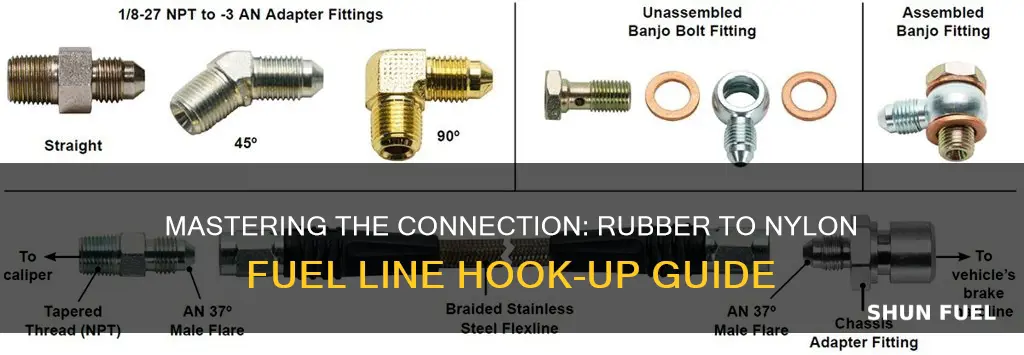
When working with different types of fuel lines, it's important to understand the proper techniques for connecting them to ensure a secure and efficient fuel transfer system. In this guide, we'll explore the process of hooking up a rubber fuel line to a nylon fuel line, providing step-by-step instructions and highlighting the key considerations to ensure a successful and safe connection.
Characteristics | Values |
---|---|
Materials | Rubber, Nylon |
Connection Type | Clamping, Fitting, Adhesive Bonding |
Advantages | Flexibility, Durability, Corrosion Resistance |
Disadvantages | May require specialized tools, Potential for fuel leakage if not properly connected |
Steps | 1. Clean both lines. 2. Use a fuel line fitting or clamp. 3. Ensure a tight seal. 4. Test for leaks. |
Considerations | Fuel type, Temperature range, Pressure requirements |
Safety | Follow manufacturer guidelines, Ensure proper ventilation, Avoid contact with skin |
Alternatives | Stainless steel, Aluminum, Braided fuel lines |
Maintenance | Regular inspections, Replace if damaged |
What You'll Learn
- Preparation: Ensure both lines are clean, dry, and free of debris
- Clamps: Use appropriate fuel line clamps for a secure connection
- Alignment: Align the lines properly to ensure a smooth flow
- Tightening: Tighten the clamps firmly but avoid over-tightening
- Testing: Check for leaks and ensure the connection is secure
Preparation: Ensure both lines are clean, dry, and free of debris
When preparing to connect a rubber fuel line to a nylon fuel line, it is crucial to ensure that both lines are in optimal condition to guarantee a secure and leak-free connection. The first step in this process is to inspect and clean each line thoroughly. Start by removing any visible dirt, grime, or debris from the surfaces of both lines. This can be done using a soft-bristled brush or a clean cloth to gently scrub the areas where the lines will be connected. Pay close attention to any bends or kinks in the lines, as these areas may require extra cleaning to remove built-up contaminants.
After cleaning, it is essential to dry the lines completely. Moisture can compromise the integrity of the connection, leading to potential leaks or corrosion. Use a clean, lint-free cloth or a soft-bristled brush to remove any remaining moisture from the surfaces. Ensure that the lines are completely dry before proceeding to the next step.
Debris removal is another critical aspect of preparation. Small particles or contaminants can interfere with the connection process and cause issues down the line. Inspect the lines again and use a fine-tipped tool or a small brush to carefully remove any debris that may be present. This step ensures that the surfaces of the lines are smooth and free from any foreign matter that could affect the bond between the rubber and nylon materials.
Additionally, it is recommended to inspect the lines for any signs of damage or wear. Look for cracks, tears, or any other imperfections that might weaken the lines and affect their ability to connect properly. If any damage is found, it is best to replace the affected lines to ensure a reliable fuel system.
By following these preparation steps, you create a solid foundation for a successful connection. Clean, dry, and debris-free lines will allow for a stronger bond and reduce the risk of leaks or other issues when hooking up the rubber and nylon fuel lines. This meticulous approach to preparation is an essential part of any fuel line installation or repair process.
Fuel Line Cleaner Overload: When More Isn't Always Better
You may want to see also
Clamps: Use appropriate fuel line clamps for a secure connection
When connecting rubber fuel lines to nylon fuel lines, using the right clamps is crucial for a secure and reliable join. Here's a detailed guide on how to achieve this:
Choose the Right Clamps: Select fuel line clamps specifically designed for the materials you're working with. Rubber and nylon fuel lines often require different clamp types. For rubber, consider using metal or stainless steel clamps with a smooth interior to avoid damaging the rubber. Nylon fuel lines might benefit from rubber or plastic clamps that provide a tight grip without causing any permanent deformation.
Prepare the Lines: Before clamping, ensure both fuel lines are clean and free of any debris or contaminants. Cut the lines to the desired length, allowing for a small overlap to ensure a snug fit. This preparation step is essential for a clean and secure connection.
Apply Clamps: Start by positioning the clamps over the overlapping sections of the fuel lines. Ensure the clamps are centered and aligned properly. Tighten the clamps firmly, but be careful not to overtighten, as this can cause damage to the fuel lines. The goal is to create a secure connection without compromising the integrity of the lines.
Secure and Test: After clamping, ensure the connection is secure by giving the lines a gentle tug to check for any play or movement. If everything feels tight and secure, you can proceed with further assembly or testing. It's important to double-check the clamps periodically, especially in high-vibration environments, to ensure they remain tight and intact.
Remember, the key to a successful connection is using the right tools and taking the time to prepare and secure the fuel lines properly. This approach will help ensure a reliable and long-lasting join between rubber and nylon fuel lines.
Nylon Fuel Line: Choosing the Right Material for Optimal Performance
You may want to see also
Alignment: Align the lines properly to ensure a smooth flow
When connecting rubber and nylon fuel lines, proper alignment is crucial to ensure a seamless and efficient flow of fuel. Here's a detailed guide on how to achieve this:
Start by ensuring that both fuel lines are clean and free from any debris or contaminants. Any dirt or residue can affect the connection's integrity. Use a suitable cleaner and a soft cloth to wipe down the surfaces where the lines will be joined. This step is essential for a secure and leak-free connection.
Next, inspect the fuel lines for any damage or wear. Look for cracks, tears, or any signs of deterioration. If you notice any issues, it's best to replace the affected lines to avoid potential leaks and ensure optimal performance. Healthy lines will provide a solid foundation for a proper connection.
Now, it's time to align the lines. Carefully position the rubber and nylon fuel lines so that they are parallel to each other. Ensure that the lines are aligned in a way that allows for a smooth and continuous flow of fuel. Any misalignment can lead to turbulence and potential fuel loss. Take your time to get this step right, as it forms the basis of a successful connection.
Use a fuel line connector or adapter that is compatible with both materials. These connectors are designed to securely join different types of fuel lines. Slide the connector onto the rubber line, ensuring it covers the entire length of the line. Then, carefully align the nylon line with the connector, making sure it fits snugly. The connector should provide a tight seal, preventing any fuel from escaping.
Finally, secure the connection by tightening the connector's fasteners or clips. Follow the manufacturer's instructions for the specific tool and torque required. A secure connection will ensure that the lines remain aligned and that the fuel flows smoothly without any interruptions. Regularly check and maintain these connections to guarantee reliable performance.
Chevy 2500 Fuel Line Removal: A Step-by-Step Guide
You may want to see also
Tightening: Tighten the clamps firmly but avoid over-tightening
When connecting rubber and nylon fuel lines, it's crucial to ensure a secure and leak-free bond. The tightening process is a critical step in achieving this. Here's a detailed guide on how to tighten the clamps effectively:
Start by ensuring that the fuel lines are properly aligned and positioned. The rubber and nylon lines should be connected at the appropriate points, ensuring a smooth and continuous flow path. Once aligned, it's time to apply the clamps. Use the recommended type of clamp for the specific fuel line materials. Clamps designed for rubber and nylon are typically made of durable materials like stainless steel or aluminum to withstand the fuel's pressure and temperature.
Now, begin tightening the clamps. Use a wrench or a spanner to apply firm pressure to the clamp's adjustment mechanism. The goal is to create a tight seal without causing any damage to the fuel lines. As you tighten, you should feel resistance, indicating that the clamp is securing the connection. However, be cautious not to over-tighten. Excessive force can lead to line distortion, cracking, or even breakage. Aim for a snug fit, ensuring the clamp is tight enough to prevent any movement or leakage.
A good practice is to test the tightness by gently pulling on the connected lines. If the connection holds firm and there's no give or movement, you've achieved the desired tightness. Remember, the key is to find the balance between a secure hold and avoiding any potential harm to the fuel lines.
In summary, tightening the clamps is an art that requires precision and care. By following these instructions, you can ensure a reliable and long-lasting connection between your rubber and nylon fuel lines, contributing to the overall efficiency and safety of your fuel system.
Fuel Line Disconnect: 2007 F-150 Guide
You may want to see also
Testing: Check for leaks and ensure the connection is secure
When connecting rubber and nylon fuel lines, ensuring a secure and leak-free joint is crucial to prevent fuel leaks and potential engine damage. Here's a detailed guide on how to test and verify the connection:
Preparation: Before testing, ensure you have the necessary tools and materials, including fuel line connectors, a fuel line inspection kit or soapy water, and a clean workspace. It's essential to work in a well-ventilated area when handling fuel to prioritize safety.
Assembly Process: Start by carefully cleaning the ends of both fuel lines. Remove any dirt, corrosion, or debris that might interfere with the connection. Then, apply a thin layer of fuel line connector compound or tape to the ends, ensuring an even coating. This step is vital as it provides a protective barrier and promotes a secure bond. Next, carefully insert the rubber fuel line into the nylon fuel line, ensuring it is fully seated and aligned properly. Tighten the connector securely, following the manufacturer's instructions for the specific tool required.
Leak Test: The critical step is to perform a thorough leak test to ensure the connection is intact. You can use a fuel line inspection kit, which typically includes a pressure gauge and a test port. Attach the kit to the connection and slowly increase the pressure. Listen for any hissing sounds, which indicate a potential leak. Alternatively, you can use soapy water as a simple and effective method. Spray a small amount of soapy water onto the connection and observe for any bubbles forming. Bubbles signify a leak, and you should investigate further to identify the source. If no leaks are detected, the connection is secure.
Security Check: In addition to the leak test, inspect the connection for any visible signs of damage or looseness. Ensure that the connector is tight and secure, with no visible gaps or movement. You can use a wrench to double-check the tightness, but be cautious not to overtighten, as this can also cause damage.
Documentation: After successfully testing and securing the connection, document the process with notes or photographs. This documentation will be valuable for future reference, especially if any issues arise. It also ensures that you can quickly identify and rectify any problems if the fuel line fails during operation.
By following these testing procedures, you can confidently ensure that the rubber and nylon fuel lines are properly connected, providing a reliable and safe fuel supply to your engine.
PEX Tubing for Fuel Oil: A Feasible Option?
You may want to see also
Frequently asked questions
Connecting rubber and nylon fuel lines requires a careful and precise approach. Start by ensuring both lines are clean and free of any debris or contaminants. Use a fuel line adapter or a specialized fuel line coupling that is designed for these types of materials. These adapters often have a rubber or nylon insert that creates a secure seal between the two lines. Apply a thin layer of fuel line adhesive or tape around the coupling and the ends of the fuel lines, then carefully slide the coupling over the lines, ensuring a snug fit. Finally, secure the connection with fuel line clips or ties to prevent any movement or leakage.
While a regular hose clamp might seem like a quick fix, it is not the most reliable method for joining rubber and nylon fuel lines. Hose clamps are typically designed for metal or flexible plastic lines and may not provide an airtight seal. The materials of rubber and nylon have different properties, and a regular hose clamp might not accommodate the expansion and contraction of these lines, leading to potential leaks over time. It is best to use a dedicated fuel line coupling or adapter for a secure and long-lasting connection.
Yes, having the right tools can make the process easier and more efficient. You will need a fuel line coupling or adapter that matches the sizes of your rubber and nylon fuel lines. Additionally, a fuel line adhesive or tape, fuel line clips or ties, and a cleaning agent or solvent to remove any dirt or grime from the lines are essential. It is also helpful to have a pair of pliers or a fuel line cutter to ensure a clean and precise connection.
Achieving a tight seal is crucial to prevent fuel leaks and ensure the safety of your vehicle. After applying the fuel line adhesive or tape, ensure that the coupling is slid over the lines smoothly and securely. Check that the coupling is not twisted or kinked, as this can affect the seal. Once the coupling is in place, use fuel line clips or ties to hold the lines taut and prevent any movement. It is recommended to test the connection by applying slight pressure and checking for any leaks before finalizing the installation.