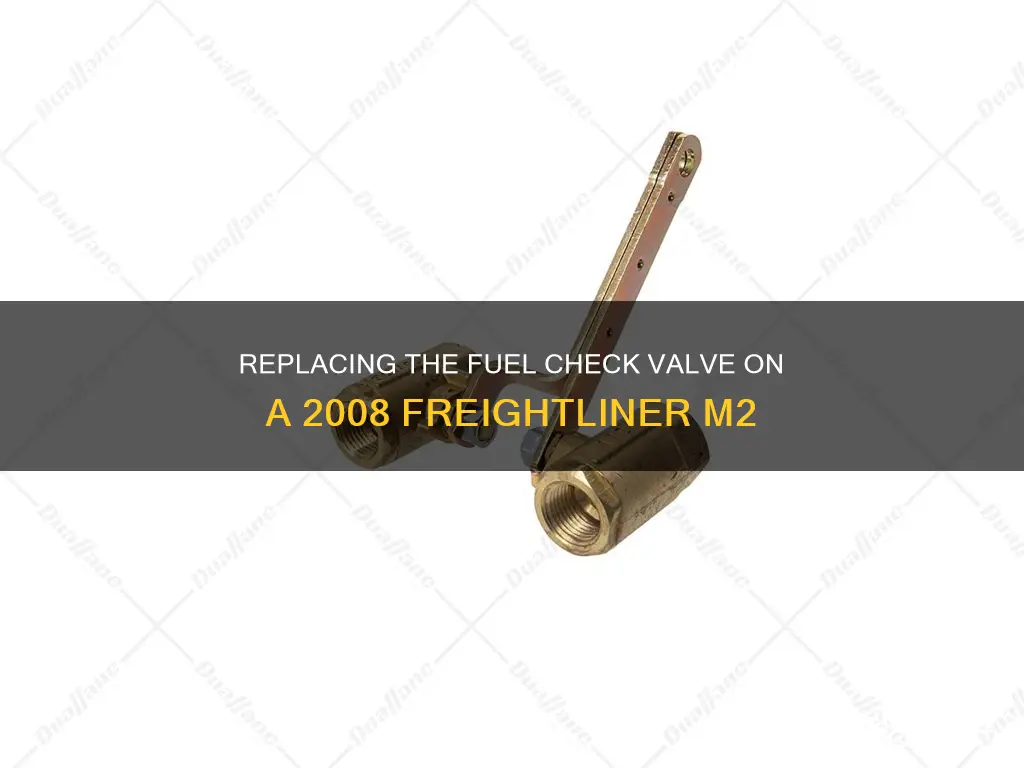
If you are experiencing issues with your 2008 Freightliner M2, such as a water fuel fault or a crank sensor fault, it may be necessary to replace the fuel check valve. This process involves checking for fuel contamination, replacing fuel and air filters, and monitoring fuel pressure and fluctuations. An injector test may also be advisable to identify any potential valve issues.
What You'll Learn
Check for water contamination in the fuel
Water in your fuel tank can cause serious issues with your engine, so it's important to check for contamination and address it promptly. Here are some detailed steps to help you check for water contamination in the fuel system of your 2008 Freightliner M2:
Signs and Symptoms of Water Contamination:
- Difficulty Starting the Engine and Power Decrease: Water in the fuel can cause issues with the combustion process, leading to rough idling, stalling, and difficulty starting the engine.
- Engine Sputtering and Hesitation: Water in the fuel can cause irregular combustion, resulting in engine sputtering and hesitation during acceleration.
- Rough Idling and Misfires: Water can disrupt the fuel density that injectors are designed to handle, leading to injector stress, engine stalling, and uneven firing of cylinders.
- Unexpected Engine Stalling: Initially, the engine may run fine, but over time, fuel combustion weakens due to water contamination, which can lead to sudden engine stalls.
- Unusual Fuel Smell: Water can alter the typical gasoline smell, making it unpleasant. This could be an early indication of water contamination.
Testing for Water Contamination:
- Visual Inspection: Drain a small amount of fuel into a clear glass container and let it sit for about 30 minutes. Water is denser than gasoline, so it will form a clear layer at the bottom of the container.
- Water Detection Additives: Use water-detecting additives, such as Kolor Kut Water Finding Paste. Apply the paste to a dipstick or a weighted string and insert it into the fuel tank. If water is present, the paste will change colour, usually turning red.
Preventing Water Contamination:
- Maintain Fuel Quality: Use high-quality fuel from reputable sources, and store it in reliable, above-ground fuel tanks.
- Fuel Cap Maintenance: Ensure your fuel cap is in good condition and properly sealed. Replace it if it is faulty or worn to prevent water ingress.
- Regular Vehicle Maintenance: Regularly inspect your fuel system to detect issues early on. Keep the fuel tank as full as possible to minimize air space and avoid condensation.
If you suspect water contamination in your fuel system, it is important to take action immediately. Drain and clean the fuel tank, then refill it with fresh fuel to prevent damage to your engine and fuel system.
Replacing Fuel Injectors in Nissan Frontier: Step-by-Step Guide
You may want to see also
Monitor fuel pressure and its fluctuations
To monitor fuel pressure and its fluctuations, you can start by checking the pressure at the priming port, which should ideally read 90-110 psi at 1800 rpm and around 75-80 psi at idle, with no fluctuation. If you observe fluctuations, there could be a few potential issues.
Firstly, check the suction side of the big fuel filter mounted on the frame rail. If you notice a lot of consistent bubbles, it indicates that air is being sucked in on the suction side. In this case, bypass the suction side and run the fuel into a bucket, then recheck the fuel pressure.
Another potential issue could be the two-stage valve located on the high-pressure pump or the doser pressure regulator in the high-pressure manifold, which can cause hard start or no-start problems if they are stuck open.
Additionally, leaking injectors can also cause fluctuations in fuel pressure. To check for this, remove the EGR hot pipe and inspect for large amounts of fuel. If there is fuel present, stop cranking the engine and remove the injectors.
It is also important to check for external fuel leaks by spraying all the fittings with soap to identify any leaks.
By monitoring the fuel pressure and addressing these potential issues, you can identify and resolve fluctuations in fuel pressure.
Replacing Fuel Tank Vent Valve in Mercedes-Benz W203
You may want to see also
Conduct an injector test
To conduct an injector test on a 2008 Freightliner M2, follow these steps:
Listening for Bad Fuel Injectors
First, put on safety gear, including eye protection and gloves, to protect yourself from injury while working on the engine. Next, open the hood of your Freightliner and locate the fuel injectors. You can refer to the service manual for your vehicle to find their exact location. Most applications have one fuel injector per cylinder, usually located on the intake manifold and connected by a fuel rail.
Now, find a thin, metal rod or screwdriver that is at least a foot long. Place one end of this tool on a fuel injector and hold it at an angle that allows you to bring your ear close to the other end. Listen for an audible clicking sound, which indicates that the injector is being activated. Repeat this process for each injector. If you find one that is not clicking, there may be an issue with the injector or its electronic control.
Ensuring the Injectors Are Receiving Power
Turn the key to the "on" position without starting the engine to activate the vehicle's electrical system. Connect a test light to the negative terminal of the battery. Locate the two wires going into each injector; one of these wires should be a 12-volt constant that continuously receives power. Use the test light to check each wire for voltage. If neither wire makes the light turn on, there is an issue with the power reaching the fuel injector. Repeat this process for each injector.
Checking the Trigger Circuit for the Injectors
For this step, connect the test light to the positive terminal of the battery. Have an assistant start or turn over the engine. Use the test light to probe the opposite wire of the constants identified in the previous step. With the engine running at idle, the test light should flicker dimly, and more brightly when your helper applies throttle by pressing the gas pedal. This light represents the signal being transmitted by the ECU to the injector to spray fuel. If the test light is not lighting up, the injector may be faulty or there could be an issue with the electronic control unit.
Disconnect the wiring clips to each injector and begin the test again. With none of the injectors connected, the flickering pulse should transmit through all the wires without issue. Keep the test light connected as you reconnect each fuel injector one by one. When you connect a faulty injector, the pulse intensity should dim.
Additional Tips
- If your vehicle won't run, attempting to turn it over for too long can kill the battery and damage the starter.
- Cover any holes in the wire's protective coating with electric tape when you're done testing.
- If you have long hair, tie it back tightly to prevent it from getting caught in any moving parts under the hood.
- Consult your vehicle's service manual or a mechanic for specific instructions related to your Freightliner model.
Please note that this information is intended to provide general guidance and that consulting a certified mechanic or a Freightliner-specific manual is recommended for detailed, model-specific instructions.
Replacing the Fuel Door on a 2010 F150: Easy Steps
You may want to see also
Check for a faulty control valve
To check for a faulty control valve, you will need to monitor the fuel pressure and check its readings and fluctuations. You can do this by turning the key on and listening for the lift pump, which will be operating if present. If the pressure appears fine, but you are still experiencing surging, you can try slightly opening any of the fuel lines on the rail to cause a leak. If the pressure falls and the surging ceases, resulting in the engine running smoothly, then there may be a return issue, which could be caused by a faulty control valve.
Another way to check for a faulty control valve is to conduct an injector test. If the injector test is normal, and you are still experiencing issues, then the problem may be related to a faulty control valve or a restriction.
If you are experiencing a water fuel fault and a crank sensor fault, it is recommended to change all the fuel filters and see if that solves the problem. If you are still experiencing issues, it may be related to the control valve.
If your engine is sufficiently new, you can also try conducting the injector cut-out test or the inject test, which evaluates all six injectors one by one for load and volume. If opening a line allows the engine to operate normally without surging and there is no power loss, this suggests there might be a return issue, which could be caused by a faulty control valve.
Replacing Honda SH150 Fuel Pump: Step-by-Step Guide
You may want to see also
Check for a malfunctioning check valve
To check for a malfunctioning check valve, you can start by looking for signs of wear and tear on the valve itself. The springs and seats of check valves are common wear parts, so inspect those areas for any damage. Additionally, contaminated oil could cause debris to build up on the seat of the check valve, preventing it from closing properly.
You can also perform a pressure test to identify any issues. Add a tee on the cylinder cap side, attach a gauge, extend the stabilisers, and monitor the gauge for any changes in pressure. If there is a slow leak, you may need to repair or replace the check valve.
If you are experiencing issues with your fuel system, such as hard starts or air in the fuel lines, it could be due to a faulty check valve. Start by checking for any leaks in the fuel system and replacing the fuel filters to see if that resolves the issue. If not, you may need to inspect the bypass valves and check for any cracks or damage in the fuel system.
It's important to note that check valves are critical safety features in certain systems, such as outriggers in aerial lifts, where valve failure could result in instability or loss of function. Regular maintenance and inspections can help identify potential issues before they become more serious problems.
How Nuclear Submarines Require Refueling to Operate
You may want to see also