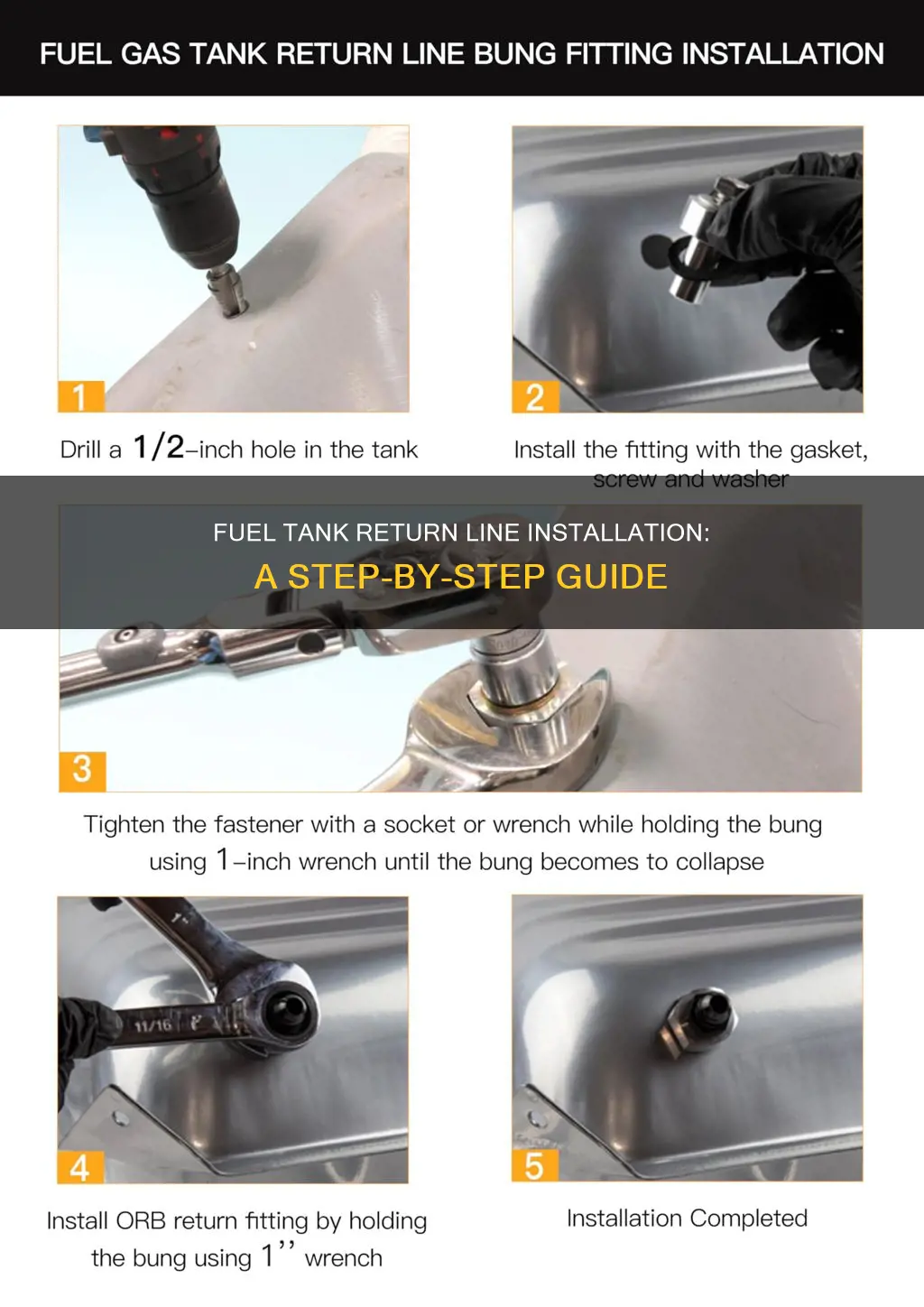
Installing a return line in a fuel tank is a crucial step to ensure efficient fuel management and prevent contamination. This process involves connecting a dedicated line to the fuel tank, allowing excess fuel to flow back to the engine's fuel supply, thus maintaining optimal pressure and performance. The return line is an essential component in fuel systems, especially in high-performance vehicles or those with complex fuel configurations. By following a systematic approach, this guide will provide a step-by-step process to install the return line, ensuring a smooth and reliable fuel system operation.
What You'll Learn
- Tank Preparation: Clean and inspect the tank, ensuring it's free of debris and ready for the return line installation
- Line Routing: Plan the optimal path for the return line, considering fuel flow and tank geometry
- Fittings and Connections: Choose appropriate fittings and ensure secure, leak-free connections for the return line
- Testing and Verification: Test the system for leaks and ensure proper fuel flow and pressure
- Final Adjustments: Make any necessary adjustments to the return line and fuel system for optimal performance
Tank Preparation: Clean and inspect the tank, ensuring it's free of debris and ready for the return line installation
Before you begin the installation process, it's crucial to ensure the fuel tank is in optimal condition. Start by thoroughly cleaning the tank to remove any dirt, grime, or debris that may have accumulated over time. This step is essential as it prevents any contaminants from affecting the performance of the return line. Use a suitable cleaning agent recommended for fuel tanks and follow the manufacturer's instructions. Rinse the tank thoroughly to eliminate any residue and ensure a clean environment for the installation.
Once the tank is clean, proceed with a comprehensive inspection. Check for any signs of corrosion, cracks, or damage that could compromise the tank's integrity. Inspect the interior walls and the bottom of the tank for any debris or foreign objects that might have settled. Pay close attention to the areas where the return line will be installed, ensuring there are no obstructions or potential interference points. This inspection is vital to identify any issues early on and make the necessary adjustments or repairs before proceeding with the installation.
If you notice any issues during the inspection, address them promptly. For example, if there are small cracks or corrosion, consider repairing or replacing the affected parts to ensure a secure and reliable installation. It's important to maintain the tank's structural integrity to prevent any fuel leaks or other complications. Additionally, check the tank's capacity and ensure it can accommodate the return line without any restrictions.
After completing the cleaning and inspection, verify that the tank is free from any debris or contaminants. This ensures that the return line functions optimally without any interference or blockages. Proper preparation at this stage will contribute to a successful and efficient installation process, minimizing the risk of future issues. Remember, a well-maintained tank is essential for the longevity and performance of the fuel system.
Teflon Tape on Fuel Lines: A Safe Bet?
You may want to see also
Line Routing: Plan the optimal path for the return line, considering fuel flow and tank geometry
When planning the route for the return line in a fuel tank, it's crucial to consider the fuel flow dynamics and the geometric constraints of the tank. The primary goal is to ensure efficient and reliable fuel return while minimizing potential issues like cavitation or fuel sloshing. Here's a step-by-step guide to help you plan the optimal path:
- Understand Fuel Flow: Begin by visualizing the fuel flow within the tank. Fuel typically enters the tank through a filler neck and is then distributed to the engine via a delivery line. When the engine operates, fuel returns to the tank through the return line. Understanding this flow is key to determining the optimal line placement.
- Consider Tank Geometry: The shape and layout of the fuel tank play a significant role in line routing. Different tank designs may have varying levels of complexity. For instance, a flat-bottomed tank might offer more straightforward routing options compared to a curved or sloped tank. Identify the tank's key features, such as baffles, fuel pumps, and any existing lines, to understand the available space and potential obstacles.
- Route Planning: Start by placing the return line at the lowest point of the tank, ensuring it aligns with the fuel flow direction. This helps in preventing airlock and promoting efficient fuel return. If the tank has a baffle, consider routing the line along the baffle to maintain a stable fuel level. For tanks with multiple compartments, carefully plan the line path to avoid crossing into other compartments, as this can lead to fuel mixing issues.
- Optimize Line Length and Placement: Aim for a shorter line length to reduce pressure drop and ensure efficient fuel return. Avoid sharp bends or kinks in the line, as these can restrict flow. Instead, opt for gentle curves and consider using flexible materials to accommodate the tank's geometry. Properly secure the line to prevent movement, which could lead to damage or disconnection.
- Consider Engine Mounting and Space Constraints: Take into account the engine's mounting position and any surrounding components. The return line should not interfere with other parts or cause clearance issues. Ensure that the line is routed away from heat sources or high-temperature areas to prevent damage.
By carefully considering fuel flow, tank geometry, and practical constraints, you can design an efficient and reliable return line installation. This planning process ensures that the fuel system operates optimally, providing consistent performance and longevity.
Mastering the Art of Bending Stainless Steel Fuel Lines
You may want to see also
Fittings and Connections: Choose appropriate fittings and ensure secure, leak-free connections for the return line
When installing a return line in a fuel tank, the choice of fittings and connections is critical to ensure a secure and leak-free system. The primary goal is to create a tight seal that can withstand the pressure and temperature variations associated with the fuel system. Here's a detailed guide on how to approach this task:
Select the Right Fittings: Begin by choosing fittings that are compatible with the materials used in your fuel tank and return line. Common materials include steel, aluminum, and various plastics. For example, if your fuel tank is made of aluminum, consider using fittings specifically designed for aluminum to ensure a proper fit and corrosion resistance. Fittings come in various types, such as elbows, tees, unions, and couplings, each serving a specific purpose. Select the fitting that best matches the shape and orientation required for your installation.
Consider the Size and Material: Fittings should be sized appropriately to accommodate the return line's diameter. Using a fitting that is too small can restrict fuel flow and create pressure buildup, potentially leading to leaks. Additionally, ensure that the fittings are made from materials that can withstand the corrosive properties of fuel. Stainless steel, for instance, is a popular choice due to its durability and resistance to rust and corrosion.
Secure Connections: Properly securing the fittings is essential to prevent leaks. Here are some key steps:
- Threaded Connections: If using threaded fittings, ensure the threads are clean and free of debris. Apply a thin layer of thread sealant (also known as pipe compound) to the male threads before assembly. Tighten the fitting securely, but be careful not to over-tighten, as this can damage the threads or the fitting itself.
- Clamped Connections: For clamped fittings, ensure the clamp is made from a compatible material and is the correct size for the return line. Place the fitting over the line, position the clamp on the fitting's tail, and secure it tightly. The clamp should be tight enough to create a seal but not so tight that it distorts the fitting or line.
- Welding or Soldering: For a more permanent connection, welding or soldering can be used. These methods provide a strong, reliable bond but require specialized skills and equipment. Always follow safety guidelines and consider the potential impact on the fuel system's performance and longevity.
Test for Leaks: After making all the connections, it is crucial to test the system for any leaks. This can be done by applying a small amount of diesel or fuel-compatible sealant to the connections and observing for any seepage. Alternatively, use a pressure gauge to check for leaks under pressure. If any leaks are detected, carefully inspect the connections and tighten or adjust them as necessary.
By carefully selecting the right fittings and ensuring secure, leak-free connections, you can effectively install a return line in your fuel tank, contributing to a more efficient and reliable fuel system.
Fixing a Flooded Fuel Line: A Step-by-Step Guide
You may want to see also
Testing and Verification: Test the system for leaks and ensure proper fuel flow and pressure
Before finalizing the installation, it's crucial to thoroughly test and verify the system to ensure its functionality and safety. The primary focus of this testing phase is to identify and rectify any potential leaks and to confirm that the fuel flow and pressure are within the required parameters.
Start by applying a comprehensive leak test to the entire system. This involves using a soapy water solution or a specialized leak detection spray to coat the surfaces of the fuel tank, return line, and any connections. Inspect the system carefully for any bubbles or signs of leakage. Pay close attention to the joints and fittings, as these areas are more susceptible to leaks. If any leaks are detected, carefully clean the affected areas and reapply the test solution to ensure the issue is resolved.
Once the leak test is completed, proceed with the fuel flow and pressure verification. This can be done by starting the engine and monitoring the fuel gauge. Ensure that the fuel level rises and falls as expected, indicating proper fuel flow. Check for any unusual noises or vibrations that might suggest a restriction or blockage in the system. Additionally, measure the fuel pressure using a suitable gauge to confirm it meets the manufacturer's specifications. Proper fuel flow and pressure are essential to ensure the engine operates efficiently and avoids potential damage.
Consider using a fuel pressure regulator if the pressure is consistently too high or too low. This component helps maintain the desired fuel pressure, ensuring optimal engine performance. It's also beneficial to check the return line's functionality by observing the fuel flow when the engine is idling and during acceleration. The return line should facilitate smooth and consistent fuel flow, contributing to the engine's overall responsiveness.
In summary, the testing and verification process is critical to the success of the installation. By meticulously checking for leaks and confirming fuel flow and pressure, you can ensure the system operates as intended, providing a reliable and safe fuel supply to the engine. This step is an essential part of the overall procedure, allowing for any necessary adjustments and ensuring a high-quality finish.
Fuel Line Removal: A Guide to Draining Gas Safely
You may want to see also
Final Adjustments: Make any necessary adjustments to the return line and fuel system for optimal performance
After completing the initial setup, it's crucial to perform final adjustments to ensure the return line and fuel system are functioning optimally. This step is essential to guarantee efficient fuel flow and prevent any potential issues. Here's a detailed guide on making those crucial final touches:
Inspect and Test the Return Line: Begin by thoroughly inspecting the installed return line. Check for any visible signs of damage, such as cracks, leaks, or kinks. Ensure that all connections are secure and tightly fastened. If any issues are found, address them immediately. Test the line by starting the engine and monitoring for any unusual noises or vibrations. The line should be smooth and flexible, allowing for slight movement without excessive flexing.
Adjust Clamps and Hoses: Pay close attention to the clamps and hoses connected to the return line. Ensure they are properly tightened to maintain a secure seal. Adjust the hose clips if they are too tight, as this can restrict fuel flow. Similarly, check the hose connections to the fuel tank and pump. Make sure they are correctly aligned and fastened to prevent any leaks or disconnections during operation.
Fine-Tune Fuel System: With the return line in place, it's time to fine-tune the overall fuel system. Check the fuel pump's operation by listening for its activation when the engine is running. Ensure the pump is delivering fuel at the correct pressure. Adjust the fuel pressure regulator if necessary to maintain optimal pressure levels. This step is critical to prevent engine performance issues and ensure efficient combustion.
Vacuum Test (Optional): For vehicles with a vacuum-assisted fuel system, consider performing a vacuum test. This test helps identify any potential issues with the fuel tank's vacuum seal. Use a vacuum gauge to measure the tank's vacuum level when the engine is off and running. Compare the readings to the manufacturer's specifications. Any significant deviations may indicate a problem with the fuel tank or return line installation.
Final Checks: Before considering the installation complete, perform a series of final checks. Start the engine and monitor for any unusual sounds or smells. Check for any fuel leaks around connections and ensure the fuel gauge functions correctly. Test-drive the vehicle to assess engine performance, acceleration, and overall responsiveness. These final checks will provide valuable insights into the system's functionality.
By meticulously following these final adjustments, you ensure that the return line and fuel system are optimized for performance, reliability, and longevity. This process is a critical step in the overall installation procedure, contributing to a well-functioning fuel system in your vehicle.
Sealing Fuel Lines: A Comprehensive Guide to Effective Repairs
You may want to see also
Frequently asked questions
A return line, also known as a fuel return line, is an essential component in a fuel system that helps to maintain proper fuel pressure and ensure efficient operation. It connects the fuel tank to the engine, allowing fuel to flow back into the tank after it has been used, thus preventing fuel accumulation and maintaining a steady fuel supply.
If you notice any issues with fuel pressure, such as hard starts, stalling, or inconsistent engine performance, it could be a sign that your fuel tank lacks a return line. Additionally, if you've recently replaced the fuel pump or made modifications to the fuel system, installing a return line might be necessary to optimize performance and prevent fuel-related problems.
While it is possible to install a return line as a DIY project, especially if you have some mechanical experience, it is recommended to seek professional assistance for a successful and safe installation. Fuel system work can be complex, and improper installation may lead to fuel leaks, engine damage, or other hazardous situations.
The process typically involves the following steps: 1) Locate the fuel tank and identify the appropriate mounting points for the return line. 2) Cut the fuel line to the desired length and attach the return line using suitable fittings and clamps. 3) Ensure a secure connection and proper routing to avoid any obstructions. 4) Test the fuel system for leaks and proper functionality. It is crucial to follow manufacturer guidelines and consult a professional for specific instructions tailored to your vehicle.