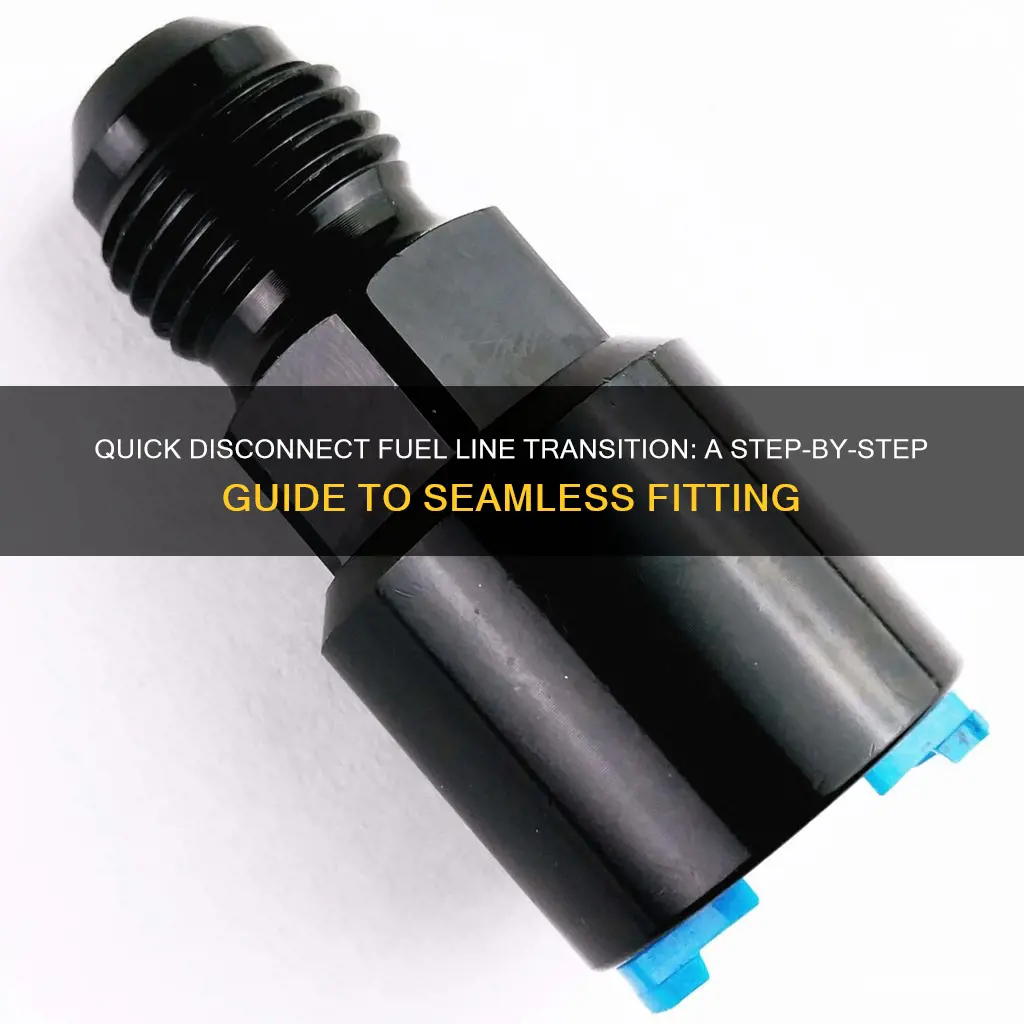
Transitioning a quick disconnect fuel line to a fitting is a useful skill for anyone working on fuel systems, whether it's for a car, boat, or other machinery. This process involves replacing the existing quick disconnect with a more permanent or compatible fitting to ensure a secure and reliable fuel supply. The key to a successful transition is understanding the specific requirements of the fuel line and the fitting, including the correct size, material, and compatibility with the fuel type. This guide will provide a step-by-step approach to ensure a smooth and safe transition, covering the necessary tools, preparation, and installation techniques.
What You'll Learn
- Preparation: Ensure you have the right tools and disconnect fuel line quickly and safely
- Line Inspection: Check for damage or wear before disconnecting to avoid leaks
- Fitting Compatibility: Verify the fitting size and material match the fuel line
- Tightening Techniques: Use the correct torque and angle for a secure connection
- Testing: Confirm the connection is leak-free and functional after reassembly
Preparation: Ensure you have the right tools and disconnect fuel line quickly and safely
Before you begin the process of disconnecting the fuel line, it's crucial to ensure you have the necessary tools and equipment to make the task efficient and safe. This preparation will help you avoid any potential hazards and ensure a smooth transition. Firstly, gather the required tools, which typically include a fuel line disconnect tool or a fuel line cutter, a pair of adjustable pliers or a fuel line clamp, and a rag or cloth for protection. These tools are essential for safely and effectively disconnecting the fuel line.
Having the right tools is just the first step; you also need to prepare your workspace. Find a well-lit, flat area where you can comfortably work without tripping over obstacles. Ensure the area is clear of any potential hazards, such as sharp objects or flammable materials. It's also a good idea to wear protective gear, including gloves and safety goggles, to shield yourself from any potential fuel spills or debris.
Now, let's focus on the fuel line itself. Locate the quick-disconnect fuel line on your vehicle, which is usually a metal or rubber hose with a quick-release fitting. Identify the fitting and ensure it is securely attached to the fuel line. If it's not already disconnected, you may need to loosen the fitting slightly to make the disconnection process easier. Remember, the goal is to quickly and safely disconnect the fuel line, so take your time and be methodical in your approach.
Once you've prepared your tools and workspace, and located the fuel line, you're ready to proceed with the disconnection. Always follow the manufacturer's instructions for your specific vehicle model, as fuel lines can vary in design. Typically, you'll need to use the fuel line disconnect tool or clamp to release the fitting and disconnect the line. Take care not to overtighten or force the disconnect, as this can damage the fuel line or fittings.
By ensuring you have the right tools, preparing your workspace, and carefully locating and disconnecting the fuel line, you can efficiently and safely transition the quick-disconnect fuel line to a fitting. This preparation is key to avoiding potential hazards and ensuring a successful fuel line disconnection. Remember, always prioritize safety and take your time to complete the task correctly.
Optimizing Fuel Flow: Choosing the Right Fuel Line for Injection
You may want to see also
Line Inspection: Check for damage or wear before disconnecting to avoid leaks
Before attempting to disconnect a quick-disconnect fuel line, it is crucial to conduct a thorough inspection to ensure the process is done safely and effectively. This step is often overlooked but is essential to prevent fuel leaks and potential hazards. Here's a detailed guide on how to inspect the fuel line for any damage or wear:
Start by visually examining the fuel line for any visible signs of deterioration. Look for cracks, brittleness, or any discolouration along the length of the line. Over time, fuel lines can degrade due to exposure to fuel, heat, and vibration, making them more susceptible to damage. Check for any bends or kinks in the line, as these can cause stress points and potential failure. Ensure that the fuel line is not pinched or compressed, as this can restrict fuel flow and lead to potential issues. Inspect the fittings and connectors for any signs of corrosion or damage. Corrosion can weaken the connection and lead to leaks. Look for any signs of rust or oxidation around the threads and ports of the fittings.
Pay close attention to the condition of the fuel line's outer covering or sheath. This protective layer shields the inner fuel line from external elements. Inspect it for any tears, punctures, or signs of wear. If the sheath is damaged, it could expose the inner line to potential hazards. Check for any signs of fuel contamination or degradation. Over time, fuel can break down, leading to the formation of varnish or sludge, which can clog the line and cause issues. If you notice any unusual residue or discolouration, it may indicate a problem.
Additionally, feel the fuel line for any heat-induced softening or hardening. Extreme temperatures can affect the flexibility and integrity of the line. If it feels unusually soft or hard, it might indicate internal damage. Remember, the goal of this inspection is to identify any potential issues before disconnecting the fuel line. By taking the time to carefully examine the line, you can ensure a safe and successful transition, minimizing the risk of fuel leaks and related problems.
Snow Blower Fuel Lines: Size Guide for Optimal Performance
You may want to see also
Fitting Compatibility: Verify the fitting size and material match the fuel line
When transitioning a quick-disconnect fuel line to a fitting, ensuring proper compatibility is crucial to prevent leaks and ensure a safe and efficient fuel system. Here's a detailed guide on how to verify the fitting size and material to match the fuel line:
- Identify the Fuel Line Diameter: Start by measuring the diameter of your fuel line. This is a critical step as the fitting's internal diameter must match the fuel line's diameter to create a secure seal. Use a caliper to measure the fuel line at its widest point, ensuring you get an accurate measurement.
- Check Fitting Specifications: Obtain the specifications of the fitting you intend to use. Manufacturers typically provide detailed information about their fittings, including size and material. Look for the internal diameter and any specific dimensions that match the fuel line's requirements. Ensure the fitting's material is compatible with the fuel type you are using. Common materials include steel, brass, and various plastics, each with its own advantages and limitations.
- Compare and Match: Compare the fuel line's diameter and the fitting's specifications. If the diameters match, you have a good fit. However, if there's a discrepancy, you might need to adjust or choose a different fitting. For example, if the fuel line is slightly larger than the fitting's internal diameter, you may need to consider a larger fitting or use an adapter to ensure a proper seal.
- Consider Fitting Type: Different types of fittings may have varying compatibility. Quick-disconnect fittings often have specific sizes and thread types. Ensure the fitting you select matches the thread size and pattern of your fuel line. This is essential for a secure and leak-free connection.
- Test and Inspect: After installing the fitting, perform a visual inspection to ensure there are no visible gaps or misalignments. Test the system by applying pressure and checking for leaks. If everything is secure, you've successfully transitioned the quick-disconnect fuel line to a fitting that is compatible in size and material.
Remember, proper fitting compatibility is essential for the longevity and safety of your fuel system. Always refer to manufacturer guidelines and specifications to ensure you make the right choices for your specific application.
Ryobi Fuel Line Sizes: A Comprehensive Guide
You may want to see also
Tightening Techniques: Use the correct torque and angle for a secure connection
When transitioning a quick-disconnect fuel line to a fitting, ensuring a secure and reliable connection is crucial to prevent fuel leaks and maintain optimal engine performance. One of the key aspects of achieving this is using the correct tightening techniques, specifically focusing on torque and angle.
Torque is the rotational force applied to tighten the connection, and it plays a vital role in creating a tight seal. It's essential to use a torque wrench to apply the correct amount of torque. The recommended torque value can vary depending on the specific fuel line and fitting, so always refer to the manufacturer's guidelines or consult a technical manual. Applying too little torque may result in a loose connection, while excessive torque can damage the fittings and fuel line. Aim for a consistent and controlled application of torque to ensure a secure yet gentle connection.
The angle at which you tighten the fitting is another critical factor. It's important to tighten the fitting at the right angle to ensure even pressure distribution and a proper seal. The ideal angle can vary depending on the design of the fitting and the fuel line. Generally, a 90-degree angle is a good starting point, but it's essential to check the manufacturer's specifications. Tighten the fitting by hand first, ensuring it is aligned correctly, and then use the torque wrench to apply the specified torque. This two-step process ensures a precise and secure connection.
To summarize, achieving a secure connection when transitioning a quick-disconnect fuel line involves using the correct torque and angle. Employ a torque wrench to apply the recommended torque value, ensuring neither too much nor too little force. Additionally, pay attention to the angle, aligning the fitting at the suggested degree to facilitate even pressure distribution. By following these tightening techniques, you can create a reliable and leak-free connection for your fuel line.
Dirt Bike Fuel Line Sizing: Essential Guide for Optimal Performance
You may want to see also
Testing: Confirm the connection is leak-free and functional after reassembly
After reassembling the quick-disconnect fuel line fitting, it's crucial to conduct a thorough test to ensure the connection is leak-free and functional. This step is essential to prevent any potential fuel leaks, which can be dangerous and costly. Here's a detailed guide on how to perform this test:
Step 1: Prepare the Necessary Tools and Materials:
Before starting the test, gather all the required tools and materials. You'll need a fuel pressure gauge, a small container or a pan to catch any potential leaks, and a source of fuel (if you don't have one, you can use water as a substitute to simulate the test). Ensure you have the appropriate safety gear, such as gloves and safety goggles, to protect yourself during the process.
Step 2: Apply a Sealant or Tape:
If you haven't already, apply a small amount of fuel-resistant sealant or tape around the connection points. This extra step provides an additional layer of protection against potential leaks. Make sure the sealant is applied evenly and covers all relevant areas.
Step 3: Perform the Pressure Test:
Connect the fuel pressure gauge to the fuel line, ensuring it is securely attached. Turn on the fuel source and gradually increase the pressure using the gauge. Monitor the pressure reading and look for any signs of fuel escaping. If you notice any leaks, even a small amount, it indicates a potential issue with the connection.
Step 4: Visual Inspection:
While performing the pressure test, visually inspect the connection points for any signs of fuel leakage. Look for wet spots or fuel residue around the fitting. If you see any, it confirms that the connection is not leak-free. Additionally, check for any visible damage or deformation in the fitting that could contribute to leaks.
Step 5: Re-evaluate and Adjust:
If you identify any issues during the test, carefully re-evaluate the connection and make the necessary adjustments. This might involve tightening the fittings further, reapplying sealant, or replacing damaged components. Ensure that all connections are secure and properly aligned.
Step 6: Final Functional Test:
After addressing any potential problems, perform a final functional test. Start the engine and monitor it for any unusual noises or vibrations. Check for any fuel-related warning lights on the dashboard. If the engine runs smoothly and there are no signs of fuel leakage, your quick-disconnect fuel line connection is likely secure and functional.
Remember, proper testing is critical to ensuring the safety and reliability of your fuel system. Always follow manufacturer guidelines and best practices for reassembly and testing to avoid any potential hazards.
Understanding Fuel Filter Lines: A Comprehensive Guide
You may want to see also
Frequently asked questions
Transitioning a quick disconnect fuel line to a fitting involves a few steps. First, ensure you have the correct tools, including a fuel line cutter, a fitting, and a fuel line adapter. Start by cutting the fuel line to the desired length, leaving enough to connect to the fitting and the fuel source. Then, attach the fitting to the fuel line using the appropriate clamp or crimping tool. Make sure the connection is secure and tight. Finally, connect the other end of the fuel line to the desired fitting or component in your fuel system.
Achieving a proper seal is crucial for a successful connection. Start by cleaning the ends of the fuel line and the fitting to remove any dirt or debris. Apply a thin layer of fuel line tape or an appropriate adhesive to the fuel line and fitting, ensuring full coverage. Then, carefully slide the fuel line into the fitting, pushing it until it is fully inserted. Use a clamp or crimping tool to secure the connection and create a tight seal. Test the connection for leaks before reassembling the system.
Yes, you can reuse a quick disconnect fuel line, but it's essential to inspect it for any signs of damage or wear. Check for cracks, brittleness, or any damage to the fittings. If the fuel line appears intact and there are no visible issues, you can reuse it. However, it's recommended to replace the fuel line if it has been exposed to extreme temperatures or harsh conditions. Always ensure proper cleaning and preparation before reinstalling to maintain optimal performance and safety.