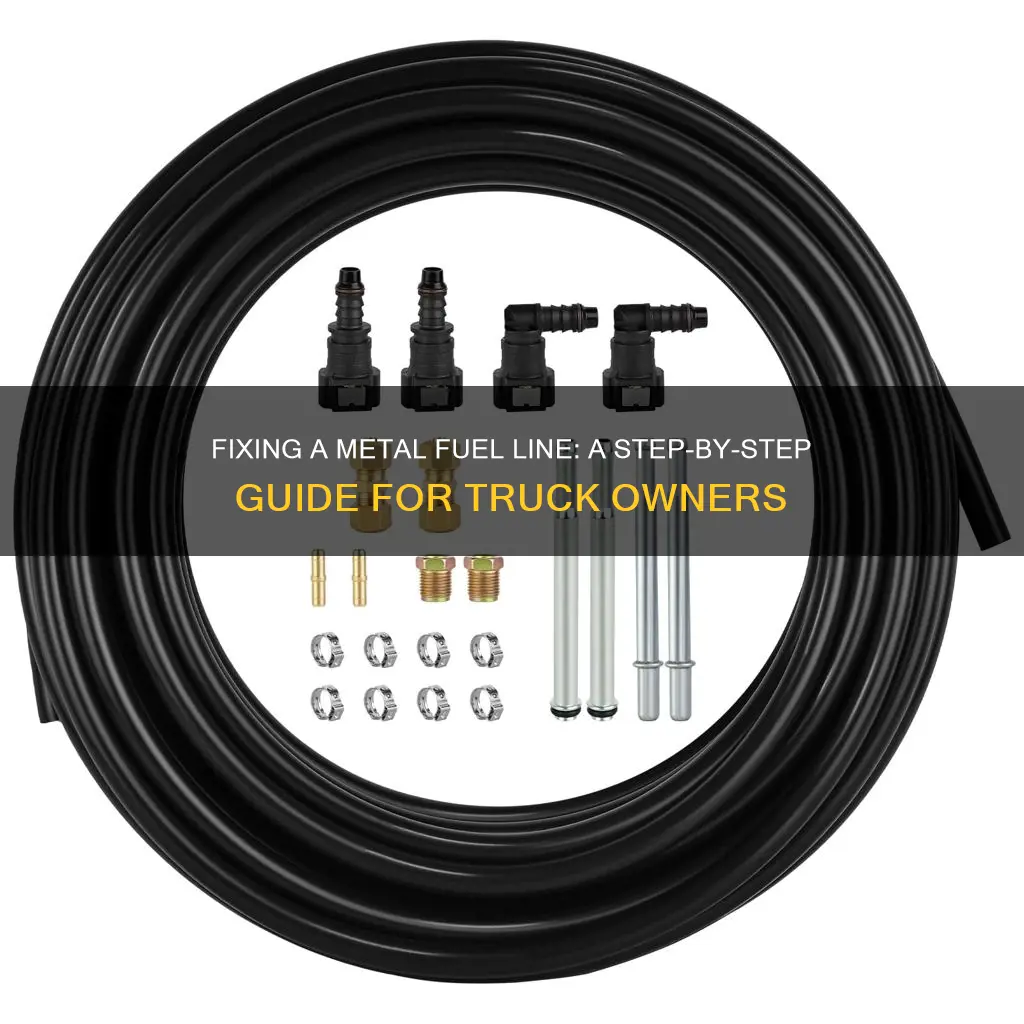
Repairing a metal fuel line on a truck can be a challenging task, but with the right tools and knowledge, it is definitely achievable. This guide will provide a step-by-step approach to fixing a damaged fuel line, ensuring your truck remains reliable and safe. From identifying the issue to choosing the appropriate repair methods, we'll cover everything you need to know to get your truck back on the road.
What You'll Learn
- Identify the damaged section: Locate the affected area using visual inspection and pressure testing
- Prepare the line: Clean the area, remove corrosion, and ensure a smooth surface for welding
- Choose the right welding technique: Select the appropriate welding method for metal fuel lines
- Secure with clamps: Temporarily clamp the line to prevent fuel leakage during the repair process
- Test and inspect: Thoroughly check the repaired line for leaks and ensure proper functionality
Identify the damaged section: Locate the affected area using visual inspection and pressure testing
When dealing with a damaged metal fuel line on a truck, the first crucial step is to accurately identify the affected section. This process involves a combination of visual inspection and pressure testing to ensure a thorough assessment.
Visual inspection is a fundamental technique to begin with. Carefully examine the fuel line for any visible signs of damage, such as cracks, corrosion, or bends. Look for areas where the metal might have become brittle or where there are visible tears or punctures. Pay close attention to any discolouration, especially if it appears rusty or discoloured, as this could indicate corrosion. Also, check for any signs of impact damage, such as dents or deformations, which might have occurred due to road debris or other external factors.
During the visual inspection, it's essential to consider the overall condition of the fuel line. Inspect the connections and fittings for any signs of leakage or damage. Ensure that all components are securely attached and in good condition. Look for any signs of heat damage, especially if the truck has been exposed to high temperatures, as this could weaken the metal over time.
Once the visual inspection is complete, pressure testing can provide further insights. This method involves inflating the fuel line with compressed air or a suitable fluid and observing for any leaks or pressure drops. Start by applying pressure to a specific section of the line and monitoring for any signs of leakage. Pay attention to the sound and feel of the line; a hissing sound or a noticeable decrease in pressure could indicate a damaged area.
Pressure testing should be conducted at different intervals along the fuel line to cover all potential problem areas. It is particularly useful for identifying internal damage that might not be visible to the naked eye. By using this method, you can pinpoint the exact location of the damage, making it easier to proceed with the necessary repairs or replacements.
Remember, a thorough inspection is key to ensuring the longevity and safety of your truck's fuel system. By combining visual inspection and pressure testing, you can accurately identify the damaged section and take the appropriate steps to repair or replace it, ensuring the truck's fuel line functions optimally and safely.
Condensation's Impact: Can Fuel Line Moisture Cause Car Sputters?
You may want to see also
Prepare the line: Clean the area, remove corrosion, and ensure a smooth surface for welding
When repairing a metal fuel line on a truck, the first crucial step is to ensure the area is prepared thoroughly for welding. This process involves a meticulous approach to guarantee a strong and durable repair. Here's a detailed guide on how to achieve this:
Cleaning the Area: Begin by thoroughly cleaning the section of the fuel line that requires repair. Use a wire brush or a specialized cleaning tool to remove any dirt, debris, or old fuel residue. It is essential to ensure that no contaminants remain, as they can interfere with the welding process and the overall integrity of the repair. Pay close attention to any bends or kinks in the line, as these areas might require extra cleaning to ensure a smooth surface.
Removing Corrosion: Corrosion is a common issue with metal fuel lines, especially if they have been exposed to fuel or moisture over time. Use a wire brush or a small hand tool to gently remove any corrosion or rust from the metal surface. If the corrosion is severe, you may need to use a wire brush with increasing force or consider using a small grinding tool to carefully remove the affected material. Ensure that you only remove the corrosion and not the protective layer of the metal, as this layer helps prevent further corrosion.
Ensuring a Smooth Surface: After cleaning and removing corrosion, the surface of the fuel line should be smooth and free of any imperfections. If there are any small bumps or irregularities, use a fine-grit sandpaper or a small file to carefully smooth them out. This step is critical to ensure that the welding process creates a strong bond without any weak points. Take your time with this process, as a smooth surface will significantly impact the success of the repair.
Once the area is thoroughly cleaned, corrosion-free, and smooth, you can proceed with the welding process, ensuring a robust and long-lasting repair for your truck's fuel line. Remember, taking the time to prepare the line correctly is essential for a successful and safe repair.
Finding the Perfect Fuel Line Fit for Your 2006 Scion TC
You may want to see also
Choose the right welding technique: Select the appropriate welding method for metal fuel lines
When it comes to repairing metal fuel lines on a truck, selecting the appropriate welding technique is crucial to ensure a robust and reliable fix. The choice of welding method depends on various factors, including the specific requirements of the fuel line, the type of metal used, and the overall condition of the line. Here's a guide to help you choose the right welding technique:
- Gas Welding: This traditional method involves the use of a gas torch to melt the base metal and create a fusion joint. Gas welding is versatile and can be applied to various metal types, making it suitable for fuel lines. It provides a strong bond when the metal is preheated, ensuring a solid weld. However, it requires skill and practice to control the flame and avoid overheating, which can lead to warping or damage to the fuel line. This technique is ideal for experienced welders who can maintain precision and control.
- Shielded Metal Arc Welding (SMAW): Also known as flux-cored arc welding, SMAW is a popular choice for fuel line repairs. It utilizes a continuous wire electrode that is fed through a welding gun, creating an arc between the electrode and the workpiece. The electrode's coating, or flux, protects the weld pool from atmospheric contamination. SMAW offers excellent control and the ability to work in various positions, making it versatile for different fuel line configurations. This method is particularly useful for repairing thinner metal fuel lines due to its precision and ability to create a consistent bead.
- Gas-Metal Arc Welding (GMAW): Commonly known as MIG welding, GMAW is a versatile process that uses a continuous metal wire electrode and a shielding gas to create a strong weld. This technique is highly efficient and produces a clean, consistent weld bead. MIG welding is suitable for both thin and thick metal fuel lines and can be performed in multiple positions. The process is relatively easy to learn and provides a strong, durable joint when properly executed.
- Oxy-Fuel Welding: This method employs a combination of oxygen and fuel gas to create a high-temperature flame for welding. Oxy-fuel welding is known for its ability to create precise, controlled heat, making it ideal for delicate repairs. It is particularly useful for small-diameter fuel lines and can be applied to various metal types. However, it requires careful handling of gases and a steady hand to avoid burns and ensure a clean weld.
When choosing a welding technique, consider the specific requirements of your fuel line repair. Factors such as the thickness of the metal, the length of the repair, and the accessibility of the area will influence your decision. It is essential to practice and gain experience with each welding method to ensure a successful and long-lasting repair. Additionally, always follow safety protocols and wear appropriate personal protective equipment when working with welding equipment.
Mastering the Art: A Guide to Removing Fuel Lines from Compression Nuts
You may want to see also
Secure with clamps: Temporarily clamp the line to prevent fuel leakage during the repair process
When dealing with a damaged metal fuel line on a truck, one of the crucial steps is to secure the line temporarily to prevent any potential fuel leakage during the repair process. This step is essential to ensure the safety of the vehicle and those around it. Here's a detailed guide on how to achieve this:
Identifying the Damage: Before clamping, inspect the fuel line to identify the specific section that requires repair. Look for any cuts, punctures, or signs of corrosion. This step is vital to ensure you clamp the correct area and prevent further leakage.
Gathering the Materials: You'll need a few essential tools and materials for this process. Obtain high-quality metal fuel line clamps specifically designed for automotive applications. These clamps should be made of durable materials like stainless steel or heavy-duty rubber to ensure a secure hold. Additionally, get some fuel line tape or a temporary sealing compound to reinforce the clamp's grip.
Clamping Technique: Start by cleaning the fuel line and the clamp's contact points to ensure a proper connection. Then, carefully position the clamp over the damaged section, ensuring it covers the entire length of the line. Tighten the clamp securely, but be cautious not to overtighten, as it may damage the line. Use the fuel line tape or sealing compound to reinforce the clamp's grip, especially if the line is thin or delicate. Ensure the clamp is tight enough to prevent any movement but not so tight that it causes damage.
Testing and Safety Measures: After clamping, it's crucial to test the system. Start the truck's engine and monitor for any fuel leaks. If no leaks are detected, proceed with the repair. However, if any leakage occurs, carefully remove the clamp and re-evaluate the damage. This temporary clamping method allows you to work on the fuel line without the constant risk of fuel spillage, making the repair process safer and more manageable.
Remember, this is a temporary solution, and the fuel line should be replaced or permanently repaired as soon as possible to ensure the truck's overall safety and performance. Always prioritize safety when working on fuel-related components in vehicles.
Mastering Ford Fuel Line Connector Removal: A Step-by-Step Guide
You may want to see also
Test and inspect: Thoroughly check the repaired line for leaks and ensure proper functionality
After completing the repair, it is crucial to thoroughly test and inspect the metal fuel line to ensure its integrity and proper functionality. This step is essential to guarantee that the vehicle's fuel system is safe and operational. Here's a detailed guide on how to conduct this inspection:
Leak Testing: Begin by applying a soapy water solution to the repaired area of the fuel line. This simple yet effective method helps identify any potential leaks. Take a small brush or a clean cloth and gently apply the soapy water mixture along the length of the line, ensuring it covers all connections and bends. If there are any cracks, holes, or improper connections, you will notice bubbles forming on the surface, indicating a leak. Make sure to check for leaks at both ends of the line, as well as any fittings or couplings. If you spot any leaks, carefully mark the location and consider the repair process if it's not already done.
Pressure Testing: For a more comprehensive assessment, perform a pressure test. This is especially important if the fuel line was damaged or altered significantly. Attach a pressure gauge to the fuel line, ensuring it is securely connected. Gradually increase the pressure in the system using a hand pump or a specialized fuel line pressure tester. As you apply pressure, closely monitor the gauge for any drops or fluctuations. A stable reading indicates a secure and leak-free connection. If the pressure drops, it suggests a potential issue, and further investigation is required.
Functionality Check: Once you've confirmed there are no leaks, it's time to test the fuel line's functionality. Start the truck's engine and listen for any unusual noises, especially hissing or roaring sounds, which could indicate a leak. Check for any fuel odors around the engine bay, as this might suggest a fuel leak. Ensure that the engine runs smoothly and that there are no fuel-related warning lights on the dashboard. Test the fuel pump's operation by listening to it and checking for any unusual sounds. Proper functionality ensures that the fuel is being delivered efficiently to the engine.
Visual Inspection: While testing, also perform a visual inspection. Look for any signs of corrosion, rust, or damage around the repaired area. Check for any visible cracks or bends in the line, especially if the repair involved cutting and re-welding the metal. Ensure that all connections are tight and secure, with no loose fittings that could cause vibrations and potential damage over time.
By following these steps, you can ensure that the metal fuel line on the truck is not only leak-free but also functions optimally, providing a safe and reliable fuel supply to the engine. It is a critical process in the overall maintenance and repair of the vehicle's fuel system.
T100 Fuel Line Guide: Choosing the Right Option
You may want to see also
Frequently asked questions
Visual inspection is the first step. Look for any visible signs of damage such as cracks, holes, rust, or corrosion along the fuel line. Also, check for any leaks or drips around the connections and fittings. If you notice any of these issues, it's crucial to address them promptly to prevent further damage and potential fuel leaks.
You'll need a few essential tools and materials for the repair. These include a fuel line cutter or a hacksaw to cut the damaged section, a fuel line crimping tool or a pair of pliers to secure the new connection, a replacement fuel line section (if needed), thread seal tape or pipe dope, and fuel line connectors or fittings. It's recommended to use high-quality materials to ensure a reliable repair.
While it is possible to repair a metal fuel line yourself, especially for minor damage, it's a task that requires careful attention to detail and some mechanical skills. If the damage is extensive or you're unsure about the process, it's best to consult a professional mechanic. They have the expertise and experience to ensure the repair is done safely and effectively, minimizing the risk of further issues.