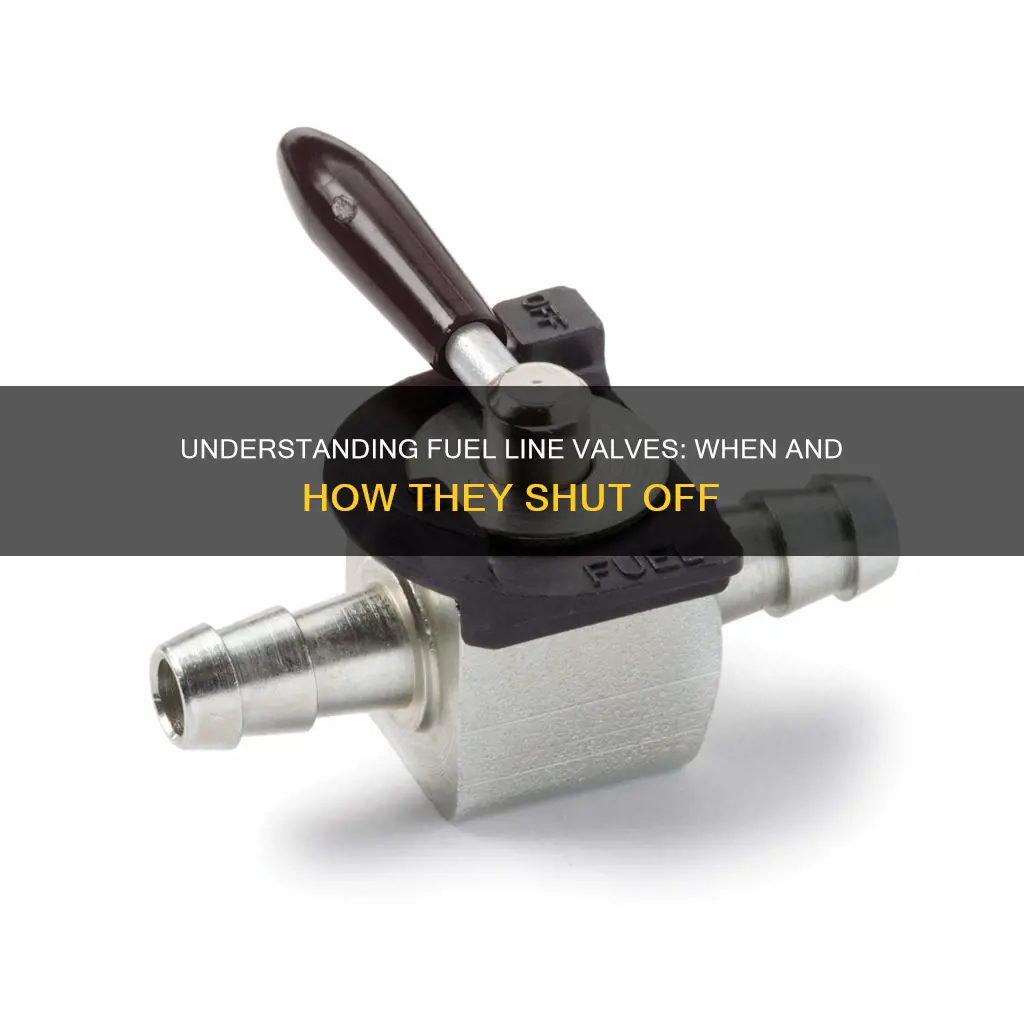
The fuel line valve is a critical component in the fuel system of a vehicle, and understanding its function is essential for maintaining optimal engine performance. This valve plays a crucial role in controlling the flow of fuel from the tank to the engine, and it is designed to shut off the fuel supply when necessary. When the engine is not in use or during specific driving conditions, the valve can be activated to prevent fuel from entering the engine, thus reducing the risk of engine damage and improving fuel efficiency. This introduction sets the stage for a discussion on the importance of the fuel line valve's shut-off mechanism and its impact on vehicle maintenance and performance.
Characteristics | Values |
---|---|
Definition | A fuel line valve is a component in a vehicle's fuel system that controls the flow of fuel from the fuel tank to the engine. |
Purpose | To regulate the fuel supply, ensuring the engine receives the correct amount of fuel for optimal performance and preventing fuel wastage. |
Operation | Typically, it is controlled by the engine control unit (ECU) or a manual switch. When shut off, it blocks the fuel flow, cutting the supply to the engine. |
Benefits | - Prevents fuel leaks and potential fires. - Protects the engine from excessive fuel pressure and potential damage. - Allows for fuel conservation during parking or when not in use. |
Considerations | - Proper maintenance is crucial to ensure the valve functions correctly. - Regular checks for leaks and proper sealing are essential. - In some cases, a shut-off valve might be required for fuel efficiency or safety reasons. |
Applications | Widely used in automotive, marine, and aviation industries for various fuel systems. |
Types | - Mechanical (manual) - Electric/Electronic (controlled by the ECU) |
Regulation | Fuel line valves are regulated by vehicle manufacturers' guidelines and industry standards to ensure safety and performance. |
What You'll Learn
- Fuel Line Pressure: Check pressure to ensure valve is functioning properly
- Valve Operation: Verify valve opens and closes as intended
- Leak Detection: Inspect for leaks around valve and fuel lines
- Fuel Pump: Test pump operation to ensure fuel flow
- Engine Performance: Monitor engine performance to confirm valve effectiveness
Fuel Line Pressure: Check pressure to ensure valve is functioning properly
Checking the pressure in your fuel lines is a crucial step in ensuring that your fuel valve is operating correctly and that your vehicle's fuel system is functioning optimally. This process involves measuring the pressure at the fuel pump and comparing it to the specified range to confirm that the valve is opening and closing as intended. Here's a detailed guide on how to perform this check:
Locate the Fuel Pump and Pressure Gauge: Start by locating the fuel pump, which is typically found in the engine compartment. It is usually a small, rectangular box with connections for fuel lines. You will also need a pressure gauge, which can be a mechanical or digital device, to measure the pressure. Ensure you have the appropriate gauge for the fuel system pressure, as different systems may require specific gauge types.
Connect the Pressure Gauge: Carefully connect the pressure gauge to the fuel pump's outlet port, ensuring a secure and tight connection. This port is specifically designed to allow access to the fuel pump's output pressure. Make sure to follow the manufacturer's instructions for proper installation to avoid any damage.
Set the Engine to Run: Start your engine and allow it to idle. This step is essential as it simulates the engine's running condition, providing a realistic pressure reading. Ensure the engine is running smoothly and stably before proceeding.
Read the Pressure: With the engine idling, read the pressure gauge. The ideal pressure range will vary depending on your vehicle's make and model, as well as the specific fuel system design. Consult your vehicle's manual or a reliable online resource to determine the correct pressure range for your car. If the pressure is within the specified range, it indicates that the fuel valve is functioning properly and regulating the fuel flow effectively.
Troubleshooting: If the pressure is too low, it may suggest a problem with the fuel pump or a restricted fuel line. In such cases, further investigation is required to identify the issue. Conversely, if the pressure is too high, it could indicate a malfunctioning fuel valve or a potential issue with the fuel pump's control mechanism. Addressing these pressure-related problems promptly is essential to prevent potential engine damage and ensure optimal vehicle performance.
Remember, regular maintenance and monitoring of your fuel system, including pressure checks, can help identify and resolve issues before they cause significant problems. Always refer to your vehicle's manual for specific instructions and recommendations regarding fuel system maintenance.
Backflushing Fuel Lines: A DIY Guide to Unclogging Tank Screens
You may want to see also
Valve Operation: Verify valve opens and closes as intended
To ensure the proper functioning of a fuel line valve, it is crucial to verify that it opens and closes as intended. This process involves a series of steps to check the valve's mechanism and ensure it operates correctly. Here's a detailed guide on how to perform this verification:
Step 1: Understanding the Valve Mechanism
Before proceeding, it's essential to have a basic understanding of the fuel line valve's design. Most fuel line valves are designed with a solenoid or a manual lever that controls the opening and closing of the valve. When energized or actuated, the solenoid or lever moves, allowing or blocking the flow of fuel. Familiarize yourself with the specific type of valve you are working on to identify the correct testing procedures.
Step 2: Inspecting the Valve
Start by visually inspecting the valve for any signs of damage, corrosion, or debris. Check for leaks around the valve body and ensure all connections are secure. Look for any visible signs of wear and tear, especially if the valve has been in use for an extended period. This initial inspection will help identify potential issues before proceeding with the testing.
Step 3: Testing the Valve's Operation
- Open the Valve: Locate the valve's actuator (solenoid or lever) and ensure it is in the 'open' position. You may need to apply manual force or use a tool to move the actuator. Observe if the valve allows fuel to flow freely.
- Close the Valve: Now, move the actuator to the 'closed' position. This action should block the fuel flow. Listen for any changes in the fuel line, such as a sudden stop in the flow or a reduction in pressure.
- Repeat and Observe: Perform the opening and closing actions a few times to ensure consistency. Observe the fuel flow and pressure changes each time. A properly functioning valve should open and close smoothly, allowing and blocking fuel flow as intended.
Step 4: Using Diagnostic Tools (Optional)
For more precise testing, you can use diagnostic tools like a fuel pressure gauge or a flow meter. Connect the gauge to the fuel line, ensuring it is secure. Open and close the valve, and monitor the fuel pressure changes. A well-functioning valve should show a noticeable change in pressure when opened and closed. Flow meters can also help measure the volume of fuel passing through the valve, confirming its operational status.
Step 5: Troubleshooting and Maintenance
If the valve fails to open or close properly, it may indicate a mechanical issue or a problem with the actuator. In such cases, further investigation is required. This could involve checking the solenoid's electrical connections, replacing worn-out parts, or seeking professional assistance for complex repairs. Regular maintenance and periodic testing are essential to ensure the valve's longevity and reliable performance.
By following these steps, you can effectively verify the valve's operation and identify any potential issues, ensuring the fuel line valve functions as intended.
Fitting Fuel: Compatibility of 3/16 Fuel Lines with 1/4 Filters
You may want to see also
Leak Detection: Inspect for leaks around valve and fuel lines
When it comes to maintaining a vehicle's fuel system, leak detection is a critical aspect that should not be overlooked. One specific area that requires careful inspection is the fuel line valve and its surrounding components. This valve is designed to control the flow of fuel from the tank to the engine, and any leaks in this system can lead to significant issues.
To begin the leak detection process, start by visually inspecting the fuel line valve and its connections. Look for any signs of damage, corrosion, or wear and tear. Over time, fuel lines can develop cracks or small holes, especially if the vehicle has been exposed to harsh weather conditions or if the lines are old and worn out. Check for any visible signs of fuel leakage around the valve, such as stains or puddles on the ground when the vehicle is parked. Even a small leak can lead to engine misfires, reduced performance, and potential safety hazards.
The next step is to use a simple yet effective method: the fuel pressure test. This test will help you identify if there are any issues with the fuel pressure regulator or the valve itself. Start the engine and listen for any unusual noises, such as hissing or roaring sounds, which could indicate a fuel leak. You can also use a fuel pressure gauge to measure the pressure at the fuel rail. If the pressure is significantly lower than the recommended range, it may suggest a problem with the fuel line or valve.
Additionally, it's essential to inspect the fuel lines for any signs of damage or deterioration. Look for any bends or kinks in the lines, as these can cause restricted fuel flow or create areas where fuel can leak. Check for any signs of rust or corrosion, especially if the vehicle is older, as this can weaken the fuel lines over time. Ensure that all connections are secure and free from any debris or contamination.
In summary, leak detection around the fuel line valve and its associated components is a crucial maintenance task. By visually inspecting the valve, checking for fuel pressure, and examining the fuel lines, you can identify potential issues before they cause major problems. Regular maintenance and prompt attention to any leaks will help ensure the vehicle's engine runs efficiently and safely.
Fixing Rusted Fuel Lines: A Step-by-Step Guide to Prevent Engine Damage
You may want to see also
Fuel Pump: Test pump operation to ensure fuel flow
Testing the fuel pump's operation is a crucial step in ensuring that your vehicle's fuel system is functioning correctly. This process involves verifying that the pump can deliver fuel to the engine as required. Here's a step-by-step guide to testing the fuel pump:
- Prepare the Vehicle: Before you begin, make sure the vehicle is parked on a level surface and the engine is cool. Turn off the ignition and disconnect the negative battery terminal to ensure safety and prevent any electrical issues during the test.
- Locate the Fuel Pump: Access the fuel pump, which is typically located near the fuel tank. It might be a separate unit or integrated into the tank. Identify the fuel pump's electrical connections and the fuel lines connected to it.
- Test the Pump's Operation: Use a fuel pressure gauge to test the pump's functionality. Connect the gauge to the fuel line, ensuring a secure connection. Start the engine and allow it to idle. Observe the gauge reading; it should show a steady rise in fuel pressure as the pump operates. If the pressure remains low or fluctuates, it indicates a potential issue with the pump or the fuel system.
- Check for Fuel Flow: To further verify the pump's performance, you can use a fuel flow meter or a simple method of observing the engine's behavior. Start the engine and let it run for a few minutes. Check for any signs of fuel starvation, such as rough idling, stalling, or reduced power. If the engine runs smoothly and consistently, it confirms that the fuel pump is delivering the required amount of fuel.
- Inspect for Leaks: After the test, inspect the fuel lines and connections for any signs of leaks. Even a small leak can lead to engine performance issues and potential safety hazards. Ensure all connections are tight and secure.
- Interpret the Results: If the fuel pump passes the test, it is likely functioning correctly. However, if you encounter any issues during the process, further investigation is required. This might include checking the fuel filter, inspecting the fuel lines for damage, or consulting the vehicle's manual for specific troubleshooting steps related to the fuel system.
Remember, proper maintenance and regular testing of the fuel pump can help prevent engine issues and ensure optimal vehicle performance. It is always recommended to consult a professional mechanic if you are unsure about any part of this process.
Can-Am Outlander 330 Fuel Line Routing: A Comprehensive Guide
You may want to see also
Engine Performance: Monitor engine performance to confirm valve effectiveness
Monitoring engine performance is a critical aspect of ensuring the proper functioning of fuel line valves, especially in systems where these valves are used to control fuel flow. When a fuel line valve is designed to shut off, it plays a vital role in preventing fuel from reaching the engine when it's not in use, which can significantly impact performance and fuel efficiency. Here's a detailed guide on how to monitor engine performance to confirm the effectiveness of these valves:
Regular Performance Checks: Implement a routine inspection schedule for your engine. This should include starting the engine and monitoring its behavior over a period. Pay close attention to the following:
- Engine Start-Up: When the engine is cold, the valve should be in a closed position to prevent fuel wastage. Observe if the engine starts smoothly and without excessive fuel consumption.
- Idle Stability: Check the engine's idle speed and stability. A properly functioning valve should ensure a steady idle, indicating that the engine is receiving the correct amount of fuel.
- Acceleration and Power: Test the engine's performance by gradually increasing the throttle. The valve should allow fuel to reach the engine during acceleration, resulting in a responsive and powerful output.
Fuel Consumption Analysis: Measuring and analyzing fuel consumption is a practical way to assess valve performance.
- Before and After Testing: Conduct tests by running the engine under various loads and conditions before and after the valve is activated. Compare the fuel usage data to identify any discrepancies.
- Fuel Efficiency: Monitor the engine's fuel efficiency over time. A well-functioning valve should contribute to improved fuel economy, as it ensures that fuel is only supplied when needed.
Engine Sensors and Diagnostics: Modern engines are equipped with advanced sensors and diagnostic systems.
- Oxygen Sensor Data: The oxygen sensor provides insights into the engine's air-fuel mixture. Monitor its readings to ensure the valve is not causing an imbalance in the mixture, which could lead to poor performance.
- Engine Control Unit (ECU) Diagnostics: The ECU can provide valuable data on engine performance. It can detect issues related to fuel flow, including valve operation, and offer error codes that can guide troubleshooting.
Load Testing: Subject the engine to various load conditions to simulate real-world driving scenarios.
- High-Load Conditions: During heavy acceleration or climbing steep inclines, the valve should allow additional fuel to reach the engine, ensuring it can handle the increased demand without compromising performance.
- Low-Load Conditions: Conversely, when the engine is idling or cruising at a steady speed, the valve should restrict fuel flow, promoting better fuel efficiency.
Visual Inspections: While monitoring performance, also conduct visual inspections of the fuel line valve and its surroundings.
- Valve Condition: Check for any signs of damage, corrosion, or debris that might affect its functionality.
- Hose and Connections: Inspect the fuel lines and connections for leaks or blockages, as these can impact the valve's ability to control fuel flow.
By following these steps, you can effectively monitor engine performance and confirm the efficiency of fuel line valves. Regular maintenance and performance checks are essential to ensure the longevity and optimal operation of the engine system.
Troubleshooting Clogged Fuel Lines: A Guide for JD L 120 Owners
You may want to see also
Frequently asked questions
The fuel line valve, often referred to as the fuel shut-off valve, is a critical component in the fuel system of a vehicle. It is typically located near the fuel tank and is designed to control the flow of fuel from the tank to the engine. When the valve is open, it allows fuel to pass through, enabling the engine to run. However, when the valve is closed, it effectively shuts off the fuel supply, preventing the engine from receiving any fuel and thus stopping the vehicle from running.
There are a few ways to check if your fuel line valve is working as it should. Firstly, you can try starting your vehicle. If the engine starts immediately and runs smoothly, the valve is likely open and functioning correctly. If the engine struggles to start or doesn't start at all, it could indicate a problem with the valve. You can also inspect the valve for any visible signs of damage or corrosion. If you notice any issues, it's best to consult a professional mechanic for a thorough inspection and potential repair.
Yes, in most cases, you can manually shut off the fuel line valve as a safety measure. This is often done by turning a small lever or screw located near the fuel tank. The exact process may vary depending on the vehicle make and model. If you encounter an emergency situation where you need to quickly stop the fuel supply, such as a leaking fuel tank or a potential fire hazard, you can manually close the valve. However, it's important to note that this should be done with caution and only as a temporary measure. It's always best to seek professional assistance for a proper repair.