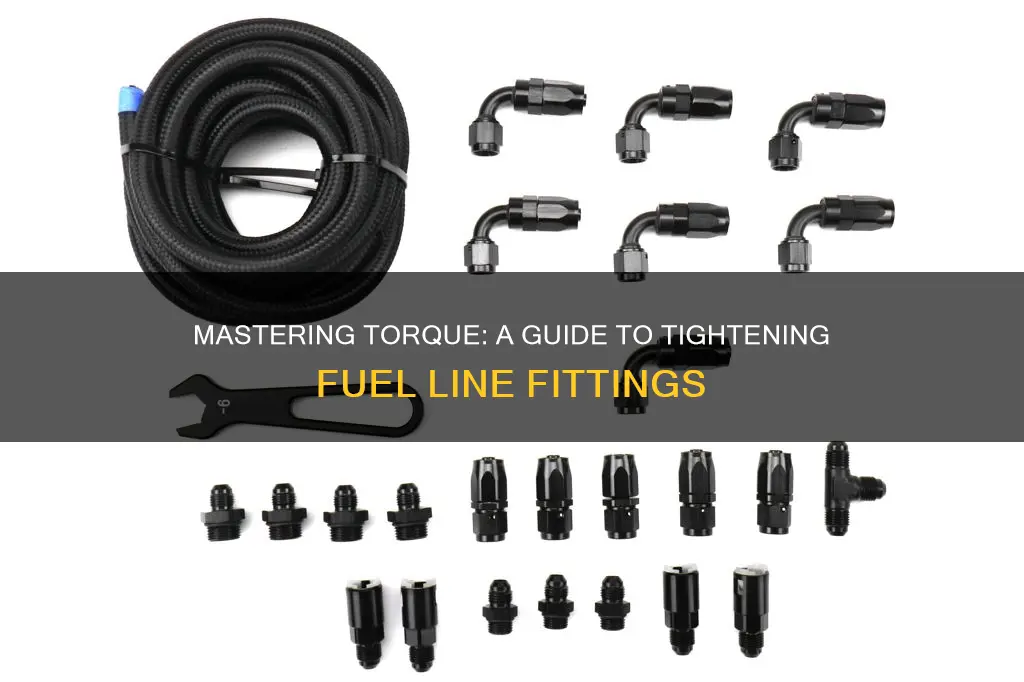
Torque fuel line fittings is a critical process in ensuring the safe and efficient operation of fuel systems in vehicles and machinery. It involves tightening the connections between fuel lines and components using the correct amount of force, known as torque, to create a secure and leak-free bond. This process is essential to prevent fuel leaks, which can lead to engine misfires, reduced performance, and potential safety hazards. Properly torqued fuel line fittings guarantee a reliable fuel supply to the engine, optimizing its performance and longevity. Understanding the correct torque specifications for different fittings and using the appropriate tools is crucial to mastering this technique.
What You'll Learn
- Prepare Tools: Gather torque wrench, fuel line, and cleaning supplies
- Clean Fittings: Remove old fuel line, clean threads, and inspect for damage
- Apply Sealant: Use fuel-resistant sealant on threads and fittings
- Torque to Specs: Tighten fittings to manufacturer's torque specifications using a wrench
- Test for Leaks: Check for leaks after installation; ensure proper torque was applied
Prepare Tools: Gather torque wrench, fuel line, and cleaning supplies
To ensure a proper and secure installation of fuel line fittings, it's crucial to have the right tools and supplies ready. Here's a step-by-step guide on preparing the necessary items:
Torque Wrench: The primary tool you'll need is a torque wrench, specifically designed to apply precise torque to fasteners. When working with fuel lines, it's essential to follow the manufacturer's recommended torque specifications to avoid over-tightening or under-tightening, which can lead to potential issues. Ensure you have a torque wrench that covers the range required for the fittings you're working with.
Fuel Line: Before you begin, make sure you have the correct fuel line that matches the specifications of your vehicle. This includes the appropriate size, material, and type of fuel line. Check the vehicle's manual or consult the manufacturer to determine the correct fuel line dimensions and any specific requirements. Having the right fuel line ensures a proper fit and prevents any potential leaks.
Cleaning Supplies: Cleaning the work area and the fuel line fittings is an often-overlooked but crucial step. Gather cleaning supplies such as a degreaser or fuel line cleaner, a brush or cleaning cloth, and a clean rag. These supplies will help remove any dirt, grease, or contaminants that could interfere with the installation process. Proper cleaning ensures a smooth and secure connection between the fittings and the fuel line.
Additionally, consider having a small container or tray to catch any debris or cleaning agents that may spill during the process. This will help keep your work area clean and organized. It's also a good idea to wear protective gloves to shield your hands from any chemicals and to ensure a comfortable grip when handling tools and fittings.
By gathering these tools and supplies, you'll be well-prepared to tackle the task of torque fuel line fittings, ensuring a professional and secure installation. Remember, taking the time to prepare and having the right equipment will contribute to a successful and safe fuel system repair or upgrade.
Optimal Diameter for Steel Fuel Lines: A Comprehensive Guide
You may want to see also
Clean Fittings: Remove old fuel line, clean threads, and inspect for damage
When dealing with fuel line fittings, ensuring a clean and proper installation is crucial for optimal performance and safety. Here's a step-by-step guide to achieving this:
- Remove the Old Fuel Line: Begin by disconnecting the old fuel line from the engine and the tank. This process may require specific tools like fuel line cutters or wrenches, depending on the type of fittings. Carefully detach the lines, ensuring you don't damage the surrounding components. It's essential to work systematically to avoid any confusion during the replacement process.
- Clean the Threads: After removing the old fuel line, inspect the threads of the fittings. Over time, these threads can become dirty, corroded, or damaged. Use a thread cleaner or a mild abrasive to scrub the threads thoroughly. Ensure you remove any debris or old sealant. For best results, consider using a thread-locking compound to ensure a secure connection.
- Inspect for Damage: Carefully examine the fittings and the surrounding areas for any signs of damage. Look for cracks, corrosion, or any signs of deterioration. If you notice any issues, it's crucial to replace the fittings to prevent potential leaks or performance problems. Take note of the make and model of the fittings to ensure you get the correct replacement parts.
- Prepare for Installation: Once the old fuel line and fittings are removed and inspected, it's time to prepare for the new installation. Ensure you have the correct tools and fittings for the specific make and model of your engine. Gather any necessary gaskets or seals to ensure a proper seal.
- Torque the Fittings Properly: When reinstalling the fuel line, torque the fittings according to the manufacturer's specifications. Over-tightening can damage the fittings, while under-tightening may lead to leaks. Use a torque wrench to apply the correct amount of force, ensuring a secure and reliable connection. This step is critical to maintaining the integrity of the fuel system.
Remember, proper cleaning and inspection of fuel line fittings are essential to ensure a safe and efficient fuel system. By following these steps, you can guarantee a reliable connection and prevent potential issues down the line. Always refer to the vehicle's manual for specific torque specifications and guidelines.
Perfect Fuel Line Size for Your 1992 Dodge D150 Pickup
You may want to see also
Apply Sealant: Use fuel-resistant sealant on threads and fittings
When working with fuel line fittings, ensuring a secure and leak-free connection is crucial. One essential step in achieving this is by applying a fuel-resistant sealant to the threads and fittings. This process not only enhances the reliability of the connection but also helps prevent fuel leaks, which can be costly and dangerous. Here's a detailed guide on how to apply the sealant effectively:
Start by ensuring you have the right materials. You'll need a high-quality fuel-resistant sealant that is compatible with the type of fuel your system uses. Common choices include silicone-based or epoxy-based sealants, specifically designed for fuel applications. These sealants are formulated to withstand the corrosive effects of fuel, ensuring long-lasting protection.
Before applying the sealant, thoroughly clean the threads and fittings. Remove any dirt, debris, or old sealant. You can use a wire brush or a small wire brush attachment on a power drill to ensure a clean surface. This step is critical because any contaminants can interfere with the sealant's ability to create a tight seal.
Once the threads and fittings are clean, apply a thin layer of the sealant. Use a small amount to avoid over-application, which can lead to messiness and potential waste. Focus on the threads and the areas where the fittings connect. Ensure you cover the entire surface, including any small grooves or ridges, as these areas can trap fuel and cause leaks if not properly sealed.
Let the sealant dry according to the manufacturer's instructions. Some sealants may require multiple coats, so follow the specific guidelines provided. After the sealant has cured, you can torque the fittings to the recommended specifications. This final step ensures that the connection is tight and secure, providing optimal protection against fuel leaks.
Remember, taking the time to apply the sealant correctly is an investment in the longevity and safety of your fuel system. It's a simple yet crucial step in maintaining a reliable and leak-free fuel line setup.
Mastering the Fuel Line Removal: A Guide for Chrysler PT Cruiser Owners
You may want to see also
Torque to Specs: Tighten fittings to manufacturer's torque specifications using a wrench
When working with fuel line fittings, it's crucial to follow the manufacturer's torque specifications to ensure a secure and reliable connection. This process involves using a wrench to apply the correct amount of force to tighten the fittings without over-tightening, which can lead to damage. Here's a step-by-step guide to help you get it right:
- Access the Fittings: Locate the fuel line fittings you need to tighten. These are typically found where the fuel lines connect to the engine, fuel pump, or other fuel system components. Ensure you have access to all the necessary fittings and the appropriate tools.
- Refer to the Manual: Obtain the vehicle or equipment manual, as it will provide the specific torque specifications for each fitting. These specifications are often listed in pounds-force per square inch (psi) or Newton-meters (Nm). Make sure to identify the correct torque value for the fitting type you are working on.
- Prepare the Wrench: Select a wrench that fits the size of the fitting's nut or bolt. Wrenches come in various sizes and types, such as open-end, box-end, or adjustable. Ensure the wrench is clean and free of any debris that might interfere with the tightening process. Consider using a wrench with a comfortable grip and a material that provides a secure hold.
- Apply the Correct Torque: Position the wrench onto the fitting's nut or bolt and apply the specified torque value. Use a torque wrench to ensure accuracy. Start by applying a slight force to feel the fitting engage, then gradually increase the pressure until you reach the desired torque. Avoid using excessive force, as it can strip threads or damage the fitting.
- Verify the Tightness: After tightening the fittings, check their tightness by hand. Ensure they are secure and do not wobble or loosen when handled. You can also use a torque wrench again to confirm that the fittings meet the manufacturer's specifications. If any fittings are too loose or tight, adjust them accordingly and recheck.
- Finalize the Connection: Once all fittings are tightened to the correct torque, secure any additional components, such as hoses or brackets, that were removed during the process. Reinstall any covers or protective caps to ensure the fuel system's integrity.
Remember, proper torque specifications are essential to maintain the performance and safety of your fuel system. Always refer to the manufacturer's guidelines and use the appropriate tools to ensure a professional and secure installation.
Fox Fuel Lines: Compatibility with Ford SN95 Models
You may want to see also
Test for Leaks: Check for leaks after installation; ensure proper torque was applied
After installing fuel line fittings, it is crucial to perform a thorough leak test to ensure the system's integrity and prevent potential issues. This step is often overlooked, but it is an essential part of the installation process. Here's a detailed guide on how to check for leaks and ensure proper torque was applied:
Leak Testing:
- Prepare the Environment: Find a suitable area, preferably an open space, to conduct the leak test. Ensure the area is well-ventilated to avoid inhaling any potential fuel vapor. Gather the necessary tools, including a fuel line fitting torque wrench, a pressure gauge, and a container to collect any potential fuel leaks.
- Connect the Fittings: Reattach the fuel line fittings to the vehicle's fuel system, ensuring they are correctly aligned and secured. Make sure all connections are tight and free from any debris or obstructions.
- Apply Pressure: Using the pressure gauge, apply a controlled amount of pressure to the fuel line fittings. The specific pressure will depend on the manufacturer's recommendations, but typically, a range of 50-100 psi (pounds per square inch) is used for fuel lines. Gradually increase the pressure and hold it for a few seconds.
- Check for Leaks: Inspect the connections thoroughly for any signs of fuel leakage. Look for wet spots, stains, or fuel accumulation around the fittings. Pay close attention to the threads, seals, and any gaskets used in the installation. If you notice any leaks, immediately release the pressure and tighten the connections further, reapplying the torque as specified.
- Torque Check: While checking for leaks, also verify that the proper torque was applied to the fittings. Use the torque wrench to measure the torque value. The correct torque specifications can usually be found in the vehicle's service manual or the manufacturer's guidelines. Tighten the fittings to the recommended torque value, ensuring they are secure without being over-tightened, which can damage the fittings.
Additional Tips:
- Always wear protective gear, such as gloves and safety goggles, when handling fuel lines to prevent any potential injuries.
- If you suspect a leak, do not ignore it. Leaks can lead to fuel contamination, engine performance issues, and potential safety hazards.
- Keep the fuel system clean and free from contaminants to ensure optimal performance.
- Regularly inspect the fuel lines and fittings, especially after any maintenance or repair work, to maintain the vehicle's overall health.
By following these steps, you can effectively test for leaks and ensure that the fuel line fittings are installed correctly, providing a reliable and safe fuel system for your vehicle.
Clogged Fuel Return Line: Engine Performance and Safety Risks
You may want to see also
Frequently asked questions
The recommended torque value for fuel line fittings can vary depending on the specific application and the manufacturer's guidelines. It's crucial to consult the vehicle's service manual or the fitting's specifications to determine the appropriate torque value. Typically, fuel line fittings require a precise torque range to ensure a secure connection without over-tightening, which can lead to damage.
To torque fuel line fittings properly, you'll need a torque wrench. Start by ensuring the engine is cool and the fuel system is empty to avoid any pressure issues. Locate the fitting and apply the specified torque in a clockwise direction, tightening it by hand first to get a feel for the resistance. Then, use the torque wrench to reach the recommended value and tighten further, being careful not to overtighten.
Reusing old fuel line fittings without re-torquing is generally not recommended. Over time, fittings can corrode, become damaged, or lose their sealing properties. Even if the fittings appear intact, the torque value might have changed due to wear and tear. It's best to replace old fittings and re-torque them to ensure a safe and reliable fuel system.
Overtightening fuel line fittings can lead to several issues. The excessive force can damage the fittings, causing cracks or even breaking them. It may also result in fuel leaks, as the fittings can become stripped or the seals compromised. Additionally, overtightening can lead to reduced fuel flow and potential engine performance problems. Always follow the recommended torque specifications to avoid these risks.
Yes, a torque wrench is essential for torqueing fuel line fittings accurately. It provides the necessary precision to apply the correct amount of force. Different types of torque wrenches are available, such as beam-style or digital, each with its own advantages. Ensure you choose the appropriate size and type for the torque value required by your application.