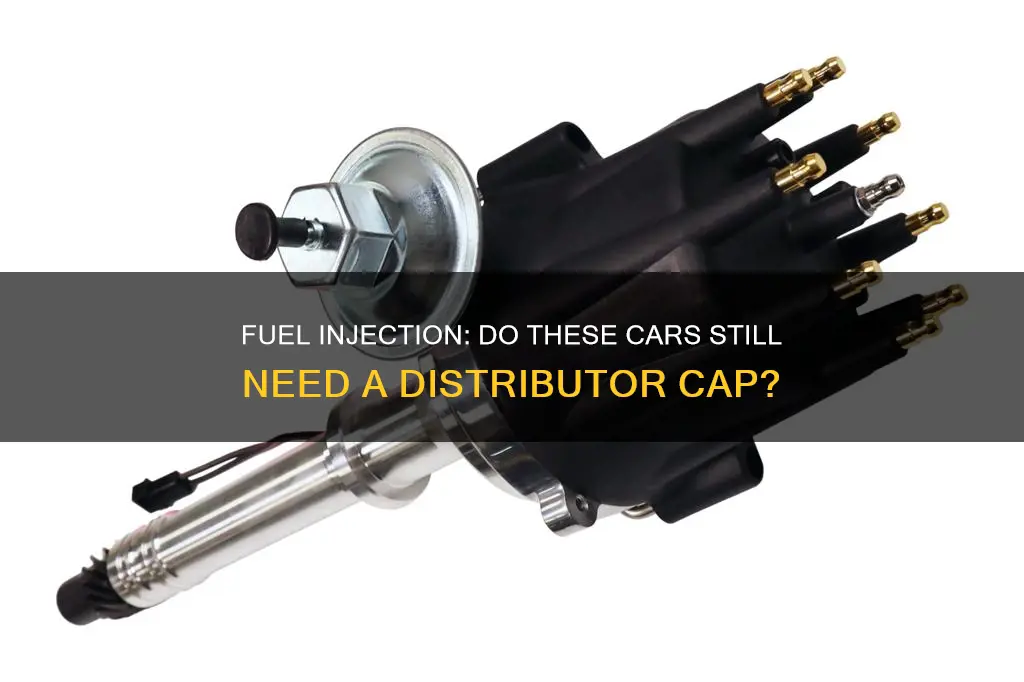
Fuel injection systems in modern cars have evolved significantly over the years, and one of the key components that has been affected by this evolution is the distributor cap. In the early days of fuel injection, distributor caps were indeed used to control the timing of the fuel injection process. However, with advancements in technology, many modern fuel injection systems have moved away from the traditional distributor cap setup. This transition has been driven by the need for more precise control over fuel injection timing, improved performance, and reduced emissions. As a result, the question of whether fuel injection cars still use distributor caps is becoming increasingly relevant, especially for those interested in the mechanics of modern vehicles.
Characteristics | Values |
---|---|
Fuel Injection System | Yes |
Distributor Cap | No |
Ignition System | Electronic (e.g., coil-on-plug) |
Spark Plug Location | Individual plugs for each cylinder |
Engine Control Unit (ECU) | Manages fuel injection and ignition timing |
Distributorless Ignition | Some modern fuel-injected engines use distributorless ignition systems, eliminating the need for a distributor cap. |
Advantages | Improved performance, fuel efficiency, and reliability compared to traditional distributor-based systems. |
Common in | Modern vehicles, especially those with electronic fuel injection and advanced ignition systems. |
What You'll Learn
- Fuel Injection Basics: Fuel injectors deliver fuel directly to the engine, bypassing the carburetor
- Distributor Cap Role: The distributor cap is not used in fuel-injected engines; spark plugs ignite fuel directly
- Ignition System Differences: Fuel-injected cars use electronic ignition systems without a distributor cap
- Spark Plug Location: Spark plugs are positioned closer to the combustion chamber in fuel-injected engines
- Engine Management Systems: Modern fuel-injected engines rely on sophisticated engine control units (ECUs) for optimal performance
Fuel Injection Basics: Fuel injectors deliver fuel directly to the engine, bypassing the carburetor
Fuel injection is a vital component of modern engine technology, offering a more efficient and controlled way of delivering fuel to the engine compared to the traditional carburetor system. The primary advantage of fuel injection is its ability to precisely manage the fuel-air mixture, ensuring optimal combustion and improved engine performance. This technology has become a standard feature in many vehicles, especially in recent years, as it provides a more reliable and powerful driving experience.
At the heart of this system are the fuel injectors, which are responsible for spraying a fine mist of fuel into the engine's intake manifold or directly into the combustion chamber. Unlike the carburetor, which mixes air and fuel in a single process, fuel injectors deliver fuel directly to the engine, bypassing the carburetor. This direct injection method allows for a more accurate control of the fuel-air ratio, resulting in better engine performance and reduced emissions.
The process begins when the engine's computer sends a signal to the fuel injectors, instructing them to release the precise amount of fuel required for the current operating conditions. This signal is based on various factors, including engine speed, load, temperature, and driver input. Each fuel injector is designed to spray fuel at a specific rate, ensuring that the fuel-air mixture is perfectly balanced for efficient combustion.
One of the key benefits of fuel injection is its ability to provide a more consistent and efficient fuel supply. By delivering fuel directly to the engine, the system eliminates the need for a carburetor, which can often lead to performance issues and reduced fuel efficiency. Fuel injectors also offer improved low-speed performance and better throttle response, making the engine more responsive and easier to control.
In summary, fuel injection technology has revolutionized the way engines operate, offering a more efficient and controlled fuel delivery system. By bypassing the carburetor and delivering fuel directly to the engine, fuel injectors provide a precise and consistent fuel-air mixture, resulting in improved performance, reduced emissions, and a more reliable driving experience. This technology continues to evolve, further enhancing the capabilities of modern vehicles.
Electric Motors: Cheaper Than Gasoline? Unveiling the Cost Comparison
You may want to see also
Distributor Cap Role: The distributor cap is not used in fuel-injected engines; spark plugs ignite fuel directly
The distributor cap is an essential component in traditional carbureted engines, where it plays a crucial role in the ignition process. However, in modern fuel-injected engines, the distributor cap has become obsolete. This is primarily due to the fundamental differences in how these two types of engines operate.
In a fuel-injected engine, the distributor's primary function is to route the high-voltage current from the ignition coil to the correct spark plug at the precise moment of ignition. This is achieved through a series of moving parts, including the distributor cap, which acts as a housing for the spark plug electrodes. The distributor cap ensures that the spark is timed correctly with the engine's intake and compression strokes. However, in fuel-injected engines, the process of delivering fuel and spark is more integrated and controlled by the engine's computer.
The key advantage of fuel injection is its ability to precisely manage the fuel-air mixture, ensuring optimal combustion. This is achieved through electronic fuel injection systems, which calculate and deliver the exact amount of fuel required for each cylinder based on engine load, temperature, and speed. As a result, the traditional distributor cap, which relies on mechanical timing and a fixed spark timing, is no longer necessary.
In fuel-injected engines, the spark plugs are ignited directly by the high-voltage current from the ignition coil, without the need for a distributor cap. This is made possible by the electronic control unit (ECU), which sends the precise timing and voltage signals to the spark plugs. The spark plugs then ignite the fuel-air mixture, ensuring efficient combustion and power delivery.
In summary, the distributor cap is not used in fuel-injected engines because the ignition process is simplified and controlled electronically. The spark plugs ignite the fuel directly, eliminating the need for a mechanical distributor cap and its associated timing components. This evolution in engine technology has led to more efficient and reliable performance in modern vehicles.
A Step-by-Step Guide to Cleaning Your Car's Fuel Tank
You may want to see also
Ignition System Differences: Fuel-injected cars use electronic ignition systems without a distributor cap
The ignition system in a fuel-injected vehicle is a crucial component that facilitates the combustion process. Unlike traditional carbureted engines, which rely on a distributor cap and rotor to manage the timing of the spark, fuel-injected cars have evolved to use electronic ignition systems. This evolution has brought about several key differences in the way these vehicles ignite their fuel.
One of the most notable changes is the absence of a distributor cap. In older engines, the distributor cap was a critical component that directed high-voltage electricity from the ignition coil to the spark plugs at the precise moment required for combustion. However, fuel-injected cars have moved away from this mechanical timing system. Instead, they employ electronic sensors and modules to determine the optimal timing for spark plug ignition. This electronic approach allows for more precise control over the engine's performance and efficiency.
Electronic ignition systems in fuel-injected cars typically consist of a few key components. These include ignition coils, which transform the low-voltage current from the battery into the high voltage needed to create a spark, and ignition modules or control units. These modules receive input from various sensors, such as the crankshaft position sensor and camshaft sensor, to determine when to fire the ignition coils. This electronic timing ensures that the spark occurs at the exact moment when the engine's pistons are positioned for optimal combustion.
The benefits of this electronic ignition system are numerous. Firstly, it eliminates the need for a distributor cap and rotor, which can wear out over time and require regular maintenance. By removing these mechanical components, fuel-injected cars reduce the chances of timing-related issues and improve overall reliability. Additionally, the electronic system provides more accurate and consistent timing, leading to better engine performance, improved fuel efficiency, and reduced emissions.
In summary, fuel-injected cars have revolutionized their ignition systems by adopting electronic controls instead of traditional distributor caps. This change has brought about more efficient and reliable engines, showcasing the continuous evolution of automotive technology. Understanding these differences is essential for mechanics and enthusiasts alike, as it highlights the unique characteristics of modern fuel-injected vehicles.
Exploring the Alcohol-Powered Car: A Sustainable Fuel Alternative?
You may want to see also
Spark Plug Location: Spark plugs are positioned closer to the combustion chamber in fuel-injected engines
In the evolution of internal combustion engines, the transition from carbureted to fuel-injected engines brought about several changes in engine design, particularly in the placement of spark plugs. One of the key differences is the location of the spark plugs in relation to the combustion chamber.
In fuel-injected engines, spark plugs are positioned much closer to the combustion chamber compared to their placement in carbureted engines. This design choice is primarily due to the nature of fuel injection itself. Fuel-injected engines deliver fuel directly into the combustion chamber, which means the air-fuel mixture is already formed and ready for ignition. As a result, the spark plug's role is to ignite this pre-mixed air-fuel mixture efficiently.
The closer placement of spark plugs to the combustion chamber in fuel-injected engines is a strategic design feature. This proximity allows for a more direct and efficient spark, ensuring that the air-fuel mixture is ignited at the optimal point in the combustion cycle. This is crucial for maintaining optimal engine performance, fuel efficiency, and power output.
This design also contributes to the overall reliability and longevity of the engine. By positioning the spark plugs closer to the combustion chamber, the engine can maintain a consistent and efficient combustion process, reducing the likelihood of misfires and other common issues associated with spark plug placement in older engine designs.
In summary, the spark plug location in fuel-injected engines is a critical aspect of their design, optimized to work in harmony with the fuel injection system. This placement ensures efficient combustion, improved performance, and a more reliable engine overall.
E85 Flex Fuel: Unleash the Power of Your Car
You may want to see also
Engine Management Systems: Modern fuel-injected engines rely on sophisticated engine control units (ECUs) for optimal performance
Modern fuel-injected engines have evolved significantly from their carbureted predecessors, and at the heart of this evolution is the Engine Control Unit (ECU). This sophisticated microcomputer is the brain of the engine, managing and optimizing its performance through a complex network of sensors and actuators. The ECU's primary role is to ensure that the engine operates efficiently, delivering the right amount of fuel and timing it precisely to maximize power and minimize emissions.
In contrast to the traditional distributor cap, which was a critical component in carbureted engines, the ECU in fuel-injected engines takes on a more comprehensive and intelligent role. The distributor cap was responsible for timing the spark to ignite the air-fuel mixture, but it lacked the intelligence and adaptability of the modern ECU. The ECU, on the other hand, continuously monitors various parameters such as engine speed, load, temperature, and exhaust gas composition. This real-time data allows the ECU to make instantaneous decisions, adjusting fuel injection timing, quantity, and even spark advance or retard to optimize performance.
The ECU's ability to adapt to changing conditions is a key advantage. For instance, during acceleration, the ECU can increase the fuel injection rate to provide more power, while also adjusting the spark timing to prevent pre-ignition. In deceleration, it can reduce fuel consumption and emissions by closing the throttle body and adjusting the air-fuel mixture. This dynamic control is far beyond the capabilities of a simple distributor cap.
Furthermore, the ECU's intelligence extends to diagnostics and self-learning. It can detect and diagnose faults in various engine systems, such as fuel injectors, sensors, and actuators. If a problem is detected, the ECU can initiate a fault code and alert the driver, often providing specific guidance on potential causes and solutions. This level of diagnostics was not possible with a distributor cap, which only served to time the spark.
In summary, the Engine Control Unit in modern fuel-injected engines is a sophisticated piece of technology that has replaced the traditional distributor cap. It manages the engine's performance, ensuring optimal fuel injection, timing, and emissions control. The ECU's intelligence and adaptability provide a level of control and efficiency that was previously unattainable, making it a critical component in the evolution of automotive engineering.
Rocket-Powered Car: Unlocking Fuel Efficiency's True Potential
You may want to see also
Frequently asked questions
No, fuel injection systems do not use a distributor cap. These systems rely on electronic fuel injection (EFI) to manage the fuel delivery, which is controlled by a computer or engine control unit (ECU). The ECU sends precise signals to the fuel injectors, bypassing the need for a distributor cap.
Fuel injection systems offer more precise control over the fuel-air mixture, resulting in improved performance, better fuel efficiency, and reduced emissions. In a traditional carburetor system, a distributor is used to manage the timing of the spark, but fuel injection systems eliminate this component.
Yes, you can convert your vehicle to fuel injection without removing the distributor cap. The process involves replacing the carburetor with a fuel injection system, which will include fuel injectors and an ECU. The distributor cap is not necessary for this conversion.
In a fuel-injected engine, the distributor cap is not required, and removing it can simplify maintenance and improve reliability. However, if you prefer to retain the original distributor cap for aesthetic or sentimental reasons, it is possible, but it may not provide any functional benefits.
Fuel injection systems can provide the spark timing information to the ignition system, but they do not rely on a distributor cap. The ECU sends signals to the ignition coil, which then provides the spark at the correct time, ensuring optimal engine performance.