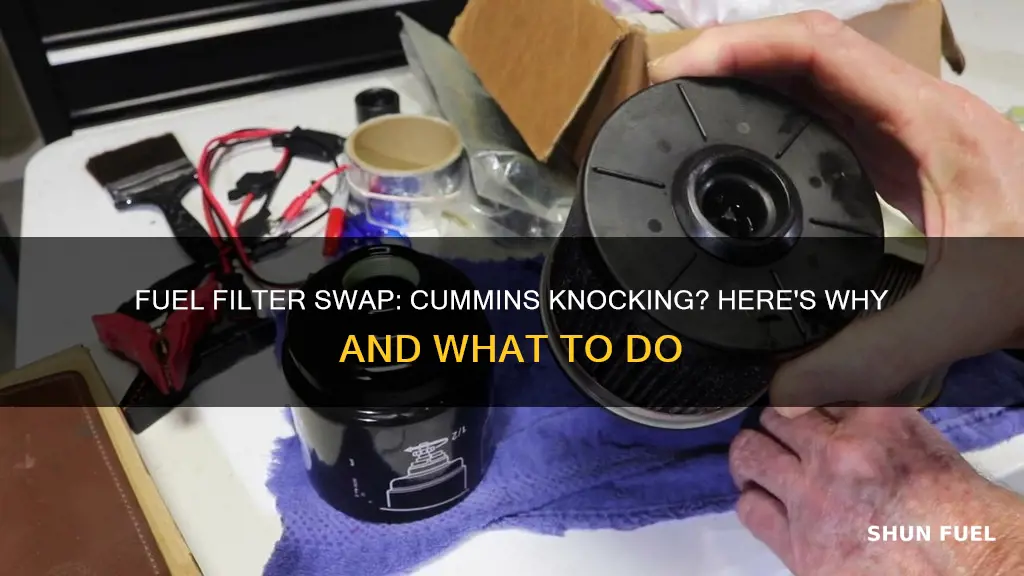
Replacing a fuel filter in a Cummins engine can be a routine maintenance task, but it's important to understand the potential consequences. While a new filter can improve fuel flow and engine performance, it's not uncommon for some owners to experience engine knocking or pinging after the replacement. This phenomenon can occur due to several factors, including incorrect filter installation, using a filter with the wrong specifications, or underlying engine issues that were not addressed during the maintenance. Understanding these potential causes can help Cummins engine owners troubleshoot and resolve any knocking issues that may arise after replacing the fuel filter.
Characteristics | Values |
---|---|
Potential Cause of Knocking | Replacing the fuel filter alone is unlikely to cause knocking in a Cummins engine. Knocking is usually related to other issues. |
Fuel Filter's Role | The fuel filter's primary function is to remove contaminants from the fuel, ensuring clean fuel delivery to the engine. |
Common Knocking Causes | Knocking can be caused by: - Incorrect fuel injection timing - Insufficient fuel pressure - Engine misfires - Overheating - Low engine oil level - Faulty spark plugs or ignition system |
Fuel Filter Replacement Benefits | Replacing a clogged or old fuel filter can improve engine performance and fuel efficiency, but it doesn't directly prevent knocking. |
Diagnosis | If you suspect knocking, a thorough diagnosis is necessary. This may involve checking fuel pressure, spark plugs, engine sensors, and other components. |
What You'll Learn
- Fuel Filter Replacement: Replacing the fuel filter may not directly cause knocking
- Engine Misfire: Knocking can be a symptom of engine misfire, unrelated to filter
- Fuel System Issues: Problems with fuel injectors or pumps can cause knocking
- Engine Design: Cummins engines have specific design considerations that affect knocking
- Maintenance and Diagnostics: Regular maintenance and proper diagnostics can prevent knocking
Fuel Filter Replacement: Replacing the fuel filter may not directly cause knocking
Replacing the fuel filter in a Cummins engine is a routine maintenance task that can help ensure optimal performance and longevity. While it is a relatively simple process, there are some common misconceptions about its impact on engine operation, particularly regarding knocking or pinging sounds. Here's an explanation to clarify why replacing the fuel filter may not directly cause knocking in a Cummins engine.
Knocking in an engine is typically associated with premature combustion, often due to issues like incorrect fuel injection timing, low-quality fuel, or engine wear. It is not a direct result of replacing the fuel filter. The fuel filter's primary function is to remove contaminants from the fuel, ensuring that only clean, debris-free fuel reaches the engine's injectors. While a clogged or dirty fuel filter can lead to reduced engine performance and potential issues, it does not directly cause knocking.
When a fuel filter is replaced, it is essential to use the correct type and size of filter recommended by the manufacturer. Using an incorrect filter or one of lower quality can potentially introduce new problems. However, as long as the replacement is done correctly, it should not introduce any issues related to knocking. The new filter will simply provide cleaner fuel, which can improve overall engine operation and potentially reduce the likelihood of knocking due to fuel-related problems.
In some cases, if the engine has been running poorly or has experienced knocking before the filter replacement, the new filter can help alleviate these issues. By ensuring a steady supply of clean fuel, the filter can help stabilize engine operation. However, it is crucial to address any underlying causes of knocking, such as engine misfires or fuel system malfunctions, to completely resolve the problem.
In summary, replacing the fuel filter in a Cummins engine is a standard maintenance procedure that should not directly cause knocking. While it can improve engine performance by providing cleaner fuel, it is essential to focus on other potential causes of knocking and ensure proper engine maintenance to address any persistent issues. Regular filter replacement is a preventative measure that contributes to the overall health and reliability of the Cummins engine.
Replacing Fuel Injector Parts: A Step-by-Step Guide for Beginners
You may want to see also
Engine Misfire: Knocking can be a symptom of engine misfire, unrelated to filter
Knocking in a Cummins engine can be a concerning issue, often associated with engine misfire. This symptom can occur even if the fuel filter has been recently replaced, indicating that the problem is not solely related to the filter. Engine misfire happens when a cylinder fails to ignite the air-fuel mixture properly, resulting in a lack of power, reduced performance, and potentially causing the engine to knock. This can be caused by various factors, including issues with the spark plugs, ignition coils, fuel injectors, or even internal engine components.
One common cause of engine misfire is a faulty spark plug. Spark plugs play a critical role in igniting the air-fuel mixture, and if they are worn out, damaged, or contaminated, the engine may struggle to start or run efficiently. Over time, spark plugs can accumulate deposits or corrosion, leading to misfires. It is essential to inspect and replace spark plugs regularly to ensure optimal engine performance.
Ignition coils are another crucial component in the ignition system. These coils amplify the battery voltage to create a high-voltage spark required for combustion. If an ignition coil fails, it can result in a misfire, causing the engine to knock. Symptoms of a failing ignition coil may include a misfire under load, rough idling, or a noticeable decrease in engine power. Replacing the faulty coil can often resolve the issue.
Fuel injectors are responsible for delivering the precise amount of fuel required for combustion. Clogged or malfunctioning fuel injectors can lead to improper fuel delivery, causing engine misfire. This can be due to various factors, such as contaminated fuel, old or faulty injectors, or issues with the fuel pump. Regular fuel filter maintenance and checking for any signs of contamination are essential to prevent fuel-related misfires.
In some cases, engine misfire can be attributed to internal engine problems. Wear and tear on engine components like valves, piston rings, or cylinder walls can lead to improper combustion, resulting in knocking. Additionally, issues with the engine's timing system, such as a faulty camshaft or crankshaft sensor, can cause misfires. Diagnosing and addressing these internal engine problems may require specialized tools and expertise.
When dealing with a Cummins engine that is knocking, it is crucial to identify the root cause of the misfire. While replacing the fuel filter can be a part of the maintenance routine, it is essential to consider other potential issues. Conducting a thorough inspection of the spark plugs, ignition coils, fuel injectors, and internal engine components can help pinpoint the exact cause of the knocking. Addressing the specific issue will ensure the engine operates optimally and prevents further complications.
Fuel Pump Replacement: 2007 Maxima Cost Guide
You may want to see also
Fuel System Issues: Problems with fuel injectors or pumps can cause knocking
Knocking in a Cummins engine can be a result of various issues, and fuel system problems are a common culprit. When it comes to fuel injectors and pumps, several factors can contribute to this issue. Firstly, fuel injectors play a crucial role in delivering the correct amount of fuel to the engine at the right time. If these injectors are malfunctioning, they may not be able to spray the fuel accurately, leading to improper combustion and potential knocking sounds. This can happen due to several reasons, such as clogged or worn-out injectors, faulty wiring, or even a malfunctioning control module that regulates the fuel injection process.
The fuel pump is another critical component in the fuel system. Its primary function is to deliver fuel from the tank to the engine at the required pressure. If the fuel pump is not functioning correctly, it might not provide the necessary pressure, resulting in poor fuel delivery. This can cause the engine to run lean, where there is an insufficient amount of fuel compared to the air in the cylinders, leading to knocking. Over time, the pump can become worn out due to constant operation, leading to reduced performance and potential fuel delivery issues.
In some cases, the problem might originate from the fuel pressure regulator. This component controls the pressure of the fuel entering the engine. If it is faulty, it may not regulate the pressure correctly, causing an imbalance in the fuel-air mixture. As a result, the engine may run too rich (excessive fuel) or too lean (insufficient fuel), both of which can trigger knocking. Regular maintenance and inspection of these fuel system components are essential to prevent such issues.
To address knocking, it is recommended to inspect the fuel injectors for any signs of damage or clogging. Cleaning or replacing faulty injectors can often resolve the problem. Additionally, checking the fuel pump's performance and replacing it if necessary can ensure proper fuel delivery. It is also advisable to inspect the fuel pressure regulator and other related components to identify any potential issues. By addressing these fuel system problems, you can effectively mitigate knocking in a Cummins engine.
Replacing Envoy Fuel Filter: Step-by-Step Guide for DIYers
You may want to see also
Engine Design: Cummins engines have specific design considerations that affect knocking
Cummins engines are renowned for their robust and powerful performance, but like any complex mechanical system, they can experience issues related to engine knocking, which is a result of premature combustion within the cylinders. This phenomenon can be influenced by various factors, including engine design considerations specific to Cummins engines. Understanding these design aspects is crucial for mechanics and enthusiasts alike to ensure optimal performance and longevity.
One critical design factor is the engine's compression ratio. Cummins engines often feature a high compression ratio, which is a measure of the volume within the cylinder before the piston is fully compressed. This design choice allows for efficient combustion and high power output. However, a higher compression ratio also means that the air-fuel mixture must be carefully managed to avoid knocking. The fuel injection system in Cummins engines is designed to precisely control the amount of fuel introduced into the combustion chamber, ensuring optimal combustion without excessive fuel that could lead to knocking.
Another design consideration is the engine's cylinder head and valve train. Cummins engines typically employ a unique cylinder head design with specific valve configurations. These valves play a vital role in controlling the airflow into the engine and the exhaust of combustion gases. Proper valve timing and lift are essential to ensure efficient combustion and prevent knocking. Any modifications or issues with the valve train can disrupt this delicate balance, potentially leading to engine knocking.
Additionally, the engine's cooling system is a critical design feature that impacts knocking. Cummins engines are known for their robust cooling systems, often featuring large radiators and efficient cooling fluids. Adequate cooling is essential to maintain optimal engine temperatures, as excessive heat can lead to knocking. The cooling system's design, including the placement of heat exchangers and the flow of coolant, must be carefully considered to ensure the engine operates within safe temperature limits.
Furthermore, the engine's overall weight and balance are important design factors. Cummins engines are often heavy-duty and powerful, and their weight distribution can affect engine behavior. Proper weight distribution ensures that the engine remains stable and balanced during operation, reducing the likelihood of knocking due to excessive vibration or uneven stress on the components.
In summary, Cummins engine design incorporates specific considerations to manage knocking, including compression ratio, fuel injection precision, cylinder head design, cooling system efficiency, and weight distribution. Understanding these design aspects is essential for mechanics and enthusiasts to maintain and modify Cummins engines effectively, ensuring they operate optimally without compromising performance or longevity.
Replacing Fuel Injectors in a 2001 Ford Focus: Step-by-Step Guide
You may want to see also
Maintenance and Diagnostics: Regular maintenance and proper diagnostics can prevent knocking
Regular maintenance and proper diagnostics are crucial for preventing knocking in Cummins engines, which can be caused by various issues, including fuel system problems. Here's how these practices can help:
Routine Maintenance: Cummins engines require regular maintenance to ensure optimal performance and longevity. This includes routine checks and replacements of various components, such as fuel filters, to prevent potential issues. By adhering to the manufacturer's recommended service schedule, you can identify and address minor problems before they escalate. For instance, replacing the fuel filter at the appropriate mileage or time intervals can significantly reduce the risk of knocking. Over time, fuel filters can become clogged or damaged, leading to contaminated fuel, which may cause engine knock. Regular maintenance ensures that the fuel system remains clean and efficient, minimizing the chances of this issue.
Diagnostic Checks: Proper diagnostics are essential to identify the root cause of knocking. When an engine knocks, it's a sign of internal engine problems, often related to the fuel system. A comprehensive diagnostic check can reveal issues like faulty injectors, malfunctioning sensors, or even problems with the engine's compression. By using specialized diagnostic tools, technicians can read error codes, analyze sensor data, and pinpoint the exact cause of the knock. This targeted approach allows for precise repairs, ensuring that the underlying issue is resolved. For example, if a diagnostic check reveals a faulty fuel pressure regulator, replacing it can prevent further knocking and potential engine damage.
Preventive Measures: Preventive maintenance and diagnostics are key to avoiding knocking. Regularly inspecting the engine for any signs of wear, damage, or contamination can help identify potential issues early on. This includes checking for fuel leaks, inspecting the condition of fuel lines and injectors, and ensuring proper fuel pressure. By addressing these factors, you can maintain the engine's health and prevent knocking. Additionally, keeping the engine's computer software up-to-date can improve fuel management and combustion efficiency, further reducing the likelihood of knocking.
Expert Advice: It is recommended to consult Cummins engine experts or authorized service centers for maintenance and diagnostic advice. These professionals have the knowledge and tools to perform thorough inspections and provide tailored solutions. They can offer guidance on the specific maintenance tasks required for your Cummins engine, ensuring it receives the care it needs to operate smoothly and reliably. Regular maintenance and proper diagnostics are essential practices that can significantly contribute to the overall health and longevity of your Cummins engine, helping to prevent knocking and other performance issues.
Replacing the Fuel Pump in a Jeep Wrangler (2004)
You may want to see also
Frequently asked questions
Replacing the fuel filter is a common maintenance task that can help improve engine performance and address various issues, including knocking. Over time, the fuel filter can become clogged or contaminated, leading to reduced fuel flow and potential engine problems. By replacing it, you ensure clean fuel delivery, which can help reduce knocking and improve overall engine operation.
Yes, a faulty or clogged fuel filter can definitely contribute to engine knocking. Knocking is often a result of improper combustion, which can be caused by various factors, including fuel-related issues. When the fuel filter is not functioning correctly, it may restrict fuel flow, leading to a lack of proper fuel-air mixture and subsequent engine knock.
While replacing the fuel filter is a good initial step, it might not always be the sole solution to engine knocking. Knocking can have multiple causes, such as engine misfires, faulty injectors, or even issues with the engine's compression. It is essential to diagnose the root cause of the knocking before replacing the fuel filter. If the issue persists after replacing the filter, further investigation and potential repairs or replacements might be required.