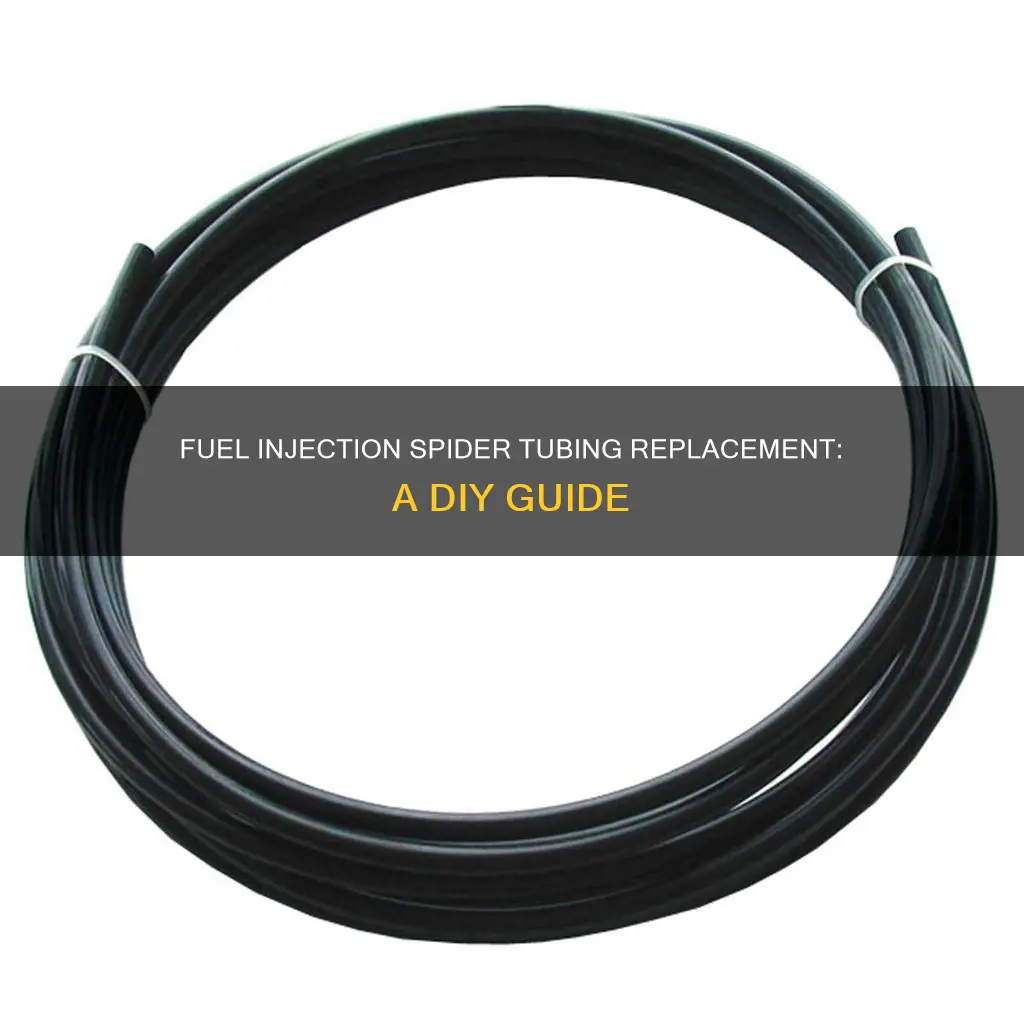
Replacing the tubing on a fuel injection spider can be a challenging task, but it is a necessary step if you want to ensure your vehicle runs smoothly and efficiently. The fuel injection spider is a crucial component in the fuel injection system, responsible for distributing fuel to the engine's cylinders. Over time, the tubing can become worn out or damaged, leading to fuel leaks, poor engine performance, and even potential safety hazards. In this guide, we will explore the process of replacing the tubing, including the necessary tools, safety precautions, and step-by-step instructions to help you get the job done right.
Characteristics | Values |
---|---|
Tubing Replacement | Yes, it is possible to replace the tubing on a fuel injection spider. This process involves removing the old tubing and installing a new one to ensure proper fuel delivery. |
Complexity | The difficulty of the replacement depends on the specific make and model of the fuel injection system. Some systems may have easily accessible tubing, while others might require more intricate disassembly. |
Tools Required | Basic automotive tools such as wrenches, screwdrivers, and possibly a fuel pressure gauge are typically needed for this task. |
Expertise | While it can be a DIY project for those with mechanical skills, it is recommended to have experience with fuel injection systems to avoid potential issues. |
Risks | Replacing tubing without proper knowledge can lead to fuel leaks, improper fuel pressure, or damage to the fuel injectors. |
Cost | The cost of replacement tubing can vary depending on the type and quality of the tubing. It may be more affordable to purchase new tubing compared to professional labor costs. |
Time | The time required for the replacement can range from a few hours to a full day, depending on the complexity of the system and the individual's skill level. |
Advantages | Replacing worn-out tubing can improve fuel efficiency, power, and overall engine performance. |
Disadvantages | Potential disadvantages include the need for specialized knowledge, the risk of errors, and the possibility of requiring additional parts or repairs. |
What You'll Learn
- Fuel Injection Basics: Understanding fuel injectors, their function, and the role of tubing
- Spider Assembly: Steps to disassemble and reassemble the fuel injection spider
- Tubing Replacement: Techniques for replacing damaged or leaking fuel tubing
- Tools and Materials: Essential tools and materials needed for the repair
- Safety Precautions: Safety measures to prevent fuel leaks and ensure proper handling
Fuel Injection Basics: Understanding fuel injectors, their function, and the role of tubing
Fuel injection is a critical component of modern vehicle engines, ensuring efficient and precise fuel delivery for optimal performance. At the heart of this system are fuel injectors, which play a pivotal role in the combustion process. These injectors are responsible for spraying a fine mist of fuel into the engine's intake manifold or directly into the combustion chamber, where it mixes with air for combustion. This process is far more efficient than traditional carburetor systems, as it allows for better control over fuel-air mixture ratios, resulting in improved power, reduced emissions, and better fuel economy.
The function of a fuel injector is to precisely meter and inject fuel into the engine at the right time and in the correct amount. This is achieved through a complex process that involves the injector's solenoid, which is an electromagnetic valve. When energized, the solenoid opens, allowing high-pressure fuel to be injected into the engine. The timing and duration of this injection are controlled by the engine's electronic control unit (ECU), ensuring the engine receives the optimal amount of fuel for each cylinder's combustion cycle.
Now, let's delve into the role of tubing in this system. Fuel injectors are connected to a fuel rail or a high-pressure fuel pump via a network of tubing. This tubing is crucial for delivering the high-pressure fuel from the fuel pump or tank to the injectors. The tubing must be designed to withstand the pressure and temperature variations within the fuel system, as well as the corrosive nature of fuel itself. Typically, fuel injectors use a type of tubing known as a fuel line or fuel rail tubing, which is made from materials like steel, aluminum, or specialized plastics.
Replacing the tubing on a fuel injector is a specialized task that requires a good understanding of the fuel injection system and engine mechanics. If the tubing is damaged or leaks, it can lead to poor fuel delivery, reduced engine performance, and potential safety hazards due to fuel leaks. Common issues that may necessitate tubing replacement include cracks, punctures, or corrosion, often caused by fuel contamination, extreme temperatures, or mechanical damage. When replacing tubing, it's essential to use the correct type and size of tubing to ensure a proper fit and maintain the system's integrity.
In summary, fuel injectors are integral to modern vehicle engines, providing precise fuel delivery for optimal performance. The tubing connected to these injectors plays a vital role in delivering high-pressure fuel, and any issues with the tubing can significantly impact engine operation. Understanding the basics of fuel injection and the role of tubing is essential for maintaining and troubleshooting fuel injection systems effectively.
Replacing the Fuel Pump in Your 99 Super Duty
You may want to see also
Spider Assembly: Steps to disassemble and reassemble the fuel injection spider
The fuel injection spider, a critical component in the fuel system of many engines, is designed to distribute fuel evenly to multiple injectors. Over time, this intricate mechanism can experience wear and tear, leading to potential performance issues. One common scenario where disassembly and reassembly might be necessary is when you need to replace damaged or worn-out tubing. Here's a step-by-step guide to help you navigate this process:
Disassembly:
- Safety First: Before you begin, ensure the engine is cool to the touch. Working on hot engines can be dangerous. Additionally, locate the fuel pump and disconnect the fuel line to prevent any accidental fuel spillage.
- Locate the Spider: The fuel injection spider is typically located near the engine's intake manifold. It is often a complex assembly with multiple components, including the spider body, injectors, and tubing.
- Remove Injectors: Start by carefully removing the fuel injectors. This process may vary depending on your engine model, but generally, you'll need to disconnect the electrical connections and carefully pull the injectors away from the manifold. Set them aside, ensuring you keep track of their orientation.
- Access the Spider: With the injectors removed, you should now have access to the fuel injection spider. Carefully lift the spider out of the manifold, being mindful of any O-rings or seals that might be present.
- Detaching Tubing: Identify the tubing connected to the spider. This tubing is responsible for delivering fuel from the pump to the injectors. Carefully cut or unscrew the tubing connections to remove the old tubing. Take note of the direction of the tubing to ensure proper reassembly.
Reassembly:
- Prepare New Tubing: If you are replacing the tubing, ensure you have a new piece that matches the original specifications. Cut the new tubing to the appropriate length, allowing for a small excess for bending and connection.
- Connect Tubing: Start by attaching one end of the new tubing to the fuel pump. Use the appropriate connectors or seals to ensure a secure and leak-free connection.
- Position the Spider: Carefully position the fuel injection spider back into the engine manifold. Ensure it is aligned correctly and that all components are in their original positions.
- Reattach Injectors: Slide the fuel injectors back into their respective positions on the manifold. Secure them using the appropriate fasteners, ensuring they are tight but not overtightened.
- Final Connections: Reconnect the electrical wiring to the injectors and double-check all connections. Reattach the fuel line to the pump, ensuring it is securely fastened.
Reassembling the fuel injection spider requires patience and attention to detail. Take your time to ensure all components are correctly aligned and secured. If you encounter any issues or have doubts about the reassembly process, consulting the manufacturer's manual or seeking professional assistance is advisable. Proper reassembly will ensure optimal fuel distribution, leading to improved engine performance.
Replacing the Fuel Pump in Your 2001 Camaro: Step-by-Step Guide
You may want to see also
Tubing Replacement: Techniques for replacing damaged or leaking fuel tubing
When it comes to replacing damaged or leaking fuel tubing, it's crucial to approach the task with precision and care. Fuel injection systems rely heavily on the integrity of their tubing to ensure optimal performance and prevent engine issues. Here's a step-by-step guide to help you navigate the process effectively:
- Assessment and Preparation: Begin by thoroughly inspecting the fuel injection system. Identify the damaged or leaking tubing section. Take note of any visible signs of wear, cracks, or corrosion. It's essential to understand the extent of the damage to determine the appropriate replacement strategy. Gather the necessary tools and replacement tubing, ensuring it matches the original specifications.
- Removal of Old Tubing: Carefully remove the damaged tubing section. This process requires patience and precision to avoid causing further damage. Start by loosening any connections or fittings securing the tubing. Be gentle to prevent tearing or puncturing the existing tubing. Carefully slide or cut the damaged section out, leaving enough length to facilitate the new tubing installation.
- Cleaning and Preparation: Once the old tubing is removed, clean the surrounding areas. Remove any debris, corrosion, or residue that could interfere with the new tubing's installation. Ensure the surface is smooth and free from contaminants. This step is vital to guarantee a secure and leak-free connection.
- Installing the New Tubing: Now, carefully insert the new tubing into the prepared area. Ensure it is aligned correctly and securely in place. Use appropriate tools or clamps to hold the tubing temporarily while you connect it to the fuel injectors and other components. Tighten the connections securely, but be cautious not to overtighten, as it may damage the tubing or connectors.
- Testing and Verification: After the installation, start the engine and monitor for any leaks. Check all connections and fittings to ensure they are tight and secure. Run the engine through its operating range to verify that the fuel system is functioning correctly. This step is critical to identifying any potential issues before they become major problems.
Remember, fuel injection systems are complex, and proper diagnosis and repair are essential. Always refer to the vehicle's manual or seek professional advice if you're unsure about any step. With careful execution, you can effectively replace damaged tubing, ensuring your fuel injection system operates optimally.
Replacing Fuel Pumps: A Step-by-Step Guide for Beginners
You may want to see also
Tools and Materials: Essential tools and materials needed for the repair
When it comes to replacing the tubing on a fuel injection spider, having the right tools and materials is crucial to ensure a successful repair. Here's a detailed breakdown of the essential items you'll need:
Tools:
- Fuel Injection Tester: This tool is essential for diagnosing the issue and ensuring the new tubing is functioning properly. It helps identify any leaks or pressure issues in the fuel system.
- Fuel Pressure Gauge: Used to measure the pressure of the fuel system before and after the repair. This gauge will help you verify that the fuel pressure is within the correct range.
- Fuel Injector Tester: A specialized tool for testing individual fuel injectors. It allows you to check for proper fuel flow and spray patterns, ensuring the injectors are functioning correctly.
- Wrenches and Pliers: Standard automotive tools for tightening and loosening nuts, bolts, and fittings. You'll need various sizes to accommodate different components.
- Socket Set: A set of sockets for accessing bolts and screws within the fuel injection system.
- Hose Clamps: Used to secure and seal the new tubing connections.
- Safety Gear: Safety goggles and gloves are essential for protecting your eyes and hands during the repair process.
Materials:
- New Tubing: Obtain the correct type and size of tubing compatible with your fuel injection system. Ensure it is made from a durable material suitable for fuel applications.
- Fittings and Adapters: You might need various fittings and adapters to connect the new tubing to the existing fuel lines and injectors.
- Fuel Filter: A replacement fuel filter is often recommended to ensure clean fuel delivery to the injectors.
- Fuel Injector Cleaners: These cleaners can help remove any deposits or contaminants from the injectors before and after the repair.
- Fuel System Sealant: A specialized sealant can be applied to ensure a secure and leak-free connection between the new tubing and existing components.
Having these tools and materials readily available will make the repair process smoother and more efficient. Remember to follow manufacturer instructions and safety guidelines throughout the process.
Replacing Fuel Pump in a '94 Firebird: Step-by-Step Guide
You may want to see also
Safety Precautions: Safety measures to prevent fuel leaks and ensure proper handling
When working on fuel injection systems, safety is paramount to prevent any accidents or costly repairs. Here are some essential safety precautions to follow when replacing tubing on a fuel injection spider:
Fuel System Isolation: Before starting any work, ensure the fuel supply to the engine is isolated. Locate the fuel pump relay or fuse and disconnect it to cut off the fuel flow. This step is crucial to prevent accidental fuel sprays or leaks while handling the system.
Ventilation and Respiratory Protection: Fuel vapor can be hazardous, so work in a well-ventilated area or use a fume hood. Consider wearing a respirator or a mask designed for fuel vapor to minimize inhalation risks. Proper ventilation is key to maintaining a safe working environment.
Personal Protective Equipment (PPE): Always wear appropriate PPE, including gloves and safety goggles. Fuel can cause skin irritation and eye damage, so protect yourself accordingly. Additionally, consider wearing long sleeves and pants to prevent any accidental contact with hot engine components.
Careful Disassembly: When removing the old tubing, be gentle and avoid forcing any connections. Fuel injection spiders are intricate, and improper handling can damage the delicate components. Take your time to carefully disconnect the tubing, ensuring you don't twist or kink the fuel lines.
Leak Testing and Inspection: After replacing the tubing, perform a thorough leak test. Check for any signs of fuel seepage around the connections and fittings. Inspect the entire fuel injection system for any damage or wear, especially in areas where the tubing was removed. This step ensures that the system is functioning correctly and safely.
Remember, when working on fuel-related systems, it's essential to be cautious and methodical. Taking these safety precautions will help prevent fuel leaks, ensure proper handling, and contribute to a successful repair or maintenance task. Always refer to the vehicle's manual and seek professional advice if needed.
Replacing Fuel Lines: Toro S200 Step-by-Step Guide
You may want to see also
Frequently asked questions
Yes, replacing the tubing on a fuel injection spider is a task that can be accomplished by a DIY enthusiast with some mechanical knowledge and the right tools. It involves removing the old tubing and installing a new one, which can be a bit tricky but is definitely feasible.
Over time, the tubing in a fuel injection spider can become worn out, cracked, or damaged due to factors like heat, fuel contamination, or mechanical stress. Common signs include fuel leaks, poor engine performance, hard starting, or erratic idling. If you notice any of these symptoms, it's advisable to inspect the tubing for any visible damage.
Accessing the tubing requires removing certain components of the fuel injection system. Start by disconnecting the fuel lines and injectors from the spider. Carefully lift the spider and inspect the tubing for any signs of damage or wear. You might need to remove additional parts or clips to gain full access. Take note of the tubing's position and any connections to ensure a proper replacement.
Yes, it's recommended to use a fuel pump flush and a fuel system cleaner to remove any old fuel and debris before replacing the tubing. You'll need a new tubing set that matches the original specifications. Carefully push the new tubing into place, ensuring it is correctly aligned. Reassemble the fuel injection system, making sure all connections are secure. It's crucial to test the system for leaks and proper functionality after the replacement.