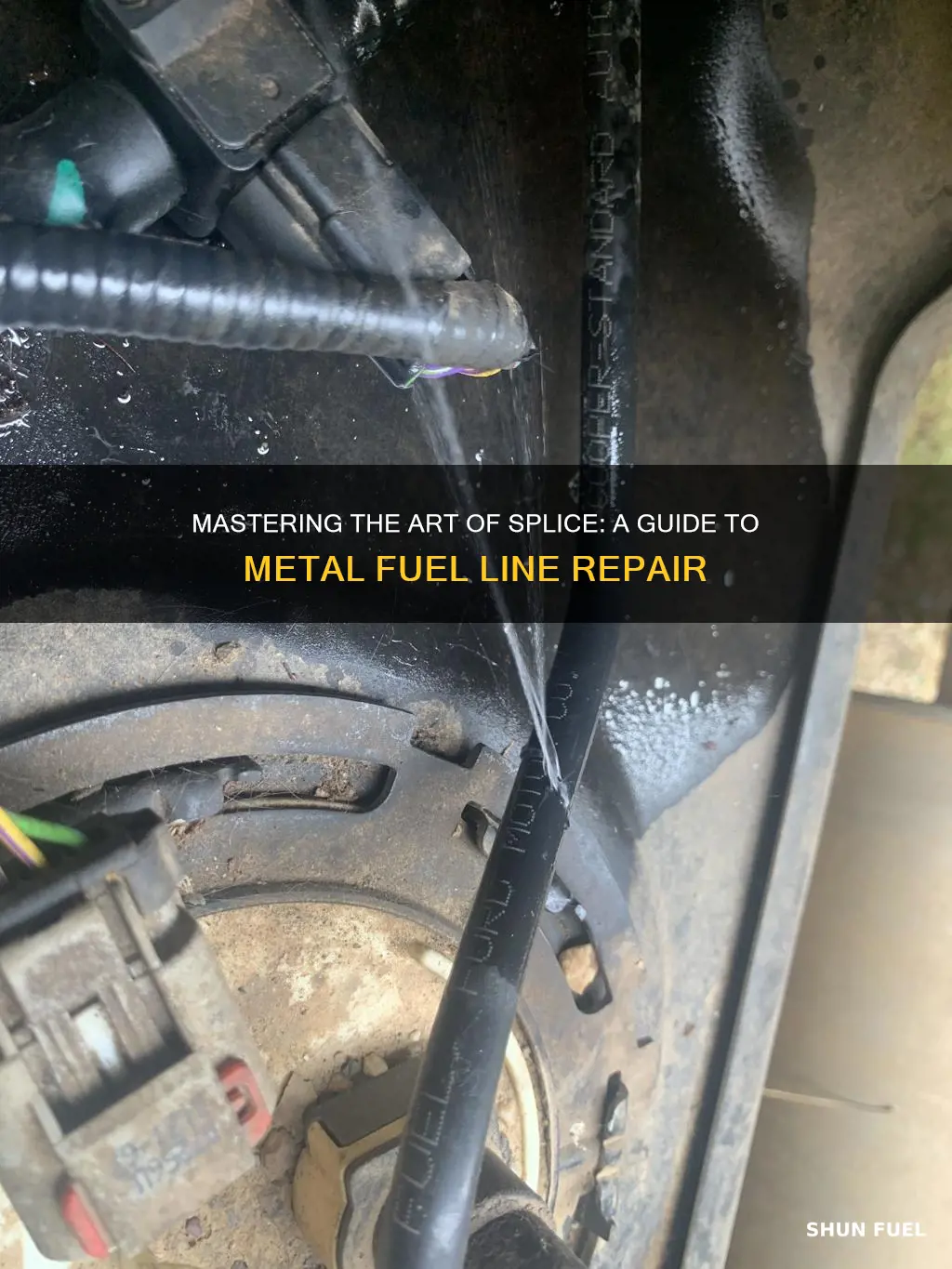
Splicing into a metal fuel line requires careful preparation and adherence to safety guidelines. This process involves connecting a new section of pipe to an existing metal fuel line, often to repair a damaged or leaking section. It is crucial to understand the specific requirements of the fuel line and the materials involved to ensure a secure and reliable connection. The procedure typically involves cleaning and preparing the ends of the fuel lines, using the appropriate tools and techniques to create a tight seal, and ensuring the splice is strong enough to handle the pressure and flow of the fuel. This guide will provide a step-by-step approach to achieving a successful splice.
What You'll Learn
- Safety Gear: Wear protective clothing, gloves, and eye protection to avoid injury
- Line Inspection: Check for damage, corrosion, or leaks before splicing
- Splicing Tools: Use the right tools like a metal-lined splice kit and a torch
- Preparation: Clean and deburr the ends of the fuel lines to ensure a tight fit
- Splicing Technique: Follow a step-by-step process, ensuring the splice is secure and leak-free
Safety Gear: Wear protective clothing, gloves, and eye protection to avoid injury
When working with metal fuel lines, it's crucial to prioritize safety to prevent any accidents or injuries. Here's a detailed guide on the essential safety gear you should wear:
Protective Clothing: Opt for durable and fire-resistant clothing specifically designed for such tasks. This could include a full-body suit or coveralls made from materials like aramid fiber or flame-resistant cotton. The clothing should be long-sleeved and cover your entire body to protect against potential splashes, burns, or contact with hazardous substances. Look for clothing that is also heat-resistant, as you might be working with hot surfaces or flames during the splicing process.
Gloves: Choose heavy-duty gloves that provide a secure grip and protect your hands from sharp edges, burns, and chemical exposure. Leather or Kevlar gloves are excellent choices for their durability and heat resistance. Ensure the gloves fit well to allow for dexterity while still offering adequate protection. Consider gloves with a textured surface for better grip, especially when handling small tools or components.
Eye Protection: Safety goggles or a face shield are essential to safeguard your eyes from potential hazards. Metal fuel lines can release hot gases, sparks, or debris during splicing, which can cause severe eye damage. Look for impact-resistant goggles that provide a secure fit and full coverage to protect your eyes and the surrounding area. Some goggles also offer side protection, ensuring a comprehensive shield against flying particles.
Additionally, consider wearing a respirator or a mask to protect your respiratory system from inhaling fumes or dust during the splicing process. This is especially important when working with older fuel lines that may contain hazardous materials. Remember, wearing the right safety gear is non-negotiable to ensure your well-being and prevent any accidents while splicing into a metal fuel line.
Gravely 812 Fuel Line: Sources for Your Outdoor Power Equipment
You may want to see also
Line Inspection: Check for damage, corrosion, or leaks before splicing
Before attempting to splice into a metal fuel line, it is crucial to conduct a thorough inspection of the line to ensure safety and the success of the repair. This initial step is often overlooked but is essential to prevent further issues and potential hazards. Here's a detailed guide on how to inspect the fuel line for damage, corrosion, or leaks:
- Visual Inspection: Start by visually examining the fuel line. Look for any visible signs of damage, such as cuts, punctures, or tears. These could be caused by various factors, including road debris, previous repair attempts, or even the line's natural wear and tear. Pay close attention to any areas where the line bends around objects or where it is subjected to tension, as these spots are more susceptible to damage. Also, check for any signs of corrosion, which might appear as rust-colored stains or a powdery substance on the line's surface. Corrosion can weaken the line's integrity over time.
- Leaks and Discoloration: Inspect the fuel line for any signs of leaks. This can be done by applying a small amount of soapy water or a leak detection dye to the line's surface. If there are any leaks, you will likely see bubbles forming or the dye seeping out. Additionally, check for discoloration in the fuel line, as this could indicate the presence of contaminants or fuel degradation.
- Pressure Testing: For a more comprehensive assessment, consider using a pressure testing method. This involves temporarily blocking the fuel line and applying pressure to the system. If the line is intact, it should hold the pressure without any leaks. This test can help identify hidden damage or corrosion that might not be visible during a visual inspection.
- Documentation and Note-Taking: As you inspect the fuel line, take detailed notes and document any issues found. Note the location, severity, and any other relevant information about the damage or corrosion. This documentation will be invaluable when planning the splicing process, as it will guide your approach and ensure you address all critical areas.
By following these inspection steps, you can identify potential problems and ensure that the fuel line is in a suitable condition for splicing. This proactive approach is essential to maintaining the safety and efficiency of the fuel system in vehicles or industrial applications. Remember, proper inspection and preparation are key to a successful and safe splicing procedure.
Choosing the Right Fuel Line for Your Side-by-Side Adventure
You may want to see also
Splicing Tools: Use the right tools like a metal-lined splice kit and a torch
When splicing into a metal fuel line, having the right tools is crucial to ensure a successful and safe repair. One essential tool is a metal-lined splice kit, which is specifically designed for this purpose. This kit typically includes a variety of metal sleeves, rings, and adapters that can be used to create a secure and durable connection between the fuel line and the existing pipe. The metal lining provides a strong and reliable bond, ensuring that the splice will withstand the pressure and temperature changes that fuel lines experience.
In addition to the splice kit, a torch is an indispensable tool for this process. A torch, or a gas-powered cutting and welding tool, allows you to precisely cut and join the metal fuel line. It provides the heat and control needed to melt and fuse the metal, creating a strong and permanent bond. When using a torch, it's important to have a steady hand and a good understanding of the technique to avoid damaging the fuel line or causing a leak.
Here's a step-by-step guide on how to use these tools effectively: First, ensure you have a clean and dry work area. Prepare the fuel line by cutting it to the desired length, making sure to leave a few extra inches for the splice. Then, carefully select the appropriate metal-lined splice kit components based on the diameter and condition of the fuel line. Slide the metal sleeve or ring onto the fuel line, ensuring it is centered and secure. Use the torch to heat the metal splice kit until it becomes soft and malleable. Carefully press the heated metal onto the fuel line, creating a solid bond. Allow the splice to cool and cure according to the manufacturer's instructions.
Remember, when working with torches and hot metal, safety should always be a top priority. Wear protective gear, including heat-resistant gloves and safety goggles, to safeguard yourself from potential burns and sparks. Additionally, ensure proper ventilation in the work area to avoid inhaling any harmful fumes.
With the right tools and a careful approach, splicing into a metal fuel line can be a manageable task. The metal-lined splice kit and torch provide the necessary strength and precision to create a reliable connection, ensuring your fuel system remains efficient and leak-free. Always follow manufacturer guidelines and safety protocols for the best results.
Mastering Fuel Line Sizing: The Ultimate Guide to 3/8" Fuel Line Fitting
You may want to see also
Preparation: Clean and deburr the ends of the fuel lines to ensure a tight fit
Before attempting to splice into a metal fuel line, it is crucial to ensure that the preparation process is thorough and meticulous. The first step in this process is to clean and deburr the ends of the fuel lines. This step is essential to guarantee a tight and secure fit, preventing any potential leaks or damage during the splicing process.
To begin, use a wire brush or a specialized deburring tool to remove any dirt, rust, or old fuel residue from the ends of the fuel lines. Focus on the areas where the lines will be joined, ensuring that the surface is clean and free from any contaminants. It is important to be thorough and patient during this step to achieve the best results.
Next, inspect the cleaned surfaces for any remaining burrs or sharp edges. Burrs can cause friction and potentially damage the fuel lines or the splicing tool. Use a fine-grit sandpaper or a deburring compound to carefully remove these burrs, creating a smooth and even surface. Take your time and work in small sections to ensure precision.
After cleaning and deburring, it is beneficial to apply a thin layer of fuel line primer or a suitable adhesive to the prepared surfaces. This step helps to ensure a strong bond between the new splice and the existing fuel line. Allow the primer to dry completely according to the manufacturer's instructions before proceeding with the splicing process.
By taking the time to properly clean and deburr the fuel lines, you create a solid foundation for a successful splice. This preparation step is often overlooked but is critical to the overall integrity and safety of the fuel line system. It ensures that the splice will withstand the pressure and temperature variations commonly experienced in automotive applications.
Toyota Fuel Line Removal: A Step-by-Step Guide for Injector Access
You may want to see also
Splicing Technique: Follow a step-by-step process, ensuring the splice is secure and leak-free
Before you begin the splicing process, ensure you have the necessary tools and materials, including a metal fuel line, a suitable splicing kit (which may include a coupling, ferrule, and crimping tool), and a source of heat if required for your specific splicing method. It's crucial to understand the specific requirements of your fuel line and the splicing technique you plan to use.
Step 1: Prepare the Fuel Line Ends
Carefully cut the fuel line to expose the desired length of the metal for splicing. Ensure a clean and precise cut, removing any burrs or sharp edges that could compromise the splice's integrity. If your fuel line has a protective coating, carefully remove it to expose the raw metal surface.
Step 2: Assemble the Splicing Kit
Follow the manufacturer's instructions to assemble your splicing kit. This typically involves inserting the coupling or ferrule onto the fuel line end, ensuring it is aligned correctly. The coupling or ferrule will provide a secure connection point for the splice.
Step 3: Apply Splicing Material (if required)
Some splicing techniques involve using a special splicing material or adhesive. If this is the case, carefully apply the material to the exposed metal surfaces, following the manufacturer's guidelines for coverage and drying time. This step ensures a strong bond between the splice and the fuel line.
Step 4: Crimp or Weld the Splicing Connection
This step varies depending on your chosen splicing method. For a crimp splice, use the crimping tool to apply pressure to the coupling or ferrule, creating a secure connection. For welding, follow the appropriate welding procedure, ensuring the splice is strong and free of defects.
Step 5: Test for Leaks
After completing the splice, it's crucial to test for any leaks. Use a soapy water solution or a specialized leak detection kit to inspect the splice and the surrounding area. If any leaks are detected, carefully identify the source and re-splicing may be necessary.
Step 6: Final Inspection
Once you've confirmed there are no leaks, perform a final inspection to ensure the splice is secure and aesthetically pleasing. Check for any sharp edges or protruding parts that could cause damage or interference. Make any necessary adjustments to ensure a smooth and seamless connection.
Remember, splicing a metal fuel line requires precision and attention to detail. Always refer to the specific instructions provided with your splicing kit, and if in doubt, consult a professional for guidance.
Evinrude Outboard Fuel Line Sizing: 1999 200 HP Guide
You may want to see also
Frequently asked questions
Splicing into a metal fuel line is a technique used to connect two sections of fuel line or to repair a damaged section. It ensures a secure and leak-free connection, allowing for the safe transfer of fuel in automotive or industrial applications.
Before splicing, ensure the metal fuel line is clean and free of any debris or contaminants. Use a wire brush or a specialized cleaner to remove any corrosion or old fuel residue. Prepare the ends of the fuel line by deburring and smoothing the edges to create a clean and flat surface for the splice.
You will need a metal fuel line splice kit, which typically includes a ferrule or sleeve, a crimping tool, and a fuel line clamp. Choose the appropriate size of ferrule or sleeve that matches the diameter of your fuel line. Ensure you have the necessary tools for crimping and clamping, following the manufacturer's instructions for each tool.
While temporary fixes or quick-connect methods might be suitable for short-term solutions, they are not recommended for permanent or long-term use. Splicing provides a more secure and reliable connection, ensuring the integrity of the fuel system over time. It is essential to follow proper splicing techniques for safety and performance.
Absolutely. When splicing into a metal fuel line, always work in a well-ventilated area and wear appropriate personal protective equipment, such as gloves and safety goggles. Be cautious of fuel line pressure and ensure the engine is off and the fuel system is depressurized before starting the splicing process. Follow safety guidelines and consider seeking professional assistance if you are unsure about any step.