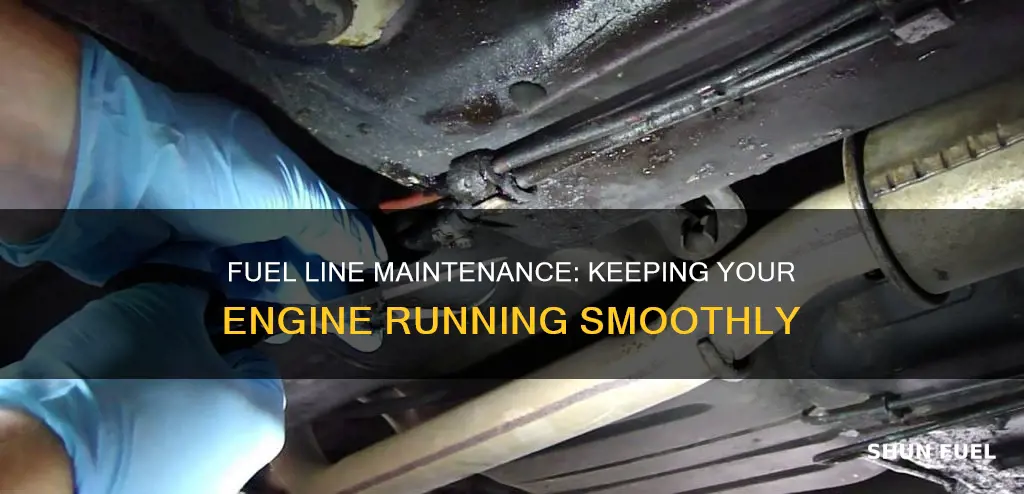
Are the fuel lines? This question often arises when troubleshooting vehicle issues, especially those related to the engine's performance and fuel system. Fuel lines are crucial components that deliver gasoline or diesel from the fuel tank to the engine, and any damage or malfunction can lead to significant problems. Understanding the role and maintenance of fuel lines is essential for vehicle owners to ensure optimal performance and prevent costly repairs.
What You'll Learn
- Fuel Line Material: Different materials like rubber, plastic, or metal are used for fuel lines
- Fuel Line Routing: Proper routing to avoid damage and ensure fuel flow
- Fuel Line Connections: Secure and leak-proof connections between fuel lines and components
- Fuel Line Inspection: Regular checks for cracks, leaks, and signs of wear
- Fuel Line Replacement: Knowing when and how to replace damaged or worn fuel lines
Fuel Line Material: Different materials like rubber, plastic, or metal are used for fuel lines
Fuel lines are an essential component of any vehicle's fuel system, responsible for transporting fuel from the tank to the engine. The choice of material for these lines is crucial, as it directly impacts performance, durability, and safety. Over time, various materials have been utilized, each offering unique advantages and disadvantages.
One of the most common materials for fuel lines is rubber. Rubber is known for its flexibility, making it ideal for accommodating the various movements and vibrations experienced during vehicle operation. It is also resistant to most fuels, including gasoline and diesel, ensuring that the material does not degrade or become brittle over time. Additionally, rubber fuel lines are generally more cost-effective compared to other materials, making them a popular choice for many vehicle manufacturers. However, rubber can be susceptible to cracking, especially in extreme temperatures, which may lead to fuel leaks.
Plastic fuel lines have also gained popularity in recent years. Plastic offers excellent resistance to corrosion and is lightweight, making it easier to install and route through the engine compartment. It is also more flexible than metal, providing better adaptability to the vehicle's movements. Modern plastic fuel lines are often made from high-density polyethylene (HDPE) or polyvinyl chloride (PVC), which are known for their strength and durability. These materials are less likely to crack or become brittle, ensuring a longer lifespan for the fuel lines.
Metal fuel lines, typically made from steel or aluminum, are known for their exceptional strength and durability. They are highly resistant to high pressures and temperatures, making them suitable for high-performance vehicles or those with larger fuel tanks. Metal lines are also less susceptible to corrosion, ensuring a longer-lasting solution. However, metal fuel lines are much stiffer than rubber or plastic, which can make installation more challenging and may limit their flexibility. This can lead to increased stress on the lines, potentially causing damage or leaks over time.
The choice of material for fuel lines depends on various factors, including the vehicle's specifications, fuel type, and environmental conditions. Modern vehicles often utilize a combination of these materials to optimize performance and safety. For instance, rubber lines might be used for the majority of the fuel system, while metal lines are employed for critical high-pressure applications. This approach ensures that the fuel lines are both durable and reliable, contributing to the overall efficiency and longevity of the vehicle's fuel system.
Brake Flush: Choosing the Right Fuel Line Size
You may want to see also
Fuel Line Routing: Proper routing to avoid damage and ensure fuel flow
Fuel lines are an essential component of any vehicle's fuel system, responsible for transporting fuel from the tank to the engine. Proper routing of these lines is crucial to ensure optimal performance and longevity of the system. Here's a detailed guide on how to route fuel lines effectively:
- Identify the Route: Begin by understanding the layout of your vehicle's engine bay and fuel system. Locate the fuel tank, which is typically positioned at the front or rear of the vehicle, and identify the fuel pump, which is responsible for pumping fuel to the engine. The fuel lines will connect the tank to the pump and then to the engine's fuel injectors or carburetor. Mark the path these lines should take on a diagram or directly on the vehicle to ensure a clear and logical route.
- Avoid High-Stress Areas: One of the primary considerations in routing fuel lines is to avoid high-stress areas where the lines could be damaged. These areas often include sharp bends, sharp corners, or areas near moving parts like the engine block or transmission. Fuel lines should be routed away from these high-stress zones to prevent cracks, punctures, or kinks that could lead to fuel leaks or system failures.
- Use Protective Materials: To safeguard the fuel lines, consider using protective materials such as rubber, plastic, or metal braiding. These materials can be wrapped around the lines to provide a layer of insulation and protection against potential impacts or abrasion. This is especially important in areas where the lines might come into contact with other components or where there is a risk of physical damage.
- Secure the Lines: Properly secure the fuel lines to ensure they remain in place and do not interfere with other components. Use tie-straps, clips, or brackets to keep the lines taut and away from the ground. Ensure that the lines are not pinched or crushed, as this can restrict fuel flow and cause potential issues. Secure the lines at regular intervals to maintain tension and prevent sagging or excessive movement.
- Consider Engine Movement: Take into account the natural movement of the engine during operation. Fuel lines should be routed in a way that accommodates this movement to prevent excessive bending or stress on the lines. Allow for some flexibility in the routing to ensure the lines can expand and contract with the engine's thermal cycles.
- Regular Inspection: Regularly inspect the fuel lines for any signs of damage, leaks, or wear. Look for cracks, brittleness, or signs of corrosion, especially in areas where the lines are exposed to the elements. Promptly address any issues found to prevent further deterioration and potential fuel system failures.
By following these guidelines, you can ensure that your fuel lines are properly routed, avoiding potential damage and ensuring a consistent fuel supply to the engine. This will contribute to the overall reliability and performance of your vehicle's fuel system.
2003 Trailblazer Fuel Line Location: A Comprehensive Guide
You may want to see also
Fuel Line Connections: Secure and leak-proof connections between fuel lines and components
Fuel line connections are a critical aspect of any vehicle's fuel system, ensuring efficient and safe operation. These connections must be secure and leak-proof to prevent fuel loss, engine performance issues, and potential safety hazards. Here's an in-depth look at the process of creating robust fuel line connections:
Understanding the Components: Before connecting fuel lines, it's essential to understand the various components involved. These include the fuel tank, fuel pump, fuel filter, injectors or carburetor, and the engine itself. Each component has specific requirements for fuel line connections, such as the type of fuel line material, diameter, and routing. For instance, high-pressure fuel lines near the engine require robust connections to withstand the force.
Preparation and Assembly: Proper preparation is key to a successful connection. Start by cleaning the fuel lines and components to remove any dirt, corrosion, or debris. Use a suitable solvent to ensure a clean surface for the connection. Then, assemble the components, ensuring that all parts are aligned correctly and securely fastened. This includes using the right type of fuel line clips, brackets, or ties to hold the lines in place without causing damage.
Secure Connections: The goal is to create a tight, leak-free seal. This can be achieved through various methods, such as crimping, clamping, or using specialized fuel line connectors. Crimping involves deforming the fuel line to create a secure grip around the component, while clamping uses mechanical pressure to hold the line in place. Specialized connectors, often made of durable materials like brass or stainless steel, provide a precise fit and are designed to withstand fuel pressure. It's crucial to follow manufacturer guidelines for the correct installation process.
Testing for Leaks: After the connections are made, thorough testing is essential. This typically involves using a fuel pressure gauge to check for leaks and ensuring that the system holds pressure. Visual inspections can also be performed to identify any signs of damage or improper installation. If any issues are found, the connections should be rechecked and tightened or replaced as necessary.
Regular Maintenance: Even after a successful installation, regular maintenance is vital. Over time, fuel lines can degrade due to fuel exposure, temperature changes, and mechanical stress. Inspect the connections periodically for any signs of wear, cracks, or corrosion. Replacing worn-out fuel lines and connections can prevent potential failures and ensure the vehicle's fuel system operates optimally.
Miata Fuel Line Sizes: A Comprehensive Guide
You may want to see also
Fuel Line Inspection: Regular checks for cracks, leaks, and signs of wear
Fuel lines are an essential component of any vehicle's fuel system, responsible for transporting gasoline or diesel from the tank to the engine. Over time, these lines can develop various issues that may lead to performance problems or even engine failure. Therefore, it is crucial to perform regular inspections to identify and address potential problems early on. This article will guide you through the process of inspecting your fuel lines for cracks, leaks, and signs of wear.
Start by visually examining the fuel lines for any visible damage. Look for cracks, splits, or punctures along the length of the lines, especially where they connect to the fuel tank and the engine. These areas are more susceptible to wear due to the constant movement and pressure within the system. Inspect the lines for any signs of corrosion or rust, which can weaken the material and lead to leaks. Also, check for any signs of damage caused by road debris, such as small cuts or punctures, especially if the vehicle has been driven over rough terrain.
Next, perform a pressure test to check for leaks. This is a critical step as it helps identify any small leaks that might not be visible to the naked eye. You will need a fuel pressure gauge and a small amount of fuel. Start by disconnecting the fuel pump and temporarily blocking the return line to prevent fuel from draining back into the tank. Then, connect the gauge to the fuel line and apply pressure. If there is a leak, you will notice a drop in pressure or fuel escaping from the line. It is important to note any changes in pressure and the location of any leaks to pinpoint the source of the issue.
While inspecting the fuel lines, pay attention to the overall condition of the system. Look for any signs of wear, such as frayed or damaged insulation, which can expose the lines to the elements and potential corrosion. Check for any loose connections or fittings, as these can lead to fuel leaks and reduced performance. Additionally, inspect the fuel filter, as a clogged or damaged filter can restrict fuel flow and cause issues with the lines. Regularly replacing the fuel filter is an essential part of maintenance to ensure the longevity of the fuel lines.
In summary, regular fuel line inspections are vital to maintaining a healthy vehicle. By visually examining the lines for cracks and corrosion, performing pressure tests to identify leaks, and checking for overall wear and tear, you can ensure that your fuel system operates efficiently. Remember, early detection of issues with the fuel lines can prevent costly repairs and potential engine damage. It is always recommended to consult a professional mechanic if you are unsure or if any issues are found during the inspection process.
Fuel Line Break: Engine Chaos Unveiled
You may want to see also
Fuel Line Replacement: Knowing when and how to replace damaged or worn fuel lines
Fuel lines are an essential component of your vehicle's fuel system, responsible for transporting gasoline or diesel from the tank to the engine. Over time, these lines can become damaged or worn due to various factors such as age, corrosion, or accidents. When this happens, it's crucial to replace the fuel lines promptly to ensure optimal engine performance and prevent potential safety hazards. This guide will provide you with an overview of when and how to replace damaged or worn fuel lines.
Signs of Fuel Line Issues:
Before proceeding with a replacement, it's essential to recognize the signs of fuel line problems. Common indicators include fuel leaks, engine misfires, reduced power, or strange noises coming from the engine. If you notice any of these symptoms, it's advisable to inspect the fuel lines for any visible damage or wear. Look for cracks, punctures, corrosion, or any signs of deterioration. Additionally, check for any loose connections or fittings that may have come loose over time.
When to Replace Fuel Lines:
Fuel line replacement is necessary when the lines are visibly damaged, worn out, or leaking. Here are some scenarios that warrant a replacement:
- Visible Damage: If you notice any tears, holes, or significant bends in the fuel line, it's a clear sign of damage that requires immediate attention.
- Corrosion: Over time, fuel lines can corrode, especially if your vehicle operates in harsh environments or has been exposed to salt on roads. Corrosion can lead to reduced fuel flow and potential engine issues.
- Leaking Fuel: A telltale sign of a failing fuel line is a fuel leak. If you notice any liquid under your vehicle or smell gasoline, it's crucial to inspect the lines for damage.
- Age: As fuel lines age, their flexibility and integrity can diminish. Older vehicles or those with high mileage may require fuel line replacement to maintain optimal performance.
Steps for Fuel Line Replacement:
Replacing fuel lines is a task that requires careful execution to ensure a safe and successful outcome. Here's a general guide:
- Prepare the Vehicle: Park the vehicle on a level surface, engage the parking brake, and allow the engine to cool down.
- Locate the Fuel Lines: Identify the fuel lines that need replacement. They are typically located along the frame rail and under the vehicle.
- Drain the Fuel: Locate the fuel tank and drain valve. Open the valve to release any remaining fuel in the lines.
- Remove Old Lines: Carefully cut or sever the damaged fuel lines, ensuring you have enough length to install the new lines.
- Install New Fuel Lines: Slide the new fuel lines into place, ensuring they are routed correctly and securely fastened.
- Connect and Test: Reattach any fittings and connections, ensuring a tight seal. Start the engine and check for any leaks.
Remember, fuel line replacement can be complex, and it's recommended to consult a professional mechanic if you're unsure about any step. Regular maintenance and timely replacements will help ensure your vehicle's fuel system operates efficiently and safely.
Fixing a Steel Fuel Line: A Step-by-Step Guide
You may want to see also
Frequently asked questions
Fuel lines are a network of tubes or hoses that carry gasoline or diesel from the fuel tank to the engine. They are crucial for delivering the fuel required for the engine to run, ensuring optimal performance and preventing engine misfires.
It is recommended to inspect fuel lines at least once a year or every 10,000 miles. Regular inspections can help identify any leaks, cracks, or damage that may lead to fuel contamination or engine issues.
Yes, fuel lines can be a source of various engine problems. Leaking fuel lines can result in fuel wastage, engine misfires, and reduced performance. Cracked or damaged lines may cause fuel contamination, leading to engine knocking, reduced power, and potential long-term engine damage.
Look out for symptoms like engine hesitation, rough idling, reduced power, or a noticeable decrease in fuel efficiency. If you notice any fuel odor inside the car or see puddles of fuel around the vehicle, it could indicate a fuel line leak.
Regular maintenance is key. Keep your fuel tank clean and ensure it is properly sealed. Use the recommended fuel type and additives to maintain fuel quality. Inspect the fuel lines for any signs of wear and tear, and replace them if necessary to avoid potential engine complications.