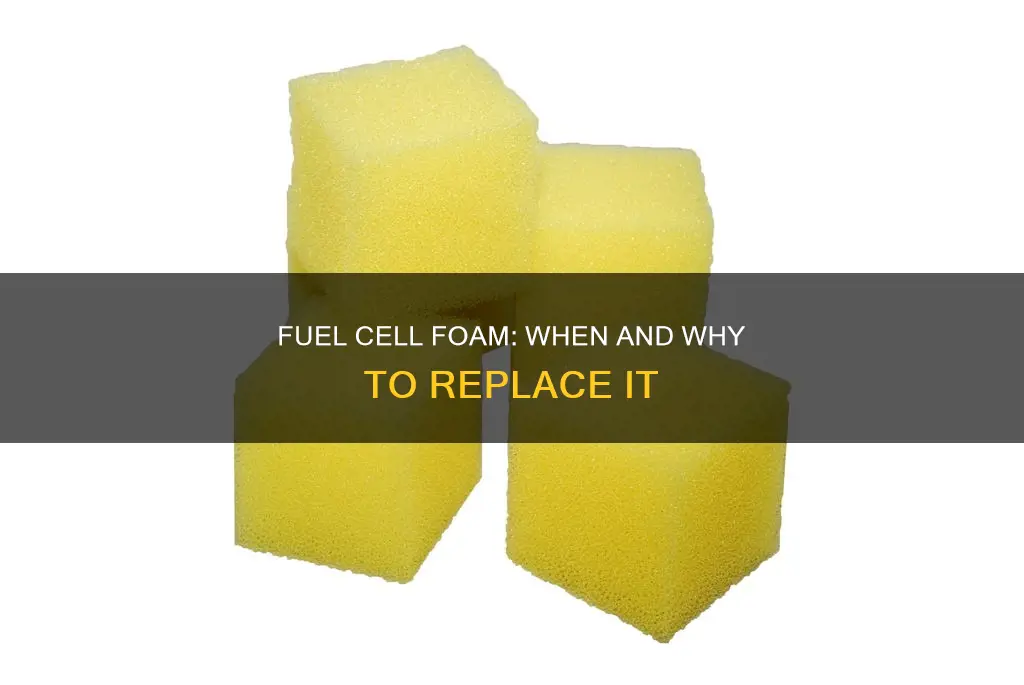
When it comes to maintaining fuel cell vehicles, one common question that arises is whether the foam used in the fuel cell system needs to be replaced. Fuel cell foam, a critical component in these vehicles, serves as a sealant and insulator, ensuring the efficient operation of the fuel cell. Over time, this foam can degrade due to various factors, including temperature fluctuations, chemical exposure, and normal wear and tear. Understanding the replacement schedule and signs of deterioration is essential for vehicle owners to ensure optimal performance and longevity of their fuel cell systems. This paragraph aims to explore the necessity of replacing fuel cell foam and provide insights into the factors that influence its lifespan.
What You'll Learn
- Fuel Cell Foam Condition: Inspect for damage, degradation, or contamination
- Performance Impact: Foam condition affects fuel cell efficiency and longevity
- Replacement Frequency: Regularly check and replace foam to maintain optimal performance
- Material Considerations: Choose foam compatible with fuel cell design and materials
- Maintenance Protocols: Establish a maintenance schedule for foam replacement and inspection
Fuel Cell Foam Condition: Inspect for damage, degradation, or contamination
Fuel cell foam, a critical component in fuel cell systems, plays a vital role in ensuring optimal performance and longevity. Regular inspection of this foam is essential to maintain the efficiency and reliability of fuel cell technology. The primary purpose of this inspection is to identify any potential issues related to damage, degradation, or contamination, which could significantly impact the overall functionality of the fuel cell.
When inspecting the fuel cell foam, the first step is to visually examine its condition. Look for any visible signs of damage, such as tears, punctures, or excessive wear. These physical damages can compromise the foam's ability to retain its structural integrity, leading to potential leaks or reduced performance. Additionally, check for any signs of degradation, which might be less apparent but equally concerning. Degradation can occur due to factors like age, chemical exposure, or improper maintenance, and it may result in a loss of foam density and effectiveness.
Contamination is another critical aspect to consider during the inspection process. Over time, the foam can accumulate contaminants such as dirt, dust, or even corrosive substances from the fuel cell environment. These contaminants can infiltrate the foam structure, affecting its performance and potentially causing blockages or reduced efficiency. It is crucial to identify and remove any visible contaminants to ensure the foam's optimal functioning.
To perform a thorough inspection, consider using specialized tools and techniques. For instance, magnifying glasses or microscopes can help identify microscopic damage or degradation. Additionally, non-destructive testing methods, such as eddy current or ultrasonic testing, can be employed to detect internal flaws or structural issues without causing further damage to the foam. These advanced inspection techniques provide a comprehensive understanding of the foam's condition.
In summary, regular inspection of fuel cell foam is a critical maintenance task. By visually examining the foam for damage, degradation, and contamination, you can ensure that any potential issues are identified early on. This proactive approach to maintenance helps prevent system failures and promotes the longevity of fuel cell technology, ultimately contributing to a more sustainable and efficient energy solution.
Fuel Injector Replacement: An Easy DIY Task?
You may want to see also
Performance Impact: Foam condition affects fuel cell efficiency and longevity
The condition of the foam in a fuel cell system is a critical factor that significantly influences the overall performance and longevity of the fuel cell. Foam, often made from a polymeric material, serves as a separator and gas diffusion layer, allowing for the efficient transfer of reactants and the collection of the generated electricity. However, over time, this foam can degrade, leading to a cascade of performance issues.
One of the primary impacts of degraded foam is a decrease in the efficiency of the fuel cell. As the foam ages, it may become more permeable to gases, leading to increased gas leakage. This leakage can result in a loss of reactant, reducing the overall efficiency of the cell. Additionally, the degraded foam may not effectively separate the anode and cathode, leading to a higher rate of crossover, where hydrogen or oxygen atoms cross from one side of the cell to the other, causing internal short circuits and further reducing efficiency.
The performance decline due to foam degradation is not limited to efficiency. The foam's structural integrity is crucial for maintaining the mechanical stability of the fuel cell stack. If the foam is damaged or worn out, it can lead to physical damage to the cell components, including the catalyst layers and the bipolar plates. This damage can cause a loss of active surface area, further reducing the cell's ability to generate electricity.
Moreover, the condition of the foam can also affect the longevity of the fuel cell. Foam that is no longer effective at separating gases can lead to increased corrosion and degradation of the cell's components, particularly the catalyst layers. This can result in a shorter operational lifespan for the fuel cell, as the cell may require more frequent maintenance or replacement.
In summary, the performance and longevity of a fuel cell are closely tied to the condition of the foam. Regular inspection and maintenance of the foam layer are essential to ensure optimal performance and extend the life of the fuel cell system. This includes checking for signs of degradation, such as cracking, swelling, or discoloration, and taking appropriate action, such as replacing the foam, to maintain the efficiency and reliability of the fuel cell.
Nuclear Fusion: The Future of Energy or a Misguided Dream?
You may want to see also
Replacement Frequency: Regularly check and replace foam to maintain optimal performance
Regular maintenance of fuel cell systems is crucial to ensure their longevity and optimal performance. One critical aspect often overlooked is the condition of the foam used within these systems. Fuel cell foam, typically made of a lightweight, insulating material, plays a vital role in maintaining the structural integrity of the fuel cell and preventing leaks. Over time, this foam can degrade, leading to potential issues that may compromise the system's efficiency and safety. Therefore, it is essential to establish a regular replacement schedule for this foam to mitigate these risks.
The replacement frequency for fuel cell foam is a critical consideration for system owners and operators. Given the harsh operating conditions of fuel cells, including high temperatures and pressures, the foam can deteriorate more rapidly than other components. As a general guideline, it is recommended to inspect the foam at least once a month. This frequent inspection allows for the early detection of any signs of degradation, such as cracks, tears, or disintegration. If any issues are found, the foam should be replaced immediately to prevent further damage and potential system failure.
In addition to monthly inspections, a more comprehensive maintenance schedule should be implemented. This schedule should include regular cleaning and replacement of the foam, especially in areas that are more susceptible to wear and tear, such as the fuel cell's inlet and outlet ports. Over time, these ports can become clogged or damaged, leading to reduced performance and potential safety hazards. By regularly replacing the foam in these critical areas, you can ensure that the fuel cell system operates efficiently and safely.
The process of replacing the foam involves carefully removing the old material and installing new, high-quality foam. This task should be performed by trained professionals to ensure proper installation and avoid any potential damage to the fuel cell. When selecting replacement foam, it is essential to choose a material that meets the specific requirements of the fuel cell system, including its operating temperature and pressure ranges. Using the correct type of foam will help maintain the system's performance and extend its lifespan.
In summary, regular checks and replacements of fuel cell foam are essential for maintaining the system's optimal performance and safety. By adhering to a strict maintenance schedule, including monthly inspections and more frequent replacements in critical areas, operators can ensure that their fuel cell systems operate efficiently and reliably over their entire lifespan. This proactive approach to maintenance will ultimately save costs and prevent potential system failures.
Replacing the Fuel Sender in Your 1981 Camaro
You may want to see also
Material Considerations: Choose foam compatible with fuel cell design and materials
When designing and maintaining fuel cells, one crucial aspect often overlooked is the choice of foam material. The foam plays a vital role in the overall performance and longevity of the fuel cell, and selecting the right type is essential. The primary purpose of foam in fuel cells is to provide insulation, absorb vibrations, and facilitate efficient heat management. Therefore, it is imperative to consider the compatibility of the foam with the specific fuel cell design and materials used.
One key factor to consider is the thermal conductivity of the foam. Fuel cells generate a significant amount of heat during operation, and efficient heat dissipation is crucial to prevent overheating. Foam with low thermal conductivity can help retain heat within the fuel cell, ensuring optimal operating temperatures. This is particularly important in high-performance fuel cells where temperature control is critical for efficiency and longevity.
Additionally, the compressibility and density of the foam should be evaluated. Fuel cells often operate under high-pressure conditions, and the foam must be able to withstand these pressures without compromising its structural integrity. A foam with suitable compressibility can absorb vibrations and shocks, reducing the risk of damage to the fuel cell components. It should also have a consistent density to ensure uniform performance and prevent localized stress points.
Furthermore, the choice of foam material should consider its chemical compatibility with the fuel cell's components. Fuel cells often use corrosive chemicals, such as hydrogen and oxygen, which can interact with certain foam materials over time. Selecting a foam made from materials resistant to these chemicals is essential to prevent degradation and ensure the long-term reliability of the fuel cell system.
Lastly, the environmental impact of the foam should be considered. With growing concerns about sustainability, choosing foam materials that are recyclable or biodegradable can contribute to a more eco-friendly fuel cell design. This aspect is becoming increasingly important as the industry aims to minimize the environmental footprint of fuel cell technology. By carefully evaluating these material considerations, engineers can make informed decisions to optimize the performance and longevity of fuel cells while ensuring compatibility with their unique design requirements.
Replacing the Fuel Pump in Your 1989 Camaro: Step-by-Step Guide
You may want to see also
Maintenance Protocols: Establish a maintenance schedule for foam replacement and inspection
Establishing a maintenance schedule for foam replacement and inspection is crucial for ensuring the optimal performance and longevity of fuel cell systems. Fuel cell foam, often used to insulate and protect the fuel cell stack, plays a vital role in maintaining the system's efficiency and reliability. Over time, this foam can degrade or become compromised, leading to potential issues. Therefore, a proactive maintenance approach is essential.
The first step in creating an effective maintenance protocol is to identify the specific foam type used in the fuel cell system. Different types of foam may have varying lifespans and replacement requirements. For instance, some foams are designed to be durable and long-lasting, while others might be more susceptible to environmental factors. Once the foam type is determined, you can tailor the maintenance schedule accordingly.
A recommended maintenance schedule could involve regular inspections at predefined intervals. These inspections should include a thorough examination of the foam's condition. Look for signs of wear, tear, disintegration, or any visible damage. Check for any gaps or voids that might have formed between the foam and the fuel cell components. Early detection of these issues is key to preventing potential system failures. If any defects are found, immediate replacement of the affected foam is necessary.
During the inspection process, it is also beneficial to clean the foam to remove any accumulated dirt, debris, or contaminants. This cleaning process should be gentle to avoid further damage to the foam. Regular cleaning can help maintain the foam's integrity and ensure it performs its intended function effectively.
In addition to visual inspections, consider implementing a testing protocol for the foam's performance. This could involve measuring the foam's thickness and density at various points to ensure it meets the required specifications. If the foam's performance deviates from the expected standards, it may indicate a need for replacement. By combining visual inspections with performance testing, you can establish a comprehensive maintenance routine.
Remember, the frequency of these maintenance tasks should be based on the specific requirements of the fuel cell system and the environmental conditions it operates in. Regular maintenance will help ensure the fuel cell foam remains in optimal condition, contributing to the overall reliability and efficiency of the fuel cell system.
Replacing the Fuel Filter: A Step-by-Step Guide for 2004 Monte Carlo SS Owners
You may want to see also
Frequently asked questions
The frequency of replacing the fuel cell foam depends on various factors, including the type of foam, the vehicle's usage, and environmental conditions. Generally, it is recommended to inspect the foam regularly and replace it if it shows signs of wear, tear, or damage. Over time, foam can degrade due to heat, chemicals, or physical impact, leading to reduced performance and potential safety hazards. It's best to consult the vehicle's manual or seek professional advice for specific replacement intervals.
Replacing fuel cell foam can be a complex task and is often best left to professionals or experienced technicians. The foam is typically located in hard-to-reach areas and requires specialized tools and knowledge to remove and install correctly. DIY replacements may void warranties and could lead to further issues if not done properly. It's advisable to have the work done by authorized service centers or individuals with expertise in fuel cell maintenance.
There are several indicators that the fuel cell foam may require replacement. These include visible damage such as tears, punctures, or disintegration, especially around the edges or in areas subjected to high stress. Reduced performance, such as decreased fuel efficiency or engine misfires, could also suggest foam degradation. Additionally, if you notice any unusual noises or vibrations from the fuel cell, it might be a sign of foam-related issues. Regular maintenance and inspections can help identify these problems early on.