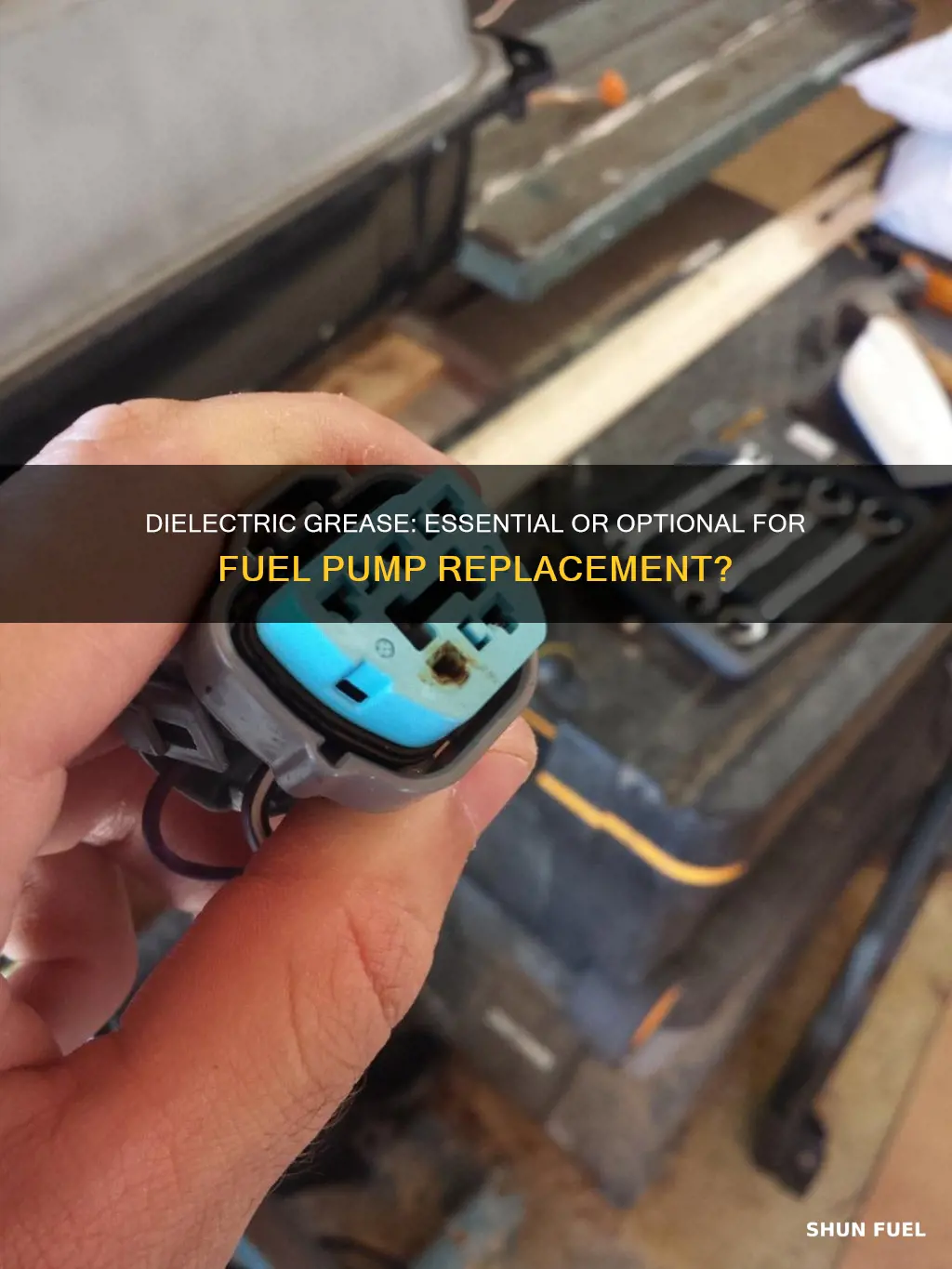
When replacing a fuel pump, it's important to consider the role of dielectric grease. This type of grease is crucial for ensuring the proper functioning of the fuel pump and the overall electrical system. Dielectric grease acts as an insulator, preventing electrical shorts and corrosion, which can be especially important in high-temperature environments. By applying dielectric grease to the fuel pump's electrical connections, you can ensure a reliable and safe operation of the vehicle's fuel system. Understanding the necessity of this step is essential for anyone working on fuel pump replacements to maintain the vehicle's performance and longevity.
Characteristics | Values |
---|---|
Application | Dielectric grease is not typically required for replacing a fuel pump. |
Purpose | The primary function of dielectric grease is to provide insulation and lubrication between electrical components to prevent arcing and corrosion. |
Relevance to Fuel Pumps | Fuel pumps are mechanical devices and do not rely on electrical connections that would benefit from dielectric grease. |
Potential Risks | Applying dielectric grease to a fuel pump could lead to fuel contamination and potential engine performance issues. |
Alternative Lubricants | Silicone-based lubricants or engine oil are often used for fuel pump maintenance, ensuring proper operation without the need for dielectric grease. |
What You'll Learn
- Dielectric Grease Benefits: Grease provides insulation and lubrication, preventing electrical shorts
- Fuel Pump Compatibility: Grease is compatible with fuel pump materials to avoid damage
- Installation Considerations: Grease application ensures proper pump installation and seals
- Maintenance and Longevity: Regular grease application extends fuel pump lifespan and performance
- Safety Precautions: Avoid using excessive grease to prevent pump malfunction and contamination
Dielectric Grease Benefits: Grease provides insulation and lubrication, preventing electrical shorts
When it comes to replacing a fuel pump, one crucial aspect that often goes unnoticed is the use of dielectric grease. This seemingly simple component plays a vital role in ensuring the longevity and reliability of your vehicle's electrical system. Dielectric grease is a specialized lubricant designed to provide insulation and protection to electrical components, especially in high-voltage environments.
The primary benefit of using dielectric grease in this context is its ability to prevent electrical shorts. Fuel pumps, particularly those in older vehicles, can be prone to developing issues due to the constant vibration and movement within the engine compartment. Over time, these vibrations can cause electrical connections to loosen or corrode, leading to potential shorts. By applying dielectric grease, you create a protective barrier that not only lubricates the moving parts of the fuel pump but also insulates the electrical contacts. This insulation prevents the buildup of moisture and contaminants, which are common causes of electrical failures.
Furthermore, dielectric grease helps to maintain the integrity of the fuel pump's wiring harness. The harness is responsible for connecting various components, and any damage or corrosion can result in erratic behavior or complete failure of the fuel pump. The grease acts as a protective shield, safeguarding the wiring against mechanical damage and environmental factors, ensuring that the electrical signals remain intact and consistent.
In addition to its insulating properties, dielectric grease also facilitates smooth operation. It reduces friction between moving parts, allowing for seamless movement of the fuel pump's internal mechanisms. This lubrication ensures that the pump functions efficiently, delivering fuel to the engine without unnecessary resistance or wear. As a result, you can expect improved performance and a longer lifespan for your fuel pump.
In summary, when replacing a fuel pump, incorporating dielectric grease is an essential step. Its ability to provide insulation, lubrication, and protection against electrical shorts and corrosion ensures that your vehicle's electrical system remains reliable and efficient. By taking this simple precaution, you can avoid potential issues and enjoy a smoother, longer-lasting fuel pump operation.
Air-Fuel Ratio Sensors: When and Why to Replace Them
You may want to see also
Fuel Pump Compatibility: Grease is compatible with fuel pump materials to avoid damage
When replacing a fuel pump, it is crucial to consider the compatibility of any substances used to ensure the longevity and proper functioning of the vehicle's engine. One common question that arises is whether dielectric grease is necessary or beneficial in this process. The answer lies in understanding the role of dielectric grease and its compatibility with fuel pump materials.
Dielectric grease, as the name suggests, is a type of lubricant specifically designed to provide insulation and protection between electrical components. It is commonly used to prevent electrical shorts and ensure the smooth operation of sensitive parts. However, when it comes to fuel pumps, the primary concern is not electrical insulation but rather the prevention of damage to the pump and the fuel system.
The materials used in fuel pumps are typically made of metals such as aluminum, brass, or steel, which are chosen for their durability and resistance to corrosion. These materials are often in close contact with the fuel, which can be highly corrosive and detrimental to the pump's performance. To avoid any potential damage, it is essential to use a lubricant that is compatible with these fuel pump materials.
Grease, in general, is a suitable option for lubricating fuel pump components. It provides a protective layer between moving parts, reducing friction and preventing wear and tear. When selecting a grease, it is crucial to choose one that is specifically formulated for automotive applications and is compatible with the materials used in the fuel pump. This ensures that the grease will not react negatively with the pump's components, causing potential damage or performance issues.
In summary, while dielectric grease may not be the primary focus when replacing a fuel pump, using a compatible lubricant is essential. Grease, when applied correctly, can help protect the fuel pump and ensure its efficient operation. It is always recommended to consult the vehicle's manual or seek professional advice to determine the best lubricants for specific fuel pump models and materials.
Replacing Ski-Doo Fuel Tank Grommets: A Step-by-Step Guide
You may want to see also
Installation Considerations: Grease application ensures proper pump installation and seals
When replacing a fuel pump, one crucial aspect often overlooked is the application of dielectric grease. This seemingly minor detail can significantly impact the pump's performance and longevity. The primary purpose of dielectric grease is to provide electrical insulation and lubrication, ensuring that the pump operates smoothly and efficiently without any electrical shorts or malfunctions.
During the installation process, various components come together, creating potential friction points. These areas require proper lubrication to facilitate a seamless assembly. Dielectric grease acts as a protective barrier, preventing direct contact between metal surfaces, which could lead to corrosion or premature wear. By applying this grease, you ensure that the pump's internal mechanisms are adequately cushioned, reducing the risk of damage during the installation process.
The fuel pump's seals are another critical area where dielectric grease plays a vital role. These seals are designed to prevent fuel leakage and maintain a tight fit between the pump and the surrounding components. Over time, seals can become brittle and lose their sealing properties. By applying grease to the seals, you create a lubricating layer that helps maintain their flexibility and integrity. This simple step ensures that the pump remains leak-free, preventing potential fuel contamination and engine issues.
Furthermore, the electrical connections within the fuel pump assembly require careful attention. Dielectric grease is applied to these connections to provide insulation and prevent arcing or short circuits. This is particularly important in high-voltage environments, where electrical discharge can cause significant damage. By using the correct type of dielectric grease, you create a reliable barrier that safeguards the pump's electrical components.
In summary, when replacing a fuel pump, the application of dielectric grease is an essential installation consideration. It ensures proper lubrication, facilitates a secure assembly, and protects critical seals and electrical connections. By paying attention to this detail, you can guarantee a successful installation, maximizing the pump's performance and extending its lifespan. Remember, a little grease goes a long way in ensuring the reliability and efficiency of your fuel pump system.
Hydrogen: A Viable Alternative to Fossil Fuels?
You may want to see also
Maintenance and Longevity: Regular grease application extends fuel pump lifespan and performance
When it comes to maintaining and extending the lifespan of your fuel pump, regular maintenance is key. One crucial aspect often overlooked is the application of dielectric grease. This simple yet effective practice can significantly enhance the performance and longevity of your fuel pump.
Dielectric grease, a specialized type of lubricant, plays a vital role in ensuring the smooth operation of fuel pumps. It is designed to withstand high temperatures and electrical insulation, making it ideal for use in fuel pump systems. When replacing a fuel pump, applying dielectric grease is essential to ensure optimal performance and prevent potential issues.
The primary function of this grease is to act as a protective barrier between moving parts within the fuel pump. It reduces friction and wear, allowing for smooth operation and minimizing the risk of premature failure. Over time, without proper lubrication, the fuel pump's internal components can become dry and prone to excessive heat, leading to potential damage.
Regular maintenance, including the application of dielectric grease, is particularly important in high-performance vehicles or those operating in extreme conditions. It helps to maintain the fuel pump's efficiency and ensures a consistent fuel supply, which is crucial for optimal engine performance. By taking this simple maintenance step, you can avoid costly repairs or premature replacements in the future.
In summary, applying dielectric grease when replacing a fuel pump is a critical step in maintaining its performance and extending its lifespan. This simple practice ensures smooth operation, reduces wear, and provides electrical insulation, ultimately contributing to the overall reliability of your vehicle's fuel system. Remember, proper maintenance can save you time and money in the long run.
Replacing the Fuel Filter: A Step-by-Step Guide for Your 2009 Cadillac CTS
You may want to see also
Safety Precautions: Avoid using excessive grease to prevent pump malfunction and contamination
When replacing a fuel pump, it's crucial to follow safety precautions to ensure the process is done correctly and safely. One important aspect to consider is the use of dielectric grease, a type of lubricant commonly used in electrical applications. While it might seem like a good idea to use grease to ensure a smooth installation, there are specific safety measures to be aware of to avoid potential issues.
Excessive use of dielectric grease can lead to several problems. Firstly, it can cause the fuel pump to malfunction. The pump's internal components, including the impeller and vanes, rely on precise clearance and alignment for efficient operation. Applying too much grease can interfere with these critical dimensions, leading to improper clearance and potential damage to the pump's mechanism. This may result in reduced performance, increased noise, or even complete failure of the pump.
Moreover, using excessive grease can contribute to contamination. Fuel pumps are designed to operate in a clean environment, and any foreign substance, including grease, can disrupt the fuel-air mixture and impact engine performance. Excessive grease can attract dirt and debris, leading to blockages in the fuel lines and injectors, which can cause engine misfires, reduced power, and even engine damage.
To ensure a safe and successful fuel pump replacement, it is recommended to use a minimal amount of dielectric grease. Apply a thin layer to the pump's components, ensuring it is evenly distributed. Focus on greasing the moving parts, such as the impeller and vanes, and avoid over-lubricating other areas. By using the correct amount, you can maintain the pump's efficiency while minimizing the risk of contamination.
Additionally, always refer to the manufacturer's guidelines and recommendations for the specific fuel pump you are working with. Different models may have unique requirements, and following these instructions will help ensure a proper and safe installation. Remember, the goal is to facilitate a smooth operation without introducing unnecessary substances that could compromise the pump's performance.
Replacing Fuel Pumps in Small Block Chevys: A Step-by-Step Guide
You may want to see also
Frequently asked questions
While dielectric grease is not a mandatory component for replacing a fuel pump, it can be beneficial in certain situations. Dielectric grease is primarily used to prevent electrical components from shorting due to moisture or friction. When replacing a fuel pump, especially if it's an older vehicle or one with a high-voltage system, applying a small amount of dielectric grease to the electrical connections can provide an extra layer of protection against moisture and ensure a secure connection. However, it's essential to use the correct type of dielectric grease and apply it sparingly to avoid any potential issues with the fuel pump's performance.
Yes, if you are installing a new fuel pump, you can generally skip the dielectric grease. Modern fuel pumps are often designed with improved insulation and moisture resistance, making the use of dielectric grease less critical. However, it's still a good practice to inspect the electrical connections and ensure they are clean and dry before reassembling the fuel pump. If you notice any corrosion or oxidation, a small amount of dielectric grease can be applied to those specific areas to enhance the pump's reliability.
Using excessive amounts of dielectric grease on the fuel pump can lead to several issues. Firstly, it may cause the pump to become sluggish or less efficient due to the added friction. Secondly, the grease can attract dirt and debris, potentially leading to clogging or contamination of the fuel system. Additionally, if the grease is not applied correctly, it might accumulate in areas where it shouldn't, causing electrical shorts or interference with other components. It's crucial to use the grease sparingly and only where necessary to ensure optimal fuel pump performance and longevity.