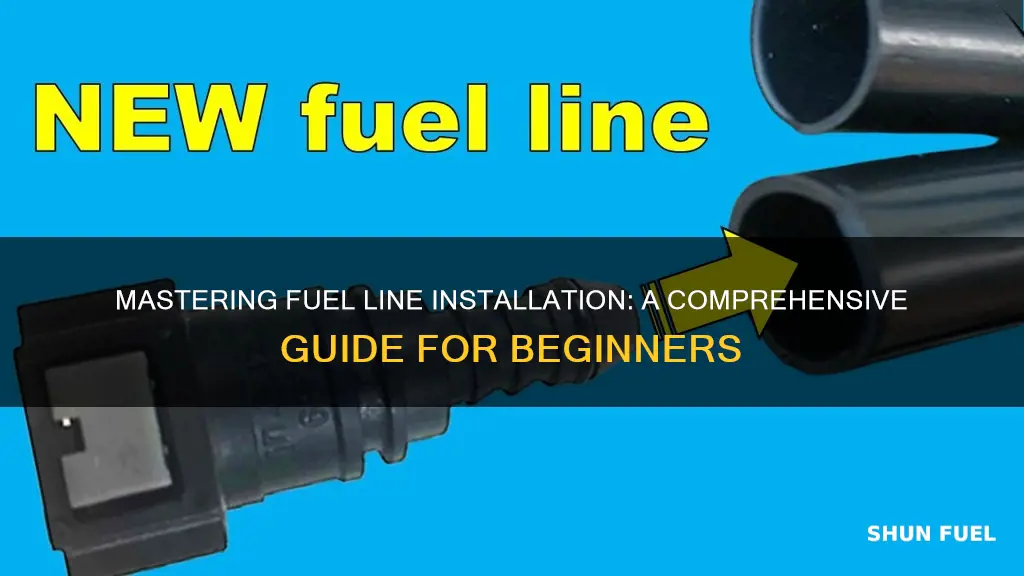
Running fuel lines is a crucial step in any vehicle maintenance or repair project. It involves connecting the fuel tank to the engine, ensuring a steady supply of fuel for optimal performance. This process requires careful planning and execution to prevent fuel leaks and ensure the system's reliability. The steps typically include selecting the appropriate fuel lines, preparing the connections, and securely attaching the lines to the fuel pump and engine block. Proper installation is essential to maintain the vehicle's efficiency and safety.
What You'll Learn
- Fuel Line Routing: Ensure proper placement to avoid damage and maintain fuel flow
- Clamps and Fittings: Use secure, compatible clamps and fittings for a tight seal
- Fuel Filter Maintenance: Regularly check and replace filters to prevent contamination
- Pressure Testing: Test fuel lines for leaks and pressure to ensure optimal performance
- Material Selection: Choose appropriate materials for fuel lines based on vehicle requirements
Fuel Line Routing: Ensure proper placement to avoid damage and maintain fuel flow
Fuel line routing is a critical aspect of vehicle maintenance that often requires careful consideration to ensure optimal performance and longevity. Proper placement of fuel lines is essential to prevent damage and maintain a consistent fuel flow throughout the engine's operation. Here's a comprehensive guide to help you navigate this process:
When running fuel lines, the primary goal is to maintain a secure and direct path from the fuel tank to the engine. Start by identifying the fuel lines' intended route, which is typically along the vehicle's frame or beneath the body panels. It's crucial to keep the lines away from moving parts, such as the exhaust system and suspension components, to avoid potential damage during operation. Begin by laying out the fuel lines along the chosen path, ensuring they are not kinked or twisted, as this can restrict fuel flow and cause potential issues.
Secure the fuel lines using appropriate clamps or brackets to prevent movement and potential damage. The lines should be tightly fastened to the vehicle's body or frame, providing a stable foundation. Avoid tight bends or sharp turns in the fuel lines, as these can lead to fuel restriction and potential engine performance issues. Instead, aim for a smooth, gentle curve to allow for expansion and contraction due to temperature changes.
Pay close attention to the engine bay, as this area is prone to various components that could potentially damage the fuel lines. Route the lines away from intake manifolds, exhaust systems, and other high-heat sources to prevent melting or damage. Consider using protective sleeves or insulation to shield the fuel lines from these potential hazards. Additionally, ensure that the lines are not pinched or compressed, as this can restrict fuel flow and cause engine misfires.
In some cases, you might encounter the need to cross or pass over other components. When this happens, it's essential to use appropriate protective measures. For example, if a fuel line needs to cross a suspension component, consider using a rubber or plastic shield to protect the line from potential damage. Proper insulation and shielding will ensure the fuel lines remain intact and functional over time.
Regularly inspect the fuel lines for any signs of wear, damage, or leaks. Over time, fuel lines can deteriorate due to fuel contamination, heat, or physical stress. Look for any cracks, brittleness, or signs of corrosion, and replace the lines if necessary. Maintaining a clean and well-maintained fuel system is crucial for optimal engine performance and longevity.
Cold Weather's Impact: Why Diesel Gels in Fuel Lines
You may want to see also
Clamps and Fittings: Use secure, compatible clamps and fittings for a tight seal
When it comes to running fuel lines, ensuring a tight and secure seal is crucial to prevent leaks and maintain the integrity of your fuel system. One of the key components to achieving this is the use of appropriate clamps and fittings. Here's a detailed guide on how to utilize them effectively:
Choosing the Right Clamps and Fittings:
Start by selecting clamps and fittings that are specifically designed for fuel lines. These components should be made from materials compatible with the fuel type you are using, typically gasoline or diesel. Look for clamps with a robust construction and a secure grip to ensure they can withstand the pressure and movement within the fuel system. Common types include metal or plastic clamps with adjustable or fixed-width designs.
Measuring and Positioning:
Accurate measurement is essential. Ensure that the fuel lines are properly sized to fit the clamps and fittings. Measure the diameter of the fuel lines and choose clamps with an appropriate inside diameter to provide a snug fit. Position the clamps at regular intervals along the fuel lines, typically every 6 to 12 inches, to secure the lines and prevent sagging or bending.
Installation Technique:
When installing the clamps, apply firm pressure to create a tight seal. Avoid using excessive force, as it may damage the fuel lines. Instead, use the appropriate tools, such as a clamp pliers or a hydraulic clamp tool, to ensure a secure grip. Ensure that the clamps are positioned correctly, with the fuel line centered and the clamp's screw or adjustment mechanism tightened securely.
Compatibility and Material Considerations:
Always check the compatibility of the clamps and fittings with the fuel lines and the overall fuel system. Some materials may require specific types of clamps to avoid damage. For example, rubber or plastic fuel lines might need soft-faced clamps to prevent scratching or puncturing. Additionally, consider the temperature and environmental conditions your fuel system will operate in to ensure the chosen clamps can withstand those factors.
Regular Inspection and Maintenance:
Regularly inspect the clamps and fittings for any signs of wear, corrosion, or damage. Over time, clamps can loosen or degrade, so it's essential to check and tighten them periodically. Keep the fuel lines clean and free from debris to prevent blockages and ensure optimal performance.
Understanding the Fuel Tank Return Line: A Comprehensive Guide
You may want to see also
Fuel Filter Maintenance: Regularly check and replace filters to prevent contamination
Fuel filter maintenance is a crucial aspect of vehicle care that often goes overlooked. Regularly checking and replacing fuel filters is essential to ensure optimal engine performance and prevent contamination that can lead to costly repairs. Here's a comprehensive guide to help you understand the importance of this maintenance task and how to perform it effectively.
Over time, fuel lines and filters can accumulate contaminants such as dirt, moisture, and debris. These impurities can originate from various sources, including the fuel tank, fuel pump, and even the air intake system. When left unchecked, these contaminants can cause significant issues. For instance, dirt and grime can restrict fuel flow, leading to reduced engine power and potential performance problems. Moisture, on the other hand, can cause corrosion within the fuel system, resulting in expensive repairs. Therefore, regular maintenance is key to preventing these issues.
Checking your fuel filter regularly is a simple yet effective way to identify potential problems early on. Most vehicles have easily accessible fuel filters, often located near the engine or under the car. You can inspect the filter for any signs of contamination, such as a dirty appearance, leaks, or a buildup of debris. If you notice any of these issues, it's time to replace the filter. A clean and well-maintained filter ensures that the fuel flowing to your engine is free from impurities, promoting efficient combustion and overall engine health.
Replacing the fuel filter is a straightforward process that can be done at home with basic tools. Start by locating the filter, which is typically a cylindrical component with an inlet and outlet port. Carefully remove the old filter, being mindful of any fuel that may still be present in the system. After replacing it, ensure that you bleed the fuel lines to remove any air bubbles and prime the fuel pump to ensure proper fuel circulation. This simple maintenance task can save you from potential engine issues and keep your vehicle running smoothly.
In summary, regular fuel filter maintenance is an easy and cost-effective way to keep your vehicle in top condition. By checking and replacing the filters as recommended, you can prevent contamination, maintain optimal engine performance, and avoid costly repairs. Remember, a little preventative care goes a long way in ensuring your car's longevity and reliability.
Ryobi 825R Fuel Line: Size and Compatibility Guide
You may want to see also
Pressure Testing: Test fuel lines for leaks and pressure to ensure optimal performance
Pressure testing is a critical step in ensuring the integrity and performance of fuel lines in any vehicle or machinery. This process involves applying controlled pressure to the fuel lines to check for any potential leaks or weaknesses that could compromise the system's functionality. Here's a comprehensive guide on how to perform this essential test:
Preparation: Before initiating the pressure test, it is crucial to gather the necessary tools and materials. You will require a pressure gauge, preferably a mechanical gauge with a range suitable for fuel line testing. Ensure you have a supply of compressed air or a specialized fuel line testing machine that can generate the required pressure. Additionally, prepare a clean, dry workspace to facilitate the testing process.
Procedure: Start by disconnecting the fuel lines from the fuel tank and any other connected components. This step ensures that the lines are isolated and allows for accurate testing. Then, attach the pressure gauge to one end of the fuel line and the compressed air source to the other. Gradually increase the pressure, typically starting from a low setting and gradually building up. The goal is to reach a pressure that simulates the fuel system's normal operating conditions. As you apply pressure, inspect the fuel lines for any visible signs of leakage, such as fuel dripping or bubbles forming.
During the test, pay close attention to any unusual noises or vibrations that may indicate potential issues. Leaks can often be identified by the presence of fuel vapor or a distinct smell of gasoline. It is essential to test the entire length of the fuel line, including connections and fittings, to ensure no hidden leaks exist. If you detect any leaks, immediately release the pressure and inspect the affected area for damage or corrosion.
Troubleshooting: If leaks are found, address them promptly. Common causes of leaks include damaged fuel lines, faulty fittings, or corrosion. In such cases, consider replacing the affected sections or tightening connections. It is crucial to identify and rectify these issues before retesting. Additionally, check for any signs of fuel contamination or degradation, as this can affect the test results and overall system performance.
Safety Considerations: When performing pressure testing, always prioritize safety. Ensure that the testing area is well-ventilated to prevent the inhalation of fuel vapors. Wear appropriate personal protective equipment, such as gloves and eye protection, to safeguard against potential hazards. It is also advisable to have a fire extinguisher nearby, especially when working with compressed air or fuel.
By following these detailed steps, you can effectively pressure test fuel lines, ensuring they are leak-free and capable of withstanding the required pressure. Regular maintenance and testing are essential to maintain the reliability and safety of any fuel-powered system.
Chevy Malibu Fuel Filter: Location and Access Guide
You may want to see also
Material Selection: Choose appropriate materials for fuel lines based on vehicle requirements
When it comes to selecting the right materials for fuel lines, it's crucial to consider the specific requirements of your vehicle. Different vehicles have unique needs, and the choice of material can significantly impact performance, safety, and longevity. Here's a guide to help you make an informed decision:
- Temperature Resistance: One of the primary factors to consider is the temperature range your vehicle operates in. Fuel lines need to withstand extreme temperatures, especially in engines. For high-temperature applications, materials like stainless steel or high-temperature plastics such as polyetheretherketone (PEEK) are excellent choices. These materials offer superior heat resistance, ensuring the fuel lines remain flexible and intact even under intense heat. In contrast, for vehicles operating in colder climates, materials like rubber or flexible hoses with a protective layer can provide the necessary flexibility and insulation.
- Chemical Compatibility: Fuel lines must be compatible with the type of fuel your vehicle uses. Different fuels have varying chemical compositions, and some materials may degrade or become brittle when exposed to certain fuels. For example, gasoline-specific fuel lines should be made from materials resistant to gasoline's solvents and additives. Similarly, diesel fuel lines require materials that can withstand the fuel's higher temperature and pressure. Always refer to the vehicle's manual or consult experts to determine the appropriate fuel line material for your specific fuel type.
- Flexibility and Durability: Fuel lines need to be flexible to accommodate engine movement and vibrations during operation. Materials like rubber, silicone, or braided hoses offer excellent flexibility. However, flexibility should not compromise durability. Look for materials that provide a balance between flexibility and strength to ensure the fuel lines can withstand the rigors of the vehicle's environment. Reinforced hoses with layers of fabric or steel wire can offer added protection against punctures and abrasion.
- Pressure Rating: Consider the pressure requirements of your vehicle's fuel system. High-pressure fuel systems, common in modern engines, demand materials with superior pressure-bearing capabilities. Materials like stainless steel or high-performance plastics can handle the increased pressure without compromising performance. Always check the manufacturer's specifications to ensure the chosen material meets or exceeds the required pressure rating.
- Vehicle-Specific Considerations: Different vehicles have unique fuel systems and requirements. For instance, classic cars or vintage vehicles may have specific fuel line materials that were commonly used during their production era. Researching the vehicle's history and consulting with specialists can provide valuable insights. Additionally, consider factors like the vehicle's age, intended use (daily driver or racing), and any modifications made to the fuel system.
Remember, selecting the right material is a critical step in ensuring the safe and efficient operation of your vehicle's fuel system. Always consult vehicle manuals, seek expert advice, and consider the specific needs of your vehicle to make an informed choice.
Perfect Fuel Line Size for Husqvarna 137 Chainsaw
You may want to see also
Frequently asked questions
Before installing fuel lines, ensure they are clean and free of any debris or contaminants. Inspect the lines for any damage or leaks, and replace any sections that are worn out or compromised. It's crucial to use the correct type of fuel line for your specific application, as different fuels and environments may require specialized materials.
Proper routing is essential to prevent damage and ensure optimal performance. Fuel lines should be routed away from heat sources, vibrations, and sharp edges. Keep the lines as straight as possible to minimize stress and potential leaks. Use appropriate clamps or ties to secure the lines in place, allowing for some flexibility to accommodate movement.
Leaks can be a significant issue, so it's important to take preventive measures. Ensure all connections are tight and secure, using the right type of fuel line connectors for your fuel type. Regularly inspect the lines for any signs of damage, corrosion, or wear, especially at bends and fittings. Applying a suitable fuel-resistant tape or sealant can provide an extra layer of protection.
Regular maintenance is key to keeping fuel lines in good condition. Check for any signs of deterioration, such as cracking, softening, or discoloration. Keep the lines free from clogs and debris by using a fuel filter and regularly replacing it. It's also beneficial to inspect the lines for any signs of contamination, which can be caused by old fuel or improper storage.
Yes, having the right tools can make the installation process easier. You'll need fuel line cutters or knives to make precise cuts, fuel line connectors or fittings suitable for your fuel type, and a fuel filter to ensure clean fuel delivery. Additionally, a fuel line brush can help clean and prepare the lines for installation.