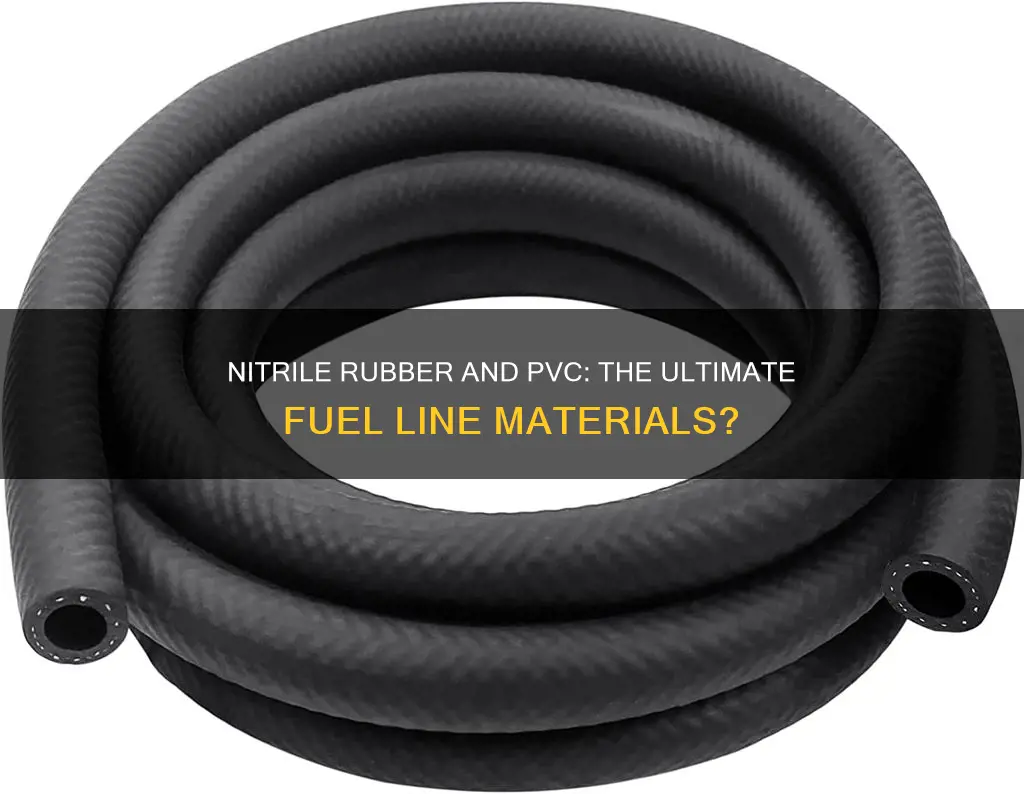
Nitrile rubber and PVC are two common materials used in the manufacturing of fuel lines for vehicles and machinery. While both have their advantages, the question of whether they can be used for fuel lines is an important consideration for engineers and manufacturers. In this paragraph, we will explore the properties of nitrile rubber and PVC and discuss their suitability for fuel line applications, considering factors such as chemical resistance, flexibility, and durability.
Characteristics | Values |
---|---|
Chemical Resistance | Nitrile rubber and PVC can both withstand various chemicals found in fuel, including gasoline, diesel, and aviation fuels. |
Flexibility | These materials offer good flexibility, allowing the fuel lines to bend and move without cracking or breaking. |
Temperature Range | Both nitrile rubber and PVC can handle a wide range of temperatures, making them suitable for fuel lines exposed to varying climates. |
Durability | The materials are known for their durability, ensuring long-lasting performance and resistance to wear and tear. |
Cost-Effectiveness | Nitrile rubber and PVC are relatively inexpensive, making them a cost-effective choice for fuel line applications. |
Availability | These materials are widely available and easily accessible for manufacturing fuel lines. |
Compatibility | They are compatible with the materials used in fuel tanks and engines, ensuring a secure and reliable connection. |
Environmental Impact | PVC may have environmental concerns due to its non-biodegradable nature, while nitrile rubber is a more sustainable option. |
Color | Both can be colored to match the fuel line's purpose and appearance. |
Standard Sizes | Various standard sizes are available to accommodate different fuel line requirements. |
What You'll Learn
- Chemical Resistance: Nitrile and PVC can withstand fuel chemicals, ensuring durability
- Flexibility: Both materials offer flexibility, crucial for fuel line movement and bending
- Temperature Tolerance: PVC excels in heat resistance, while nitrile handles cold temperatures
- Fuel Compatibility: Nitrile rubber is ideal for gasoline, while PVC is better for diesel
- Cost-Effectiveness: PVC is cheaper, making it a popular choice for fuel lines
Chemical Resistance: Nitrile and PVC can withstand fuel chemicals, ensuring durability
Nitrile rubber and PVC are excellent choices for fuel lines due to their exceptional chemical resistance properties. These materials are specifically designed to withstand the harsh conditions of fuel environments, ensuring the longevity and reliability of the fuel delivery system. When it comes to fuel lines, the primary concern is the compatibility of the materials with the various chemicals present in gasoline, diesel, and other fuels.
Nitrile rubber, a synthetic elastomer, offers remarkable resistance to a wide range of chemicals commonly found in fuels. It can effectively resist the degradation caused by gasoline, diesel, and even aviation fuels. This resistance ensures that the fuel lines remain intact and functional over extended periods, even in the presence of these corrosive substances. The molecular structure of nitrile rubber provides a protective barrier, preventing fuel chemicals from breaking down the material and causing potential leaks or failures.
Similarly, PVC (polyvinyl chloride) is a versatile material known for its chemical stability. It can endure exposure to various fuel chemicals without showing signs of deterioration. PVC's resistance to fuel-related chemicals makes it an ideal candidate for fuel line applications. Its ability to maintain structural integrity under these conditions is crucial for the safe and efficient operation of fuel systems.
The combination of nitrile rubber and PVC offers a powerful solution for fuel line requirements. These materials can withstand the corrosive nature of fuel chemicals, ensuring that the fuel lines remain durable and reliable. This chemical resistance is essential for maintaining the performance and safety of fuel systems, especially in automotive, aviation, and marine applications where fuel lines are constantly exposed to harsh environments.
In summary, nitrile rubber and PVC are highly suitable materials for fuel lines due to their superior chemical resistance. Their ability to resist fuel-related chemicals ensures the long-term durability and functionality of fuel delivery systems, making them essential components in various industries.
Fuel Line Repair: A Step-by-Step Guide for PC800 Owners
You may want to see also
Flexibility: Both materials offer flexibility, crucial for fuel line movement and bending
Nitrile rubber and PVC (polyvinyl chloride) are both excellent choices for fuel lines due to their inherent flexibility, which is a critical factor in ensuring the longevity and reliability of the fuel system. This flexibility is essential to accommodate the various movements and bends that fuel lines may experience within a vehicle's engine compartment.
Nitrile rubber, a synthetic material, is known for its superior flexibility and resilience. It can withstand a wide range of temperatures, making it ideal for fuel lines that may be exposed to varying climate conditions. The material's ability to bend and stretch without permanent deformation is crucial for fuel lines, as they often need to navigate through tight spaces and make sharp turns. This flexibility also reduces the risk of cracking or breaking, ensuring a longer-lasting fuel line.
PVC, on the other hand, offers its own set of advantages in terms of flexibility. While it may not be as temperature-resistant as nitrile rubber, it is still a viable option for fuel lines. PVC's flexibility allows it to conform to the shape of the fuel line's path, providing a secure and reliable connection. This material is also lightweight, which can be beneficial for fuel lines as it reduces the overall weight of the system, minimizing stress on the fuel lines during vehicle operation.
The flexibility of both nitrile rubber and PVC is particularly important in fuel lines because it allows for easy installation and maintenance. Fuel lines need to be routed through various engine components, and their flexibility ensures that they can be manipulated into the required positions without causing damage to the vehicle's internal structures. Additionally, this flexibility reduces the likelihood of fuel leaks, as the lines can move and adjust without putting excessive strain on the connections.
In summary, the flexibility of nitrile rubber and PVC is a key reason why they are well-suited for fuel line applications. This property ensures that fuel lines can withstand the physical demands of the engine environment, providing a reliable and long-lasting solution for fuel delivery. When selecting a material for fuel lines, considering the flexibility offered by these materials is essential to guarantee optimal performance and safety.
Optimizing Performance: Choosing the Right Fuel Line for Your 50 HP Outboard
You may want to see also
Temperature Tolerance: PVC excels in heat resistance, while nitrile handles cold temperatures
When considering the use of materials for fuel lines, temperature tolerance is a critical factor to ensure the safety and efficiency of the system. Here's an analysis of how PVC and nitrile rubber perform in this regard:
PVC's Heat Resistance: PVC, or polyvinyl chloride, is renowned for its excellent heat resistance properties. It can withstand relatively high temperatures, making it a popular choice for various applications, including fuel lines. In automotive and industrial settings, fuel lines often operate at elevated temperatures due to the engine's heat. PVC's ability to maintain its structural integrity and flexibility at these temperatures is a significant advantage. It ensures that the fuel lines remain pliable and resistant to cracking or degradation, even when exposed to hot engine components. This heat tolerance is particularly beneficial in preventing fuel leaks and maintaining the overall reliability of the fuel system.
Nitrile's Cold Temperature Performance: In contrast, nitrile rubber, a type of synthetic rubber, excels in handling cold temperatures. Nitrile is known for its excellent low-temperature flexibility, which is crucial for fuel lines operating in colder environments. When fuel lines are exposed to freezing temperatures, nitrile's ability to remain flexible prevents brittleness and cracking. This is essential to maintain the integrity of the fuel system, especially in regions with harsh winters. Nitrile's performance in cold temperatures ensures that the fuel lines can withstand the rigors of winter without compromising their functionality.
The combination of PVC's heat resistance and nitrile's cold temperature performance makes them an ideal pair for fuel line applications. While PVC provides reliability in hot environments, nitrile ensures the system's longevity in colder conditions. This temperature tolerance is a key consideration for engineers and designers, as it directly impacts the overall performance and safety of the fuel line system. Understanding these material properties allows for informed decisions when selecting the right materials for specific temperature-challenging environments.
Fuel Line Leaks: Spotting the Signs and What to Do
You may want to see also
Fuel Compatibility: Nitrile rubber is ideal for gasoline, while PVC is better for diesel
Nitrile rubber and PVC are both commonly used materials in fuel lines, but their suitability depends on the type of fuel being transported. When it comes to fuel compatibility, nitrile rubber is generally considered ideal for gasoline applications. This is because nitrile rubber has excellent resistance to gasoline's volatile nature, which includes its ability to dissolve certain types of rubber over time. Nitrile rubber's chemical structure allows it to withstand the corrosive effects of gasoline, making it a reliable choice for fuel lines in vehicles that run on this type of fuel.
On the other hand, PVC (polyvinyl chloride) is often preferred for diesel fuel lines. Diesel fuel has a higher boiling point and contains additives that can be more aggressive compared to gasoline. PVC's chemical inertness and resistance to heat make it a better option for withstanding the challenges posed by diesel fuel. It can handle the higher temperatures and chemical properties of diesel, ensuring a longer lifespan for the fuel lines.
The choice between nitrile rubber and PVC for fuel lines is crucial to ensure the safe and efficient operation of vehicles. For gasoline-powered engines, nitrile rubber provides the necessary protection against the dissolving effects of the fuel, while for diesel engines, PVC offers the required heat resistance and chemical stability. Understanding the specific requirements of the fuel type is essential to select the appropriate material for fuel lines, ensuring optimal performance and longevity of the vehicle's fuel system.
In summary, while both materials have their advantages, nitrile rubber and PVC are chosen based on the fuel's characteristics. Nitrile rubber excels in gasoline applications due to its resistance to gasoline's volatile nature, whereas PVC is the preferred choice for diesel fuel lines because of its ability to handle higher temperatures and chemical properties. This knowledge ensures that fuel lines are compatible with the fuel they carry, promoting safer and more efficient vehicle operations.
Unraveling the Mystery: What's Beneath the Fuel Line in Elite: Dangerous
You may want to see also
Cost-Effectiveness: PVC is cheaper, making it a popular choice for fuel lines
When considering the use of materials for fuel lines, cost-effectiveness is a critical factor, especially for automotive and industrial applications. Among the various options available, PVC (polyvinyl chloride) stands out as a highly cost-effective choice. This is primarily due to its relatively low production and procurement costs compared to other materials like nitrile rubber.
The affordability of PVC is a significant advantage, especially for projects with tight budgets or those requiring large quantities of fuel lines. Its cost-effectiveness is further enhanced by the ease of manufacturing, which allows for efficient production processes and reduced material waste. This efficiency in production translates to lower overall costs, making PVC an attractive option for both manufacturers and consumers.
In the automotive industry, where fuel lines are essential for delivering fuel from the tank to the engine, cost is a major consideration. PVC's affordability ensures that vehicle manufacturers can incorporate high-quality fuel lines without significantly increasing the vehicle's price. This is particularly important in mass production, where keeping costs low is crucial for competitiveness.
Additionally, the durability of PVC fuel lines is often comparable to that of nitrile rubber, which further justifies its cost-effectiveness. PVC can withstand the corrosive effects of fuel and the stresses of everyday use, ensuring a long service life. This durability means that while PVC may be cheaper upfront, it can still provide reliable performance over an extended period, making it a sustainable and cost-efficient choice.
In conclusion, the cost-effectiveness of PVC is a key factor in its widespread use for fuel lines. Its affordability, combined with its durability and ease of manufacturing, makes it an ideal material for applications where cost is a primary concern without compromising on quality and performance. This balance of cost and reliability is what makes PVC a popular and practical choice in various industries.
Optimizing Fuel Delivery: Choosing the Right Size Fuel Line for LO206 Engines
You may want to see also
Frequently asked questions
Yes, both nitrile rubber and PVC can be used for fuel lines, but there are some important considerations to keep in mind. Nitrile rubber is a popular choice for fuel lines due to its excellent resistance to fuel oils, gasoline, and other petroleum-based products. It is known for its durability and flexibility, making it suitable for a wide range of temperatures and fuel types. PVC, or polyvinyl chloride, is also commonly used for fuel lines, especially in automotive applications. It is lightweight, easy to install, and offers good chemical resistance, making it a cost-effective option. However, it is important to note that PVC may not be as flexible as nitrile rubber, and it can become brittle over time, especially in low-temperature conditions.
Nitrile rubber offers several advantages for fuel line applications. Firstly, it has superior resistance to fuel oils, gasoline, and other petroleum-based products, ensuring that the fuel lines remain intact and leak-free over time. This material is also known for its excellent flexibility, allowing it to withstand temperature variations without becoming brittle. Nitrile rubber can be used in a wide range of temperatures, making it suitable for both hot and cold climates. Additionally, it is resistant to UV radiation, which is beneficial for outdoor applications.
While PVC is a viable option for fuel lines, it does have some limitations. One of the main disadvantages is its lower flexibility compared to nitrile rubber. PVC can become stiff and brittle, especially in low-temperature environments, which may lead to cracking or breaking over time. This can result in fuel leaks and potential safety hazards. Additionally, PVC may not be as resistant to certain types of fuels, such as high-octane gasoline or ethanol blends, which can cause degradation and reduce the lifespan of the fuel lines.
Choosing the right material for fuel lines depends on various factors, including the type of fuel used, operating temperatures, and environmental conditions. If you are dealing with petroleum-based fuels and require high flexibility and durability, nitrile rubber is an excellent choice. It provides superior resistance to fuel oils and gasoline. On the other hand, if you are working with a wide range of temperatures and need a lightweight, cost-effective solution, PVC can be a suitable option. However, it is crucial to consider the specific requirements of your application and consult with industry experts or manufacturers to ensure the chosen material meets the necessary standards and regulations.