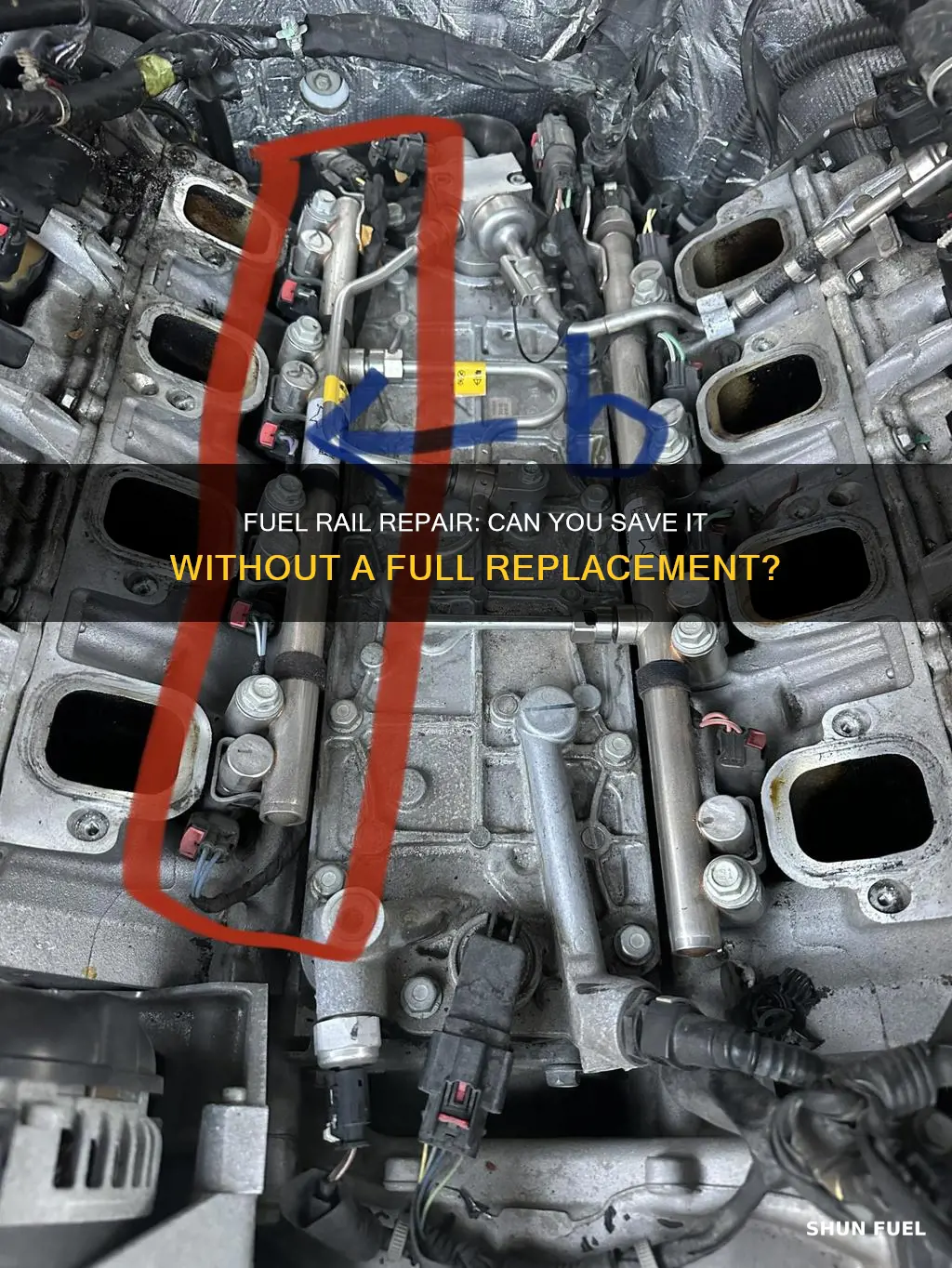
Fixing a fuel rail without replacing it is a common goal for vehicle owners and mechanics alike. A fuel rail, which delivers fuel to the engine, can become damaged or clogged over time due to various factors such as age, poor fuel quality, or engine issues. While replacing the entire fuel rail can be costly and time-consuming, there are several methods to repair it. These methods may include cleaning the fuel rail to remove deposits, replacing faulty fuel injectors or sensors, or even using specialized fuel rail repair kits. This approach can save money and extend the life of the vehicle, making it an attractive option for those looking to maintain their vehicles without incurring significant expenses.
What You'll Learn
- Fuel Rail Clogging: Use a fuel line cleaner to remove debris and restore pressure
- Leak Repair: Identify and fix leaks with sealant or replacement of damaged parts
- Pressure Regulation: Adjust the fuel pump or regulator to maintain optimal pressure
- Hose Inspection: Check hoses for cracks, leaks, or damage and replace if necessary
- Sensor Calibration: Calibrate fuel pressure sensors to ensure accurate readings and performance
Fuel Rail Clogging: Use a fuel line cleaner to remove debris and restore pressure
Fuel rail clogging can be a common issue that affects engine performance and fuel efficiency. Over time, debris, contaminants, and varnish can accumulate in the fuel lines, leading to reduced pressure and potential engine misfires. While replacing the fuel rail is an option, it can be an expensive and time-consuming process. Fortunately, there are several methods to address this problem without replacing the entire fuel rail. One effective approach is to use a fuel line cleaner, which can help remove the accumulated debris and restore optimal fuel pressure.
Fuel line cleaners are designed to dissolve and remove contaminants, such as varnish, sludge, and water, that can build up inside the fuel lines. These cleaners typically come in concentrated liquid form and are applied directly to the fuel lines. Before using the cleaner, it is essential to ensure that the engine is off and the vehicle is in a safe position to prevent any accidental starting. Start by locating the fuel lines, which are usually found under the hood, and identify the fuel rail, a metal component that connects the fuel injectors to the engine.
Connect a fuel pressure gauge to the fuel rail to measure the current pressure. This step is crucial to determine the extent of the clogging and to monitor the improvement after cleaning. Once the gauge is connected, carefully pour the fuel line cleaner into the fuel tank, following the instructions provided by the manufacturer. Allow the cleaner to circulate through the fuel system for the recommended duration, which may vary depending on the product. During this time, the cleaner will work to dissolve and loosen the debris within the fuel lines.
After the specified time has passed, disconnect the fuel pressure gauge and recheck the pressure. If the pressure has increased significantly, it indicates that the cleaner has effectively removed the debris. However, if the pressure remains low or shows no improvement, further investigation or professional assistance may be required. It is important to note that while fuel line cleaners can be effective, they may not completely eliminate all clogs, especially in severe cases. In such instances, seeking professional help to replace the fuel rail might be necessary.
In summary, addressing fuel rail clogging without replacing the entire assembly is possible through the use of fuel line cleaners. This method can help restore fuel pressure and improve engine performance. By following the instructions provided with the cleaner and monitoring the fuel pressure, vehicle owners can effectively tackle this issue and potentially avoid costly repairs. Regular maintenance and the use of fuel additives can also contribute to preventing future clogs and ensuring optimal engine operation.
Replacing Fuel Pump in 2003 Envoy: Step-by-Step Guide
You may want to see also
Leak Repair: Identify and fix leaks with sealant or replacement of damaged parts
When dealing with a fuel rail leak, it's important to identify the source of the issue before attempting any repairs. Fuel rail leaks can be caused by various factors, such as worn-out gaskets, cracked hoses, or damaged fuel injectors. The first step is to inspect the fuel rail and its components thoroughly. Look for any visible signs of damage, such as cracks, corrosion, or dislodged parts. Pay close attention to the connections and seals, as these areas are prone to leaks.
If the leak is due to a small crack or a minor issue with the sealant, a simple solution is to use a high-quality fuel rail sealant. These sealants are designed to create a tight seal and prevent fuel leaks. Clean the affected area, ensuring it is dry and free of debris. Apply the sealant according to the manufacturer's instructions, making sure to cover the entire damaged area. Allow sufficient time for the sealant to cure, and then test the fuel rail for any remaining leaks.
In some cases, the leak might be more severe, requiring the replacement of damaged parts. For instance, if the fuel rail has a cracked hose or a damaged injector, it is best to replace these components. Start by disconnecting the fuel lines and hoses carefully, ensuring you have the necessary tools and knowledge to avoid any further damage. Inspect the fuel injectors for any signs of wear or damage, and consider replacing them if they are beyond repair. When replacing parts, ensure you use genuine or high-quality aftermarket replacements to guarantee compatibility and performance.
After replacing any necessary parts, reattach the fuel lines and hoses securely. Double-check all connections to ensure they are tight and properly sealed. Test the fuel rail system to ensure there are no further leaks. It is crucial to follow the manufacturer's guidelines for any specific procedures or pressure tests that may be required after repairs.
Remember, while it is possible to fix fuel rail leaks without replacing the entire rail, it is essential to address the root cause of the leak. Proper identification and repair techniques can save time and money, ensuring your vehicle's fuel system operates efficiently and safely. Always exercise caution when working on fuel-related components, and if you are unsure, consult a professional mechanic.
Replacing Fuel Injector in Ford 9700 Tractor: Step-by-Step Guide
You may want to see also
Pressure Regulation: Adjust the fuel pump or regulator to maintain optimal pressure
When dealing with fuel rail issues, one common solution that often arises is adjusting the fuel pump or regulator to ensure optimal pressure. This approach can be a cost-effective way to address problems without replacing the entire fuel rail assembly. Here's a detailed guide on how to tackle this:
Identifying the Problem: Before making any adjustments, it's crucial to identify the root cause of the fuel rail issue. Low fuel pressure is a common symptom that can be caused by various factors. It could be due to a faulty fuel pump, a clogged filter, or even a malfunctioning regulator. Inspect the fuel system for any visible signs of damage or blockages.
Fuel Pump Inspection: Start by checking the fuel pump, which is responsible for creating the necessary pressure to deliver fuel to the engine. If the pump is weak or failing, it might not be able to generate the required pressure. You can test the pump's performance using a fuel pressure gauge. If the pressure reading is significantly lower than the recommended range, you may need to replace the pump. However, if the pump is functioning adequately, proceed to the next step.
Regulator Adjustment: The fuel regulator is a critical component that controls the pressure of the fuel entering the engine. Over time, regulators can become dirty or malfunction, leading to incorrect pressure settings. To adjust the regulator, locate it and inspect for any signs of contamination or damage. If it appears clean and intact, you can try adjusting the regulator's settings. This process may vary depending on the make and model of your vehicle, so consult the manufacturer's guidelines or seek professional advice for specific instructions.
Maintaining Optimal Pressure: The goal is to achieve the optimal fuel pressure required by your engine. This pressure is typically specified in the vehicle's manual. If the fuel pump is functioning correctly, adjusting the regulator to the correct setting should resolve the issue. Ensure that the fuel pressure gauge reads within the recommended range for your engine. Regularly monitoring and maintaining this pressure will help prevent further problems and ensure efficient engine operation.
Remember, while adjusting the fuel pump or regulator can be a viable solution, it requires careful diagnosis and technical knowledge. If you're unsure about any step, it's best to consult a professional mechanic who can provide guidance tailored to your specific vehicle.
Replacing Fuel Lines: A 91 Sportster Guide
You may want to see also
Hose Inspection: Check hoses for cracks, leaks, or damage and replace if necessary
When it comes to maintaining a fuel rail system, one crucial aspect often overlooked is the inspection and care of the hoses. These hoses play a vital role in transporting fuel from the tank to the engine, and any damage or malfunction can lead to significant performance issues. Here's a comprehensive guide on how to inspect and address hose-related problems without resorting to a full replacement.
Start by visually inspecting the hoses for any visible signs of wear and tear. Look for cracks, tears, or any form of damage along the length of the hose. Over time, hoses can degrade due to heat, fuel contamination, or general wear, making them susceptible to cracks. These cracks may not always be visible to the naked eye, so it's essential to be thorough. Check for any signs of fuel leakage around the hose connections and fittings. Even a small leak can lead to engine misfires and reduced performance. If you notice any fuel residue or wet spots around the hose, it could indicate a potential issue.
The next step is to feel the hoses for any unusual resistance or flexibility. Hoses should be flexible enough to accommodate engine movement without restricting fuel flow. If you encounter stiff or rigid hoses, it might indicate internal damage or blockages. Additionally, listen for any hissing or bubbling sounds near the hose connections, which could suggest a fuel leak or air bubble within the hose.
If you identify any cracks, leaks, or damage during your inspection, it's crucial to take immediate action. Start by cleaning the affected area to ensure a proper repair. You can use a hose cleaner or a mild detergent to remove any fuel residue. Once cleaned, inspect the hose further to determine the extent of the damage. For minor cracks or small leaks, you might be able to repair the hose using a specialized hose repair kit. These kits typically include a sealant or adhesive that can be applied to the damaged area to seal it. However, for more severe damage, it is often best to replace the hose entirely to avoid potential fuel leaks and engine issues.
Regular maintenance and inspections are key to keeping your fuel rail system in optimal condition. By checking the hoses for cracks, leaks, and damage, you can identify and rectify issues before they escalate. Remember, while some hose repairs can be temporary solutions, it is always advisable to replace hoses that show significant wear or damage to ensure the long-term reliability of your engine.
Replacing the Fuel Pump in Your Commodore Ute
You may want to see also
Sensor Calibration: Calibrate fuel pressure sensors to ensure accurate readings and performance
Sensor calibration is a crucial process in maintaining the performance and accuracy of fuel pressure sensors in a vehicle's fuel rail system. Over time, these sensors can drift and provide incorrect readings, leading to poor engine performance and potential issues. Calibration ensures that the sensors provide precise data, allowing the engine to operate efficiently and safely. Here's a detailed guide on how to calibrate fuel pressure sensors:
Understanding the Sensors: Begin by familiarizing yourself with the specific fuel pressure sensors in your vehicle. Different car models may have varying sensor types and locations. Typically, these sensors are responsible for measuring the pressure of the fuel in the rail and sending this information to the engine control unit (ECU). Understanding their function is key to successful calibration.
Tools and Equipment: You will need specialized tools for sensor calibration. This includes a fuel pressure gauge, a diagnostic scanner or a handheld calibrator, and possibly a fuel pressure regulator adjustment tool. These tools will help you measure and adjust the sensor's performance accurately. Ensure you have access to a clean, well-lit workspace with good ventilation.
Step-by-Step Calibration Process:
- Preparation: Start by disconnecting the negative battery terminal to prevent any electrical interference during the calibration process. Locate the fuel pressure sensor(s) and their respective wiring harnesses.
- Measurement: Using the fuel pressure gauge, measure the fuel pressure at the rail. Record this baseline reading. Then, disconnect the sensor's wiring harness and temporarily remove it. Measure the pressure again to establish a reference point for calibration.
- Calibration Procedure: Connect the diagnostic scanner or calibrator to the vehicle's OBD-II port. Follow the manufacturer's instructions to initiate the calibration process. This may involve adjusting the sensor's electrical signal or applying a specific voltage/current to the sensor.
- Comparison and Adjustment: Compare the new fuel pressure reading with the baseline measurement. If the readings are significantly different, you may need to adjust the sensor's position, clean or replace the sensor, or fine-tune the calibration settings. Repeat the measurement and calibration process until you achieve accurate readings.
- Reinstallation: Once calibrated, reattach the sensor and secure it in place. Reconnect the wiring harness and ensure all connections are tight and secure.
Important Considerations:
- Always refer to the vehicle's service manual for specific sensor locations and calibration procedures.
- Calibration should be performed in a controlled environment to ensure accurate results.
- If you encounter persistent issues or the sensor readings remain inaccurate, further investigation or professional assistance may be required.
- Regular sensor maintenance and calibration can prevent potential engine problems and ensure optimal fuel system performance.
By following these steps, you can effectively calibrate fuel pressure sensors, ensuring they provide accurate readings and contribute to the overall reliability of your vehicle's fuel rail system.
Replacing 2001 F150 Fuel Filter: Step-by-Step Guide
You may want to see also
Frequently asked questions
Yes, it is possible to repair a fuel rail without a full replacement. Common issues like cracks, leaks, or blockages can often be addressed by replacing individual components such as the fuel injectors, fixing the rail's housing, or using specialized sealants and coatings to restore its integrity.
Look out for symptoms like erratic engine performance, hard starts, poor fuel efficiency, and engine misfires. These issues may be caused by a faulty fuel rail, but they could also stem from other problems. A professional diagnosis is recommended to identify the exact cause.
While some minor issues can be tackled by experienced DIY enthusiasts, most fuel rail repairs are best left to professionals. Specialized tools and knowledge are often required to access and fix the rail effectively. It's crucial to ensure proper installation and functionality to avoid further complications.