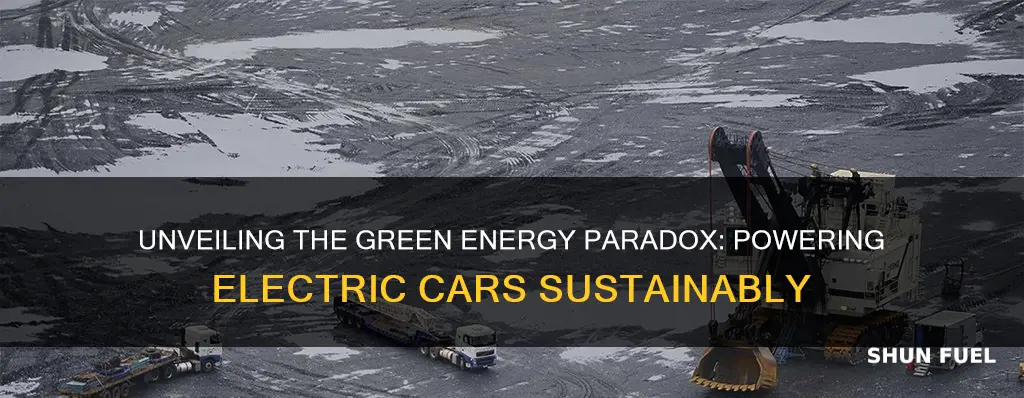
The production of electric vehicle (EV) batteries has sparked debates about its environmental impact, particularly regarding the use of fossil fuels. This paragraph aims to shed light on the complex relationship between fossil fuels and the manufacturing process of electric car batteries. It will explore the various stages of battery production, from raw material extraction to assembly, and discuss the role of fossil fuels in different processes. By examining the energy-intensive nature of battery manufacturing and the potential for renewable energy sources to mitigate environmental concerns, this introduction sets the stage for a deeper exploration of the topic.
Characteristics | Values |
---|---|
Energy Consumption | The production of lithium-ion batteries for electric vehicles (EVs) requires a significant amount of energy, primarily from fossil fuels. It is estimated that the manufacturing process can consume up to 1000 kWh of electricity per battery, with a large portion of this energy coming from non-renewable sources. |
Carbon Emissions | Manufacturing EV batteries contributes to greenhouse gas emissions. The process can result in the release of carbon dioxide (CO2) and other pollutants. Studies suggest that the production of a single lithium-ion battery can emit around 10-20 tons of CO2, depending on the energy mix used. |
Resource Extraction | Extracting raw materials for batteries, such as lithium, cobalt, and nickel, often involves energy-intensive processes and can have environmental impacts. Mining and processing these materials may require substantial fossil fuel-based energy, especially in regions with limited access to renewable energy sources. |
Recycling and Second-Life Uses | While the initial production is energy-intensive, advancements in recycling technologies can help mitigate the environmental impact. Recycling EV batteries can reduce the need for primary material extraction and lower the overall carbon footprint. Second-life applications, where used batteries are repurposed, can also contribute to a more sustainable battery ecosystem. |
Regional Variations | The environmental impact of battery production varies by region. Areas with a higher reliance on renewable energy sources for electricity generation can significantly reduce the carbon intensity of battery manufacturing. Countries with well-established renewable energy infrastructure may have a lower environmental footprint compared to those heavily dependent on fossil fuels. |
Efficiency Improvements | Ongoing research and development in battery technology aim to improve energy efficiency and reduce the environmental impact. Newer battery designs and materials can potentially lower the energy requirements and carbon emissions associated with production. |
What You'll Learn
- Resource Extraction: Mining of raw materials like lithium, cobalt, and nickel from the earth
- Refining Processes: Chemical processes to purify and refine these materials for battery production
- Manufacturing Technology: Advanced machinery and techniques used to assemble battery cells
- Energy Consumption: Significant energy use during manufacturing, often from fossil fuels
- Recycling Potential: The ability to recycle batteries and reduce reliance on new fossil fuel-based materials
Resource Extraction: Mining of raw materials like lithium, cobalt, and nickel from the earth
The process of extracting raw materials for electric vehicle (EV) batteries is a complex and resource-intensive endeavor, often requiring significant energy and, ironically, sometimes fossil fuels. The primary raw materials in question are lithium, cobalt, and nickel, which are essential components of lithium-ion batteries, the most common type used in EVs. These materials are extracted through mining, a process that can have both positive and negative environmental impacts.
Lithium, for instance, is primarily obtained through a process called 'hard rock mining'. This method involves extracting lithium ore from the earth, often from underground mines or open-pit mines. The ore is then crushed and ground to release the lithium minerals, which are then separated and refined. This process can be energy-intensive, and in some cases, it may require the use of fossil fuels to power the mining equipment and processing facilities. However, it is worth noting that the energy requirements for lithium mining are generally lower compared to other battery metals.
Cobalt, another critical component, is predominantly sourced through a process known as 'cobalt mining'. This involves extracting cobalt-rich minerals, often in conjunction with copper and nickel, from the earth. The most common method is underground mining, where miners extract the ore from tunnels. The ore is then processed to separate the cobalt, which is a challenging and energy-demanding process. Historically, cobalt mining has been associated with the use of fossil fuels, as the energy-intensive nature of the process often relies on coal-fired power plants.
Nickel, while not as energy-intensive to mine as lithium or cobalt, still requires significant resources. It is often extracted through a process called 'nickel mining', which can be done through both underground and open-pit methods. The ore is then processed to extract the nickel, which is then used in battery production. The mining and processing of nickel can also have environmental impacts, including habitat destruction and water pollution, especially if not managed sustainably.
The extraction of these raw materials is a crucial step in the production of EV batteries, but it also highlights the environmental challenges associated with the industry. As the demand for electric vehicles increases, so does the need for these raw materials, putting pressure on mining operations to meet the growing supply. It is essential to consider the energy sources and sustainability practices employed in the mining process to minimize the environmental footprint of EV battery production.
Car Charging: Fuel-Free Power for Your Vehicle
You may want to see also
Refining Processes: Chemical processes to purify and refine these materials for battery production
The production of electric vehicle (EV) batteries does indeed involve processes that can indirectly utilize fossil fuels, primarily in the form of energy-intensive manufacturing and refining steps. While the end goal is to reduce carbon emissions, the initial stages of battery manufacturing can have a significant environmental impact.
One critical aspect is the extraction and purification of raw materials. Lithium, for instance, is often obtained through mining, a process that can be energy-intensive and may rely on fossil fuels for its operation. The same goes for the extraction of other metals like cobalt, nickel, and manganese, which are essential components of EV batteries. These metals are typically sourced through mining operations, and the energy required for extraction and processing can originate from fossil fuel-based power plants.
Chemical refining processes play a vital role in preparing these raw materials for battery production. For lithium, a common refining method involves the use of solvents and chemical reactions to separate lithium compounds from impurities. This process often demands significant energy input, which, if sourced from fossil fuels, can contribute to greenhouse gas emissions. Similarly, refining cobalt and nickel involves complex chemical processes, including solvent extraction and precipitation, which may also rely on fossil fuel-derived energy.
The manufacturing of battery cells and packs is another area where fossil fuels come into play. The production of electrolytes, separators, and other components often requires energy-intensive processes, such as polymer synthesis and chemical vapor deposition. These processes can be energy-intensive and may depend on fossil fuel-based energy sources, especially in regions with a heavy reliance on coal or natural gas power plants.
However, it's important to note that the development of more sustainable practices and technologies is ongoing. Researchers and engineers are exploring ways to reduce the environmental impact of EV battery production. This includes developing more efficient extraction methods, implementing renewable energy sources for refining and manufacturing, and designing recycling processes to minimize the need for new raw material extraction. As the industry evolves, the goal is to minimize the reliance on fossil fuels while maximizing the benefits of electric mobility.
VP Fuel in Nitro Cars: Unleash the Power!
You may want to see also
Manufacturing Technology: Advanced machinery and techniques used to assemble battery cells
The process of manufacturing electric vehicle (EV) batteries is a complex one, and it is indeed an energy-intensive operation, but the primary focus is on minimizing the environmental impact. The production of battery cells for electric cars involves several advanced machinery and techniques to ensure efficiency and sustainability.
One crucial aspect is the use of automated assembly lines. These lines utilize robotic arms and machines to precisely place and secure various components within the battery cells. The robots are programmed to handle delicate tasks, such as inserting electrodes, connecting wiring, and sealing the cells. This automation ensures high accuracy and consistency, reducing the risk of human error and improving overall production quality. The machinery is designed to work at high speeds, allowing for rapid assembly, which is essential to meet the growing demand for electric vehicles.
Advanced machinery also plays a vital role in the manufacturing of battery cells themselves. The process begins with the preparation of raw materials, which are carefully sourced and processed to ensure purity and quality. These materials are then fed into specialized machines that shape and form the electrodes, which are the heart of the battery cell. For instance, roll-to-roll coating machines are used to apply thin layers of active material onto metal substrates, creating the anode and cathode. This technique allows for high-volume production and precise control over the material's thickness.
Another critical technology is the use of advanced welding and sealing systems. These machines employ laser or ultrasonic welding techniques to securely join the battery cell's components, ensuring a robust and leak-proof structure. The sealing process is crucial to prevent any potential hazards associated with battery operation. Modern sealing methods use automated systems that apply heat and pressure to create an airtight barrier, protecting the battery's internal components.
Furthermore, the manufacturing process incorporates energy-efficient practices. Many battery manufacturers invest in renewable energy sources to power their facilities, reducing the reliance on fossil fuels. This includes the use of solar panels and wind turbines to generate clean energy, which is then utilized during the production stages. By adopting such sustainable practices, the industry aims to minimize its carbon footprint and contribute to a greener future.
Tesla's Electric Revolution: Do These Cars Need Gas?
You may want to see also
Energy Consumption: Significant energy use during manufacturing, often from fossil fuels
The production of electric vehicle (EV) batteries is an energy-intensive process, and a significant portion of this energy often comes from fossil fuels, which raises concerns about the environmental impact of electric cars. The manufacturing of lithium-ion batteries, the most common type used in EVs, requires substantial energy input at every stage, from raw material extraction to component assembly.
One of the primary energy-intensive processes is the extraction and processing of raw materials. Lithium, a key component in lithium-ion batteries, is typically obtained through mining, which is a highly energy-demanding activity. The extraction process itself can consume large amounts of electricity, often generated by fossil fuel power plants, especially in regions where renewable energy sources are scarce. For instance, the production of lithium-ion batteries in China, a major global manufacturer, has been associated with significant energy consumption and greenhouse gas emissions due to the country's heavy reliance on coal-fired power plants.
The manufacturing process also requires substantial energy. The production of battery cells involves various chemical reactions and physical processes, all of which demand energy. This energy is often supplied by electricity grids, and in many cases, these grids are still heavily dependent on fossil fuels, particularly in the initial stages of battery manufacturing. The energy-intensive nature of this process means that the environmental benefits of electric cars may be partially offset by the energy used to produce their batteries.
Furthermore, the recycling and disposal of used batteries also contribute to energy consumption. Recycling lithium-ion batteries is a complex process that requires significant energy input, and the recycling infrastructure is still developing. Proper disposal of batteries is crucial to prevent environmental contamination, but it also requires energy-intensive processes to handle and process the waste.
In summary, the manufacturing of electric car batteries is a significant energy consumer, and the reliance on fossil fuels at various stages of production can negate some of the environmental advantages of electric vehicles. As the demand for EVs grows, it is essential to address this energy consumption issue by promoting renewable energy sources and improving the efficiency of battery manufacturing processes to minimize the environmental footprint of the electric car industry.
The Surprising Truth: Does Your Car's Fuel Expire?
You may want to see also
Recycling Potential: The ability to recycle batteries and reduce reliance on new fossil fuel-based materials
The recycling potential of electric vehicle (EV) batteries is a crucial aspect of the sustainability of the EV industry. As the demand for electric cars rises, so does the need to address the environmental impact of battery production and disposal. One of the key benefits of recycling EV batteries is the ability to reduce the reliance on new fossil fuel-based materials, which can have significant environmental consequences.
Battery recycling involves a process that extracts valuable materials from used batteries, such as lithium, cobalt, nickel, and manganese. These materials can then be reused in the manufacturing of new batteries, reducing the need for extracting them from raw mineral sources. For instance, lithium-ion batteries, commonly used in electric cars, contain significant amounts of lithium, which is a finite resource. By recycling these batteries, we can recover the lithium and ensure a more sustainable supply for future battery production. This process not only conserves natural resources but also minimizes the environmental impact associated with mining and extracting raw materials.
The recycling process typically begins with the collection of used batteries from various sources, including end-of-life vehicles. These batteries are then carefully disassembled to separate the different components. The black mass, a mixture of cathode and anode materials, can be processed to recover valuable metals. Through processes like hydrometallurgy and pyrometallurgy, metals like cobalt, nickel, and manganese can be extracted and purified. This recycling stream provides a sustainable source of these materials, reducing the demand for new mining operations that often rely on fossil fuels and can have detrimental environmental effects.
Furthermore, recycling EV batteries can help in mitigating the environmental impact of the entire battery lifecycle. When batteries are not recycled, they often end up in landfills, leading to soil and water contamination due to the release of toxic chemicals. By implementing effective recycling practices, we can minimize the environmental risks associated with battery disposal. This is especially important as the number of electric cars on the road increases, ensuring that the recycling infrastructure can handle the growing volume of batteries.
In summary, the recycling potential of electric car batteries is a powerful tool to combat the environmental challenges associated with the EV industry. It allows for the reduction of reliance on new fossil fuel-based materials, conserves natural resources, and minimizes the ecological footprint of battery production. As the world transitions towards a more sustainable transportation system, investing in and improving battery recycling technologies will play a vital role in ensuring a greener and more responsible future for the electric vehicle market.
Fuel Pump Cracks: Signs, Causes, and Solutions
You may want to see also
Frequently asked questions
No, electric car batteries themselves do not directly use fossil fuels in their manufacturing process. The production of lithium-ion batteries, which are commonly used in electric vehicles, involves various materials and processes, but fossil fuels are not a primary component. The focus is on recycling, reusing, and sourcing sustainable materials like lithium, nickel, cobalt, and manganese.
The sourcing of materials for batteries is a complex process, but it is moving towards more sustainable practices. Many manufacturers are now focusing on recycling and reusing materials to reduce the environmental impact. For instance, lithium can be recycled from used batteries, and cobalt can be sourced through responsible mining practices. However, some materials still require traditional mining methods, which may have environmental consequences.
The automotive industry is actively working towards reducing its reliance on fossil fuels. Many companies are investing in research and development to create more sustainable battery production methods. This includes exploring solid-state batteries, which could offer higher energy density and reduced material usage. Additionally, efforts are being made to improve recycling technologies, making the entire battery lifecycle more environmentally friendly.
Electric car batteries contribute to a more sustainable future by reducing greenhouse gas emissions and air pollution. By eliminating the direct use of fossil fuels in transportation, electric vehicles help decrease the carbon footprint associated with driving. Furthermore, the production and recycling of batteries can be designed to minimize environmental harm, especially when compared to the extraction and processing of fossil fuels.