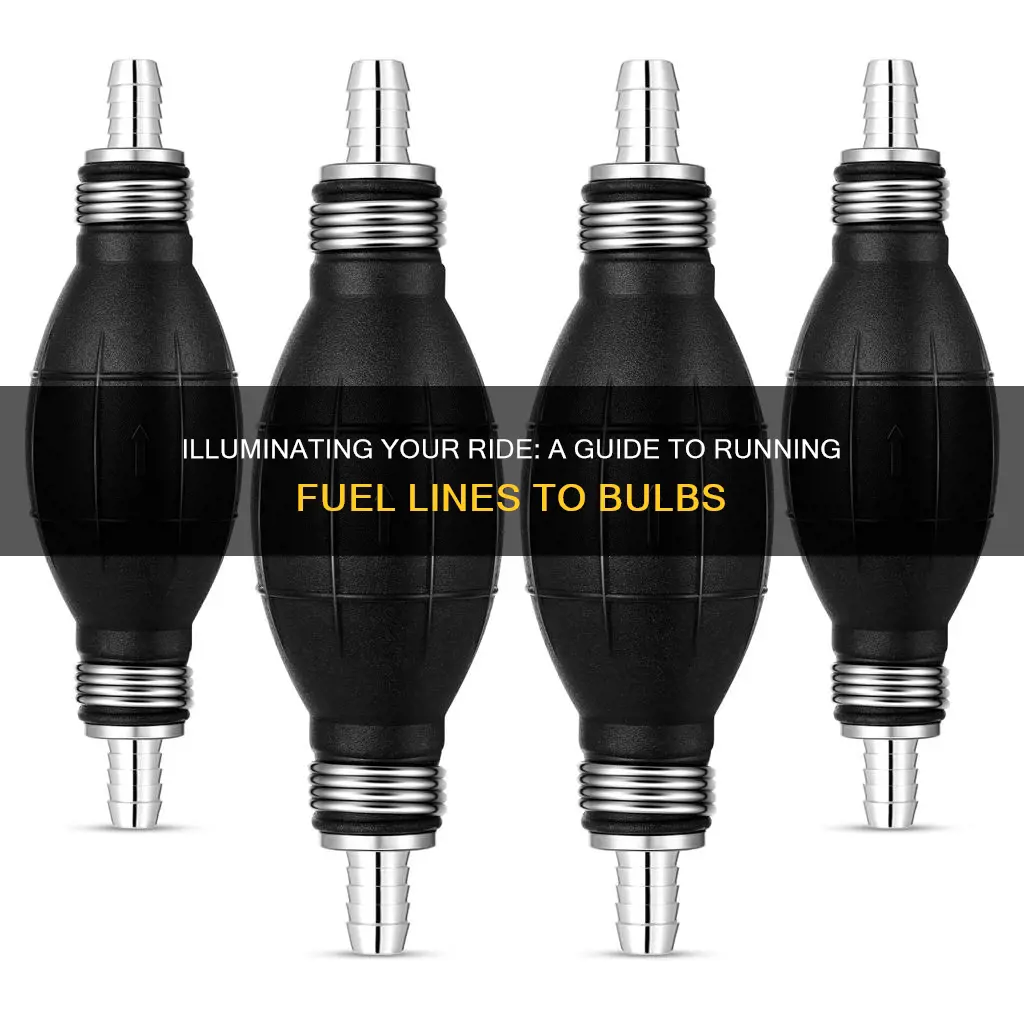
Running fuel lines to a bulb is a common automotive task that requires careful planning and execution to ensure the system is reliable and safe. This process involves connecting the fuel source to the bulb, which can be a challenging task due to the need for precise routing and secure attachments. The steps involve identifying the appropriate fuel line size and material, ensuring compatibility with the bulb's requirements, and properly securing the connections to prevent leaks and ensure optimal performance. This guide will provide a detailed overview of the process, including tips for successful installation and troubleshooting common issues.
What You'll Learn
- Route Planning: Map out the optimal path for fuel lines, considering vehicle structure and bulb placement
- Material Selection: Choose appropriate fuel line material for durability and compatibility with fuel type
- Fittings and Connectors: Use correct fittings and connectors for secure and leak-free connections
- Routing Techniques: Employ techniques like loops, bends, and sleeves to protect lines from damage
- Testing and Inspection: Thoroughly test and inspect fuel lines for leaks and proper functionality before installation
Route Planning: Map out the optimal path for fuel lines, considering vehicle structure and bulb placement
When planning the route for fuel lines to reach the bulbs, it's crucial to consider the vehicle's structure and the bulbs' placement to ensure a safe and efficient setup. Here's a step-by-step guide to help you map out the optimal path:
- Understand the Vehicle's Anatomy: Begin by familiarizing yourself with the vehicle's layout. Identify the engine compartment, the firewall (if present), and the areas where the fuel tank and bulbs are located. Understanding the vehicle's structure will help you decide on the best entry and exit points for the fuel lines. For instance, if the fuel tank is in the rear, you might need to run the lines through the firewall to access the front-mounted bulbs.
- Assess Bulb Placement: Determine the exact location of the bulbs. Some vehicles have bulbs mounted in easily accessible areas, while others might require more intricate routing. Consider the bulb's orientation and any obstructions around it. For instance, if the bulb is located near the dashboard, you'll need to plan a route that avoids any sharp bends or tight spaces that could restrict fuel flow.
- Map Out the Route: Using a diagram or a physical model of the vehicle, start plotting the path for the fuel lines. Aim for a route that is as direct and straightforward as possible. Here are some key considerations:
- Entry Point: Choose an appropriate entry point for the fuel lines, typically near the fuel tank. Ensure there are no critical components or hot surfaces that could damage the lines.
- Routing Through the Compartment: Run the lines through the engine compartment, keeping them away from moving parts and high-temperature areas. Use appropriate protective sleeves or conduits to shield the lines from potential hazards.
- Firewall Considerations: If the fuel tank is on the opposite side of the firewall from the bulbs, carefully plan the route through the firewall. This might involve using specialized fittings or adapting the lines to fit through the small openings.
Optimize for Safety and Efficiency: As you plan the route, prioritize safety and efficiency:
- Avoid sharp bends and kinks in the fuel lines, as these can restrict flow and potentially cause damage over time.
- Ensure the lines are not too close to heat sources or under heavy load-bearing areas.
- Consider using flexible fuel lines that can accommodate slight bends and movements without compromising performance.
Finalize and Secure: Once you've mapped out the optimal route, secure the fuel lines in place. Use appropriate fasteners, clips, or ties to keep the lines organized and prevent them from coming loose during operation. Regularly inspect the routing to ensure it remains intact and free from damage.
Remember, proper route planning is essential to ensure the fuel lines function correctly and safely. By considering the vehicle's structure and bulb placement, you can create a well-organized and efficient fuel line routing system.
Brake Line Magic: Can It Work for Diesel Fuel Lines?
You may want to see also
Material Selection: Choose appropriate fuel line material for durability and compatibility with fuel type
When it comes to selecting the right material for fuel lines, especially when connecting to a bulb, the primary goal is to ensure durability and compatibility with the fuel type. The fuel line material should withstand the corrosive nature of different fuels, such as gasoline, diesel, or even ethanol blends, and remain flexible over a wide temperature range. This is crucial to prevent leaks and ensure the system's longevity.
One of the most commonly used materials for fuel lines is rubber, which offers excellent flexibility and resistance to most fuel types. Natural rubber is a traditional choice, providing a good balance of durability and cost-effectiveness. However, it may not be the best option for high-temperature environments or when dealing with fuels containing ethanol, as it can degrade over time. For these cases, synthetic rubber, such as neoprene or EPDM (ethylene propylene diene monomer), is preferred due to its enhanced resistance to heat and ethanol.
For applications requiring even higher performance, such as high-pressure fuel systems or those operating in extreme temperatures, braided stainless steel fuel lines are an excellent choice. These lines are known for their exceptional strength, flexibility, and resistance to corrosion. The stainless steel braiding provides a durable outer layer, while the inner material can be chosen to suit the fuel type, such as a rubber or plastic compound. This combination ensures a reliable and long-lasting fuel supply to the bulb.
In addition to the material's inherent properties, it's essential to consider the manufacturing process and any additional coatings or treatments. Some manufacturers use specialized coatings to protect the fuel line material from fuel degradation, ensuring a longer lifespan. For instance, a protective layer of zinc or a specialized fuel-resistant rubber coating can be applied to the inner surface of the fuel line to prevent fuel from coming into direct contact with the material, thus reducing the risk of corrosion and degradation.
When choosing the material, it's also important to consider the overall system design and installation. The fuel lines should be routed carefully to avoid sharp bends or kinks, which can stress the material and lead to premature failure. Proper support and protection, such as fuel line guards or clips, can help maintain the integrity of the fuel lines and ensure a safe and efficient fuel supply to the bulb.
Oregon vs. Tygon: Choosing the Best Fuel Line for Your Needs
You may want to see also
Fittings and Connectors: Use correct fittings and connectors for secure and leak-free connections
When working on fuel line installations, especially when connecting to a bulb, it's crucial to use the right fittings and connectors to ensure a secure and leak-free system. The primary goal is to maintain the integrity of the fuel supply while ensuring the safety of the vehicle. Here's a detailed guide on the importance of using appropriate fittings and connectors:
Understanding the Importance of Fittings and Connectors:
Fittings and connectors play a vital role in joining fuel lines to various components, including bulbs, pumps, and tanks. These components must be designed to withstand the pressure and temperature variations associated with fuel systems. Using the correct fittings ensures that the fuel lines remain tightly sealed, preventing any potential leaks that could lead to dangerous situations, such as fuel spills or fires. Additionally, proper connectors facilitate easy assembly and disassembly, making maintenance and repairs more accessible.
Choosing the Right Fittings:
Select fittings that are compatible with the fuel line material and the specific application. Common materials for fuel lines include rubber, vinyl, and braided steel. Each material requires a specific type of fitting to ensure a secure seal. For example, rubber fuel lines often use compression fittings, which involve compressing the fitting onto the line to create a tight seal. Vinyl lines might use quick-connect fittings for convenience. Always refer to the manufacturer's guidelines or consult a technical manual to determine the appropriate fitting type.
Connector Selection:
Connectors are essential for joining fuel lines to various components. When choosing connectors, consider factors such as the type of fuel line, the application, and the ease of installation. For instance, bulb-to-line connections might require specialized connectors that provide a secure and reliable seal. Some connectors use O-rings or gaskets to create a tight seal, while others might employ clips or clips for a more secure hold. Ensure that the connectors are compatible with the fuel line diameter and material to avoid any potential leaks or damage.
Installation Techniques:
Proper installation techniques are crucial to achieving a leak-free connection. When connecting fittings and connectors, ensure a tight fit by following the manufacturer's instructions. Over-tightening can damage the fuel line, while under-tightening may result in leaks. Use the appropriate tools, such as wrenches or pliers, to secure the fittings without applying excessive force. Take the time to inspect the connections regularly, especially in high-pressure areas, to identify and address any potential issues promptly.
Testing and Inspection:
After installing the fuel lines and connectors, it is essential to test the system for leaks. Use a soapy water solution or a specialized fuel line leak detector to identify any potential issues. Inspect all connections, including the bulb-to-line interface, to ensure there are no visible signs of damage or leakage. Proper testing ensures that the fuel system is safe and functional, reducing the risk of unexpected failures.
Toyota Fuel Line Removal: A Step-by-Step Guide for Beginners
You may want to see also
Routing Techniques: Employ techniques like loops, bends, and sleeves to protect lines from damage
When running fuel lines to a bulb, proper routing techniques are essential to ensure the lines are secure, protected from damage, and comply with safety regulations. Here are some detailed methods to achieve this:
Loops and Bends: One of the most common and effective techniques is to create loops and bends in the fuel lines. This method helps to secure the lines and prevent them from being pulled or damaged. Start by identifying the length of the line you need to route. Then, create a loop at the beginning and end of the line to provide a secure anchor point. Bends should be made at regular intervals along the line to maintain tension and prevent kinking. Ensure that the bends are gentle and do not create sharp angles that could lead to damage or restriction.
Sleeve Protection: Fuel lines are vulnerable to damage from sharp edges, vibrations, and heat sources. To protect the lines, consider using sleeves made of flexible, durable materials such as rubber or plastic. Slide the sleeve over the fuel line, ensuring it covers any potential areas of contact with other components or surfaces. This protective layer safeguards the line from abrasion and impact, especially in areas where the line passes through tight spaces or near moving parts.
Routing Channels: Designate specific channels or paths for the fuel lines to follow. This can be achieved by creating small grooves or channels in the surrounding components or using dedicated routing channels provided by the manufacturer. Ensure that the channels are wide enough to accommodate the fuel lines and allow for slight movement. This technique helps to keep the lines organized and reduces the risk of damage from sharp turns or collisions with other parts.
Secure Anchors: At regular intervals, secure the fuel lines using anchors or ties. These anchors can be small clips, ties, or even specialized fuel line anchors. Secure the lines at the bulb, any joints, and where they cross other components. This prevents the lines from becoming loose or tangled and minimizes the risk of damage during vehicle operation or maintenance.
By employing these routing techniques, you can effectively protect the fuel lines from potential hazards and ensure a safe and efficient fuel supply to the bulb. Remember to follow the manufacturer's guidelines and consider the specific requirements of your vehicle's fuel system for optimal results.
Understanding B1 Fuel Line: A Comprehensive Guide
You may want to see also
Testing and Inspection: Thoroughly test and inspect fuel lines for leaks and proper functionality before installation
Before proceeding with the installation of fuel lines to a bulb, it is crucial to conduct a comprehensive testing and inspection process to ensure the system's safety and reliability. This step is often overlooked but is essential to prevent potential issues and costly repairs down the line. Here's a detailed guide on how to thoroughly test and inspect the fuel lines:
Leak Testing: Start by identifying the fuel lines that will be connected to the bulb. Ensure you have the necessary tools, including a soapy water solution or a specialized fuel line leak detector. Clean the fuel lines and the bulb's fuel ports to remove any dirt or contaminants. Then, carefully apply the soapy water solution or leak detector to the connections and along the length of the fuel lines. Look for any bubbles forming on the surface, which indicates a potential leak. If bubbles are present, carefully inspect the area to locate the source of the leak. This step is critical as fuel leaks can lead to dangerous situations, including fire hazards and environmental contamination.
Pressure Testing: Fuel lines should be able to withstand the pressure of the fuel system. Set up a pressure testing setup by connecting the fuel lines to a test gauge and the bulb's fuel supply. Gradually increase the pressure and monitor the gauge for any drops or fluctuations. The fuel lines should maintain stable pressure without any leaks or signs of damage. If the pressure drops, it may indicate a blockage or a weak point in the line. This test is essential to ensure the fuel system's integrity and to identify any potential issues before installation.
Functionality Check: After confirming there are no leaks, it's time to test the fuel lines' functionality. Start the engine and monitor the fuel flow. Check for any unusual noises, such as hissing or gurgling, which could indicate a restriction or air in the line. Ensure that the fuel is delivered smoothly and consistently to the bulb. If the engine runs erratically or stalls, it may suggest a problem with the fuel lines or the bulb's fuel supply. This step helps verify that the fuel lines are capable of delivering the required fuel volume and pressure to the bulb.
Visual Inspection: A thorough visual inspection is essential to identify any physical damage or wear. Examine the fuel lines for any signs of cracks, punctures, or kinks. Check for sharp bends or twists that might cause damage during installation. Look for any signs of corrosion or degradation, especially if the lines have been exposed to harsh conditions. Ensure that all connections are secure and free from any debris or contaminants. This visual assessment will help you catch potential issues early on and ensure a smooth installation process.
By following these testing and inspection procedures, you can guarantee that the fuel lines are in optimal condition, ready for a successful installation. It is a critical step that should not be rushed, as it directly impacts the safety and performance of the fuel system.
Understanding the Linear Fuel Mass Model: A Comprehensive Guide
You may want to see also