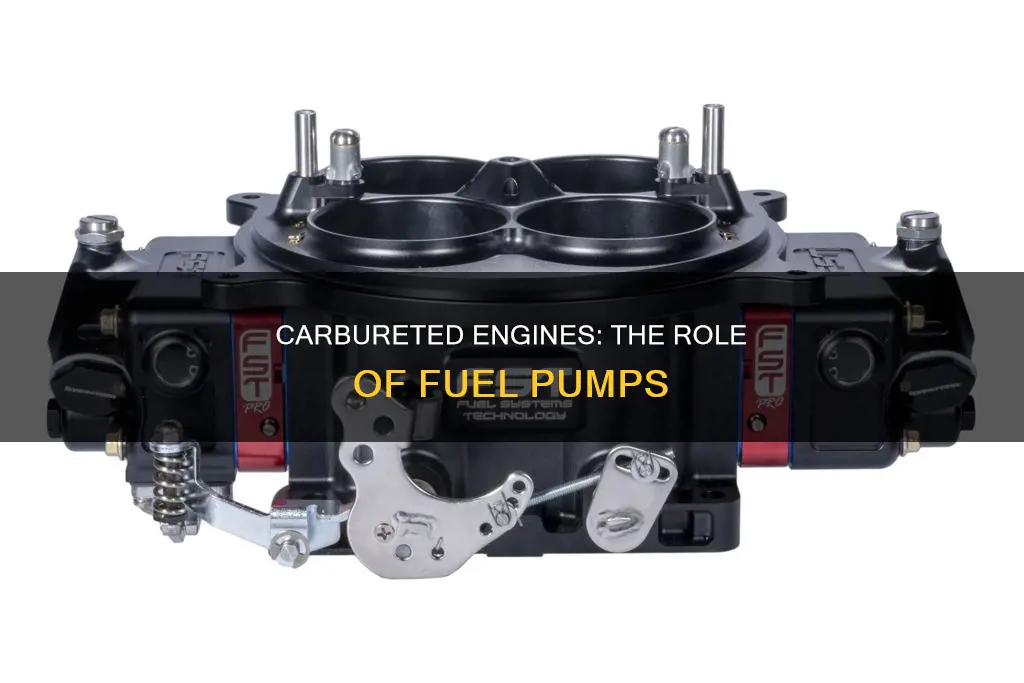
Do carbureted cars have fuel pumps? The answer is no. Carbureted cars rely on a different system to deliver fuel to the engine. Instead of a fuel pump, they use a carburetor, which is a device that mixes air and fuel in the correct ratio and delivers it to the engine. This system is simpler and more cost-effective than a fuel pump system, which is why many older cars and some modern vehicles still use carburetors.
Characteristics | Values |
---|---|
Carburetor Function | A carburetor is a device that mixes air and fuel in the correct ratio for combustion. It is a simpler system compared to fuel injection. |
Fuel Pump Requirement | Carbureted engines typically do not require a separate fuel pump. The fuel is supplied by the fuel tank and gravity feed to the carburetor. |
Fuel Pressure | Carbureted engines rely on atmospheric pressure to draw fuel from the tank, so no additional fuel pump is needed to create pressure. |
Engine Performance | While carbureted engines are simpler, they may not offer the same level of performance and efficiency as fuel-injected engines, especially at higher RPMs. |
Maintenance | Carbureted systems can be more prone to issues like carbon buildup and require regular cleaning and adjustment. |
Modern Usage | Carbureted engines are less common in modern vehicles due to the advantages of fuel injection, but some classic car enthusiasts still prefer them. |
What You'll Learn
Carburetor Design: Fuel Pumps in Carbureted Engines
In the realm of carbureted engines, the concept of fuel pumps might seem counterintuitive, as one might assume that the carburetor itself, with its intricate system of jets and passages, would be sufficient to deliver fuel to the engine. However, the design of carbureted engines often incorporates fuel pumps to ensure optimal performance and efficiency. These pumps play a crucial role in the fuel delivery process, especially in high-performance applications where precise fuel management is essential.
The primary function of a fuel pump in a carbureted engine is to increase the pressure of the fuel, which is then directed to the carburetor. This increased pressure ensures that the fuel is delivered to the engine at a rate that matches the engine's demand, even under varying load conditions. Carbureted engines rely on the fuel pump to maintain a consistent fuel-air mixture, which is critical for efficient combustion and power output. By providing a steady and controlled supply of fuel, the pump contributes to the engine's ability to operate smoothly and deliver optimal performance.
Designing the fuel pump system requires careful consideration of several factors. Firstly, the pump's capacity and flow rate must be matched to the engine's requirements. This involves calculating the necessary fuel pressure and flow to ensure the engine receives the correct amount of fuel at all operating conditions. Engineers often use specialized tools and simulations to optimize the pump's performance, taking into account factors such as engine speed, load, and ambient temperature.
Another critical aspect of carburetor design is the integration of the fuel pump into the overall fuel system. The pump must be positioned to provide efficient fuel delivery while minimizing pressure losses. Designers often place the pump close to the engine to reduce the length of fuel lines, which can lead to pressure drops. Additionally, the pump's design should consider factors like noise reduction, as fuel pumps can generate significant noise, especially in high-performance applications.
In summary, while it might seem redundant, fuel pumps are an essential component of carbureted engine design. They ensure that the engine receives the required fuel at the right pressure, enabling efficient combustion and optimal performance. The careful design and integration of fuel pumps contribute to the overall reliability and power output of carbureted engines, making them a vital consideration in automotive engineering.
Powering the Future: Fuel Cells, Batteries, or Engines? Unlocking the Mystery
You may want to see also
Fuel Injection: Comparison with Carbureted Systems
Fuel injection systems have revolutionized the automotive industry, offering a more efficient and precise way of delivering fuel to the engine compared to traditional carbureted systems. While carbureted engines rely on a carburetor to mix air and fuel, fuel injection systems take a more direct approach, providing a higher level of control and performance. This comparison aims to highlight the advantages and differences between these two fuel delivery methods.
One of the key advantages of fuel injection is its ability to deliver fuel with greater accuracy and efficiency. In a carbureted system, the carburetor mixes air and fuel in a specific ratio, which is determined by the engine's speed and load. This process can be less precise, especially at higher RPMs or during rapid changes in engine conditions. Fuel injection, on the other hand, injects fuel directly into the engine's intake manifold or cylinders, ensuring a more consistent and controlled fuel-air mixture. This results in improved power output, better fuel economy, and reduced emissions.
The precision of fuel injection is further enhanced by its electronic control. Modern fuel injection systems use sophisticated sensors and computer controls to monitor engine parameters such as temperature, pressure, and speed. These sensors provide real-time data, allowing the fuel injection system to adjust the fuel-air mixture accordingly. For instance, during high-load conditions, the system can deliver a richer mixture to meet the engine's increased power demands, while maintaining optimal performance at lower loads. This level of control is particularly beneficial for high-performance vehicles and engines operating in diverse conditions.
In contrast, carbureted systems lack this level of electronic control. Carburetors are mechanical devices that rely on the engine's vacuum and throttle position to mix fuel and air. While they are simpler in design, they can struggle to provide a consistent fuel-air mixture, especially under varying load conditions. This can lead to reduced performance and increased emissions compared to fuel-injected engines. Additionally, carbureted systems may require more frequent tuning and adjustments to maintain optimal performance, making them less reliable in the long term.
The benefits of fuel injection extend beyond performance and efficiency. These systems also contribute to improved engine longevity and reduced maintenance. By delivering fuel directly to the engine, fuel injection minimizes the risk of fuel-related issues such as carbon buildup and engine knocking. The precise control over the fuel-air mixture also helps prevent premature engine wear and extends the lifespan of critical engine components. Furthermore, fuel injection systems are often more reliable, as they have fewer moving parts and are less susceptible to mechanical failures compared to complex carbureted systems.
Maximize Your Miles: A Guide to Car Fuel Economy Calculation
You may want to see also
Carburetor Function: Role of Pumps in Fuel Delivery
In the world of internal combustion engines, the carburetor is a crucial component, especially in older vehicles. It is a device that mixes air and fuel in the correct ratio for efficient combustion. While the carburetor itself is responsible for this mixing, the role of pumps in fuel delivery is often overlooked. This is particularly true for carbureted cars, as they have a slightly different fuel delivery system compared to fuel-injected engines.
The primary function of a pump in a carbureted car is to ensure a consistent and controlled supply of fuel to the engine. Carburetors rely on a vacuum-based system to draw fuel from the tank and mix it with air. This process is facilitated by a small pump, often located near the fuel tank. This pump creates a slight pressure, which helps to push fuel through a series of passages and into the carburetor. The pump's role is to maintain a steady flow of fuel, ensuring that the engine receives the required amount of fuel for optimal performance.
In a typical carbureted system, the pump is designed to operate in conjunction with the engine's vacuum. As the engine runs, the vacuum created by the intake manifold pulls fuel from the tank. The pump then assists in this process, providing the necessary pressure to keep the fuel flowing. This is crucial because it ensures that the carburetor receives a continuous supply of fuel, allowing for precise control over the air-fuel mixture. Without the pump, the vacuum alone might not be sufficient to draw fuel, leading to potential performance issues.
The pump's operation is often regulated by a float valve, which is a critical component in the fuel tank. This valve monitors the fuel level and signals the pump to activate when the tank is low. When the fuel level drops, the float valve opens, allowing the pump to start the fuel delivery process. This mechanism ensures that the engine always has access to the required fuel, even during prolonged operation.
In summary, while the carburetor is the primary mixing device, pumps play a vital role in the fuel delivery process of carbureted cars. These pumps work in harmony with the engine's vacuum to ensure a steady and controlled supply of fuel. Understanding this relationship is essential for anyone working on or maintaining a carbureted engine, as it highlights the importance of proper maintenance and the potential consequences of neglecting these components.
Old Fuel: The Smoking Car Mystery
You may want to see also
Engine Performance: Impact of Fuel Pumps on Carbureted Cars
The relationship between fuel pumps and carbureted engines is an important aspect of automotive performance and efficiency. While it might seem counterintuitive, carbureted cars do indeed utilize fuel pumps as a crucial component in their fuel delivery system. This is in contrast to fuel-injected engines, which rely on electronic fuel injection systems to manage fuel delivery.
In a carbureted engine, the fuel pump's primary role is to ensure a consistent and controlled supply of fuel to the carburetor. The carburetor is responsible for mixing the fuel with air and then directing it into the engine's cylinders. The fuel pump's operation is often driven by the engine's vacuum, which creates a low-pressure area that pulls fuel from the tank and pushes it through a series of small passages to the carburetor. This process is essential for maintaining the proper air-fuel mixture, which is critical for efficient combustion and optimal engine performance.
The impact of a well-functioning fuel pump on engine performance is significant. It ensures that the engine receives the correct amount of fuel at the right time, allowing for precise control over the air-fuel mixture. This results in improved power output, better fuel efficiency, and reduced emissions. When the fuel pump delivers fuel effectively, the engine can operate at its peak, providing a smooth and responsive driving experience.
However, the performance of a carbureted engine can be greatly affected by the fuel pump's efficiency and reliability. If the fuel pump fails or becomes inefficient, the engine may experience issues such as poor acceleration, rough idling, and even stalling. This is because the fuel pump's role in maintaining a steady fuel supply becomes compromised, leading to an improper air-fuel mixture and potential engine misfires.
In summary, fuel pumps play a vital role in the performance of carbureted cars by ensuring a consistent fuel supply to the carburetor. Proper functioning of the fuel pump is essential for maintaining the engine's efficiency, power, and overall reliability. Understanding this relationship can help car owners and mechanics appreciate the importance of regular maintenance and timely replacement of fuel pumps to keep carbureted engines running optimally.
Is Toyota's 88 Octane Fuel the Best Choice for Your Car?
You may want to see also
Maintenance: Replacing Fuel Pumps in Carbureted Vehicles
When it comes to carbureted vehicles, the relationship between the fuel pump and the carburetor is an important one. While it might seem counterintuitive, carbureted cars do indeed utilize fuel pumps to ensure a steady supply of fuel to the engine. This is in contrast to fuel-injected vehicles, which rely on electronic systems to manage fuel delivery. The fuel pump's primary role is to deliver fuel from the tank to the carburetor, where it is mixed with air and then fed into the engine's cylinders. This process is crucial for maintaining optimal engine performance and efficiency.
Over time, fuel pumps in carbureted vehicles can wear out due to various factors such as age, contamination, or mechanical issues. When this happens, the engine may start to experience symptoms like poor acceleration, rough idling, or even stalling. One of the most common signs of a failing fuel pump is a lack of power or hesitation when the accelerator is pressed. This is because the pump is unable to provide the required fuel volume to meet the engine's demands.
Replacing a fuel pump in a carbureted vehicle is a task that requires careful attention to detail and some mechanical know-how. Here's a step-by-step guide to help you through the process:
- Preparation: Before you begin, ensure you have the necessary tools and parts, including the new fuel pump, a fuel filter, and any required seals or gaskets. It's also a good idea to drain the fuel tank and run the engine dry to prevent any fuel-related issues during the replacement.
- Locate the Fuel Pump: The fuel pump is typically located near the fuel tank or in the engine compartment, depending on the vehicle's design. Carefully inspect the pump for any signs of damage or wear. You may need to remove some panels or access panels to get to it.
- Remove the Old Pump: Disconnect the electrical connections and hoses attached to the fuel pump. Carefully lift the pump out of its mounting position, being mindful of any O-rings or seals that may need replacement. Take note of the pump's orientation to ensure proper installation of the new part.
- Install the New Pump: Carefully insert the new fuel pump into the mounting position, ensuring it is aligned correctly. Secure it with the appropriate fasteners and torque them according to the vehicle's specifications. Reattach the electrical connections and hoses, ensuring a tight and secure fit.
- Test and Bleed: After installation, start the engine and allow it to run. Check for any leaks or unusual noises. If everything appears normal, you may need to bleed the fuel lines to remove air bubbles. This process involves running the engine at different speeds while simultaneously opening and closing the fuel valve to ensure a steady fuel supply.
- Final Checks: Once the engine is running smoothly, perform a thorough inspection to ensure there are no fuel leaks. Check the fuel gauge and ensure it reads correctly. Test-drive the vehicle to confirm that the engine performs optimally and that all symptoms related to the old fuel pump have been resolved.
Remember, replacing a fuel pump is a specialized task, and if you're unsure about any step, it's best to consult a professional mechanic. Proper maintenance of the fuel pump can help ensure your carbureted vehicle runs smoothly and efficiently for years to come.
Plutonium: A Nuclear Fuel for the Road?
You may want to see also
Frequently asked questions
No, carbureted cars do not typically have fuel pumps. Carburetors are mechanical devices that mix air and fuel in the correct ratio for combustion, and they draw fuel from the tank using atmospheric pressure. The fuel is then atomized and delivered to the engine via the carburetor's passages.
In a carbureted engine, the fuel is supplied directly from the fuel tank to the carburetor. The carburetor has a float bowl that holds a small amount of fuel, and as the engine runs, it creates a partial vacuum that pulls fuel from the tank into the bowl. This process is known as 'float bowl suction'.
While not always necessary, some high-performance carbureted engines may benefit from an auxiliary fuel pump. This pump ensures a consistent and high-pressure fuel supply, especially during high-load conditions or when the engine is running at high RPMs. It can improve performance and fuel delivery precision.
Yes, most carbureted vehicles will have a fuel line that connects the fuel tank to the carburetor. This line is usually made of rubber or plastic and is designed to withstand the pressure and temperature changes associated with the engine's operation.
Yes, it is possible to retrofit a fuel pump to a carbureted car, especially in high-performance or modified applications. However, it requires careful consideration of the engine's fuel requirements, pump capacity, and the overall fuel system design to ensure proper functionality and performance.