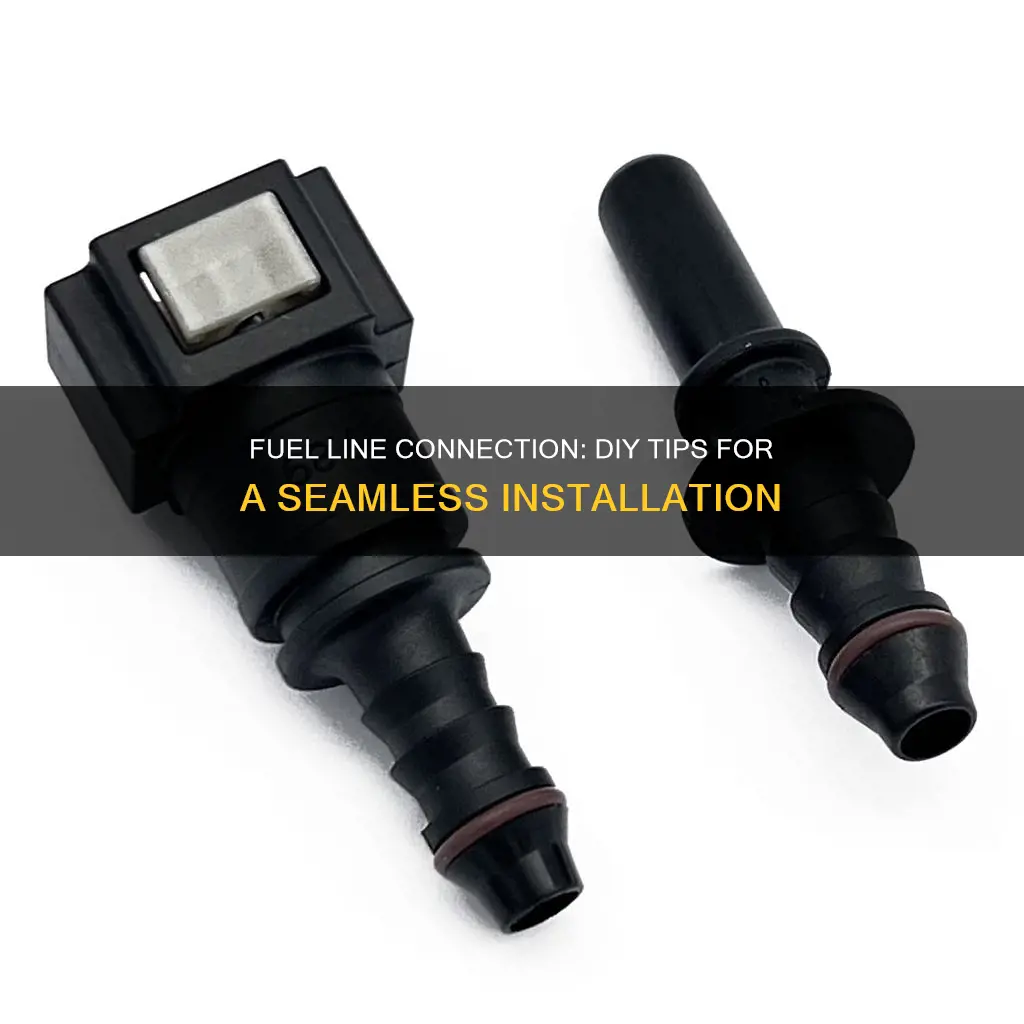
Connecting a fuel line without a connector can be a challenging task, but it is possible with the right tools and knowledge. While using a connector is the most common and recommended method for fuel line installation, there are situations where bypassing the connector might be necessary. This could be due to specific vehicle requirements, limited space, or the need for a custom setup. However, it's crucial to understand the potential risks and legal implications of bypassing the connector, as it may compromise the safety and efficiency of the fuel system. This paragraph introduces the topic by highlighting the potential reasons for considering this unconventional approach while emphasizing the importance of careful consideration and adherence to safety standards.
Characteristics | Values |
---|---|
Safety | Connecting a fuel line without a proper connector can be dangerous. It may lead to fuel leaks, which can cause fires or explosions. |
Reliability | Without a connector, the fuel line connection is less secure and more prone to coming loose, potentially causing fuel loss and engine issues. |
Maintenance | It can be challenging to access and repair the fuel line if it's not properly connected, making maintenance and troubleshooting more difficult. |
Performance | A secure connector ensures a consistent and controlled flow of fuel, which is crucial for optimal engine performance and fuel efficiency. |
Legal Considerations | In some regions, modifying fuel lines without proper connectors might be against regulations, leading to legal issues. |
Longevity | Proper connectors help protect the fuel line from damage, ensuring its longevity and reducing the risk of premature wear and tear. |
Cost | While a connector might add a small cost, it is a worthwhile investment to ensure safety and proper engine function. |
What You'll Learn
- Fuel Line Material: Choose the right material for your fuel line, considering compatibility and durability
- Fitting Types: Understand different fuel line connectors and fittings to ensure proper installation
- Pressure Testing: Test the fuel line for leaks after connecting to ensure a secure seal
- Fuel Line Routing: Route the fuel line safely, avoiding sharp bends and potential damage
- Fuel Pump Compatibility: Ensure the fuel pump is compatible with the fuel line size and pressure
Fuel Line Material: Choose the right material for your fuel line, considering compatibility and durability
When it comes to choosing the right material for your fuel line, compatibility and durability are key factors to ensure a safe and efficient fuel delivery system. The material you select should be able to withstand the harsh conditions of fuel transport, including temperature variations, pressure, and chemical resistance. Here's a detailed guide to help you make an informed decision:
- Rubber or Synthetic Materials: Rubber is a traditional and widely used material for fuel lines due to its flexibility and resilience. Natural rubber or synthetic compounds like neoprene or butyl rubber are excellent choices. These materials offer good resistance to fuel degradation and can handle a range of temperatures. Look for fuel lines made from these compounds, especially if your vehicle operates in extreme weather conditions. For example, neoprene fuel lines are known for their ability to resist fuel leaks and provide a long-lasting solution.
- Reinforced Rubber: For high-performance applications, consider reinforced rubber fuel lines. These lines are constructed with a layer of fabric or steel wire reinforcement, providing added strength and flexibility. This design makes them less prone to damage from sharp edges or vibrations, ensuring a longer lifespan. Reinforced rubber is often used in racing or modified vehicles where fuel line durability is critical.
- Braided Steel or Stainless Steel: If you're seeking the ultimate in durability, braided steel or stainless steel fuel lines are the way to go. These materials offer exceptional resistance to fuel leaks and can withstand extreme temperatures and pressure. Braided steel lines are flexible and less prone to kinking, making them ideal for high-performance vehicles. Stainless steel, being more expensive, provides superior corrosion resistance, ensuring a long-lasting and reliable fuel supply.
- Compatibility Considerations: It's crucial to choose a material that is compatible with the type of fuel your vehicle uses. Different fuels have varying chemical compositions, and some materials may degrade or become brittle over time when exposed to certain fuels. Always refer to your vehicle's manual or consult experts to determine the recommended fuel line material for your specific engine and fuel type.
- Installation and Maintenance: Proper installation is essential to ensure the longevity of your fuel line. Follow manufacturer guidelines and consider using fuel line connectors or fittings that match the chosen material. Regular maintenance, such as checking for cracks, brittleness, or fuel leaks, will also contribute to the overall durability of the fuel system.
Remember, the choice of fuel line material depends on various factors, including your vehicle's requirements, operating conditions, and personal preferences. By selecting the right material, you can ensure a reliable and safe fuel supply, optimizing your vehicle's performance and longevity.
Understanding Snowmobile Fuel Lines: Inside the Gas Tank
You may want to see also
Fitting Types: Understand different fuel line connectors and fittings to ensure proper installation
When it comes to connecting fuel lines, understanding the various fitting types is crucial to ensure a secure and reliable installation. Fuel lines are an essential component of any vehicle's fuel system, and proper connections are vital to prevent leaks and ensure optimal performance. Here's an overview of different fuel line connectors and fittings:
- Quick-Connect Fittings: These fittings are designed for easy and quick installations. They typically feature a male end with a threaded or bayonet-style connector that mates with a female port on the fuel line. Quick-connect fittings are commonly used in automotive applications due to their convenience. They often include a locking mechanism to ensure a tight seal, preventing fuel leakage. When using these fittings, ensure that the male and female ends align properly and that the locking feature is engaged to secure the connection.
- Compression Fittings: Compression fittings are another popular choice for fuel line connections. They involve inserting a fuel line into a fitting with a compression nut and ferrule. The ferrule is made of a hard, durable material that compresses around the fuel line, creating a tight seal. This type of fitting requires careful insertion and tightening to ensure a secure connection. It's essential to use the correct size and type of ferrule for the fuel line diameter to guarantee a reliable seal.
- Clamp-Style Fittings: As the name suggests, these fittings use a clamp to secure the fuel line in place. The clamp is typically made of metal or durable plastic and is designed to apply pressure evenly around the fuel line, creating a tight seal. Clamp-style fittings are often used in situations where quick disassembly is required, such as in racing applications or when working with flexible fuel lines. Ensure that the clamp is tightened securely but carefully to avoid damaging the fuel line.
- Swivel Fittings: Swivel fittings are useful when there is a need for flexibility and movement in the fuel line. These fittings allow the fuel line to rotate, which is beneficial in certain engine configurations or when routing the fuel line around obstacles. Swivel fittings often feature a ball or sphere that allows for 360-degree rotation. When installing these fittings, ensure that the fuel line is properly aligned and that the swivel mechanism is not obstructed.
Understanding the different fitting types is essential for a successful fuel line installation. Each fitting type has its advantages and is suited to specific applications. Always refer to the manufacturer's guidelines and recommendations for the specific fuel line and vehicle you are working with. Properly identifying and using the correct fittings will ensure a secure connection, minimize the risk of fuel leaks, and contribute to the overall performance and safety of your vehicle's fuel system.
Poulan Prolink P335 Fuel Line Size: Essential Guide for Optimal Performance
You may want to see also
Pressure Testing: Test the fuel line for leaks after connecting to ensure a secure seal
When connecting a fuel line, it is crucial to ensure a secure and leak-free seal to prevent any potential hazards. Pressure testing is an essential step to verify the integrity of the connection and identify any potential issues before putting the system into operation. Here's a detailed guide on how to perform this test:
Preparation: Before initiating the pressure test, gather the necessary tools and materials. You will need a fuel pump, a pressure gauge, a container to collect fuel, and a source of compressed air or nitrogen. Ensure that the fuel line is clean and free of any debris or contaminants that could interfere with the test results.
Procedure: Start by attaching the fuel pump to the fuel line and connecting the output to the pressure gauge. Securely fasten the connections to avoid any leaks during the test. Open the fuel pump to allow fuel to flow through the line. Gradually increase the pressure using the compressed air or nitrogen source while monitoring the gauge. The pressure should rise steadily, indicating a good seal. As you increase the pressure, keep an eye on the fuel level in the container. If any fuel accumulates, it suggests a leak in the system.
Leak Detection: The key to this test is to observe any signs of fuel escaping during the pressure application. Even a small leak can lead to significant issues over time. Look for any fuel seeping from connections, joints, or where the fuel line meets the pump. Additionally, pay attention to any unusual noises or vibrations, which could indicate a problem. If you detect any leaks, immediately release the pressure and inspect the connections. Tighten or adjust the fittings as necessary to ensure a secure seal.
Safety Precautions: During the pressure test, ensure that the area is well-ventilated and clear of any flammable materials. Always follow safety protocols when working with fuel and compressed air. Wear appropriate personal protective equipment, such as gloves and safety goggles, to protect yourself from potential hazards.
Diesel Kleen: Effective Fuel Line Cleaner?
You may want to see also
Fuel Line Routing: Route the fuel line safely, avoiding sharp bends and potential damage
When it comes to fuel line installation, proper routing is crucial to ensure the safety and reliability of your vehicle's fuel system. The fuel line should be carefully planned to avoid any sharp bends or kinks, as these can lead to potential issues and damage over time. Here's a detailed guide on how to route the fuel line effectively:
Start by referring to your vehicle's manual or seeking professional advice to understand the optimal path for the fuel line. This is essential to ensure you don't interfere with other components or create unnecessary strain. The goal is to create a smooth and direct route, minimizing any potential hazards. Identify the source of the fuel supply, typically the fuel pump or tank, and determine the most efficient way to reach the engine or the desired fuel-injected system.
As you begin the routing process, aim for gentle curves and avoid sharp angles. Sharp bends can cause stress on the fuel line, leading to potential cracks or leaks. Instead, use a variety of gentle curves and straight sections to create a smooth flow. Consider the material of the fuel line; some materials may be more flexible and easier to manipulate, allowing for better control during the routing process.
Pay close attention to the areas where the fuel line will pass through or near other components. Ensure that there is sufficient clearance to prevent any damage or interference. For example, avoid routing the fuel line directly over a hot engine component or in a location where it could be easily damaged during maintenance or repairs. Proper insulation and protection might be required in such cases.
Additionally, when connecting the fuel line, ensure that you use the appropriate connectors and fittings. These connectors should be securely fastened to prevent any leaks or disconnections. Avoid overtightening, as it can damage the fuel line. By following these routing practices, you can significantly reduce the risk of fuel line-related issues and ensure a safe and efficient fuel supply to your vehicle's engine. Remember, proper installation and maintenance are key to avoiding costly repairs and ensuring the longevity of your vehicle's fuel system.
Mastering the Art of Fuel Line Removal: A Step-by-Step Guide
You may want to see also
Fuel Pump Compatibility: Ensure the fuel pump is compatible with the fuel line size and pressure
When considering connecting a fuel line without a connector, it's crucial to prioritize safety and ensure compatibility with the fuel pump. The fuel pump plays a vital role in delivering fuel to the engine, and its compatibility with the fuel line is essential for optimal performance and safety. Here's a detailed guide on how to ensure compatibility:
Fuel Line Size: The diameter of the fuel line is a critical factor. It should match the specifications of the fuel pump to ensure efficient fuel flow. If the fuel line is too small, it may restrict the flow, leading to reduced engine performance and potential fuel starvation. Conversely, a fuel line that is too large can create unnecessary pressure and may even cause the fuel to vaporize, reducing its energy content. Always refer to the vehicle's manual or consult the manufacturer's guidelines to determine the correct fuel line size for your specific pump and engine.
Pressure Compatibility: Fuel pumps operate within a specific pressure range, and it's essential to match this range with the fuel line's capabilities. If the fuel line pressure is too low, the pump may struggle to deliver fuel effectively, resulting in poor engine performance. On the other hand, excessive pressure can lead to fuel line damage or even fuel spray. Ensure that the fuel line material and design can withstand the pump's pressure output without compromising its integrity.
Material and Construction: The material and construction of the fuel line are vital considerations. Different materials have varying levels of flexibility, durability, and resistance to fuel degradation. For example, rubber fuel lines are commonly used and offer good flexibility, while braided steel lines provide excellent durability and resistance to pressure. Choose a fuel line material that complements the pump's design and ensures a secure connection.
Installation and Fitting: Proper installation is key to ensuring compatibility. When connecting the fuel line without a connector, ensure a tight and secure fit. Use appropriate fittings and clamps to prevent leaks and ensure the line is securely attached to the pump and the engine. Follow the manufacturer's instructions for installation to avoid any potential issues.
By carefully considering fuel pump compatibility, including line size, pressure, material, and installation, you can ensure a safe and efficient fuel delivery system. It is always recommended to consult the vehicle's manual or seek professional advice to make informed decisions regarding fuel system modifications.
Mastering the Art of Splice: Rubber Fuel Line Repair Guide
You may want to see also
Frequently asked questions
While it is technically possible to connect a fuel line without a connector, it is not recommended for safety and reliability reasons. Fuel lines are designed to be connected with specific connectors to ensure a secure and leak-free fit. Using a connector provides additional support, prevents fuel leaks, and makes it easier to replace or repair the fuel line if needed.
Connectors are crucial for fuel lines as they provide a reliable and secure connection point. They ensure that the fuel line is tightly sealed, preventing any potential fuel leaks. Additionally, connectors often have built-in o-rings or seals that further enhance the integrity of the connection, reducing the risk of fuel contamination and potential engine issues.
In some cases, you might consider using quick-release fittings or clamps instead of connectors. Quick-release fittings can provide a temporary solution for fuel line connections, especially during maintenance or repairs. However, for a permanent installation, it is best to use the appropriate connectors designed for fuel lines to ensure long-term reliability.
Modifying the fuel line to connect without a connector is generally not advised. Fuel lines are precision-engineered components, and any modifications can compromise their functionality and safety. It is always best to follow the manufacturer's guidelines and use the recommended connectors to ensure compatibility and avoid potential hazards.
Connecting a fuel line without a connector can lead to several risks. Without the proper seal and support, there is a higher chance of fuel leaks, which can cause engine misfires, reduced performance, and potential damage to the engine over time. Additionally, a poorly connected fuel line may not withstand vibrations or temperature changes, leading to potential failures.