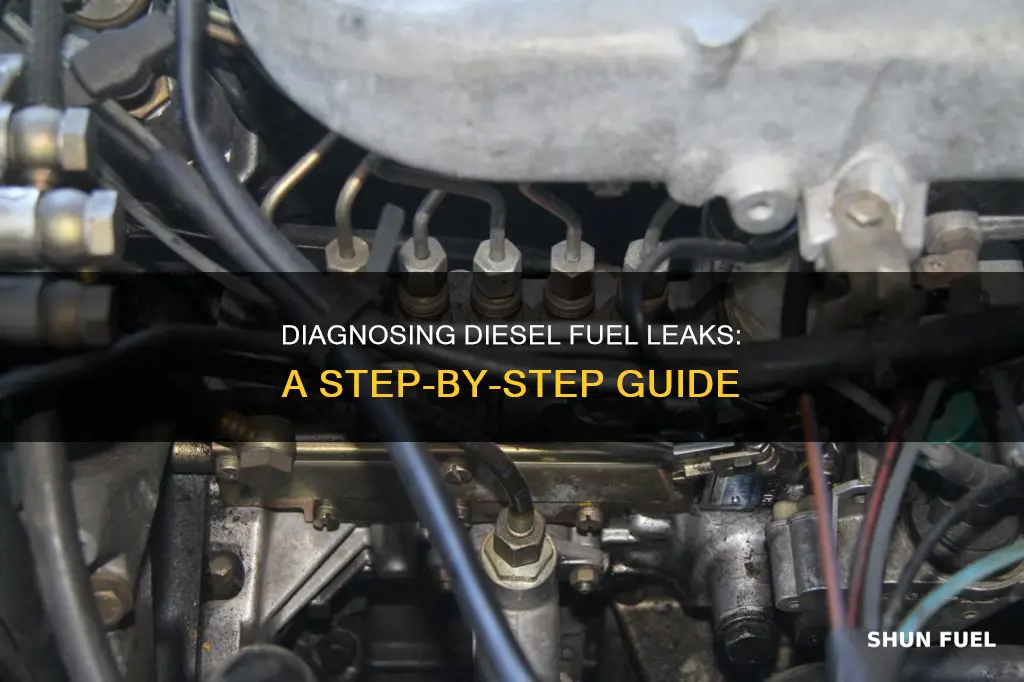
Identifying air leaks in diesel fuel lines is crucial for maintaining the performance and longevity of diesel engines. This guide will provide a step-by-step approach to help you locate and fix these leaks, ensuring optimal fuel delivery and engine operation. By following these methods, you can save time and money, as well as prevent potential engine damage caused by air intrusion in the fuel system.
What You'll Learn
Inspect visually for bubbles or condensation
When inspecting diesel fuel lines for air leaks, visual inspection is a crucial step that can help you identify issues early on. Start by examining the fuel lines for any visible signs of damage, such as cracks, punctures, or tears. These physical imperfections can provide entry points for air to enter the system. Look for any discolored or wet areas along the lines, as this could indicate the presence of air bubbles or condensation. Condensation, in particular, can form when the fuel line temperature drops below the dew point of the surrounding air, leading to water accumulation.
Pay close attention to the connections and fittings. Over time, these components can loosen or corrode, creating gaps that allow air to infiltrate. Inspect the threads and seals at these points for any signs of damage or wear. Even a small gap can be a potential entry point for air, so ensure all connections are secure and intact.
Another visual clue to look out for is the presence of bubbles or foam in the fuel. Air bubbles can form when fuel lines are filled with air during the fueling process or when the system is disturbed. If you notice any bubbles rising to the surface of the fuel, it's a strong indicator of an air leak. Similarly, if the fuel appears foamy or bubbly, it suggests that air has entered the system and is mixing with the fuel.
In addition to bubbles, keep an eye out for condensation. When air enters the fuel lines, it can carry moisture, leading to condensation inside the lines. This moisture can cause corrosion and degradation of the fuel, affecting engine performance. Condensation often appears as small droplets or a misty appearance along the fuel lines. If you notice any wet spots or a milky-like substance, it's a clear sign of air-related issues.
Remember, during this visual inspection, to be thorough and methodical. Walk or drive the vehicle through various terrains and conditions to simulate real-world scenarios. This will help you identify any intermittent or hard-to-spot leaks. By carefully examining the fuel lines, connections, and fuel itself, you can effectively locate and address air leaks, ensuring optimal performance and longevity of your diesel engine.
Tractor Fuel Line Location: A Comprehensive Guide
You may want to see also
Use a fuel pressure gauge to check for drops
To effectively locate an air leak in your diesel fuel lines, utilizing a fuel pressure gauge is a crucial step. This tool allows you to measure the pressure of the fuel as it exits the fuel pump, providing valuable insights into the system's performance. Here's a detailed guide on how to use a fuel pressure gauge to identify and address air leaks:
Preparation and Safety: Before you begin, ensure you have the necessary tools, including a fuel pressure gauge, a wrench, and a safe working environment. It's essential to work on the vehicle in a well-ventilated area to avoid inhaling any fuel vapor. Additionally, disconnect the battery to prevent any accidental electrical discharges while working on the fuel system.
Locate the Fuel Pressure Gauge: Most modern vehicles have a fuel pressure gauge integrated into the dashboard. If your vehicle doesn't have a built-in gauge, you can use a portable digital gauge. Connect the gauge to the fuel line, ensuring a secure and tight connection. The gauge should display the fuel pressure reading.
Check for Pressure Drops: With the gauge connected, start the engine and allow it to idle. Observe the fuel pressure reading on the gauge. A healthy diesel fuel system should maintain a steady pressure within the specified range, typically between 30 to 60 psi (pounds per square inch). If you notice a significant drop in pressure, it could indicate an air leak. For instance, if the pressure drops by 10 psi or more within a few seconds of starting the engine, it's a strong sign of an issue.
Isolating the Leak: If a pressure drop is detected, carefully inspect the fuel lines for any visible signs of damage, cracks, or disconnections. Use a flashlight to examine the lines for any signs of deterioration or punctures. Pay close attention to connections and fittings, as these are common areas where leaks occur. You might also need to remove certain components, like fuel filters or lines, to access hard-to-reach areas.
Troubleshooting: If the leak is not immediately visible, you may need to use a methodical approach to narrow down the source. Start by checking the fuel pump's operation and ensuring it's delivering fuel at the correct pressure. Then, check the fuel injectors for any blockages or malfunctions. Consider using a fuel pressure tester to measure pressure at different points in the system, helping to pinpoint the exact location of the leak.
Remember, using a fuel pressure gauge is a critical diagnostic tool for identifying air leaks in diesel fuel lines. By following these steps, you can efficiently locate and repair the issue, ensuring your vehicle's fuel system operates optimally.
Dodge Ram Fuel Line Replacement: A Step-by-Step Guide for 1997 Models
You may want to see also
Apply a soapy solution to suspect areas
To locate and repair air leaks in diesel fuel lines, a methodical approach is essential. One of the most effective techniques is to use a soapy solution, which can help identify the source of the leak. Here's a step-by-step guide on how to apply this method:
Start by preparing the soapy solution. Mix a mild dish soap with water, ensuring a good concentration of the soap. The soap acts as a detergent, creating bubbles that will help visualize the air leaks. Avoid using harsh chemicals or detergents that might damage the fuel lines.
Next, locate the suspect areas where leaks are suspected. These are typically the points where fuel lines connect to the engine, the fuel tank, or other components. Inspect the lines for any visible signs of damage, corrosion, or wear. Look for areas where the lines might be pinched, kinked, or damaged, as these can cause air leaks.
Now, apply the soapy solution to these suspect areas. Spray or pour the mixture onto the fuel lines, ensuring an even coverage. Pay close attention to the areas where the lines connect to various components, as these joints are common leak points. The soap will create bubbles, and any air leaks will be indicated by the formation of these bubbles.
As you apply the solution, observe the fuel lines carefully. The bubbles will provide a clear indication of the presence of air. If a leak is present, you will see bubbles forming at the source of the leak. This method is highly effective because it allows you to pinpoint the exact location of the leak without the need for extensive disassembly of the fuel system.
Once you've identified the leak, you can proceed with the necessary repairs. This might involve tightening connections, replacing damaged sections of the line, or addressing any other issues that caused the leak. Remember, regular maintenance and inspection of fuel lines can prevent such leaks and ensure the efficient operation of your diesel engine.
Dodge Truck Fuel Line Sizes: A Comprehensive Guide
You may want to see also
Listen for hissing sounds near fuel lines
When dealing with diesel fuel lines, one of the most effective ways to identify an air leak is by listening for hissing sounds near the fuel lines. This method is based on the principle that air bubbles in the fuel lines create a distinct, high-pitched noise. Here's a step-by-step guide on how to locate and address this issue:
Start by locating the fuel lines, which are typically found under the hood and along the sides of the engine compartment. These lines carry fuel from the tank to the engine. Inspect the fuel lines for any visible signs of damage, such as cracks, punctures, or loose connections. If you notice any physical damage, it could be the source of the air leak. However, sometimes, the leak might be internal, and you'll need to listen carefully.
Engage the engine and listen for any unusual noises. When the engine is running, air bubbles in the fuel lines will create a hissing sound as they move through the system. This sound is often described as a high-pitched, whistling noise. Pay attention to areas where the fuel lines connect to the engine, as these points can be common sources of leaks. The hissing might be more pronounced when the engine is idling or under load, as the pressure and flow rate of fuel can affect the sound.
To further assist in the diagnosis, you can use a stethoscope or a similar listening device to amplify the sound. Place the stethoscope near the fuel lines and listen for any abnormal noises. This tool will help you pinpoint the exact location of the leak, making it easier to address the issue. Remember, the hissing sound is a clear indicator of air in the fuel system, which can lead to reduced engine performance and potential damage over time.
If you successfully identify the source of the hissing, you can then proceed to repair or replace the affected fuel line segment. Ensuring a tight connection and using the appropriate fuel line material is crucial to prevent future leaks. Regular maintenance and inspection of the fuel system can help you catch these issues early and maintain the longevity of your diesel engine.
Mastering Fuel Line Clip Removal: A Step-by-Step Guide
You may want to see also
Use a fuel leak detector to identify issues
When it comes to diagnosing air leaks in diesel fuel lines, using a fuel leak detector can be an effective and efficient method. These detectors are specifically designed to identify fuel leaks, which can be caused by various issues such as damaged lines, faulty fittings, or worn-out components. Here's a step-by-step guide on how to utilize a fuel leak detector for this purpose:
Preparation and Safety: Before beginning the process, ensure you have the necessary safety gear, including gloves and eye protection, as you will be working with fuel. It's crucial to drain the fuel system to prevent any accidental spills or fires. This might involve draining the fuel tank or using a fuel pump bypass kit to release the fuel from the lines.
Application of the Detector: Start by applying the fuel leak detector to the fuel lines. These detectors typically come in spray cans or bottles and contain a chemical that reacts with fuel when a leak is present. Follow the manufacturer's instructions for application. Spray the detector onto the suspected areas, including connections, fittings, and any visible damage on the lines. Allow the detector to dry and then inspect the areas for any changes.
Identifying Leaks: The fuel leak detector will change color or exhibit a visible reaction when it comes into contact with fuel. This reaction indicates the presence of a leak. Look for discolored patches or areas where the detector has reacted, as these will pinpoint the locations of the leaks. For example, if you see a blue-to-red color change, it signifies a fuel leak. This method is particularly useful for hard-to-reach areas or small leaks that might not be visible to the naked eye.
Troubleshooting and Repair: Once you've identified the leaks, you can proceed with the necessary repairs. This may involve replacing damaged lines, tightening loose fittings, or addressing other components that might be causing the leaks. It's essential to address these issues promptly to prevent further damage and potential safety hazards.
Regular Maintenance: To ensure the longevity of your diesel fuel system, regular maintenance checks are recommended. Using a fuel leak detector as part of your maintenance routine can help catch issues early on, preventing costly repairs and potential breakdowns. This proactive approach can save you time and money in the long run.
Fuel Line Cleaning Costs: A Breakdown of Expenses
You may want to see also
Frequently asked questions
Air leaks in diesel fuel lines can be tricky to detect, but there are a few methods you can try. Firstly, listen for any unusual sounds like hissing or bubbling, which could indicate air entering the system. You can also use a pressure gauge to check for pressure drops, as air leaks will cause a rapid decrease in pressure. Additionally, inspect the lines for any visible signs of damage, corrosion, or discolouration, as these could be indicators of internal leaks.
Air leaks can occur due to several reasons. One common cause is the deterioration of rubber components over time, such as fuel filters, lines, and gaskets, which can crack and allow air to seep in. Corrosion and contamination of the fuel system can also lead to air bubbles. Additionally, improper installation or damage during maintenance work might result in air entering the fuel lines.
Repairing an air leak requires a systematic approach. Start by identifying the source of the leak, which could be a damaged fuel line, a faulty gasket, or a compromised fuel filter. Replace any worn-out components and ensure proper sealing. It's crucial to use high-quality replacement parts designed for diesel engines. After repairs, bleed the fuel system to remove any air bubbles and check for proper pressure. Regular maintenance and prompt attention to any issues can help prevent future air leaks.