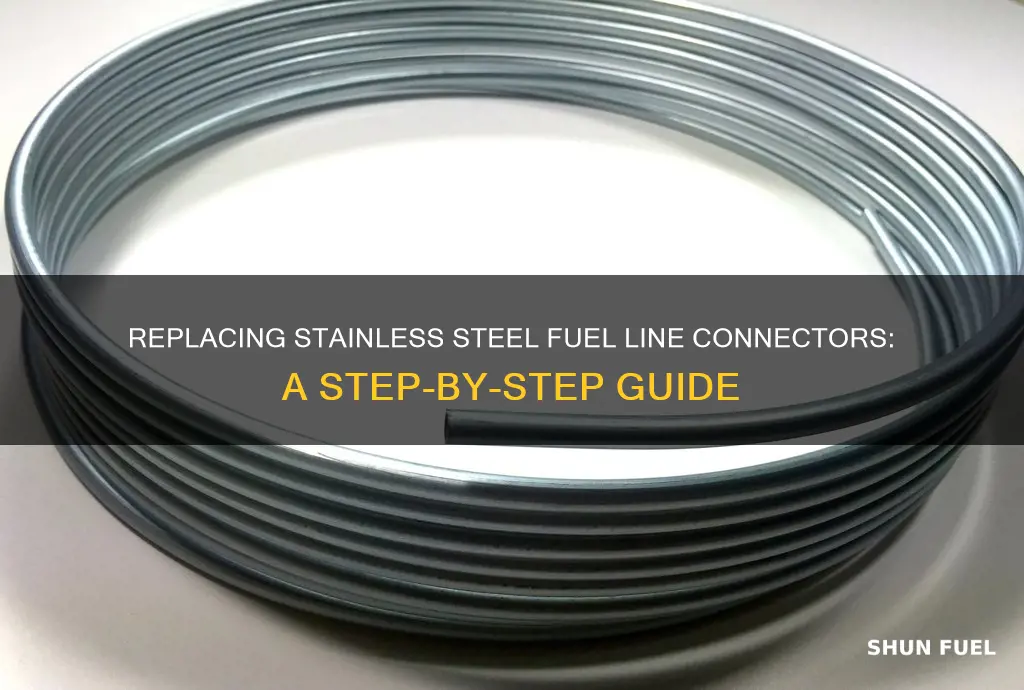
Replacing a stainless steel fuel line connector is a complex task that requires careful attention to safety. The process can vary depending on the make and model of the vehicle, but there are some general guidelines to follow. Before beginning any work, it's important to gather the necessary tools and materials, including a fuel line repair kit, tubing, fittings, and lubricants. It's also crucial to exercise caution when working with flammable liquids and to ensure that all work is done in a well-ventilated area.
How to replace stainless steel fuel line connectors
Characteristics | Values |
---|---|
Required tools | Tube cutter, caulking gun, flaring tool clamp, roll of tubing, fittings, lubricant, line clamp, razor blade or tubing cutter |
Process | Cut tubing, insert into caulking gun, clamp tubing, lubricate fitting, assemble, remove clamp |
Tips | Ensure tubing is rated for fuel, don't use flexible fuel hose for long runs, don't use braid stainless steel lines, use nylon tubing for repairs |
What You'll Learn
Using a steel fuel line repair kit
Step 1: Cut the Steel Fuel Line
Use a tubing cutter or a single-edge razor blade to make a clean cut through the steel fuel line. This step is necessary if you need to remove a damaged section of the line or replace it entirely.
Step 2: Prepare the New Fitting
Lubricate the new fitting lightly. You can use hydraulic jack oil or a similar lubricant. This will help the fitting slide onto the tubing more easily.
Step 3: Secure the Tubing
Insert the cut end of the steel fuel line into a clamp. You can use the clamp from a brake line flaring kit or a wooden clamp if you don't have access to the former. Ensure the clamp corresponds to the size of your tubing. Leave only enough tubing exposed to fit the fitting.
Step 4: Position the Clamp and Tubing
Place the clamp with the tubing into a caulking gun. Ensure the tubing doesn't get kinked in the process. Position the caulking gun so that there is just enough room between the plunger and the tubing to fit the fitting.
Step 5: Attach the Fitting
Hold the fitting and the tubing in alignment, and begin to squeeze the handle of the caulking gun. It usually takes just a few clicks to seat the fitting fully.
Step 6: Release and Inspect
Release the clamp from the tubing. Inspect your work to ensure the fitting is secure and properly attached.
Additional Tips:
- If you're connecting steel lines together, consider using a flare nut and cap fittings. These are typically cheaper and can create a secure connection.
- When splicing in a new section of the fuel line, compression fittings or flaring the line with new fittings and unions are both suitable options.
- Always use fuel-rated hoses or tubing to ensure safety.
- If you're repairing a rusted fuel line, consider replacing the entire line, as the rest of it might not be far behind.
- For a temporary fix, you can try stretching a smaller braided hose over a larger steel hose using a screwdriver. However, this may not create a secure, long-lasting connection.
By following these steps and tips, you can effectively use a steel fuel line repair kit to replace or repair stainless steel fuel line connectors.
Replacing Your Fuel Rail: Step-by-Step Guide for DIY Mechanics
You may want to see also
Joining a steel line with a rubber hose
First, it is important to ensure you are using the correct type of hose. For fuel lines, it is essential to use a hose that is rated for fuel injection, as regular fuel hose cannot withstand the pressure.
Next, you need to prepare the steel line. This involves flaring the end of the line, which can be done with a flaring tool. Flaring the line provides a secure connection and helps to prevent leaks. It is also recommended to use a barbed fitting on the steel line, which will help hold the hose in place and provide a better seal.
Now you are ready to attach the hose. Slide the hose onto the steel line, pushing it on as far as it will go. It may be necessary to use a lubricant to make this process easier. Once the hose is in place, secure it with two "fuel injection" hose clamps. Do not use worm gear clamps, as these can damage the hose.
Finally, check your work carefully for any signs of leaks. Ensure all connections are tight and that the hose is securely clamped in place.
This process will create a safe and secure joint between the steel line and the rubber hose, preventing leaks and ensuring the fuel system functions correctly.
Replacing the Fuel Pump in Your 1991 Ford F150 Truck
You may want to see also
Using nylon tubing
Nylon tubing can be used as a cost-effective and time-efficient repair method when replacing a stainless steel fuel line connector. It is important to note that nylon tubing can be used for an entire length of the fuel line or just a section.
To attach nylon tubing to a steel fuel line, you will need to ensure that the inner diameters of both lines are similar to prevent changes in flow characteristics and increased pressure in the smaller diameter line. You can use a compression-style fitting to merge the two pieces of the fuel line together. It is also recommended to use a flare nut and cap fittings, along with a tubing flare end kit, to ensure a secure connection.
When cutting the tubing, it is best to use a single-edge razor blade or a tubing cutter to ensure a clean cut. To attach the tubing to the fitting, you can use a caulking gun and a line clamp to hold the tubing in place while you assemble the connection. It is also suggested to use a light lubricant on the fitting to aid in the assembly process.
Additionally, nylon tubing should not be heated to attach it to the steel fuel line, as this can cause damage. Instead, you can try using a large Phillips-head screwdriver to pry and stretch the tubing over the steel line. Alternatively, you can spray silicone or motor oil on the steel tube to aid in the connection.
It is important to prioritize safety when working with fuel lines and to ensure that all materials and connections are properly rated for fuel use.
Mustang Fuel Rail Pressure Sensor: DIY Replacement Guide
You may want to see also
Bending your own lines
When bending your own lines, it is important to consider the type of hard line you will be using. There are four types of hard lines used for braking systems: steel, soft steel, stainless steel, and nickel-copper alloy. Each has its benefits and drawbacks.
Steel is the most common type of hard line and is affordable, durable, and easy to find. However, it is hard to bend and prone to rust. Soft steel, on the other hand, is made of low-carbon steel, making it easier to bend. It is coated with Polyvinyl Fluoride (PVF) to protect against corrosion, which is more effective than galvanizing.
Stainless steel is impervious to rust and easy to bend, but it is expensive and difficult to flare. You will need a good-quality flaring tool to make double flares with stainless steel tubing. Finally, nickel-copper hard lines have the strength of steel, are rust-proof, and easy to bend. They are reasonably priced but may be hard to find locally.
When bending your own lines, it is important to have the proper tools. There are several types of tools available, from simple radius tools to more accurate lever-action benders. While you can bend lines by hand, using tools will help you achieve more accurate results. Simple benders are cheap but have a high chance of ruining the tubing. Lever-action benders, on the other hand, use mechanical advantage to make bending lines easier and allow for more complex layouts. Spring-type benders are basic tools meant for gentle, large-diameter bends and are typically used for copper and aluminum tubing.
In addition to the right tools, you should also have the proper fittings and consider the length of the line you are working with. Short lines are much easier to work with than long lines. If you are replacing a line, use the existing line as a reference. If you are creating a new line, you can use bailing wire or a wire coat hanger to create a reference for your bends.
Finally, don't forget about the flares and fittings. Slide the fitting all the way to the flare before bending the line to avoid having to straighten or cut the line. Make sure you map out your bends and don't forget the nut before flaring the line. Bending lines is a skill that anyone can learn, but it does take practice to master.
Replacing Mechanical Fuel Pump on 22R: Step-by-Step Guide
You may want to see also
Buying pre-bent lines
When it comes to replacing fuel lines, one option is to replace the entire line with a pre-bent line. This can be done through aftermarket or new car dealer sources. While this option can be the most expensive and labor-intensive, it offers the longest-lasting repair, returns the vehicle to like-new condition, and prevents future leaks.
If you are considering buying pre-bent lines, there are several factors to keep in mind. Firstly, ensure that pre-bent lines are available for your specific vehicle model. Not all vehicles may have this option. Secondly, look for pre-bent lines that are designed to fit your vehicle exactly like the original equipment manufacturer (OEM) factory lines. This ensures a precise fit and ease of installation.
When buying pre-bent lines, opt for those made from high-quality materials, such as stainless steel, which offer improved durability and corrosion resistance. Some manufacturers offer limited lifetime warranties on their pre-bent lines, providing added assurance and peace of mind. Additionally, consider purchasing from suppliers who offer installation support, such as detailed instructions, installation videos, and live technical assistance.
Another factor to consider is the shipping time for your pre-bent lines. Opt for suppliers who offer fast shipping options to get your vehicle back on the road as soon as possible. Some suppliers even offer free next-day shipping, ensuring that you receive your parts promptly.
In summary, when buying pre-bent lines, verify compatibility with your vehicle, choose high-quality materials, look for installation support, and consider suppliers with fast shipping options. By taking these factors into account, you can make an informed decision and ensure a successful fuel line replacement.
Replacing Gas Tank Fuel Line: Step-by-Step Guide
You may want to see also
Frequently asked questions
It is recommended to use a pushlock fastener of the proper size to match the hard line. You would flare it, use an AN nut and sleeve, then mate it to the pushlock fitting.
It is not recommended to attach a nylon fuel line to a steel fuel line. It is best to replace the line. However, if you must, you can try to stretch the nylon tubing by working a large Phillips-head screwdriver inside of it, prying it side to side. You can also try spraying silicone or motor oil on the steel tube to make it easier to attach the nylon tubing.
There are three options for replacing fuel lines:
- Replace the entire line with a pre-bent line. This is the most expensive and labor-intensive option but it is the longest-lasting repair.
- Bend your own lines. This option requires investing in bending and flaring tools.
- Use nylon tubing and specific fittings. This is a cost-effective and time-efficient option when pre-bent lines are not available.
It is important to avoid reengineering the fuel line routing and mounting methods. Do not replace long runs of hard line with flexible fuel hose as this can be dangerous and difficult to seal. Also, do not use braid stainless steel lines unless it is for a racecar or rock crawler.