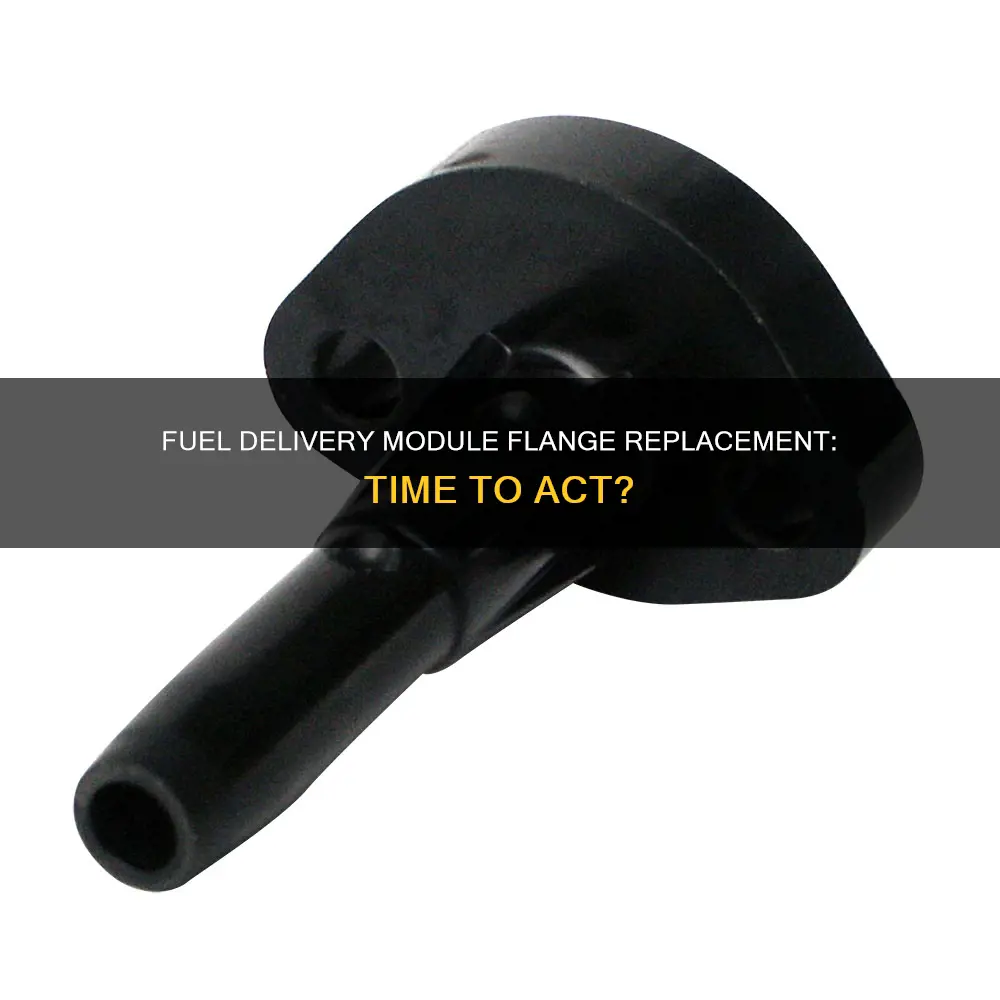
The fuel delivery module flange is a critical component in the fuel system of a vehicle, and its longevity is essential for optimal engine performance. Over time, the flange can wear out due to various factors such as heat, corrosion, and mechanical stress. Understanding the appropriate replacement timeline for this part is crucial for vehicle owners to ensure their engines run efficiently and avoid potential breakdowns. This guide will explore the factors influencing the lifespan of the fuel delivery module flange and provide insights into when and how to replace it.
What You'll Learn
- Diagnosis: Inspect for leaks, corrosion, or damage to the flange
- Tools: Gather necessary tools: wrenches, sockets, and possibly a torque wrench
- Safety: Ensure engine is cool and disconnected from power sources
- Removal: Carefully remove the old flange, following manufacturer's instructions
- Installation: Tighten new flange securely, using correct torque specifications
Diagnosis: Inspect for leaks, corrosion, or damage to the flange
When diagnosing and inspecting the fuel delivery module flange, it is crucial to follow a systematic approach to ensure the issue is accurately identified. The flange is a critical component that connects the fuel pump to the engine, and any damage or malfunction can lead to fuel delivery problems. Here's a detailed guide on how to inspect for leaks, corrosion, or damage:
Visual Inspection: Begin by visually examining the flange and its surrounding areas. Look for any visible signs of damage, such as cracks, warping, or distortion. Inspect the flange's surface for corrosion or rust, especially in areas where it connects to the fuel pump and the engine block. Corrosion can weaken the flange's integrity and lead to leaks. Check for any signs of leakage around the flange's mounting points or connections. Even a small leak can cause significant issues over time.
Leak Detection: To identify leaks, you can use a simple yet effective method. Remove the fuel pump and temporarily disconnect the fuel lines. Apply a small amount of diesel fuel or a suitable leak detection fluid around the flange's connections and mounting points. Observe the area for any signs of fuel seepage or dripping. Even a small amount of fuel escaping indicates a potential leak. If a leak is detected, further investigation is required to determine the cause and extent of the damage.
Corrosion Assessment: Corrosion can be a silent killer for the flange's performance. Inspect the flange for any signs of white or green deposits, which are indicative of corrosion. Pay close attention to the threads and mounting surfaces. Corroded threads can make it difficult to secure the flange properly, leading to potential fuel leaks. If corrosion is present, consider using a rust remover or a wire brush to clean the affected areas. Ensure that all corrosion is removed to prevent further issues.
Damage Evaluation: Carefully examine the flange for any signs of damage that may have been caused by excessive vibration, heat, or previous repairs. Look for any signs of melting, burning, or excessive wear. If the flange shows signs of damage, it might need to be replaced to prevent further complications. In some cases, minor damage can be repaired, but it's essential to assess the extent of the damage before making a decision.
Remember, proper diagnosis is key to determining whether a replacement is necessary. If you notice any leaks, corrosion, or damage during the inspection, it is advisable to consult a professional mechanic or refer to the vehicle's manual for specific guidelines on replacing the fuel delivery module flange.
Replacing Husqvarna Trimmer Fuel Line: A Step-by-Step Guide
You may want to see also
Tools: Gather necessary tools: wrenches, sockets, and possibly a torque wrench
To replace the fuel delivery module flange, it's crucial to have the right tools to ensure a smooth and efficient process. Start by gathering a set of wrenches, including both standard and adjustable types. The flange is typically secured with bolts, so you'll need wrenches that can provide the necessary grip and leverage to loosen and tighten these bolts. A set of sockets is also essential, as the bolts might be of a specific size or type, requiring the appropriate socket to fit and turn them. For example, you might need a 1/2-inch drive socket set, which covers common bolt sizes.
In addition to the standard tools, a torque wrench is a valuable asset. This tool is used to apply a specific amount of torque to the bolts, ensuring they are tightened to the manufacturer's recommended specifications. Over-tightening can damage the flange or surrounding components, while under-tightening can lead to leaks or poor performance. A torque wrench helps you achieve the precise torque value required for a secure and reliable installation.
Consider the size and type of your vehicle's bolts and the flange's design when selecting the appropriate wrenches and sockets. Some vehicles might use metric bolts, while others might have imperial sizes. Ensure you have the right sizes to match the existing hardware. It's also a good idea to keep a variety of socket sizes and types, as different vehicles and flange designs may require unique bolt configurations.
Having the right tools is essential for a successful repair, ensuring that you can work efficiently and effectively without causing further damage. With the necessary tools in hand, you'll be well-prepared to tackle the replacement of the fuel delivery module flange, ensuring a secure and reliable connection.
Refilling Lighter Fluid: A Step-by-Step Guide to Replenishing Fuel
You may want to see also
Safety: Ensure engine is cool and disconnected from power sources
Before attempting any maintenance or repair work on a fuel delivery module, it is crucial to prioritize safety. One of the most important steps is to ensure that the engine is cool and disconnected from power sources. Working on an engine while it is hot can be extremely dangerous and may lead to severe burns or injuries. Therefore, it is essential to allow the engine to cool down completely before proceeding with any repairs.
To ensure the engine is cool, you should park the vehicle in a well-ventilated area and let it idle for a sufficient period. The cooling system's purpose is to regulate the engine's temperature, and it may take some time for the engine to reach a safe operating temperature. Typically, it is recommended to wait for at least 30 minutes to an hour after the engine has stopped before attempting any maintenance tasks. This waiting period allows the engine to cool down and reduces the risk of accidents.
Additionally, it is imperative to disconnect the vehicle from power sources to ensure safety. This includes turning off the ignition switch and removing the key if it is a manual start system. For vehicles with a push-button start or keyless ignition, ensure that the engine is completely shut off. Disconnection from power sources prevents the risk of electrical shocks or accidental starts during the repair process. It is a simple yet vital step that should not be overlooked.
Once the engine is cool and disconnected from power sources, you can proceed with the specific task of replacing the fuel delivery module flange. This may involve removing the old flange, installing a new one, and ensuring proper sealing to prevent fuel leaks. Always follow the manufacturer's guidelines and recommended procedures to ensure a safe and successful repair.
Remember, safety should always be the top priority when working on any vehicle. By ensuring the engine is cool and disconnected from power sources, you create a safe working environment and reduce the potential for accidents or injuries during the replacement of the fuel delivery module flange. This simple yet essential step is a fundamental part of vehicle maintenance and repair.
Replacing the Fuel Pump in Your Hyundai Elantra: Step-by-Step Guide
You may want to see also
Removal: Carefully remove the old flange, following manufacturer's instructions
When it comes to replacing the fuel delivery module flange, the removal process is a crucial step that requires careful attention to detail. Here's a step-by-step guide to ensure a successful removal:
Step 1: Gather the Necessary Tools and Information
Before you begin, make sure you have all the required tools and access to the manufacturer's instructions specific to your vehicle's make and model. This is essential as different vehicles may have unique procedures. The manufacturer's guidelines will provide valuable insights into the correct sequence of removal and any specific requirements.
Step 2: Locate the Old Flange
Identify the fuel delivery module flange you intend to replace. This component is typically located near the fuel injectors or the fuel pump, depending on your vehicle's design. Carefully inspect the area to locate the flange, ensuring you understand its position and any associated connections or attachments.
Step 3: Disconnect Power and Fuel Lines (if applicable)
In some cases, you may need to disconnect power or fuel lines connected to the flange. This step ensures a safe and efficient removal process. Carefully detach any wires or hoses, taking note of their positions for future reference during reinstallation.
Step 4: Follow the Manufacturer's Instructions
Now, carefully remove the old flange, adhering strictly to the manufacturer's guidelines. This step is critical to ensure you don't damage surrounding components or create any safety hazards. The instructions will likely involve a specific sequence of actions, such as loosening certain bolts or nuts before removing the flange. Take your time and be methodical to avoid any mistakes.
Step 5: Inspect and Prepare for Replacement
Once the old flange is removed, inspect the area for any signs of damage or wear. This inspection will help you determine if further repairs or replacements are necessary. Prepare the new flange by following the manufacturer's recommendations for installation, ensuring it is in good condition and properly aligned.
Remember, each vehicle may have unique requirements, so always refer to the specific instructions provided by the manufacturer. This detailed approach to removal will contribute to a successful replacement process, ensuring your vehicle's fuel delivery system operates optimally.
Replacing Fuel Filter in a 2006 Trailblazer: Step-by-Step Guide
You may want to see also
Installation: Tighten new flange securely, using correct torque specifications
When replacing the fuel delivery module flange, it's crucial to follow the manufacturer's instructions for torque specifications to ensure a secure and reliable installation. The flange is a critical component that connects the fuel delivery module to the engine, and improper tightening can lead to leaks, reduced performance, or even engine damage. Here's a step-by-step guide to tightening the new flange securely:
Locate the Flange Bolts: Start by identifying the bolts that secure the flange to the fuel delivery module. These bolts are typically located at the corners of the flange and may require a specific tool for removal, depending on the vehicle's design. Carefully remove these bolts to access the flange.
Prepare the New Flange: Ensure that the new flange is free of any debris or contaminants. If necessary, clean the flange's surface to provide a smooth and even contact with the fuel delivery module. This step is essential to ensure proper sealing and prevent any potential leaks.
Apply the Correct Torque: Now, it's time to tighten the flange bolts. Refer to your vehicle's service manual or the manufacturer's guidelines for the exact torque specifications. Typically, these bolts are tightened in a sequence, starting from the center and moving outward in a star pattern. This method ensures an even distribution of force and prevents warping or damage to the flange. Use a torque wrench to apply the specified torque value, ensuring that the bolts are tightened to the correct tightness.
Check for Leaks: After tightening the bolts, inspect the flange for any signs of leaks. Visually examine the area around the flange and use a thin piece of paper or a rag to check for any oil or fuel stains. If any leaks are detected, carefully tighten the bolts further or adjust the flange's position as needed.
Final Inspection: Once you've tightened the bolts and checked for leaks, give the engine a brief run to ensure there are no issues. Pay attention to any unusual noises or vibrations during the test drive. If everything appears normal, you've successfully installed the new flange securely, following the correct torque specifications. Remember, proper installation is crucial for the longevity and performance of your fuel delivery system.
Replacing Fuel Injectors in a 2003 Dodge Grand Caravan
You may want to see also
Frequently asked questions
The time required to replace the fuel delivery module flange can vary depending on several factors, including your mechanical skills, the accessibility of the vehicle, and the availability of the necessary tools and parts. If you are a professional mechanic or have experience with car repairs, it could take around 2-3 hours to complete the task. However, for beginners or those without prior experience, it might take longer, possibly around 3-5 hours or more, as it requires careful disassembly and reassembly of the fuel system.
Replacing the fuel delivery module flange is a task that can be tackled by those with some mechanical knowledge and experience. It involves working with the fuel system, so it's important to have a good understanding of the process and take necessary safety precautions. If you feel confident in your abilities and have the required tools, you can certainly attempt the replacement yourself. However, if you're unsure or lack the necessary skills, it's advisable to consult a professional mechanic who can ensure the job is done correctly and safely.
Yes, there are a few specialized tools and equipment that you'll need to replace the fuel delivery module flange. These may include a fuel pump disconnect tool, a fuel line disconnect tool, a torque wrench, and possibly a fuel pressure gauge. Additionally, you will need a new flange and any required gaskets or seals. It's recommended to have these tools readily available before starting the replacement process to ensure a smooth and efficient repair.